Artec Leo로 빈티지 머슬카 개조를 현대화한 Tucci Hot Rods
과제: 미국의 자동차 개조 회사인 Tucci Hot Rods는 부품을 맞춤화하여 고객의 꿈의 자동차를 제작하는 데 사용할 수 있도록 부품을 더 빠르게 디지털화하는 방법을 모색했습니다.
솔루션: Artec Leo, Artec Studio, Rhinoceros 3D
결과: Tucci Hot Rods는 클래식 자동차의 조명, 통풍구, 그릴 및 기타 영역을 일련의 컷아웃을 통해 크기를 측정하는 대신 3D 스캐닝으로 디지털화합니다. 이를 통해 이 회사는 더 효율적이고 빠른 작업 흐름으로 부품을 3D 프린트하기 전에 소유자가 상상한 대로 정확하게 출력되도록 부품을 수정할 수 있습니다.
왜 Artec 3D인가? Artec Leo를 사용하면 이 회사는 Artec Studio로 생성된 모델을 편집하기 전에 핫로드 부품을 더 정확하게 캡처할 수 있으므로 생산을 위해 보내기가 더 쉬워집니다.
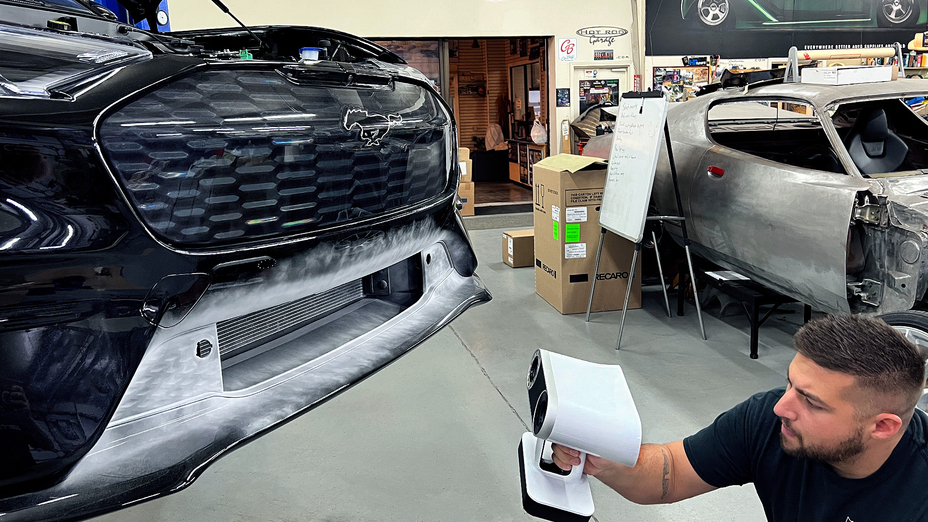
Artec Leo를 사용하여 Ford Mustang의 전면을 스캔하는 Dom Tucci. 이미지 제공: Tucci Hot Rods
핫로드는 자동차 역사에서 특별한 위치를 차지합니다. 그 뿌리는 1930년대 대공황으로 거슬러 올라갈 수 있으며, 당시 돈은 부족했지만 시간은 많았던 많은 미국 젊은이들이 자동차 개조 실험을 했습니다.
이러한 차량은 단순히 눈요기용으로만 제작된 것이 아니라 레이싱용으로 개조되었습니다. 드라이버들 사이에서 화려한 개조가 유행하고 성능 업그레이드가 이루어지면서 제2차 세계대전 이후 미국과 유럽 전역에서 공식적인 핫로드 레이싱 챔피언십이 생겨났습니다.
오늘날까지도 엔진을 개조한 최신형 및 구형 차량을 일컫는 용어인 핫로드의 레이싱은 자동차 애호가들에게 여전히 인기 있는 취미 활동입니다. 오리지널 차량을 아주 특별하게 만들었던 마법을 되찾고자 일부 수집가들은 20세기 초중반의 차량을 개조하는 작업을 계속하고 있지만, 그 과정은 말처럼 쉽지 않습니다.
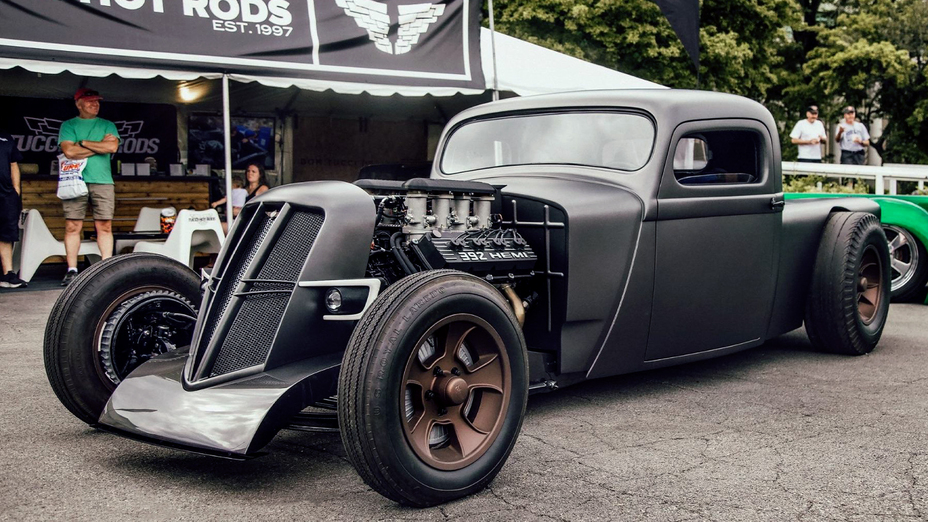
Tucci Hot Rods가 개조한 클래식 1936 Dodge 트럭. 이미지 제공: Tucci Hot Rods
클래식 자동차 부품 대부분은 생산이 중단된 지 오래고 부품의 설계 중 일부는 역사의 뒤안길로 사라졌기 때문에 개조하려면 많은 부품을 처음부터 다시 모델링해야 합니다. 기존의 수작업 패터닝 기법을 통해서도 그렇게 할 수 있지만, Tucci Hot Rods는 이제 Artec Leo의 도움으로 프로세스를 더 빠르고 정확하게 만들 수 있는 방법을 찾았습니다.
Tucci Hot Rods에서의 튜닝
지난 25년 동안 Tucci Hot Rods는 뉴욕에서 네바다에 이르는 모든 곳에서 고객을 확보하며 미국 자동차 개조 분야의 주요 업체로 자리 잡았습니다. 처음에 Dave Tucci Jr.와 그의 아내 Jill이 설립한 이 회사는 아들인 Dominick Tucci가 현재 산업 디자이너로 합류하면서 계속해서 가족 경영 회사로 남아 있습니다.
고객은 원하는 스타일이나 엔진을 중심으로 한 광범위한 계획을 세우고 이를 실현할 수단이 없는 상태에서 이 회사를 찾는 경향이 있습니다. 그리고 바로 여기서 Tucci Hot Rods는 초기 설계부터 제작 및 조립에 이르기까지 자동차 개조 애호가들의 전체 과정을 이끌어 주는 파트너로서 그 이름을 알렸습니다.
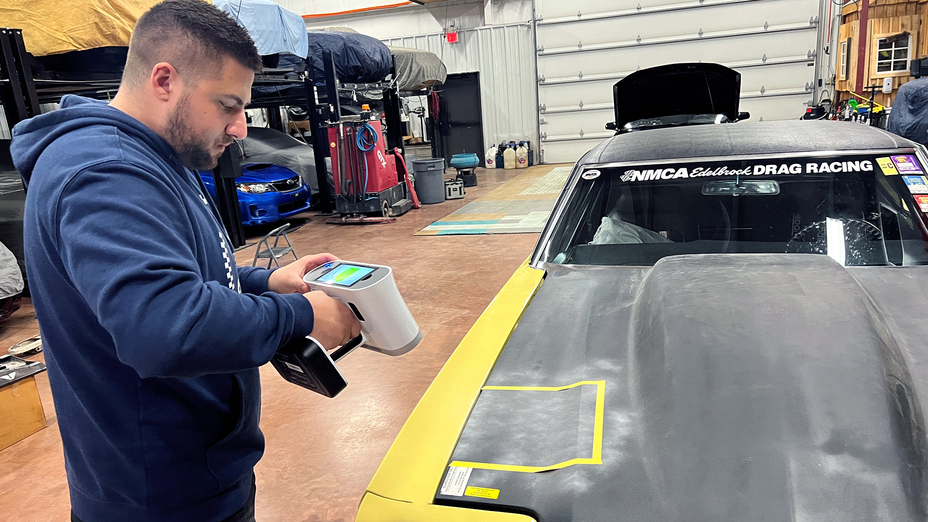
빈티지 Chevrolet 핫로드의 전면을 Artec Leo로 3D 스캔하는 Tucci. 이미지 제공: Tucci Hot Rods
인상적인 점은 이 회사는 압출 및 수지 3D 프린터를 작업 흐름에 통합하는 방법을 고안하여 렌즈, 라이트 커버, 통풍구와 같은 맞춤형 최종 사용 자동차 부품을 제작할 수 있다는 것입니다. 하지만 최근까지만 해도 이 회사는 이러한 개조 작업을 수행하는 데 필요한 측정값을 확보하는 방법에 대해서 상당한 어려움을 겪었습니다.
Dominick Tucci는 "복잡한 금속 모양이 있다고 가정하면 한 면의 패턴과 다른 면의 패턴을 만들고 치수를 측정한 다음 점을 연결하여 정확히 일치하는 모양을 만들 수 있습니다.
하지만 우리는 판지를 많이 사용했고, 프로토타입 조각을 프린트하여 어떤 것이 적합한지 확인하고, 변경하고, 새로운 것을 프린트하는 작업도 많이 했습니다. 많이 왔다 갔다 했습니다. 정말 멋진 템플릿을 만들면 2시간이 걸릴 수도 있습니다. 그 시점에서는 완벽하지 않을 수도 있습니다."라고 설명했습니다.
자동차 맞춤형 제작 현대화
Tucci Hot Rods의 부품 맞춤 방식을 획기적으로 바꾸기 위해 Tucci는 몇 년 전부터 3D 스캐닝을 실험하기 시작했습니다. 그는 처음에는 Xbox Kinect 카메라와 값싼 스캐닝 소프트웨어를 가지고 장난 삼아 사용했는데, 그것은 "아주 초보적인 표면만 포착"할 수 있었지만 고급 장치를 손에 넣을 수 있다면 "어떻게 작동할지에 대한 아이디어를 얻을 수 있었다."라고 말했습니다.
2021년 무역 박람회에서 Artec 3D 스캐너를 본 Tucci는 Artec 앰배서더인 Digitize Designs에 연락하여 Tucci Hot Rods의 요구 사항을 충족하는 올바른 장치와 소프트웨어를 선택하는 데 도움을 받았습니다. 유선 스캐너를 고려하던 이 디자이너는 완전 무선 Artec Leo의 일체형 특성과 내장형 디스플레이가 자신과 자신의 회사에 큰 도움이 되었다고 말합니다.
Tucci는 "전에는 컴퓨터에 연결된 스캐너를 사용해 본 적이 있는데, 진행 상황을 계속 확인하면서 스캔이 제대로 되고 있는지 확인해야 합니다. Artec Leo를 사용하면 항상 직접 볼 수 있습니다. 게다가 휴대성이 뛰어나서 이미 여러 번 도움이 되었습니다."라고 덧붙였습니다.
또한 Tucci Hot Rods는 Artec 3D 스캐닝을 채택하여 납기를 단축할 수 있었습니다. 이전에는 고객의 자동차 일부를 템플릿으로 제작하는 데 최대 2시간이 걸렸고, 개조 복잡도에 따라 프로토타입을 3D 프린트하는 데 최대 20시간이 걸렸습니다. Artec Leo의 0.1mm 포인트 정확도와 초당 최대 3천5백만 포인트의 데이터 캡처 속도 덕분에 Tucci와 그의 동료들은 이제 몇 분 만에 맞춤이 보장된 부품을 모델링할 수 있습니다.
"3~4일 동안 왔다 갔다 해야 했던 프로세스가 단 15분간의 스캐닝으로 대체되었습니다."
Tucci는 3D 스캐닝의 이점을 처음으로 활용한 프로젝트 중 하나인 클래식 Dodge의 맞춤형 후미등을 설계할 때에도 비용과 납기를 확실히 절감할 수 있었다고 말합니다.
Tucci는 "처음에는 3~4일 동안 템플릿을 만들고, 테스트 조각을 프린트하고, 변경하고, 다른 조각을 프린트하는 데 시간을 보냈습니다. 출력물은 최소 8~9시간이 걸렸고, 최종 부품에 사용하는 재료가 아닌 값싼 재료로 제작되었습니다. 결국 우리는 3~4일 동안 왔다 갔다 해야 했던 프로세스를 단 15분간의 스캐닝으로 대체했습니다."라고 말했습니다.
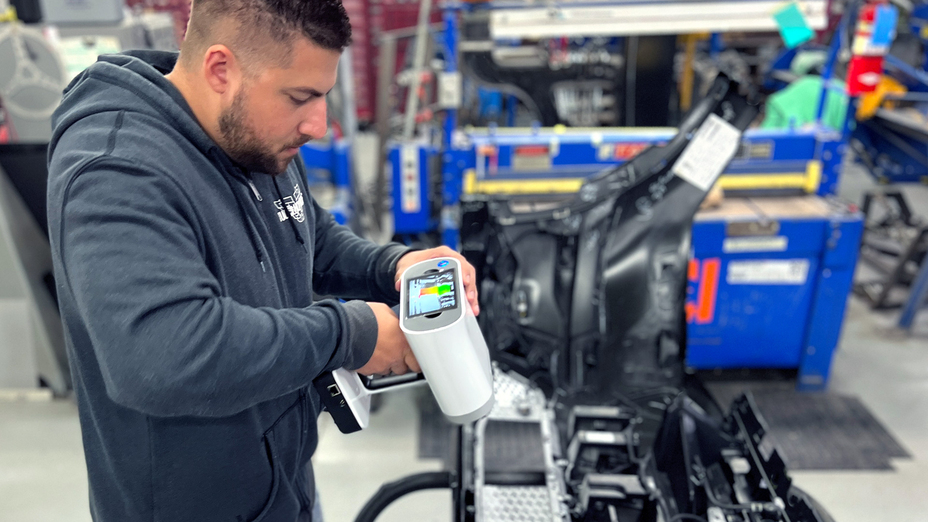
Tucci Hot Rods는 Leo의 내장형 디스플레이가 특히 유용한 기능이라는 것을 알게 되었습니다. 이미지 제공: Tucci Hot Rods
Digitize Designs의 Kyle Burdine은 "만족한 고객을 통해 맺어진 Tucci Hot Rods와의 협력을 통해 뛰어난 3D 스캐닝 전문 지식을 제공할 수 있었습니다. 평가 후, 우리는 Dom의 작업에 적합한 솔루션으로 Artec 3D를 추천했습니다. 자동차 개조 업계에서 높은 투자 수익률과 지속적인 혁신을 통해 이러한 관계의 이점은 분명합니다."라고 덧붙였습니다.
Artec Studio는 또한 회사의 생산성 향상에도 한몫을 했습니다. Tucci는 처음에 "스캔을 충분히 세밀하게 캡처하되 널리 사용되는 CAD 설계 소프트웨어인 Rhino 3D에서 작업할 수 없을 정도로 세밀하지 않게 캡처해야 하는 것“이 걱정이었다고 말합니다.
그러나 그는 이후 Digitize Designs의 안내에 따라 Artec Studio의 메시 단순화 기능을 사용하여 모델 복잡성을 줄이고 이 문제를 완전히 피하는 방법을 배웠습니다. 이제 이 프로그램을 사용하여 작은 다각형을 제거하거나 최대 편차 수준을 설정하거나 다각형 개수를 대상으로 하여 결과를 최적화하고 다른 플랫폼으로 내보낼 때 모델을 더 쉽게 관리할 수 있습니다.
Tucci는 "저는 Artec Studio에서 메시의 다각형 수를 줄이는 도구를 사용해 보기 시작했습니다. Rhino에서 이 작업을 시도할 때마다 충돌이 일어났습니다. 차라리 Artec Studio에서 작업하고 그것을 나중에 Rhino로 가져오는 것이 더 낫다는 것을 깨달았습니다.
저는 스캐너를 받기 전에 Artec Studio를 사용하고 특정 사물의 스캔 데이터를 처리하는 방법에 대해 몇 가지 교육 세션을 거쳤습니다. 이는 우리가 하는 일에 정말 효과적입니다."라고 덧붙였습니다.
자동차 3D 스캐닝 및 그 이상
Artec 3D 스캐닝으로 전환한 이후, Tucci Hot Rods는 모든 종류의 자동차 부품을 디지털화하여 개조 및 제작에 사용할 수 있도록 했습니다. 가장 먼저 스캔한 것은 1936년형 클래식 Dodge 트럭의 그릴이었습니다.
Tucci는 구성 요소의 복잡하고 볼록한 외부 모양으로 인해 기존 방법으로는 모델링하기가 특히 까다로웠으며, 초기 출력물은 앞면과 뒷면에서 0.64cm 정도 차이가 있다고 말했습니다. 차량의 해당 부분에 "오류의 여지가 많지 않았다"는 점과 그가 "정확히 들어맞는 것이 정말 중요하다"라고 말한 점을 고려할 때, 3D 스캐닝은 프로젝트의 필수 요소였습니다.
결국 이 회사는 스캔 데이터를 기초로 사용하여 자동차 그릴에 완벽하게 맞는 헤드라이트 커버를 3D 프린트할 수 있었습니다. 이러한 성공에 힘입어 Tucci와 그의 동료들은 1970년형 Mustang 머슬카와 1931년형 Model A 세단 등 빈티지 Ford를 맞춤 제작했습니다.
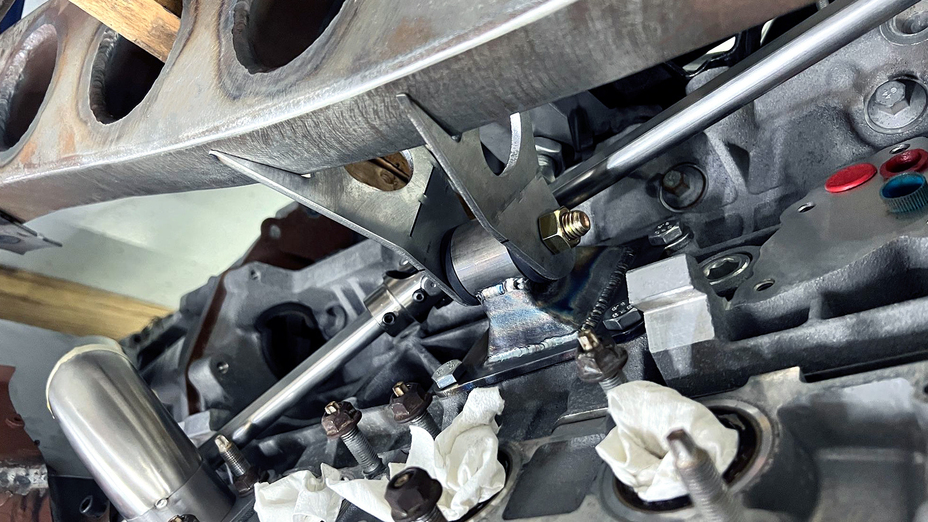
빈티지 Model A에 설치된 Tucci Hot Rods 맞춤형 모터 마운트 제작품. 이미지 제공: Tucci Hot Rods
Tucci는 "Model A를 맞춤형으로 제작하려면 이전에는 프레임 레일에 모터를 장착하고 모든 것을 골판지로 패턴화해야 했습니다. 3D 스캐닝을 통해 모터와 프레임을 제자리에서 캡처하고 모든 모터 마운트를 그린 다음 레이저로 잘라내면 모든 것이 딱 맞았습니다.
우리가 시간당 95~100달러의 인건비를 청구하고 각 자동차를 맞춤 제작하는 데 12~18개월이 걸린다는 점을 고려하면 약간의 시간 절약도 큰 도움이 될 수 있습니다."라고 설명했습니다.
Tucci Hot Rods의 포트폴리오는 계속해서 다양해지고 있으며, 최근 한 고객은 2022년형 Ford Maverick을 디지털화해 달라고 요청했고, 또 다른 고객은 클린룸을 캡처하기를 원했습니다.
뒤에 언급한 고객의 실리콘 웨이퍼 공장의 여러 층에는 기계와 펌프의 다층 배관을 연결하기 위해 콘크리트 타설 구멍이 뚫려 있었습니다. 다른 층으로 유출되는 것을 방지하기 위해 작은 연석을 설치해야 했습니다.
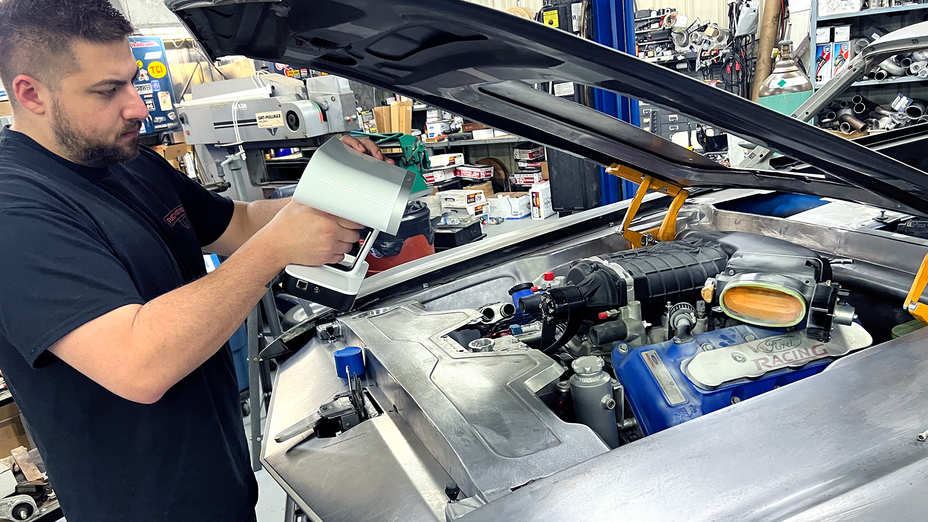
Tucci Hot Rods는 이제 비자동차 응용 분야에 Artec Leo를 도입하려고 합니다. 이미지 제공: Tucci Hot Rods
Tucci는 "우리는 각 파이프를 감싸면서 서로 고정시키는 플레이트를 개발했지만, 크기와 튜브, 통과 위치가 서로 다른 20개의 구멍을 스캔해야 했습니다. Artec Leo를 사용하여 모든 구멍을 캡처하고 레이블을 지정하고 모델로 처리할 수 있었습니다.
각 구멍마다 특별히 제작해야 하는 고유의 플레이트가 있었습니다. 3D 스캐너가 없었다면 이 프로젝트는 거의 불가능했을 것입니다."라고 말했습니다.
Tucci는 앞으로 자신의 회사에서 핫로드 측면에서든 다른 산업에서든 Artec Leo가 사업의 필수적인 부분이 되기를 바란다고 말합니다. Tucci는 그의 회사가 와서 무언가를 스캔해 달라고 누군가가 요청한다면 그러한 서비스를 제공할 수 있다고 결론 내렸습니다.
이야기 뒤에 숨겨진 스캐너
세계 최고의 휴대용 3D 스캐너를 사용해 보십시오.