포뮬러 1 자동차의 리버스 엔지니어링 및 소형 복제물의 3D 프린팅
목표: 두 개의 서로 다른 3D 스캐너로 Formula 1 자동차 전체를 스캔하여 위에서 아래까지 최고 수준의 세밀하고 빠른 속도로 자동차 캡처하기.
사용 도구: Artec Eva 및 Artec Studio
Artec의 3D 스캐너는 제품의 전체 수명 주기(PL) 단계에서 사용되는 필수적인 도구입니다. 프로토타입 제작에서 리버스 엔지니어링 또는 데이터의 품질 관리 분석을 위한 3D 모형 제작에 이르기까지 3D 스캔은 가장 빠른 작업 흐름을 달성하는 데 필수적입니다.
리버스 엔지니어링은 물체를 확대, 개선 또는 재생하기 위해 물체의 기술적 세부 사항과 구성을 캡처하는 것이 포함됩니다. 산업 엔지니어링, 자동차, 항공, 제조, 전자 제품 등과 같은 다양한 산업에서 사용되는 리버스 엔지니어링은 디지털 3D 복제물을 캡처, 분석 및 분해하여 초기 물체를 복제할 수 있습니다.
정밀한 결과물을 얻을 수 있고 사용이 쉬워 리버스 엔지니어링에 3D 스캐닝을 사용하는 것이 그 어느 때보다 인기가 있습니다. Artec의 3D 솔루션은 3Dat 속도로 물체를 캡처하는 기능뿐만 아니라 인상적인 정확성 모두 제공하며, 스마트한 후처리 소프트웨어인 Artec Studio 11은 3D 모형을 만들기 위해 대량의 데이터를 자동으로 처리할 수 있습니다. 또한 Artec의 3D 솔루션은 장치의 휴대성으로 인해 물체의 닿기 어려운 곳에 도달할 수 있으며 배터리 팩과 같이 사용하면 고정 전원이 필요하지 않습니다.
리버스 엔지니어링에 3D 기술을 사용한 좋은 예는 Artec의 영국 파트너인 Central Scanning과 CAD 및 CAM 솔루션의 주요 공급업체인 Delcam에게 자사의 F1 자동차를 약 300mm 크기로 3D 프린팅할 수 있도록 축소 3D 복제물을 제작해줄 것을 의뢰한 영국의 한 도구 제조업체가 시작한 이 프로젝트입니다.
이 자동차를 3D 스캐닝한 다음 수집된 데이터는 Delcam의 리버스 엔지니어링 소프트웨어 패키지인 PowerSHAPE에서 처리하였습니다.
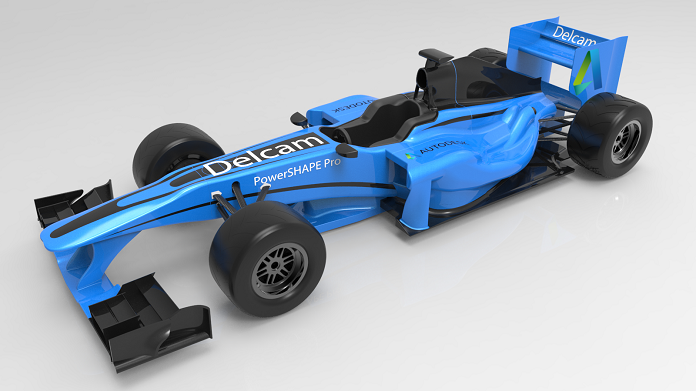
PowerSHAPE에서 완성된 F1 자동차의 모형
Central Scanning의 Paul Smith는 “이 스캔은 두 가지 유형의 스캐닝 시스템을 사용하여 이룰 수 있는 것을 알아보기 위한 테스트로 수행하였습니다”라고 말했습니다.
Steinbichler Comet L3D를 사용하여 자동차의 본체를 캡처한 다음 운전자의 조종석, 핸들, 위시본 서스펜션, 리어 스포일러, 사이드미러 및 Steinbichler Comet로 쉽게 접근할 수 없는 영역을 Artec Eva로 3D 스캔했습니다.
Paul은 “휴대성과 속도 때문에 Eva를 선택했고 마커를 추가할 필요가 없으며 그래픽을 쉽게 따를 수 있습니다”라고 말했습니다.
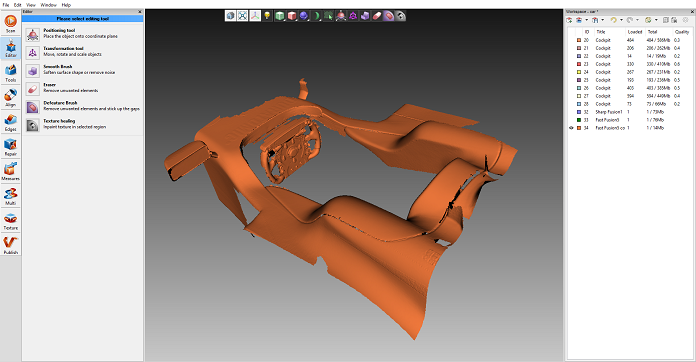
Artec Studio 10에서 조종석의 일부
이 자동차는 차주의 리셉션 영역과 작업장에서 3D 스캔하였습니다. 두 영역 모두에 안정적인 조명이 있었지만, 데이터 캡처에 영향을 미치기 때문에 직사광선은 없었습니다.
Paul은 자동차 부품을 더 쉽게 캡처하는 방법에 대한 몇 가지 조언을 했습니다.
그는 "그래픽이 있는 종이처럼 위시본 서스펜션 장치 뒤에 무언가를 추가하면, 스캐너가 텍스처를 추적하고 얇은 위시본의 형상을 캡처할 수 있습니다"라고 말했습니다..
위시본 주위에 약간의 어두운 탄소 섬유 영역이 있었습니다. 이러한 영역은 매우 가볍게 스프레이했습니다. 캡처를 쉽고 빠르게 하기 위해 스포일러 영역 주위의 빛 반사 또한 가볍게 스프레이하였습니다.
Paul은 “교정이 필요 없고 이러한 까다로운 영역에서 신속하게 설정하고 캡처할 수 있어서 Artec Eva를 사용하는 것을 좋아했습니다”라고 말했습니다.
대부분의 데이터는 처리를 빠르게 하기 위해 전역 등록 중에 표준 설정을 사용하고 텍스처 없이 처리하였습니다, Artec과 Steinbichler 빅데이터 세트는 그 후 PolyWorks에서 병합되었습니다.
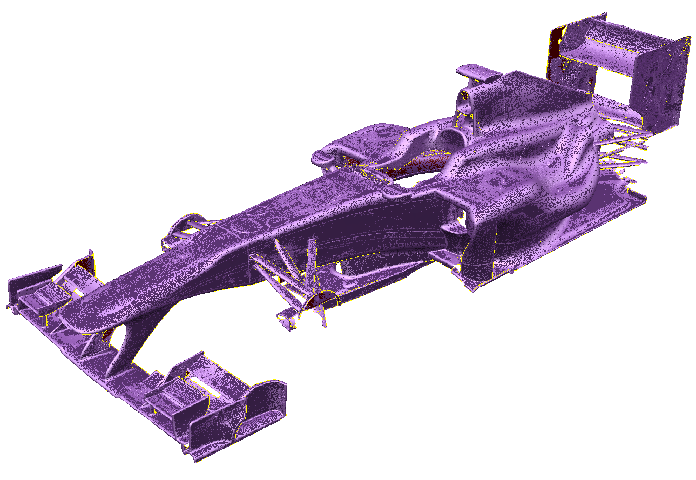
3D 데이터에서 생성된 메시.
그런 다음 약 850만 개의 삼각형인 완성된 250Mb STL 3D 모형은 Delcam에서 PowerSHAPE Pro를 사용하여 완전히 리버스 엔지니어링하였습니다. 복잡한 이중 곡면 영역은 표면 모델링에 가장 적합하였지만, 각기둥 모양으로 된 부분은 고형체를 사용하여 가장 효율적으로 만들 수 있었습니다.
Delcam의 James Slater는 “자동차의 앞뒤 수직안정판은 고형체로서 모델링한 것으로, 메시를 통해 단면을 가져와 압출한 다음 간단한 부울 연산을 사용하여 개별 조각을 병합했습니다. 이 작업은 실제로 프로젝트에 착수하기 전에 단 일주일만 훈련을 받은 여름 현장 실습 학생이 수행했습니다. 한편, 당사의 숙련된 엔지니어 중 한 명이 본체에 필요한 까다로운 표면 구조를 다루고 있었습니다. 최종 결과물은 다른 소프트웨어를 사용하여 만드는 것이 사실상 불가능한 완전히 세부적인 하이브리드 표면 및 솔리드 3D 모형이었습니다. 물론 모든 RE 프로젝트에서 가장 중요한 것 중 하나는 착수할 고품질의 정확한 메시를 갖는 것입니다”라고 설명했습니다.
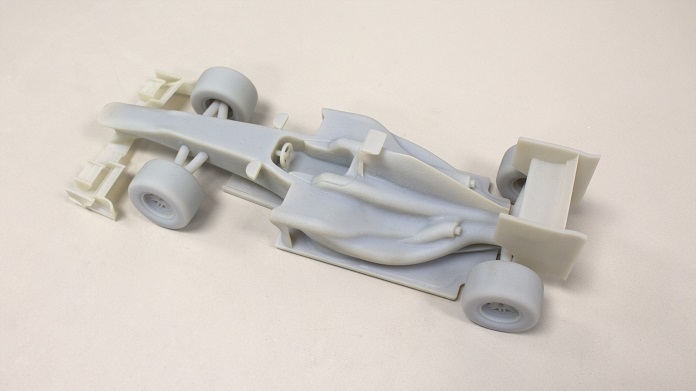
F1 자동차의 프린팅된 3D 복제물.
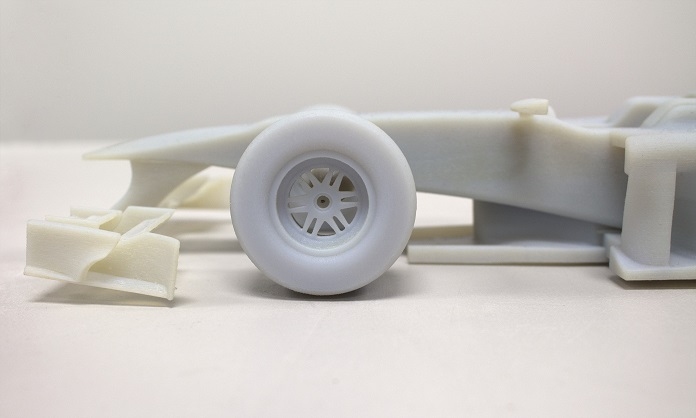
F1 자동차 축소 모형의 클로즈업.
이 자동차는 실치수로 드러났습니다. 일단 축소하고 나서 얇은 부분, 특히 위시본과 스포일러는 PowerSHAPE에서 두껍게 했습니다. 그런 다음 자동차의 디지털 복제물은 0.016mm의 인쇄 레이어로 Objet Eden 500V에서 3D 프린팅하였습니다.
이야기 뒤에 숨겨진 스캐너
세계 최고의 휴대용 3D 스캐너를 사용해 보십시오.