デジタルツインとは何ですか?
昨今、AIやVR、そして3Dスキャンなどの高度技術が製造業にますます統合されてきていますが、物理的世界と仮想的世界の境界線はかつてないほど曖昧になっており、現在私達は第4次産業革命の時代にいると言う人さえいます。この「産業 4.0」の改革で中核となるのは、パフォーマンスの追跡や改善に使用できる部品、物理的なアセット、システム、またはプロセスの仮想コピーである「デジタルツイン」です。こちらの記事では、これらのデジタルツインがどのように作成されるのか、どこに適用されるのか、そしてそれらが将来活用される可能性がある分野について説明していきます。
はじめに
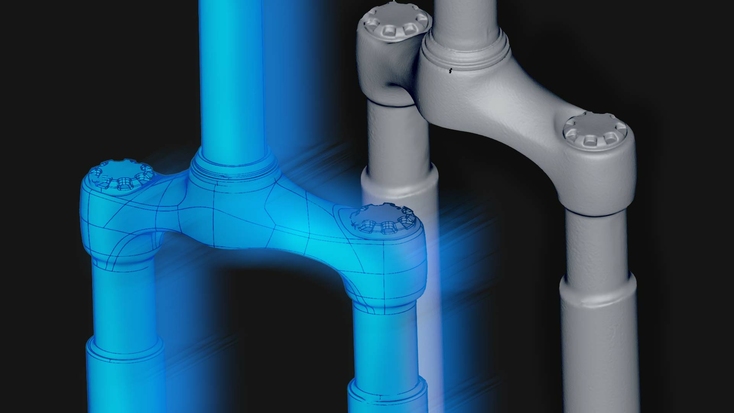
デジタルツインは単なる3Dモデルではなく、リアルタイムのデータフィードによって実際の部品や物理的なアセット、システム、プロセスに関連します。
デジタルツインは、製品の製造方法を変える可能性を持つ、新興技術の1つです。ここでデジタルツインの将来性についていきなり言及していく前に、まず「デジタルツインとは一体何なのか?」を把握しておきましょう。
基本的には、デジタルツインのコンセプトは、製品や機械、そしてより広範な設備などを仮想モデルに変換させるという考えが根本にあります。デジタルツインがデータアグリゲーション(DA)によって開発された場合でも、3Dスキャンなどの技術を使用してキャプチャされた場合でも、それらは単なるデジタルコピーではありません。実際、それらは取り付けられたセンサーを介して現実世界の人やものとデータ交換をします。このデータストリームには、生産段階にある生産物の状態から、機械的エネルギー出力に至るまでのさまざまな情報が含まれており、瞬く間に製造業者にとって非常に有益なものになりつつあります。
キーポイント
デジタルツインは、メーカーが特定のワークフローの改善を工場の現場で展開する前に、事前にそのテストを行うことを可能にしてくれます。
システムまたはプロセスのデジタルツインを使用すると、パフォーマンスのあらゆる側面を監視したり、最適化できる点を特定することができます。そしてこのデータを機械の維持管理や予防保守などの分野でも利用することで、失敗を未然に防いだり、ダウンタイムを削減できます。また、デジタルツインはメーカーが特定のワークフローの改善を工場の現場で展開する前に、小規模のシミュレーションを通してまずそのテストを行うことを可能にしてくれます。
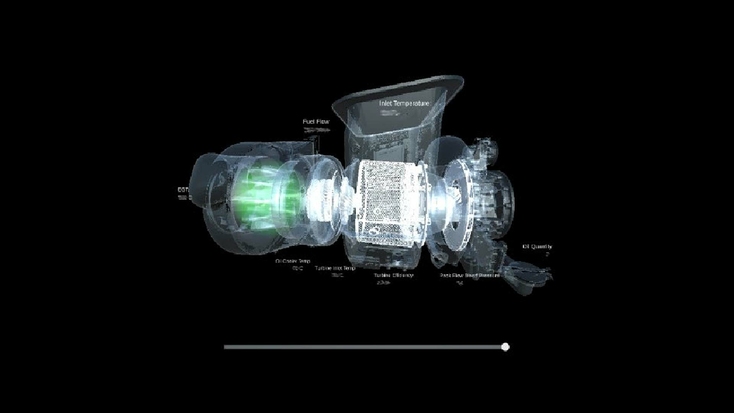
補助電源ユニット (APU)のデジタルツイン。画像出典: トゥエンテ大学
また、例えば複数の可動部品で構成されている、物理的なアセットが組み立てられた後の動作の様子を評価したい場合を思い描いて下さい。そういったケースでデジタルツインのシミュレーションを使用すると、この製品のコンポーネントがどのように相互作用するかを徹底的に調査したり、潜在的なデザインの改善点を特定することができるので、製品の研究開発部が試行錯誤を何度も繰り返すことはなくなります。
より大きな規模となると、都市計画にさえも同じアプローチを採用することが可能です。建設の持続可能性と市民の生活の質を向上させるために設計された実験的な都市景観が実際に建設された場合、建築家らはそれらが予測された通りにきちんと機能するかどうかを分析するためのしっかりとした基礎として、建設データを使用できるようになりました。
キーポイント
デジタルツインは、実際の物理的なアセットやシステム、プロセスの単なる3Dモデルではなく、リアルタイム のデータストリームによって接続されています。
今日私たちが理解しているデジタルツインの概念は、2002年にミシガン大学のマイケル・グリーブス(Michael Grieves)氏によって初めて発表されましたが、デジタルツインという名前は、その8年後に NASAのジョン・ビッカース(John Vickers)氏がこの用語を造語するまでは付けられませんでした。それ以来、この技術はニッチな(一般的ではない)製造分野から、世界のトップ産業技術トレンドの1つになりました。特にAIやAR、3Dプリントなどと並んで、完全に統合化された技術である「モノのインターネット(IoT)」の一部としてデジタルツインが機能する可能性は、メーカー達に期待を持たせています。
では、現実の世界でこれらすべてはどのように機能するのでしょうか? この記事の残りの部分では、デジタルツインの作成方法についてを詳しく説明してから、3Dスキャンがその作成プロセスの最適化にどのように役立つか、そしてその結果として得られるデジタルモデルが適用される様々な業界について言及していきます。
デジタルツインの種類
部品と物理的なアセットのデジタルツイン
製品のデジタルツインは、大きく分けて2つのタイプがあります。それは、部品 と物理的なアセットです。ここで言う部品とは、アセンブリ (サブアセンブリとも呼ばれる) のジョイントやビームなど、大規模なオブジェクトの最小で最も基本的な機能コンポーネントを指します。一方で、物理的なアセットというのは2つ以上のコンポーネントを含む製品のことであり、その相互作用はデジタルツインの仮想形式で分析されます。
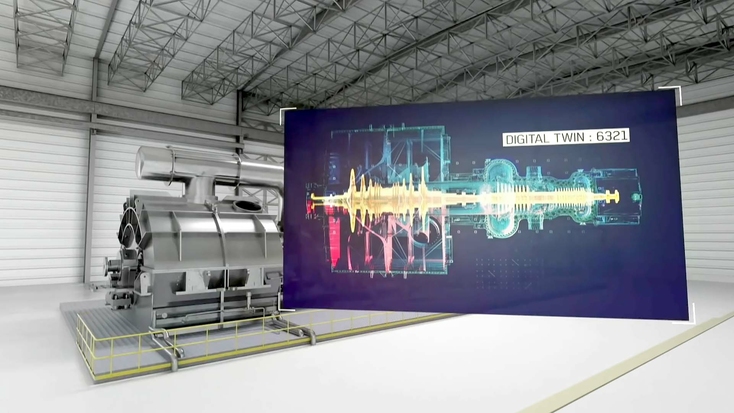
蒸気タービンのライフサイクルを延長させるために設計されたデジタルツイン。画像ソース: GE
システム用デジタルツイン
もう一段階大きいサイズでは、システムのデジタルツインがあります。これらのモデルは、完全に機能するユニットとして組み立てられた部品や物理的なアセット、またはそれらを製造するために使用された機械で構成されます。重要なのは、このデジタルツインのカテゴリを使用すると、ユーザーは 2種類の物理的なアセットがどのように相互作用するかを分析したり、パフォーマンスを向上させる上で求められる点を特定できるようになることです。
プロセス用デジタルツイン
デジタルツインをより広範囲に適用することで、工場全体のパフォーマンスの監視用に使用することもできます。これらのデジタルツインを使用すると、メーカーは生産関連のものや換気システムなどのファシリテーター関連のものでも、施設のすべてのシステムを同期化することができ、常に最高の効率での稼働を保証できます。またこれらは便利な計画ツールとしても機能します。たとえば、あるシステムが故障した場合、他のシステムにどのような影響を与えるでしょうか?
簡潔に言うと、プロセスチェーンをマクロレベルで把握することで、ユーザーは材料不足や機械メンテナンスの必要性などを事前に検出できるため、前もって計画をきちんと立ててシステムの稼働時間を最大化させることができるということです。
3Dスキャンはどこで登場しますか?
よって、これがデジタルツインの簡単な説明でした。しかし、3Dスキャンは正確にはどこに当てはまるのでしょうか? 現在、このテクノロジーは「リアリティキャプチャ」とよく表現されるデジタル化プロセスの一環として、そのようなデジタルツインの背景にあるモデルを作成するためのベストな方法の1つとなっています。
実際のキャプチャをまったく行わずに、デジタルツインのシミュレーションの実行に必要なデータを収集する計算論的モデルを開発することは可能ですが、そのためには数か月にも及ぶワークフローが必要となります。3Dスキャンはこれらの洞察に対応する、はるかに高速な手段を提供します。これは、部品からプロセスチェーンに至るまでのあらゆるものをそのままデジタル化することで実現でき、それらを即分析することも、完全に統合されたデジタルツインを作成するための基礎として利用することも可能です。
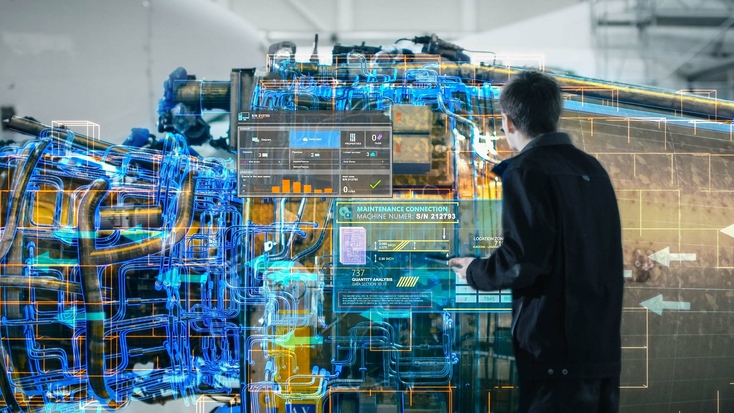
運用データとセンサーデータをリアルタイムで管理するために使用されているデジタルツイン
もちろん、その他にもリアリティキャプチャの技術は存在します。たとえばフォトグラメトリを使用すると、日常的に使用されているスマートフォンなどのデバイスで、複数の角度から撮影したオブジェクトの写真を重ね合わせてデジタルツインの作成ができます。ただし、このテクノロジーの精度はあまり高くなく、実行するには非常に時間がかかり、リアルタイムでのフィードバックを提供する傾向がないため、スキャンデータを取り損なう可能性が高くなります。
さらに、3Dスキャンは直線的な測定を提供しますが、フォトグラメトリは歪みの影響をより受けやすい傾向があります。これは、フォトグラメトリのテクノロジーが画質に大きく依存していて、その画質はカメラの解像度をはじめ、モーションブラーに至るまであらゆる影響を受ける可能性があるためです。後ほど詳しく言及しますが、精度は使用可能なデジタルツインを作成する上で非常に重要な前提条件なので、この点を考慮するとフォトグラメトリはデジタルツイン用ツールに適しているとは言えません。
キーポイント
3Dスキャンは、製品や設備を正確にデジタル化するための、より速く、より多用途な手段をメーカーに提供します。
それとは対照的に、LiDARスキャンは測量の分野でより大きな構造物をモデリングするための一般的で高精度な手段であることが証明されています。ハンドヘルド型3Dスキャナも非常に多用途で、キャプチャしたデータをキャプチャの実行中に既に確認できるように内蔵ディスプレイを備えたものもあります。これらのデバイスは非常に効果的なので、スキャン結果はCADやBIMモデルの基礎として使用でき、最終的にはデジタル ツインの作成に使用できます。
結論として、3Dスキャンの進歩により、3Dスキャンは製造に関する洞察を得て、デジタルツインの作成プロセスを加速するためのより魅力的な手段となっています。しかし、このテクノロジーの初心者にとって、最初のデバイスを購入する際に考慮すべき主な差別化要因には何があるでしょうか? これらの要因いくつかを詳しく見てみましょう。
Artec Ray II
遠隔監視を可能にする工場や不動産の内部など、広範囲のデジタルツインを計画する際には、その範囲をきちんと考慮する必要があります。三脚に取り付け可能なArtec Ray IIを利用すると、10mからの距離で1.9mmという3Dポイント精度で、最大130m離れた場所から表面を迅速にキャプチャできます。内蔵ディスプレイとこの精度のおかげで、スキャンと工場の実際のスペースのサイズとの間の偏差を最小限に抑えたい場合や、目的に合うデジタルツインをスキャン結果から得たい場合にはArtec Ray IIが最適です。
施設を細部まで忠実に再現するには、ハンドヘルド型デバイスで複雑な部品をスキャンし、そのデータをArtec Ray IIでキャプチャしたデータと組み合わせる必要がある場合もあります。 その作業は、Artec Studio内で実行が可能です。このプラットフォームは、点群データ(未加工の、もしくは前処理された)を位置合わせし、総合的にグローバル位置合わせを実行するプロセスを合理化し、驚異的なレベルの高解像度と精度で3Dモデルを作成します。
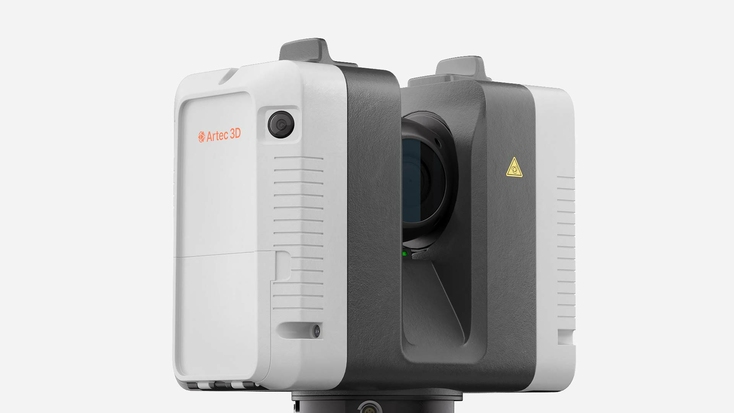
Artec 3Dの超高速の長距離用3Dスキャナ、Ray II
どの業界でも採用できるこのプロセスは、作業場から機械で満たされた倉庫に至るまで、ありとあらゆるものをデジタル化できることを意味しますが、そこから得られる利益は同じです。生産パフォーマンスをリアルタイムで追跡することで、潜在的なボトルネックが設計上の欠陥によって引き起こされたものであるか、後になって製造上の欠陥によって引き起こされたものであるかにかかわらず、可能な限り早期に潜在的なボトルネックを特定し、対処することができます。
相性抜群のコンビネーション:Ray II + Leo
プロセスではなく、物理的なアセットのデジタルツインを作成する場合は、スピードと操作性がより重要な差別化要因になるでしょう。AIを導入したコードレス型のArtec Leoは、まさにその2点をクリアしており、ユーザーは内蔵された5.5インチのディスプレイを介してスキャン中の進行状況をモニターチェックしながら、HDモードを使用して1秒あたり最大3,500万ポイントの速度でデータキャプチャを行えます。
Leoは速度のために解像度を犠牲にすることはなく、ユーザーはHDモードを使用することで小~中型オブジェクトのクリーンな高解像度スキャンを従来より簡単にキャプチャできるようになります。これらすべての機能により、Leoは製品の複雑な部分をしっかり再現してデジタルツインを作成するには最適です。
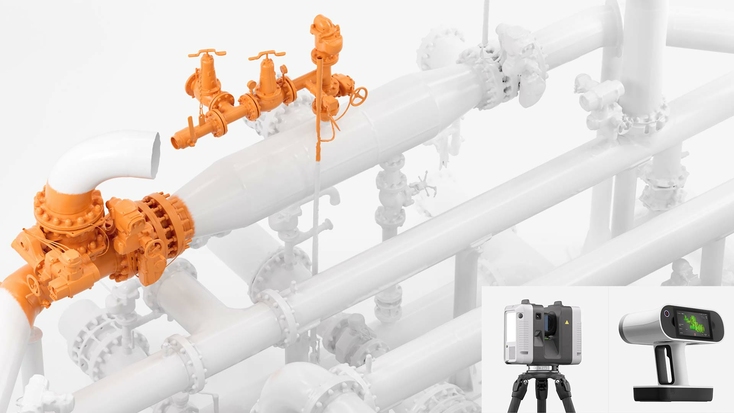
パイプネットワークの細やかなデジタルツインの作成にArtec LeoとRay IIを併用
物理的アセットが特に小さい場合は、Artec Microを使用してデジタル化するオプションも考慮すべきです。Artec Microは最大10ミクロンの精度でオブジェクトをキャプチャできるため、このデバイスを使用すると偏差を僅かなレベルに抑えてねじやサブアセンブリ部品などのモデルを開発できます。これは、後に詳しく言及しますが、デジタルツイン作成の上で信頼性の高い基盤づくりのために不可欠です。
寸法許容差
デジタルツインが生産パフォーマンスの測定における効果的なツールであるためには、まずデジタルツインが正確なデータにきちんと基づいていなければなりません。その理由は、測定に誤りがあると、結果として得られるワークフローの分析を不正確にしてしまうからです。幸いなことに、現在では実際に使用可能なデジタルツインのモデルを作成するために必要なレベルの精度を提供してくれる3Dスキャナがいくつかあります。
小~中規模のデジタルツインの開発を検討している場合は、構造化光3Dスキャンが最適です。工業用のファスナーやバルブなどのより複雑な部品をキャプチャする場合は、その有効性はおそらく寸法公差のレベルに依ります。 寸法公差とは、設計どおりにきちんと機能する部品が許容できる偏差の量のことです。
そういったスキャンの有効性を保証する技術は、 Artec Space Spiderのようなハンドヘルド型でメトロロジーグレードの3Dスキャナに確かに存在します。このスキャナは、小さく複雑なオブジェクトだけでなく、大型オブジェクトの部分的なパーツの作成もでき、その際発生する誤差は実際のサイズからわずか0.05mmのみです。
データ処理
デジタルツインにおける、見落とされがちですが重要な側面は、データ処理です。スキャンが完了したら、その結果のデータを確認して他のプラットフォームにエクスポートできる速度と容易さが、ワークフローの効率にとって極めて重要になります。実際には、これは重要な画像データをキープしながら、産業分析で一般的に使用されるプログラムと互換性のある形式でファイルを転送できることを意味します。
キーポイント
適切な3Dスキャン用ソフトウェアを使用すると、製品やシステム、または領域を迅速にキャプチャし、そのスキャン結果の3Dメッシュをデジタルツインのプラットフォームに直接エクスポートできます。
デジタルツインの作成に3Dスキャンを採用する場合、そのプラットフォームの使いやすさも考慮すべきでしょう。Artec Studioは、この点で実に本領を発揮します。このソフトウェアは、キャプチャしたデータを完全に再作成された仮想領域または製品のレプリカに処理し、STEPやIGESなどの形式でのエクスポートを可能にするだけでなく、そのプロセスを合理化します。
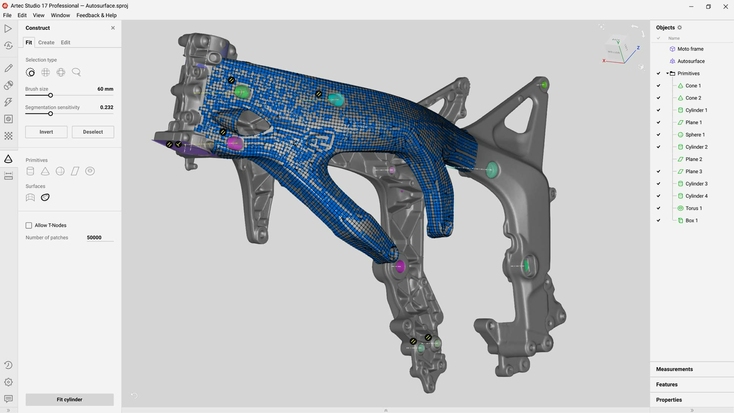
Artec Studioのオートサーフェス機能は、ワンクリックで有機的な形状をCADモデルに変換します
いくつかの簡単な質問に答えるだけで、Artec Studioの自動モードは、特定のデータセットを処理するための適切なアルゴリズムを選択してくれます。これにより、スキャンに挑む新しいユーザーがこのテクノロジーをすぐに理解し、スキャン・トゥ・メッシュのワークフローを自動化することができます。逆に、このプラットフォームの設定をいろいろ試してみたい場合は設定変更もできます。このプラットフォームは最大5億ポリゴンのデータセットを処理できるため、ほぼすべてのオブジェクトまたは領域のスキャンを処理することができます。
デジタルツインの開発方法
デジタルツインは、膨大なデータセットを使用して構築することも、物理的な領域やオブジェクトの3Dスキャンをもとにして構築することもできます。しかし、これらのプロセスは実際にはどのようなものになるのでしょうか? データをもとにしたアプローチは、物理的なアセットや、エンタープライズリソースプランニング (ERP) システム、そしてCAD設計のスケッチ等のドキュメントやファイルによって生成されたデータでトレーニングされたアルゴリズムに依存する傾向があります。このデータを使用すると、このようなデジタルツインは入力と出力の間の関係を浮彫りにし、それらの結果をもとに本番での稼働状況を予測できます。
それに比べて、リアリティキャプチャによるデジタルツインの作成はより簡単です。Ray IIなどの三脚型スキャナを用意するだけで、工場のフロアを自動的にスキャンすることができますし、Leoなどのハンドヘルド型スキャナを使用すれば、小~中型の製品をあらゆる角度から迅速にキャプチャできます。そうすることで、あらゆる物体や構造をデジタルモデルに変換することが容易になります。これは、実際にきちんと機能するデジタルツインにとって不可欠な前提条件です。ただし、スキャン対象物が更新された場合、再スキャンが必要になることもあります。
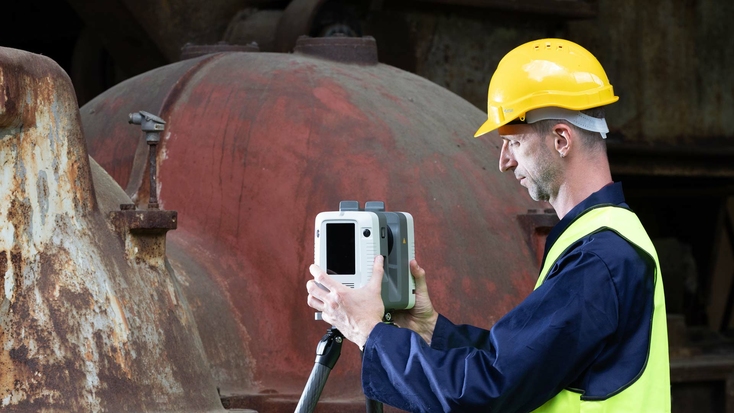
Artec Ray IIをセットアップして、大型の屋外コンテナのデジタルツインを作成するエンジニア
場合によっては、これら2つのアプローチを組み合わせ、両方の長所を活用することでハイブリッドツインを作成することも可能です。オブジェクトをデジタル化する方法のうち、どれを選択するかは前述したアプリケーションに特化した要素(キャプチャに必要な精度、速度、スケールなど)に大きく依存します。ただし、3Dモデルを作成したら、それでプロセスは終了するわけではありません。実物のモデルにセンサーを取り付け、データリンクを確立する必要があります。
先程と同様に、これらがどこに接続されるかはアプリケーションによって異なります。モデルの中には生物や特異なタイプ、熱を持つものや可変的なものもあり、それぞれが機能するには異なるデータ入力が必要となります。同様に、データからデジタルツインを構築する場合にこれらのデジタルツインを最大限に活用するには、分析とシミュレーションプログラムに投資するか、データサイエンティストの導入を検討する価値があります。
デジタルツインはどのように機能しますか?
デジタルツインは、実際の製品やシステム、プロセスにそっくりな見た目をしているだけでなく、それらと同じように機能しなければなりません。これには、デジタルツインのモデルとなった実物のパフォーマンスをリアルタイムで監視および分析できるよう、デジタルツインを実物にリンクさせる必要があります。
これらの接続は、製品のパフォーマンスが重要な領域にセンサーまたはアクチュエータを取り付けることによって確立され、製品やデジタルツイン、および導入されている製造実行システム (MES) の間でデータが相互に共有されます。この絶え間ない情報の流れのおかげで、プロセスの改善点を特定できたり、システムの動作状況を監視できるので、メーカーにとってこれは非常に有益です。
製品がバッチ製造段階に入る前に、ユーザーはこのデータストリームを展開して、製品が生産中にどのように動作し、最終的なユースケースで実行されるかを評価することもできます。そうすることで、デジタルツインのユーザーは物理的にプロトタイプを作成しなくても設計を繰り返すことができるので、材料の節約にもなり、製品をより迅速に市場に投入できるという利点があります。
デジタルツインと「モノのインターネット(IoT)」
続いては、デジタルツインがどのように機能するかに言及します。ではまず、デジタルツインを導入するとどんなメリットがあるかを見てみましょう。最も注目を集めているユースケースの1つは、モノのインターネット (IoT) を中心に展開しています。IoTとは、相互接続された電子デバイスの一式を表す、現在幅広く利用されている用語です。製造業界では、今まで長い間IoTのセットアップの傾向が予測されてきましたが、なぜそれがこの業界にとって有利なのでしょうか?
まず、ワークフローを統合すると、特にAIが導入された場合により大規模な自動化が可能になります。これにより、製品の操作に必要な人的入力の数が減り、生産性が向上すると同時に、生産品質に多大な影響を与えうるエラーのリスクを最小限に抑えられます。履歴データに基づいて、リソースをより有効に活用できる方法でクライアントの需要を満たすため、IoTのセットアップのスループットを下げたり上げたりすることも可能です。

デジタルツインのセットアップとして、農業を自動化するAI搭載の機械を用いたコンセプトを表す画像
一方、これから長期的には、特定の施設内のすべての機械をIoTネットワークに接続することで、潜在的なビジネスチャンスが訪れるのではと期待されています。人間のオペレーターへの依存が軽くなるにつれて、完全に自動化された「消灯」施設が出現する可能性も高まってきています。さらに、消費者の好みについて今まで以上に多くの情報が入手できるようになったことで、IoTのワークフローはそれを実行する人々に新たなトレンドを即活用する手段を提供します。これらすべては、デジタルツイン市場がいかに巨大であるかを表します。
キーポイント
デジタルツインや3Dスキャン、VR、そしてAIなどの高度技術の台頭により、完全に相互接続されたモノのインターネットのワークフローを作成することが可能になりました。
デジタルツイン用のソフトウェア
さて、理論上のデジタルツインの仕組みはご紹介いたしましたが、実際にデジタルツインはどのように開発・展開されるのでしょうか? 3Dモデルをデジタルツインに変換させ、その際に必要となるワークフローを最適化する支援を提供する、主要なプラットフォームのいくつかを見てみましょう。
Oracle IoT Asset Monitoring Cloud Service
ソフトウェア開発の大企業であるOracleによるデジタルツイン専用のAsset Monitoring Cloud Serviceを使用すると、ユーザーは物理的なアセットの使用状況や場所、そして全体的な状態を綿密に監視することができます。プラットフォームを使用開始する際に必要なのは、デジタルツインを構築できるデータセットもしくは3Dモデルだけです。これは、JSON形式のメタデータや、OBJ形式の一般的なモデリングファイル、そしてAutocadやSketchupなどの広く利用されているプログラムによって作成された形式のいずれかになります。
モデルをアップロードすると、Oracleユーザーはこのソフトウェアを利用して検査や位置決めを行うことができ、必要に応じてアセットをより細かく分割することができます。その後、ボタンをひとつクリックするだけでノードをこれらのサブアセットに接続できるようになります。ただし、パフォーマンスに関するライブデータを収集するには、実物のオブジェクトの関連領域にセンサーを配置する必要があります。
Oracleによると、ユーザーはそのプログラムを使用することでVirtual TwinやPredictive Twinなどを含む数種類のモデルを作成したり、Twin Projectionをチェックできるそうです。Virtual Twinは基本的にセマンティクス主導のデータモデルを使用して、観察された属性値と必要な属性値がどのように相互するかを比較します。Virtual Twinをフォークリフトなどの工場車両用に使用すると、ブレーキの磨耗やタイヤの磨耗、またはアームの長さを監視し、目的に適合しているかを確認できる便利な方法になります。
その一方で、Predictive Twinは、機械学習によって開発された分析や統計モデルに依存しており、工場現場の変化する状況に常に適応します。つまり、ライブデータを使用してアセットやシステム、そしてプロセスのパフォーマンスを監視し、最終的にはそれらの傾向や問題、解決策、さらには将来のメンテナンスのニーズを特定するのに役立ちます。Twin Projectionを使用すると、企業はその調査結果に基づいてなにかを構築したり、修復のワークフローを導入することができ、さらなる分析が必要な場合は他のOracleプログラムにそれらをエクスポートできます。
Amazon AWS IoT TwinMaker
Amazonと工業製造と言うと、あまりピンとこないかもしれませんが、AWSの子会社はクラウドサービス分野で確立されたプレーヤーです。AWSによると、このIoT TwinMakerのプラットフォームを使用すると、ユーザーは既存の3Dモデルを実世界のデータと組み合わせることで、産業機器から生産ライン全体まで、あらゆるもののデジタルツインを作成できると主張しています。
AWSの3Dモデルインポートガイドによれば、一般的に3DスキャンのプラットフォームからエクスポートされるOBJ形式などのファイルは、TwinMakerに互換性のあるGLTF形式に簡単に変換できるようになったそうです。そうすることで、プログラムの読み込み時間の短縮や、画面上のデジタルツインの表示でモデルやシーンが更新される方法を合理化するなど、他の面でも有益であると言われています。
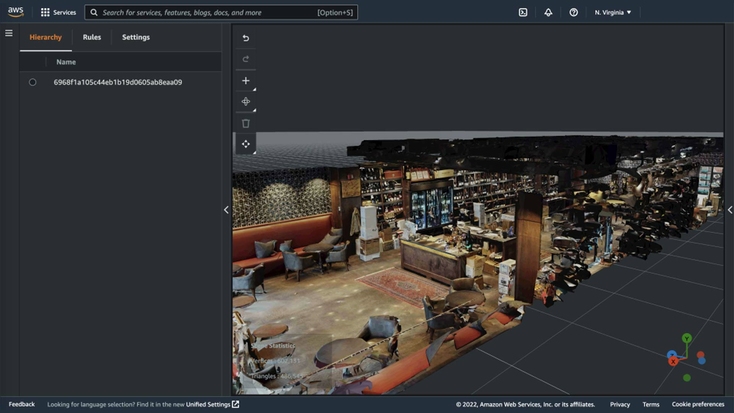
AWS IoT TwinMaker上に表示される、とあるプロセスのデジタルツインの例。画像ソース: Amazon, AWS
ユーザーはデジタルツインを準備し、それを現実世界に存在するアセットに接続させた後、AWSに組み込まれた分析ツールを展開して、本番のワークフローの全体的な流れを取得したり、AWSのパートナーによる分析ツールを使用したりできます。そのパートナーとは、SiemensやAnsysなどの知名度の高い産業用ソフトウェア開発会社が含まれます。Ansysは、独自のDigital Twin Builderを販売しており、アセットやシステム、プロセスのアップグレードの完全な仮想プロトタイプのテストを実現し、リスクが伴う実践を回避させてくれるという非常に便利なソフトウェアツールを提供しています。
Autodeskによるデジタルツイン
3Dソフトウェアの分野におけるもう1つの主要企業であるAutodeskもデジタルツイン用ソフトウェアを提供していますが、その製品は主に建設部門のみを対象としています。ビルディング インフォメーション モデリング (BIM) に互換性を持つプログラムの開発者であるAutodeskのノウハウに基づいて構築されたデジタルツインの使用で、ユーザーは設計や運用、建設データを統合できるようになります。これにより、新しいインフラを構築する方法や、それを地域に最適に統合させる方法について意思決定を行う際に、より多くの情報に基づくことができます。これはリスクを測定して軽減させたり、資本支出を最適化し、設備のメンテナンスが可能な限り効率的に実行されるようにすることで、ROI(投資利益率)を向上させることにも繋がります。また、このプラットフォームとAutodeskの他のプログラムとの統合により、ファイルの相互互換性が向上し、デジタルツインをさらに加速させる起爆剤にもなります。
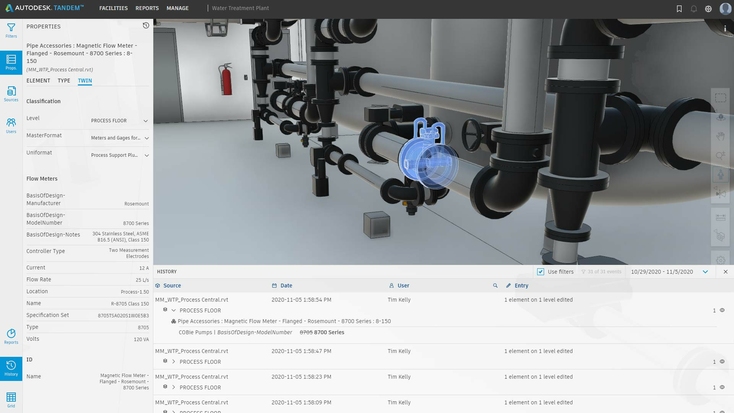
Autodesk Tandem上に表示されている電磁流量計のデジタルツイン。画像ソース: Autodesk
最後に、建設データを継続的に蓄積して分析することで、データ量が多いほどより多くの情報を得ることができるため、こういった分析はユーザーが投資意志決定を改善したり、計画の上で発生するニーズを予測したり、損失を予測するのに役立つはずです。おそらく、これは現在市場に出回っている他のプログラムのユーザーにも言えることですが、特に支出が過剰になりやすいプロジェクトの構築では、これらのメリットはより明るみになります。
キーポイント
多くのプラットフォームは一般的な3Dスキャンファイルの形式と互換性があり、これらをエクスポートしてデジタルツインに構築させることは従来より簡単になってきています。
デジタルツインの用途
製造
製造分野に適用されるすべての技術の中で、デジタルツインは今最も注目を集めています。製造現場では、デジタルツインを用いてリアルタイムのデータをもとに現場でのパフォーマンスを向上させるために必要となる点を発見したり、シミュレーションを通して製品の品質を確保したり、ダウンタイムを削減するための予知保全の計画を立てることができます。このプロセスがメーカーのリソース管理に役立っていることを示すもうひとつの例は、仮想倉庫を介するものです。3Dスキャンは、製品や予備品をデジタル化する完璧な手段を提供します。
デジタルツインは、データ収集の基盤となるだけでなく、スペアパーツや製品のデジタルデータベースを作成するためにも利用できます。そういったデータベースにより、製造現場でのメンテナンスのニーズやクライアントの需要の急増にも対応できる、オンデマンドでの製造が可能になります。デジタル化が進むと、メーカーが手元に持つ在庫が少なくなるため、倉庫コストも削減されます。この点を念頭に置くと、この技術は製造業者に短期的にも長期的にも経済的利益をもたらす可能性があるため、製造業者の間で人気が高まっていると言えます。
自動車
工業製造業で見られる利点の多くは、自動車産業でも同じように見られます。たとえば、新しい電気自動車や自動運転車のプロトタイプが本格的な生産段階に入る前に、コストがかさむ試行錯誤をなるべく減らすために、シミュレーションを通してその設計を仮想的に検証できるようになりました。しかし、このテクノロジーに自動車産業特有の利点がないわけではありません。
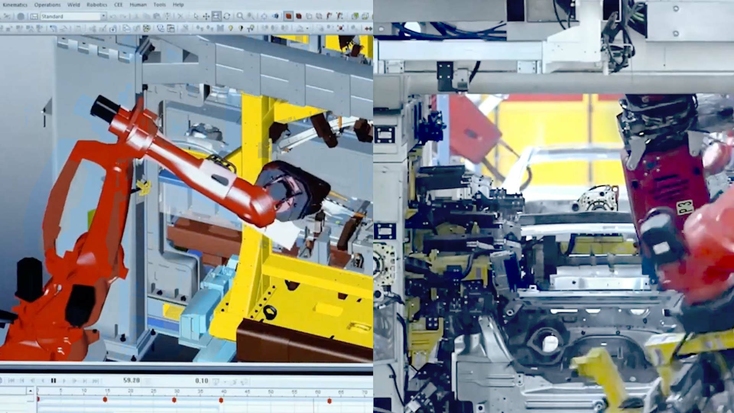
自動車生産ラインのデジタルツイン。画像ソース: Siemens
ほとんどの自動車は、複数のロボットアームが連携して部品の組み立てや溶接、コーティング、塗装などの作業を伴う、非常に複雑なワークフローを介して製造されています。デジタルツインを使用すると、プロセスを稼働させる前にサイクルタイムと生産性を最適化しながら、これらの可動部品がどのように結合するかをシミュレーションすることができます。このようなデジタルツインは、製造のモジュール化にも役立つため、自動車会社は要求に応じて限られた数のカスタム車を製造するために、システムの動作方法を変更することができます。
さらに、最終的なパフォーマンスチェックにデジタルツインを使用することで、メーカーは車両が現実に起こる状況でどのように機能するかをテストできます。実際、自動車大手企業のルノー(Renault)では、現在、ロードカー(一般公道を走る仕様の車)は生産段階に入る前に、風洞試験や衝突試験までのあらゆる検査を受けています。これにより、ルノーはエンジン出力や空気力学、ギア管理などの点でのパフォーマンスを確信し、抜かりのない状態にしています。
航空宇宙
デジタルツインが最初にNASAによって命名されたことを考慮すると、このテクノロジーは当然ながら航空宇宙用途でも、主に研究開発において必要とされています。飛行準備が整った部品には非常に細かい公差があるため、重大な故障を防いだり、航空機の寿命を延ばすためには、正確なシミュレーションが不可欠となります。デジタルツインは、メーカーが履歴データに基づいて部品がどんな場合に故障するかを予測できるようにすることで、このプロセスを促進します。
これと同じことは宇宙産業にも言えます。NASAは長い間、軌道上で発生する障害を診断し、修正するために、国際宇宙ステーションに搭載された実際のコンポーネントの仮想表現を使用してきました。近年では、この技術によって衛星を強化させる可能性が研究対象の的となっています。研究開発がさらに進めば、デジタルツインの使用で、複数の衛星群を単一のユニットとして運用できる日がいつか来ると考えられています。これにより、軍事レベルでの防衛調整だけでなく、テレビや携帯電話の信号通信にも応用できる、真に統合された衛星ネットワークの構築が実現する可能性もあります。
キーポイント
デジタルツインのルーツは航空宇宙産業にあり、衛星群の統合に関する使用に期待されています。
航空宇宙以外では、 NASAによるハイブリッドリアリティトレーニングプログラムを通して、宇宙飛行士達が他の惑星での作業の準備で、3Dスキャンはどういった支援ができるのかを示しています。NASAは、Artec EvaとSpace Spiderを活用したことで、いくつかの高度なツールのデジタルツインを作成することに成功し、将来の地球外ミッションでの展開に備えています。これらのデバイスは非常に現実的に複製されているため、NASAの士官候補生はVRでそれらを物理的に使用する方法を学ぶことができます。
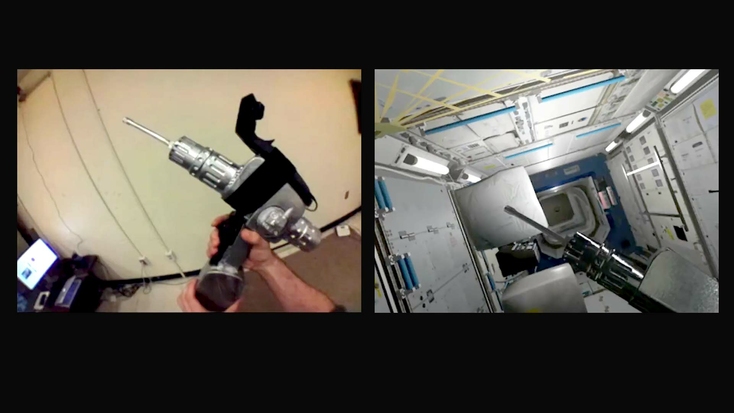
宇宙で使用するために設計されたツール (左) とそのデジタルツインのシミュレーション(右)。画像ソース: NASA
ヘルスケア
デジタルツインについて考える際、ヘルスケア分野はまず最初に思い浮かぶ業界ではないかもしれませんが、デジタルツイン技術はこの分野で今注目を集め始めています。ヘルスケア業界では、製品のパフォーマンスを最適化するためではなく、プロセスに使用される傾向があります。病院では、病床のキャパシティやリソース、ケアモデル、そして患者の安全性のバランスをとることが随時求められるため、デジタルツインはスケジュールやベッド、手術室の使用状況をリアルタイムで監視できる利点を提供します。これにより、マネージメント側はそういった情報に基づいた意思決定が容易に行えます。
将来的には、デジタルツインを人体のモデルにも適用できたり、医師が患者の個々の解剖学的構造をより深く理解できるようになることが期待されています。この洞察から、最終的にはそれぞれの患者固有の治療法を開発できる可能性もありますが、そのためにはまだ超えなければならない壁があります。これらのモデルを作成するために必要なデータを取得するには、継続的な生理学的検査が必要ですが、それらは侵襲的検査であるため、(現時点では)実行不可能となっています。
とはいえ、3Dスキャンは臨床医が人体への理解を深めるための支援ができるという有望な兆候はすでにあります。たとえばモンペリエ医科大学では、学生達はArtec Space Spiderを使用して作成されたデジタルツインを満載した、VRのシミュレーションで訓練を受けています。写真のように現実的なこれらのモデルを使用すると、高額な上に入手困難な死体に頼らず手術を練習できるようになります。間違いなく、このようなプロジェクトから得た学びや経験も、患者の完全なデジタルツインの実現に向けて前進となっているはずです。
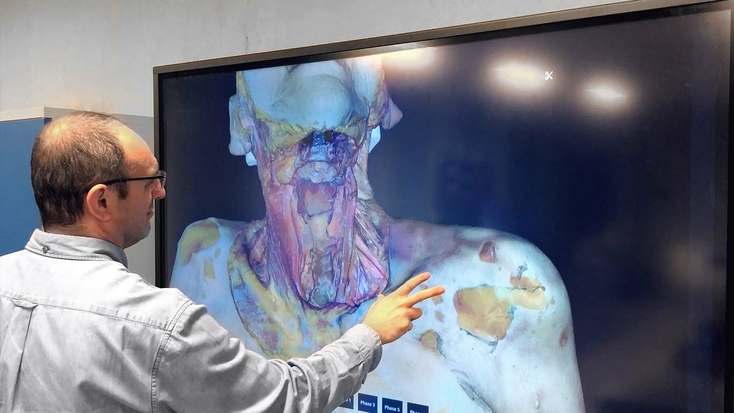
医療トレーニング用に設計されたデジタルツインを操作するギョーム・キャプティエ(Guillaume Captier)教授
建設
製造施設でのデジタルツインの作成と並んで、Artec Ray IIのようなレーザースキャナもまた、建設現場でのモデリングの一般的な手段となっています。このような長距離用デバイスを使用すると、大規模な建築現場をキャプチャしてライブモデルを作成することができ、プロジェクトの設計者は構造物を仮想的に操作できるようになります。これにより、リソースの管理と利害関係者のコミュニケーションは合理化され、情報に基づいた意思決定が容易になります。
キーポイント
Ray IIのようなレーザースキャナを使用すると、ユニークな建設計画の洞察を引き出してくれるデジタルツインの作成が可能になります。
建設ワークフローへの統合を容易にするこのデジタルツイン技術のもう1つの側面は、デジタルツインプラットフォームとCADおよびBIMモデル(この分野で特に人気のあるツール)との強力な互換性です。製品製造と同様に、これらの構造モデルのさまざまな領域にセンサーを取り付けることで暖房や換気、そして空調 (HVAC) をどのように組み込むかを計画したり、それらの進行状況を監視できます。
デジタルツインが直面している課題
上記では、デジタルツインが直面している、それぞれの用途に特化する課題についていくらか取り上げましたが、それらの用途全体に共通する課題を考慮することも重要です。デジタルツインの使用における最大の障害は不正確性です。モデルとオブジェクトの間に大きな偏差があると、結果として得られるデータと分析に歪みが生じてしまいます。
メトロロジーグレードの精度でオブジェクトを確実にキャプチャし、可能な限りベストなデジタルツインを得るには、Space Spiderのような精度重視のスキャナを使用することです。構造化光スキャンや3Dレーザースキャンは、デジタルツイン導入の際にもう1つの重大な障壁となっているコストを克服するのにも役立ちます。他のデジタルツインのインフラと並行して、従来のイメージングテクノロジーに投資するとなると、100万ドル以上も費用がかかってしまう可能性があります。
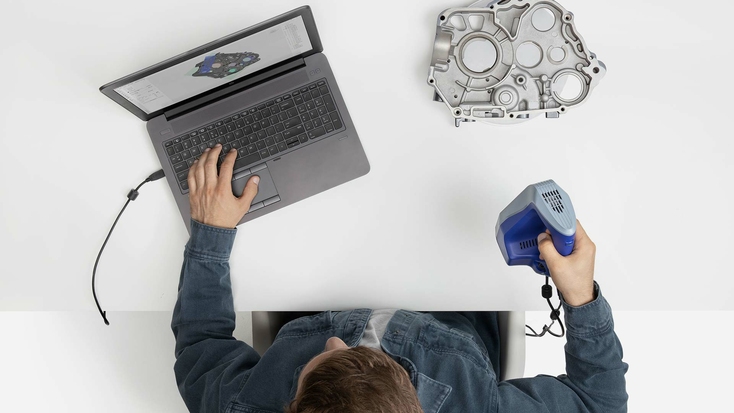
複雑な金属コンポーネントのデジタルツインを作成しているArtec Space Spider
ハンドヘルド型で軽量、そして持ち運びやすいスキャナのArtec Evaや画期的なArtec Leoはそれと対照的に大変お手頃価格となっており、ユーザーのニーズの進化に合わせて機能をアップグレードしています。
次の課題は、データの標準化が欠如している点です。もちろん、デジタルツインを構築するには相当な量のデータが必要となりますが、そのすべてに簡単にアクセスできるわけではありませんし、さまざまな形式で提供される可能性があります。同様に、デジタルツインの有効性の度合いは、それが適用される場所や、データ収集を行う間にどれほどステップがあるかなどの要因に応じて異なります。
これらの要因により、デジタルツインの利点を正確に評価するのは困難になることがあります。ただし、Artec Studioのようなプラットフォームを使用すると、広く大衆に受け入れられている形式でモデルをエクスポートする前に、モデルデータの処理を自動化してデータキャプチャの合理化・高速化が可能になります。
キーポイント
3Dスキャンの進歩により、デジタルツインのプロセスは加速し続け、より多くの新しい業界での採用が促進されていきます。
デジタルツインの未来
デジタルツイン技術が今まで主流であった製造や施設、都市計画のワークフローを削除する前に、克服すべきいくつかの障壁があることは明らかです。ただし、デジタルツイン技術が生産スループットと再現性の向上、およびより広範な計画アプリケーションにおけるプロセス効率の向上を実現できることはすでに実証されており、現在も研究開発が行われています。
デジタルツインの作成はますます容易化し、その機能も向上しており、近い将来にIoTのセットアップの一部として積極的にデータを調達できるようになるかもしれません。この進歩は、より高機能かつ多用途でアクセスしやすい3Dスキャナの出現と並行して実現しており、様々な業界での採用拡大に貢献しています。このような技術の飛躍により、デジタルツインの実験を行う多国籍企業がますます増えてきており、ノキアのような通信業界の大手企業は彼らの通信範囲を拡大し、自由に使える豊富なデータを利用可能にする新しい方法を模索しています。
産業用途以外でも、デジタルツインという用語は新しい意味を持ち始めており、仮想コピーは製品だけのものではなく、他のオブジェクトに対しても用いられるようになりました。メタバース (人々と企業が共存できる新しい仮想現実) はこれからも展開を続けていきますが、それがどのような方向に向かうのかはまだ予測できません。しかし、それが成長していくにつれて、現実世界の人物や場所、そしてアイテムのデジタルバージョンに対する需要も高まっており、これは成長しつつあるデジタルツイン市場にとって、次なる新たな未開拓地となる可能性を表しています。