Reverse engineering di un'auto di Formula 1 e stampa 3D di una sua copia in miniatura
L'obiettivo: Utilizzare due diversi scanner 3D per scansionare l'auto di Formula 1 nella sua interezza, catturandola da cima a fondo con i più alti livelli di dettaglio e velocità.
Strumenti utilizzati: Artec Eva, Artec Studio
Gli scanner 3D di Artecsono strumenti indispensabili, utilizzabili in tutte le fasi del ciclo di vita di un prodotto. In qualsiasi flusso di lavoro, che si tratti di creazione prototipi, reverse engineering o dalla realizzazione di unmodello 3Dper il controllo della qualità, la scansione 3D è vitale per ottenere il flusso di lavoro più veloce.
Il reverse engineering prevede l'acquisizione dei dettagli tecnologici e della forma di un oggetto al fine di migliorarlo o ricrearlo. Utilizzato in una varietà di settori, come l'ingegneria industriale, automobilistica, aeronautica, manifatturiera, elettronica e molti altri, consente di replicare l'oggetto iniziale scansionandolo, analizzandolo e disassemblando la sua replica 3D digitale.
L'uso della scansione 3D per il reverse engineering sta diventando sempre più popolare, grazie ai suoi risultati precisi e alla sua facilità d'uso. Le soluzioni 3D di Artec offrono sia un'incredibile precisione che la capacità di catturare un oggetto in 3D velocemente, e il software di post-elaborazione intelligente Artec Studio 11 è in grado di elaborare automaticamente grandi quantità di dati per creare il modello 3D. I dispositivi inoltre, grazie alla loro portabilità, sono in grado di scansionare i punti più difficili da raggiungere dell'oggetto e, se collegati ad un pacchetto di batterie, non richiedono una fonte di alimentazione fissa.
Un ottimo esempio dell'utilizzo della tecnologia 3D per il reverse engineering è questo progetto avviato da un produttore di utensili con sede a Birmingham che ha incaricato i partner britannici di ArtecCentral Scanninge il fornitore leader di soluzioni CAD e CAM Delcam di realizzare una replica 3D in scala della propria vettura da formula uno da poter poi stampare in 3D con una dimensione di circa 300 mm.
L'auto è stata scansionata in 3D, quindi i dati raccolti sono stati elaborati nel pacchetto software per il reverse engineering Delcam PowerSHAPE.
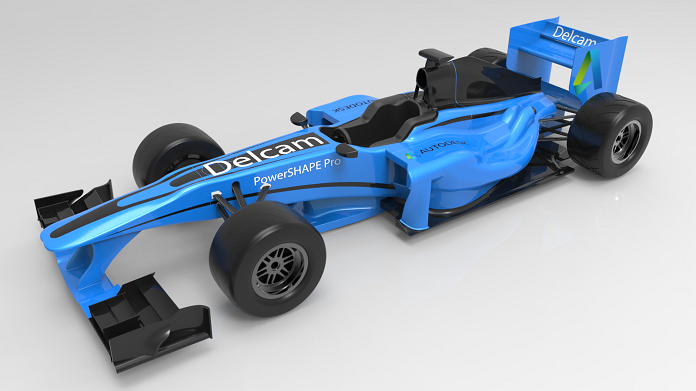
Il modello finito dell'auto F1 in PowerSHAPE.
"Questa scansione è stata eseguita come test per vedere cosa si potrebbe ottenere utilizzando due diversi sistemi di scansione", ha affermato Paul Smith di Central Scanning.
Il corpo principale della vettura è stato catturato utilizzando un Steinbichler Comet L3D, quindi l'abitacolo, il volante, le sospensioni del braccio oscillante, l'alettone posteriore, gli specchietti retrovisori esterni e le aree che non potevano essere facilmente raggiunte con lo Steinbichler sono stati scansionati in 3D con Artec Eva.
"Abbiamo scelto Eva per la sua portabilità e velocità, inoltre non abbiamo dovuto aggiungere marcatori, segue facilmente la grafica", ha detto Paul.
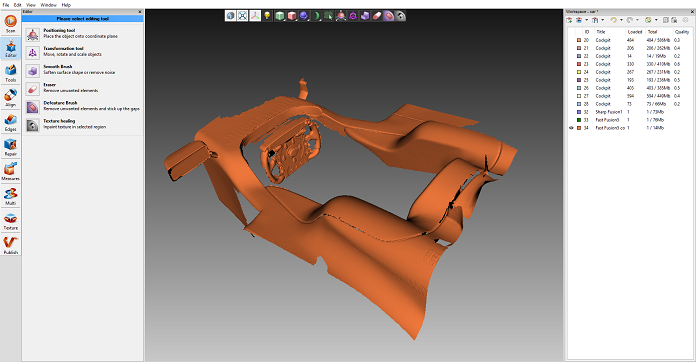
Parte dell'abitacolo in Artec Studio 10.
L'auto è stata scansionata in 3D nell'area di ricevimento e nell'officina del proprietario; entrambe le aree avevano una buona illuminazione stabile ma nessuna luce solare diretta perché ciò avrebbe ostacolato l'acquisizione dei dati.
Paul ha condiviso con noi alcuni suggerimenti su come catturare più facilmente le parti di un auto.
"L'aggiunta di qualcosa dietro le sospensioni a braccio trasversale, come della carta con dei disegni sopra, consente allo scanner di tracciare le texture e catturare la geometria del braccio trasversale sottile", ha detto.
C'erano alcune aree di fibra di carbonio scura intorno ai bracci trasversali - a quelle è stato applicato un leggero strato di spray opaco. Anche i riflessi di luce intorno alle aree dell'alettone sono stati spruzzati leggermente per facilitarne e accelerarne la cattura.
"Usare Artec Eva ci è piaciuto: non c'è stato bisogno di calibrazione, azionarlo e scansionare queste aree difficili è stato molto veloce", ha detto Paul.
La maggior parte dei dati è stata elaborata utilizzando le impostazioni standard senza texture durante la registrazione globale per accelerare il processo. I set di big data degli scanner Artec e Steinbichler sono stati quindi uniti in PolyWorks.
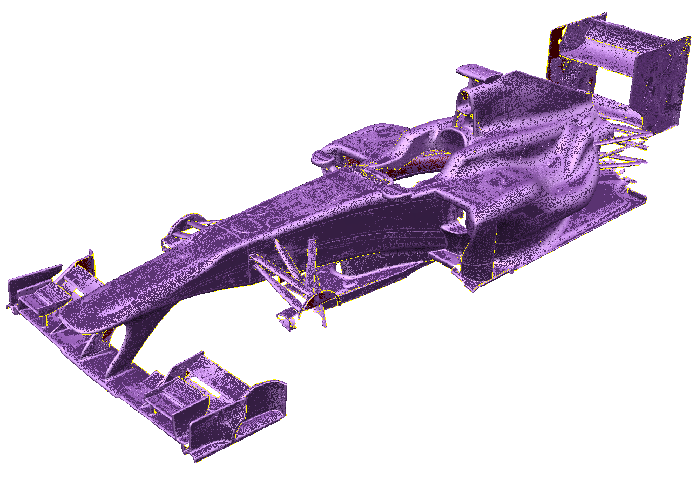
La mesh creata con i dati 3D.
Il modello 3D STL da 250 Mb, circa 8,5 milioni di triangoli, è stato quindi completamente rielaborato da Delcam utilizzando PowerSHAPE Pro. Le regioni complesse a doppia curvatura erano le più adatte per la modellazione superficiale, mentre le parti più prismatiche potevano essere formate in modo più efficiente usando solidi.
Come spiegato da James Slater di Delcam , “Le alette anteriori e posteriori della vettura sono state modellate come solidi, creati prendendo sezioni attraverso la texture, estrudendole e quindi unendo i pezzi separati usando semplici operazioni booleane. Questo lavoro è stato svolto con efficacia da uno studente in tirocinio estivo, che aveva avuto solo una settimana di formazione prima di intraprendere il progetto. Nel frattempo, uno dei nostri ingegneri più esperti era al lavoro sulla più difficile costruzione superficiale necessaria per il corpo dell'auto. Il risultato finale è stato una superficie ibrida dettagliata e un modello 3D solido che sarebbe pressoché impossibile realizzare utilizzando qualsiasi altro software. Ovviamente, uno degli aspetti più importanti in qualsiasi progetto di reverse engineering è partire da una mesh accurata e di alta qualità.”
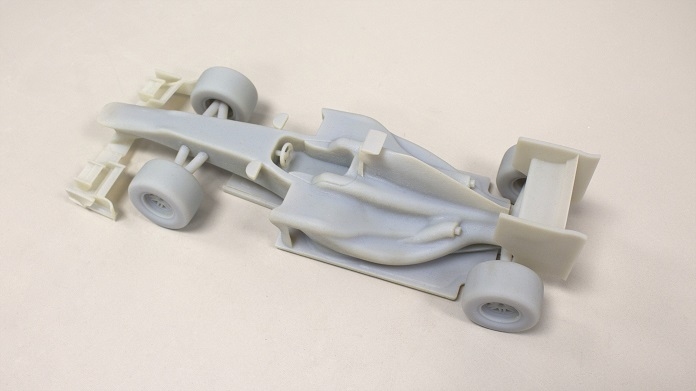
La replica 3D dell'auto da F1, stampata.
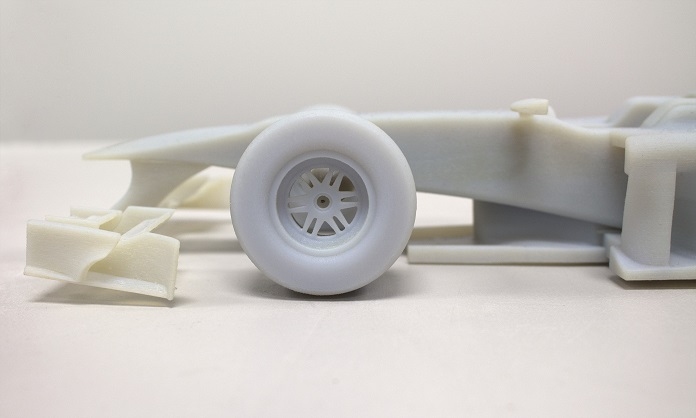
Un primo piano del modello in scala dell'auto da F1.
L'auto è stata scansionata nelle sue dimensioni originarie. Una volta ridimensionato il modello, alcune delle aree più sottili, in particolare i bracci trasversali e gli alettoni, sono stati ispessiti in PowerSHAPE. La copia digitale dell'auto è stata quindi stampata in 3D su un Objet Eden 500V con uno strato di 0,016 mm.
Scanners behind the story
Try out the world's leading handheld 3D scanners.