Comment la société israélienne A.B. Engineering utilise Artec Leo pour personnaliser le blindage des véhicules
Problématique : Tout en travaillant avec des délais serrés, scanner en 3D rapidement et minutieusement des véhicules démontés afin de construire les modèles CAO précis nécessaires à la création de blindages personnalisés pour une large gamme de voitures, de fourgons, de camions et d’autobus.
Solution : Artec Leo, Artec Studio, CATIA V5 de Dassault Systèmes
Résultat : Désormais, grâce à Artec Leo, en à peine deux heures, il est possible de scanner une voiture, une camionnette ou un camion démonté avec une précision submillimétrique, d’un pare-chocs à l’autre. Aucun spray ou cible n’est nécessaire Cinq heures de traitement et les scans sont prêts pour la CAO. L’ancien scanner 3D du client demandait l’utilisation de sprays, de milliers de cibles et une semaine entière pour scanner de tels véhicules, et une semaine supplémentaire pour traiter les scans pour la CAO.
Pourquoi Artec 3D ? Comme il est 100 % sans fil et ne nécessite pas d’ordinateur portable, Leo peut être utilisé pour des projets de scan à tout moment. Suffisamment simple pour les débutants, mais assez puissant pour les ingénieurs en métrologie, Leo permet aux clients de mener à bien leurs projets plus rapidement, avec une plus grande précision, réduisant ainsi les coûts tout en leur permettant d’accepter 200 à 300 % de travail supplémentaire sans compromettre la qualité du résultat.
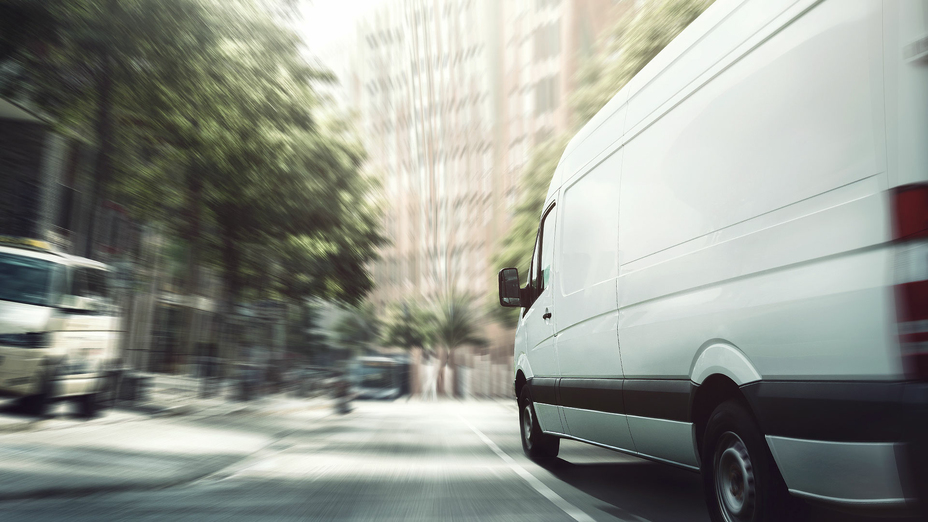
Lorsque le minivan transportant des enfants et leurs parents a franchi le coin de la rue, les deux hommes armés l’attendaient. Surgissant de derrière les voitures garées, ils ont mis leurs AK-103 en joue et ont ouvert le feu, mitraillant le véhicule qui s’approchait rapidement avec des salves contrôlées de 3 à 4 balles.
Mais le conducteur n’a pas voulu s’arrêter. En quelques secondes, les armes des tireurs étaient vides et le monospace criblé de balles s’est éloigné, ses vitres brisées mais intactes, tous les occupants à l’intérieur secoués mais indemnes.
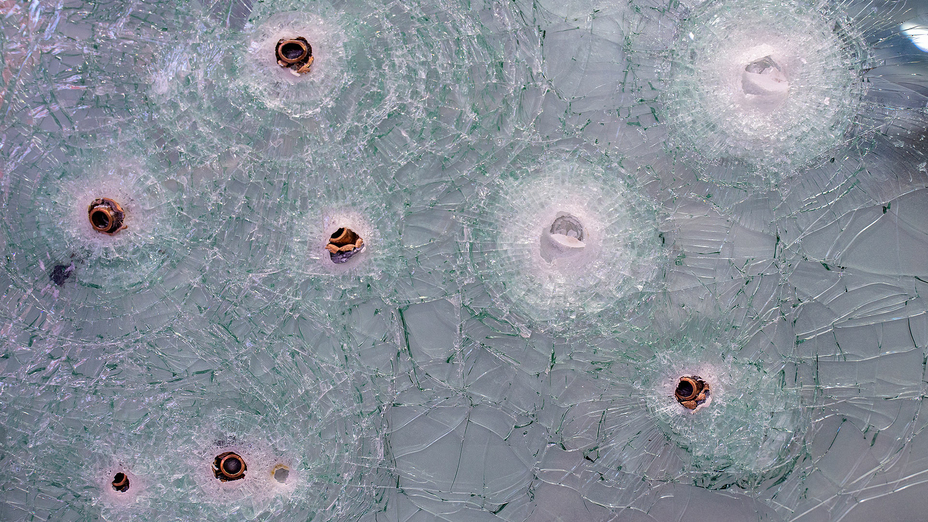
Verre pare-balles
Véhicules blindés : pas uniquement pour les papes et les présidents
Partout dans le monde, de l’Ukraine au Moyen-Orient et ailleurs, la demande en véhicules blindés n’a jamais été aussi élevée. Pas seulement pour les armées, les gouvernements et les grandes fortunes, mais aussi pour les associations et les organisations humanitaires, afin de transporter des passagers en toute sécurité, même dans les zones les plus dangereuses.
Les meilleurs de ces véhicules pare-balles sont discrètement blindés à l’aide de divers matériaux composites, d’aciers et de céramiques, capables d’arrêter toute une série de menaces balistiques, du calibre 22 au calibre 50, en fonction du niveau de blindage choisi pour chaque véhicule.
L’objectif est d’obtenir une protection maximale tout en ajoutant un minimum de poids.
Le blindage s’apparente à la confection d’un costume sur mesure pour un véhicule, même s’il est porté à l’intérieur. Il doit être aussi ajusté que possible, pour plusieurs raisons.
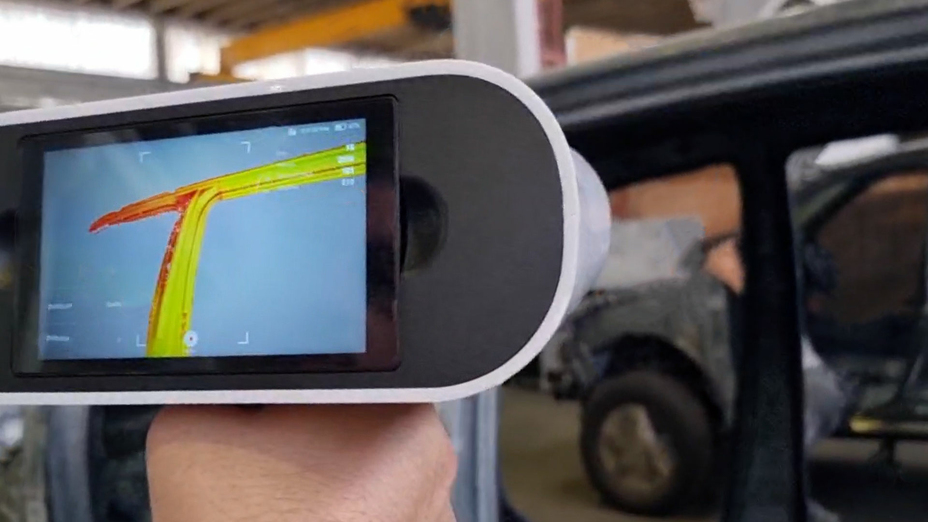
Artec Leo effectuant un scan 3D du châssis d’un Toyota Hi-Lux 2022. Image publiée avec l’aimable autorisation d’A.B. Engineering
Il faut parfois pouvoir réinstaller les pièces intérieures d’origine à leur emplacement initial, avec un minimum de modifications, pour des raisons évidentes de coût. Et, le cas échéant, le véhicule doit passer inaperçu aux yeux d’une personne (un tireur armé) qui s’entretient avec le conducteur à un poste de contrôle.
Ensuite, une fois que tout est en place, les occupants ne doivent pas ressentir de perte d’espace utile. Enfin, le blindage doit être indétectable de l’extérieur, de sorte que même des yeux bien entraînés ne parviendront pas à distinguer les voitures, les fourgons et les bus blindés des véhicules ordinaires non modifiés.
Ces « demandes de furtivité » sont formulées par les clients dans le cadre d’une mission spécifique, au cas par cas, et sont assorties d’exigences précisant la distance à laquelle le véhicule doit avoir l’air ordinaire. Ces distances peuvent aller de 50 mètres (160 pieds) jusqu’à une proximité immédiate avec le véhicule lui-même.
Pour relever un tel défi, le véhicule doit d’abord être dépouillé jusqu’au châssis et aux éléments les plus élémentaires, puis mesuré aussi précisément que possible, jusqu’au moindre millimètre carré.
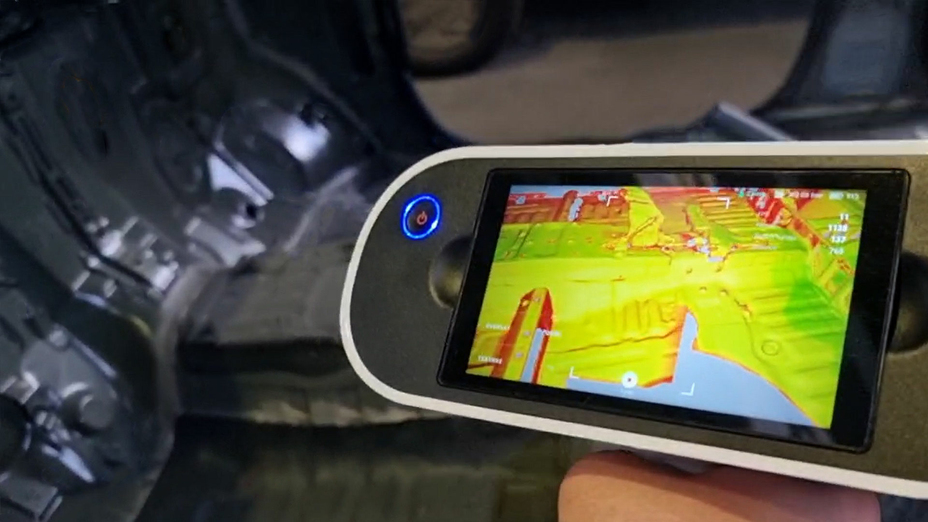
Artec Leo effectuant un scan 3D du châssis d’un Toyota Hi-Lux. Image publiée avec l'aimable autorisation d’A.B. Engineering
Puis, au cours des étapes suivantes, tous les éléments de blindage personnalisés peuvent être conçus en CAO et fabriqués dans des conditions strictes, de sorte que, une fois qu’ils sont installés et les pièces d’origine remises en place, il n’y a que peu ou pas d’espace entre le blindage, les portes et toute autre partie potentiellement vulnérable du véhicule.
Lorsque cela n’est pas possible, de nouvelles garnitures intérieures personnalisées sont créées pour imiter parfaitement celles d’origine, tout en laissant plus d’espace pour le blindage.
Ce processus peut prendre de 1 à 2 mois pour un petit véhicule, tel qu’un camion Toyota J79, jusqu’à plus de 4 mois pour un grand SUV complexe, tel qu’un Chevrolet Suburban.
Blindage de véhicule grâce au scan 3D
L’un des spécialistes du blindage de véhicules dont la réputation est largement méritée dans le secteur est la société israélienne A.B. Engineering Ltd., entreprise d’ingénierie mécanique qui travaille depuis 2012 avec les plus grandes firmes de l’aérospatiale et de la défense. Le scan 3D est à la base même de tout leur workflow de blindage.
Selon le fondateur et PDG de l’entreprise, Irakly (Ika) Baitish, « lorsqu’il s’agit de blinder un véhicule pour protéger au maximum ses occupants, de même que le moteur, le groupe motopropulseur et d’autres pièces essentielles qui font rouler le véhicule afin qu’il puisse quitter la zone dangereuse, il est absolument essentiel de commencer par des mesures précises.
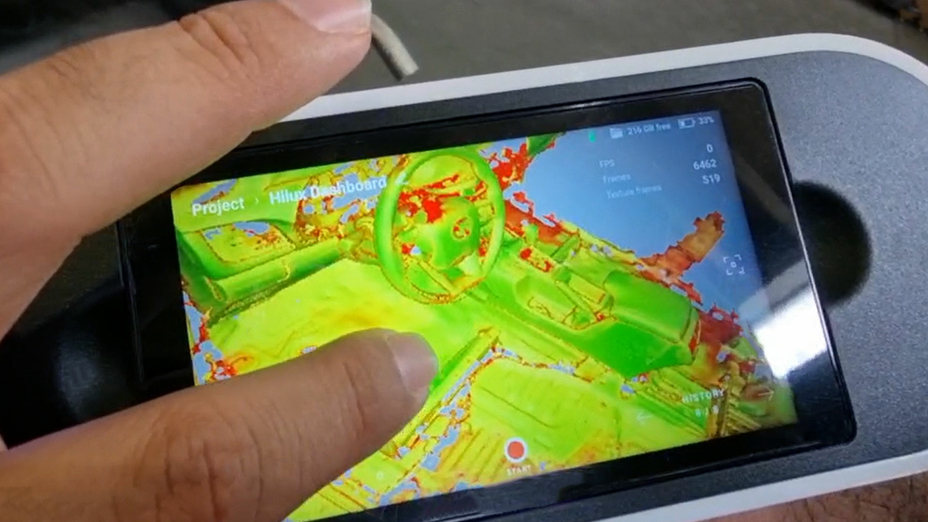
Visualisation d’un scan 3D du Hi-Lux sur l’écran tactile du Leo. Image publiée avec l’aimable autorisation d’A.B. Engineering
C’est pourquoi nous avons choisi le scan 3D comme moyen de mesure, car il nous permet d’obtenir les dimensions exactes de l’ensemble du véhicule, y compris les zones qui sont normalement difficiles à mesurer manuellement, comme la cloison pare-feu, qui sépare le conducteur du compartiment moteur », poursuit-il.
Une fois les scans 3D du véhicule traités, ils les exportent dans leur système de CAO, CATIA V5 de Dassault Systèmes.
Ils utilisent alors les scans comme modèles de référence pour concevoir les panneaux balistiques et les autres composants de blindage à fabriquer, puis ils les installent virtuellement dans le véhicule, afin de s’assurer que les résultats finaux se traduiront par une protection sans faille d’un pare-chocs à l’autre après la mise en place du blindage dans les semaines suivantes.
Trouver le bon scanner 3D
Mais tous les scanners 3D ne se valent pas. Au début, Ika et son équipe utilisaient un scanner 3D portable haut de gamme bien connu, qui nécessitait un grand nombre de cibles et de grandes quantités de spray, ainsi qu’un ordinateur portable, quelques câbles et une alimentation électrique de 220V.
Un projet typique de l’époque a été le scan de l’habitacle et du châssis dépouillés d’un Skoda Kodiaq qui avait besoin d’être blindé.
Après avoir posé plus de 3 000 autocollants et appliqué les quantités de spray nécessaires, il leur avait fallu deux semaines pour effectuer le scan, et les données obtenues n’étaient pas aussi propres que souhaité.
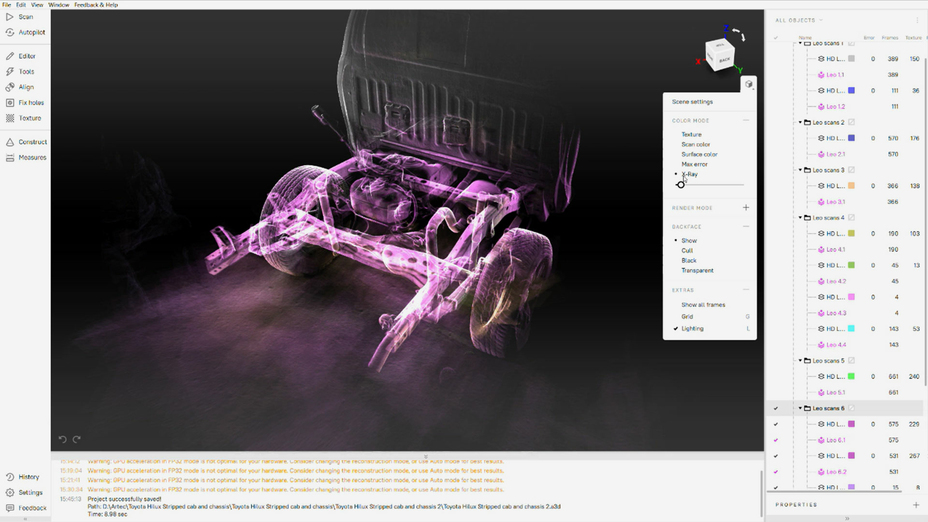
Capture d’écran Artec Studio : aperçu en mode Rayons X du scan effectué par Leo de l’arrière du Hi-Lux. Image publiée avec l'aimable autorisation d’A.B. Engineering
Avant de pouvoir assembler les scans avec certitude et créer un modèle 3D très précis pour la CAO, une semaine supplémentaire de nettoyage des données et de nouvelles mesures manuelles avait été nécessaire.
L’un des membres de l’équipe (le perdant au jeu de la courte paille) avait été chargé de décoller les quelques 3 000 cibles du véhicule, puis de le nettoyer. Malheureusement, certains autocollants avaient laissé des résidus sur les panneaux intérieurs, les rendant inutilisables.
Devant le temps et les efforts considérables que cela demandait, Ika comprit que leur scanner 3D ralentissait sérieusement son équipe.
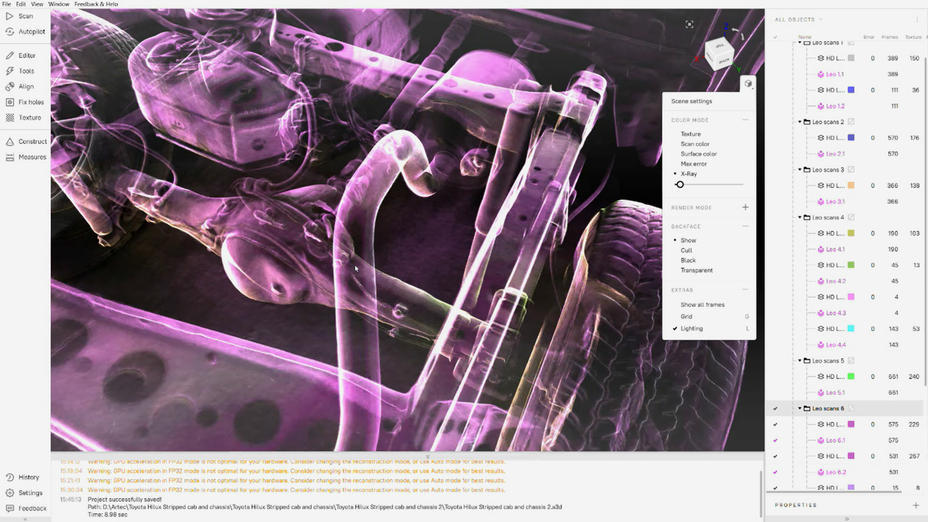
Capture d’écran Artec Studio : aperçu en mode Rayons X du scan effectué par Leo de l’arrière du Hi-Lux. Image publiée avec l'aimable autorisation d’A.B. Engineering
Dans un secteur où les délais des projets ne sont pas flexibles, chaque jour et chaque heure peuvent être décisifs. C’est pourquoi, une fois le projet terminé, Ika s’est mis à la recherche d’un meilleur scanner 3D.
Adieu les semaines de scan, les cibles et les sprays !
Très vite, il a trouvé le site internet d’Artec 3D et s’est intéressé à l’Artec Leo, un scanner 3D portable professionnel qui est depuis des années la référence en matière de rétro-ingénierie, de criminalistique, de soins de santé et d’autres applications.
Offrant des scans 3D couleur haute résolution avec une précision submillimétrique, Leo est équipé d’un écran tactile et d’une batterie intégrée, ce qui le rend 100 % portable, avec une vitesse d’acquisition élevée et un large champ de vision de numérisation.
Scanner une Toyota Hi-Lux 2022 plus rapidement que jamai
Pour illustrer la façon dont le workflow d’A.B. Engineering s’est amélioré depuis l’adoption de Leo, l’un de ses récents projets de blindage impliquait le scan de l’habitacle et du châssis dépouillés d’un pick-up Toyota Hi-Lux 4 portes de 2022.
Leo en main, Ika et son équipe se sont mis au travail pour capturer le véhicule Toyota. À peine deux heures plus tard, sans avoir eu à placer une seule cible ou pulvériser le moindre produit, le scan était terminé.
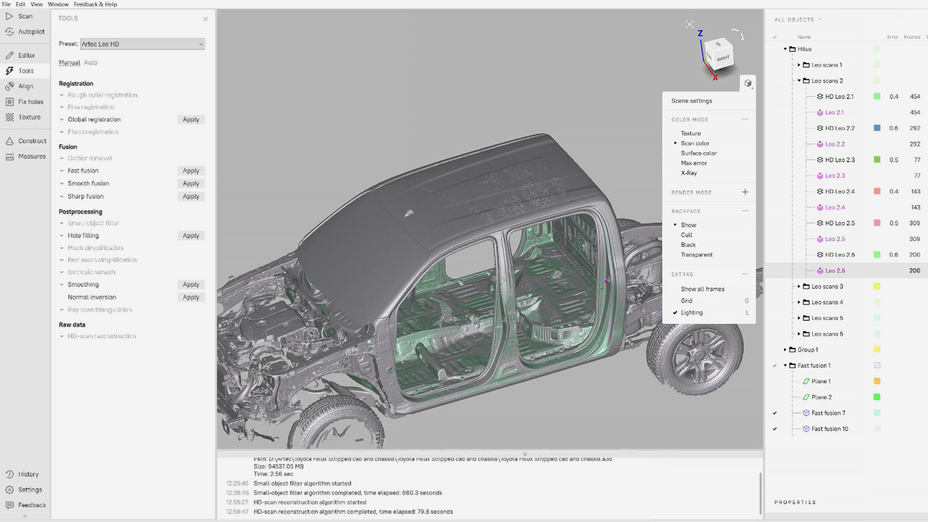
Capture d’écran d’Artec Studio : scans Leo combinés du Hi-Lux. Image publiée avec l'aimable autorisation d’A.B. Engineering
À partir de là, il n'a fallu que cinq heures au logiciel Artec Studio pour traiter les scans et créer les fichiers STL qui ont été envoyés à la CAO pour concevoir le blindage du Hi-Lux.
Comparé à leur ancien scanner, qui nécessitait une semaine de numérisation + une autre semaine de traitement pour obtenir presque les mêmes résultats, mais avec une qualité nettement inférieure, le contraste était étonnant.
Selon les propres termes d’Ika, « comparé à ce que nous faisions auparavant, Leo nous offre une différence de vitesse incroyable. Et les données que nous obtenons avec Leo sont beaucoup plus propres, sans aucun problème de décalage. »
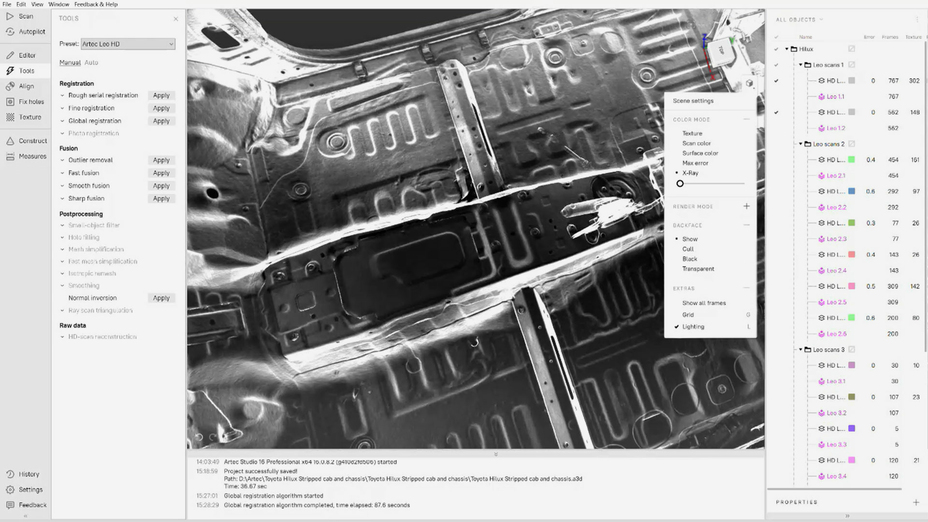
Capture d’écran d’Artec Stucio : aperçu en mode Rayons X du scan effectué par Leo de l’intérieur du Hi-Lux. Image publiée avec l'aimable autorisation d’A.B. Engineering
Et il poursuit : « Notre processus de mesure s’est considérablement amélioré, tant en termes de temps que de qualité. Leo a radicalement changé la qualité de nos résultats techniques et notre capacité à obtenir les quelques pourcents supplémentaires indispensables pour éliminer les failles balistiques, ce qui peut littéralement sauver des vies. »
« Chaque véhicule exige une approche personnalisée »
Pour chaque véhicule à blinder, Ika et son équipe consultent le client, en tenant compte du degré de protection balistique nécessaire, de l’utilisation prévue du véhicule, ainsi que des attentes concernant les délais et les améliorations secondaires à y apporter.
Sur ce dernier point, un travail de blindage typique peut facilement ajouter 500 à 2 000 livres (230 à 900 kg) au poids total d’un véhicule. Pour faire face à une telle augmentation, des freins, des essieux, des transmissions et des groupes motopropulseurs spéciaux et robustes sont parfois nécessaires.
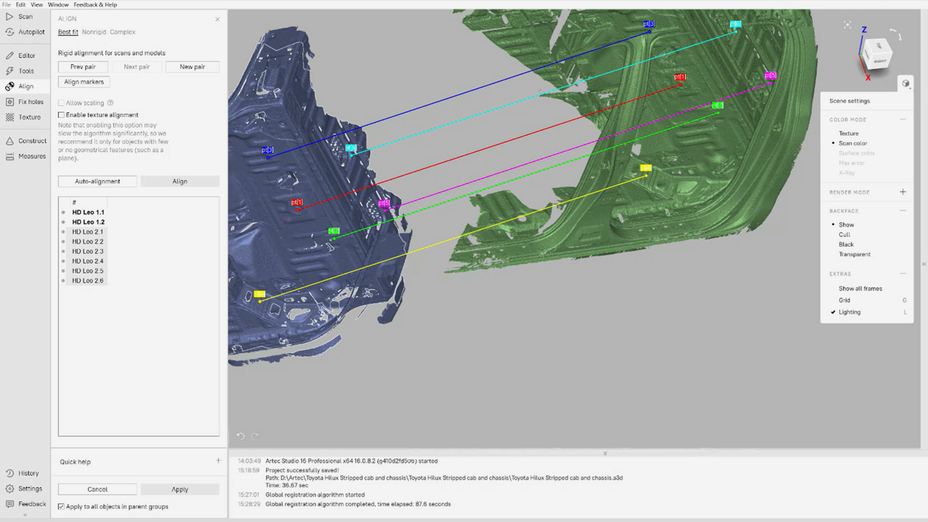
Alignement facile des scans par Leo du Hi-Lux dans Artec Studio. Image publiée avec l'aimable autorisation d’A.B. Engineering
« Comme ce " renforcement " du véhicule implique l’ajout d’un poids important, explique Ika, nous sommes encore plus contraints d’optimiser le blindage pour qu’il soit le plus léger possible tout en offrant une protection maximale.
Et il ajoute : Maintenant que nous avons Leo, il est beaucoup plus facile et rapide d’obtenir ce genre de résultat. »
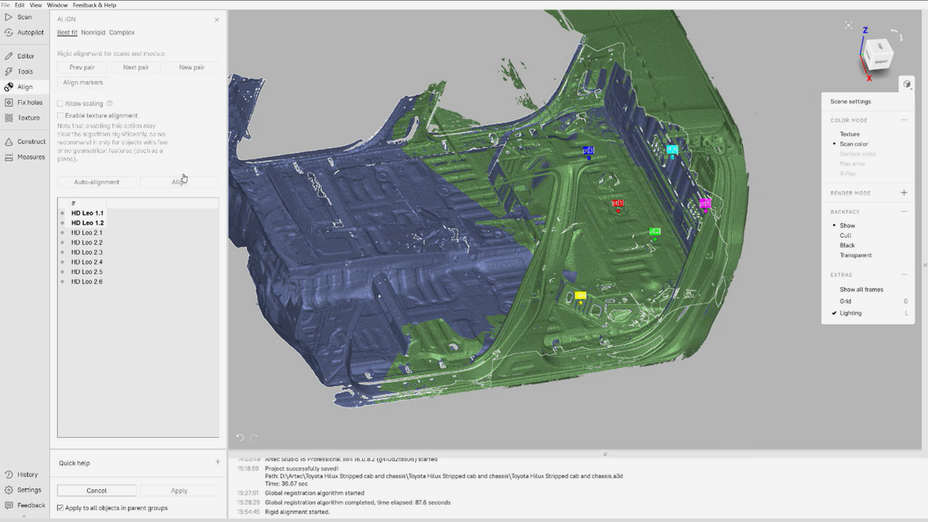
En quelques clics, les scans du Hi-Lux sont alignés dans Artec Studio. Image publiée avec l'aimable autorisation d’A.B. Engineering
Un travail testé sur un champ de tir
Ika et son équipe sont fermement convaincus de la qualité de leur travail, quelle que soit la taille ou la complexité du projet, et Leo leur permet de le faire encore plus sereinement. Une récente démonstration de la qualité de leur blindage parle d’elle-même.
L’un de leurs véhicules, un camion blindé lourd, a été emmené dans un centre d’essais à balles réelles, où plus de 800 balles de tous calibres (jusqu'à .50) provenant d’une variété d’armes ont été tirées sur le véhicule, sans aucun impact.
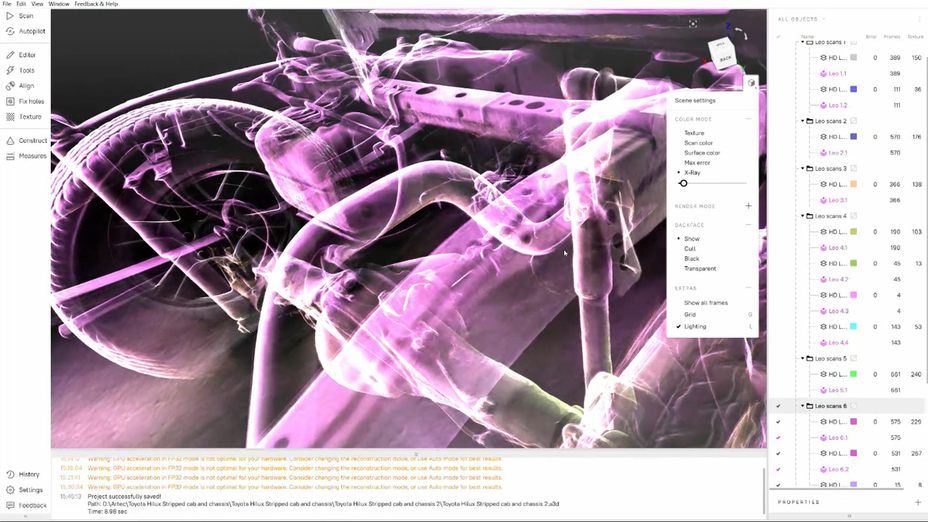
Aperçu en mode Rayons X du scan effectué par Leo de l’arrière du Hi-Lux. Image publiée avec l'aimable autorisation d’A.B. Engineering
En revanche, un autre véhicule blindé, d’une entreprise concurrente, a été soumis à un feu nourri de balles provenant des mêmes armes. Il a subi des centaines d’impacts, dépassant largement le point où, dans un scénario réel, les occupants n’auraient eu aucune chance de survie.
Leo en déplacement : le blindage des voitures, des camions, des bus et des avions
Depuis des années, l’équipe d'ingénieurs et de techniciens expérimentés d’A.B. Engineering réalise des projets de blindage simples ou complexes pour une grande variété de véhicules, d’avions et d’autres objets.
« Leo étant facile à emporter, nous prenons l’avion et nous nous rendons sur le lieu de notre prochain projet. Une fois sur place, nous savons que nous aurons terminé en un temps record et que toutes les données se trouveront sur la carte SD de Leo, propres et prêtes à l'emploi, » explique Ika.
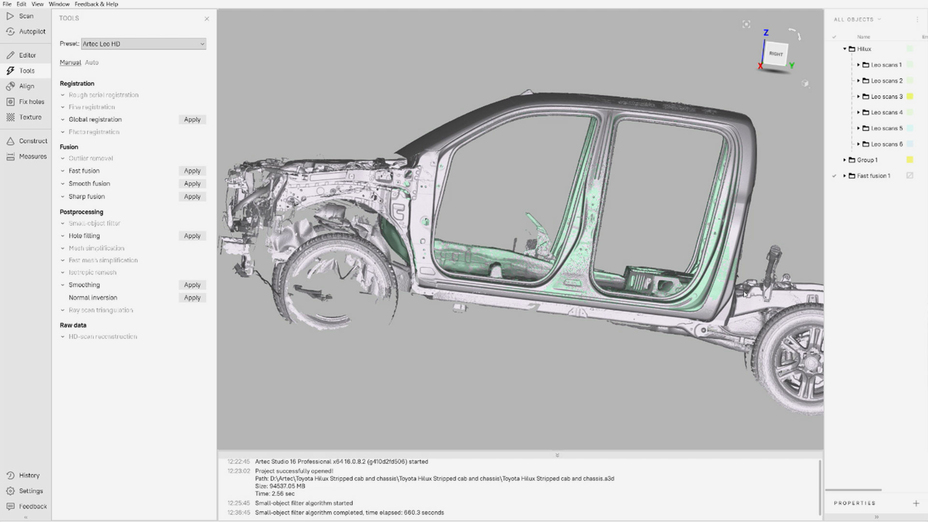
Prêt pour la CAO : capture d’écran Artec Studio des scans Leo combinés du Hi-Lux. Image publiée avec l'aimable autorisation d’A.B. Engineering
Il poursuit : « Le simple fait de pouvoir emporter le scanner sans même un ordinateur portable sur le terrain, partout dans le monde, est un énorme avantage, et l’option de scan sans cible est un autre avantage considérable, puisque nous n’avons pas besoin de préparer l’objet que nous scannons. Cela signifie également que nous ne laissons aucune trace du processus de numérisation, ce qui peut parfois s ‘avérer crucial. »
Un afflux régulier de demandes et de recommandations tout au long de l'année
D’un point de vue stratégique, Leo a permis à Ika et à son équipe d’être beaucoup plus compétitifs. Aujourd’hui, grâce à Leo, chaque projet incluant un scan 3D requiert deux semaines de moins de temps d’ingénierie qu’auparavant. Cela permet à l’entreprise de proposer des prix plus bas à ses clients, ce qui se traduit par un afflux régulier de demandes et de recommandations tout au long de l’année.
Ika explique : « Avant d'adopter Leo, le scan 3D représentait 20 à 30 % du coût total pour le client, en raison du temps qu’il nécessitait. Avec Leo, cette opération ne représente plus que 5 à 10 % du coût du projet. Dans certains cas, nous pouvons donc facturer 20 % de moins qu’un concurrent qui utilise un scanner 3D moins perfectionné, comme celui que nous avions auparavant.
Scanners behind the story
Try out the world's leading handheld 3D scanners.