Un matériau de construction validé par Artec offre des perspectives pour un avenir durable
Problématique : Découvrir si un nouveau biomatériau à base de sucre peut insuffler une nouvelle vie à un modèle de bloc de construction vieux de 300 ans et en faire un outil de construction moderne et viable.
Solution : Artec Leo, Artec Studio, SOLIDWORKS
Résultat : Un workflow d’inspection innovant, dans lequel le scan 3D d’Artec est utilisé pour vérifier que les dalles coulées ne présentent pas de déformations. La numérisation et l’analyse de plus d’une centaine d’échantillons ont permis d’obtenir les informations nécessaires pour perfectionner la formule du « Sugarcrete® ». Celle-ci peut désormais être utilisée pour fabriquer des blocs aux propriétés homogènes, prêts à être utilisés dans des projets d’architecture durable partout dans le monde.
Pourquoi Artec 3D ? : La vitesse de Leo, son écran intégré et sa configuration sans fil rendent la numérisation rapide et facile, même pour les novices en la matière. C’est cette convivialité, associée à un niveau incroyable d’exactitude et de précision, qui permet aux utilisateurs de réaliser des tâches d’inspection complexes.
Bon marché et facile à réaliser, le ciment est incroyablement populaire. En fait, à part l’eau, le ciment est la ressource la plus utilisée sur Terre. Mais il est aussi un facteur important du réchauffement climatique.
Pour fabriquer du béton pour la construction, il faut d’abord produire du ciment en faisant cuire du calcaire, de l’argile et d’autres matériaux dans un four, selon un processus gourmand en énergie et à forte émission de CO2. Si l’on considère les dommages causés par l’extraction des ingrédients, les émissions dues au transport et l’impact des villes bétonnées sur notre santé, le ciment est aujourd’hui l’un des plus grands fléaux écologiques de notre planète.
Tandis que les principaux acteurs de l’industrie tentent de compenser leur colossale empreinte carbone par le piégeage du carbone ou les énergies vertes, d’autres cherchent à remplacer purement et simplement le ciment dans le domaine de la construction.
La paille, le bambou et même les coquilles d’œuf ont été envisagés comme alternatives. Il est souvent proposé que les matériaux expérimentaux soient également imprimés en 3D, afin de réduire les déchets. Cependant, malgré les essais concluants, rien n’a pu détrôner le ciment de sa place au cœur de la construction moderne.
Le sucre : notre gentil sauveur de l’environnement ?
L’une des approches les plus récentes et les plus innovantes pour résoudre ce problème épineux est en cours de développement à l’Université d’East London (UEL).
En collaboration avec les experts en raffinage du sucre de Tate & Lyle Sugars, l’équipe de l’UEL travaille sur un substitut basé sur un sous-produit de la canne à sucre. Vous vous demandez peut-être : « Pourquoi la canne à sucre ? » Il se trouve que la canne à sucre est la culture la plus répandue dans le monde.
Près de deux milliards de tonnes sont récoltées chaque année dans le monde, produisant 600 millions de tonnes de tiges broyées en une sorte de pulpe appelée « bagasse ». Jusqu’à récemment, cette matière était en grande partie éliminée, mais elle est de plus en plus souvent réutilisée. Le matériau est généralement recyclé comme biocarburant, mais l’équipe de l’UEL pense qu’il pourrait également servir dans le secteur de la construction.
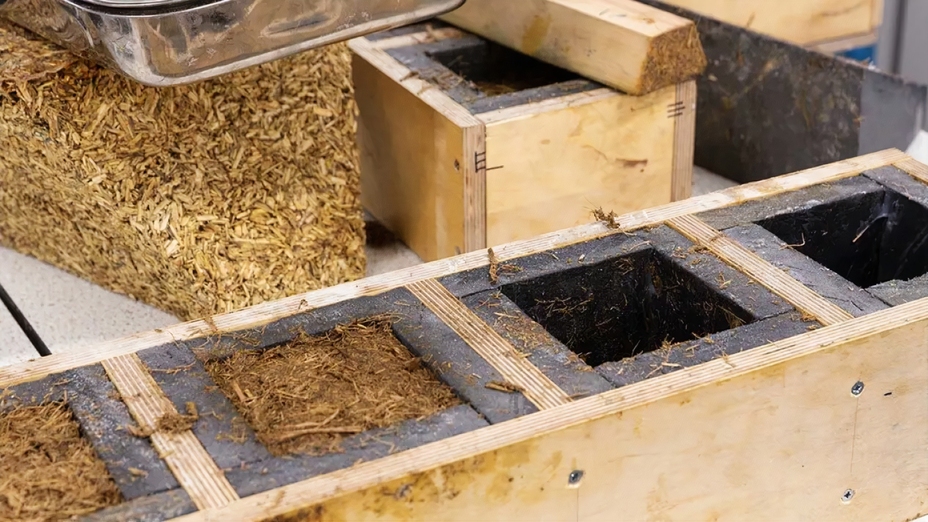
Gros plan sur le processus de pressage des blocs Sugarcrete®. Photo par Chromaphotography, avec l’aimable autorisation de l’UEL
Afin de concrétiser ce potentiel, l’équipe a mis au point un matériau 4 à 5 fois plus léger que la brique, dont l’empreinte carbone est réduite de 15 à 20 %. Mais plutôt que de fabriquer des briques à partir de leur formulation, baptisée Sugarcrete®, ils ont collaboré avec les architectes de Grimshaw pour redonner vie à un projet datant de 1699.
Cette année-là, l’architecte français Joseph Abeille avait présenté des voûtes plates à assemblage à sec composées de dalles qui s’emboîtaient les unes dans les autres pour transférer les charges sur l’ensemble de leur surface. La conception modernisée de l’équipe comporte désormais des traverses périmétriques post-tensionnées, qui réduisent de 90 % la dépendance à l’acier, ce qui en fait une base idéale pour une infrastructure respectueuse de l’environnement.
Cependant, lorsqu’ils ont commencé à presser les blocs en Sugarcrete®, les chercheurs de l’UEL ont constaté un retrait important. Le secteur de la construction étant très réglementé, l’équipe avait besoin d’un moyen de mesurer, de quantifier et de résoudre ce problème. La réponse ? Un processus de R&D unique, accéléré et validé par le scan 3D de précision à grande vitesse d’Artec.
La numérisation au « Fab Lab » de l’UEL
Heureusement pour l’équipe de Sugarcrete®, l’UEL dispose désormais d’un laboratoire de fabrication numérique équipé d'outils de numérisation, dont Artec Eva Lite, Artec Eva, Artec Space Spider, et Artec Leo.
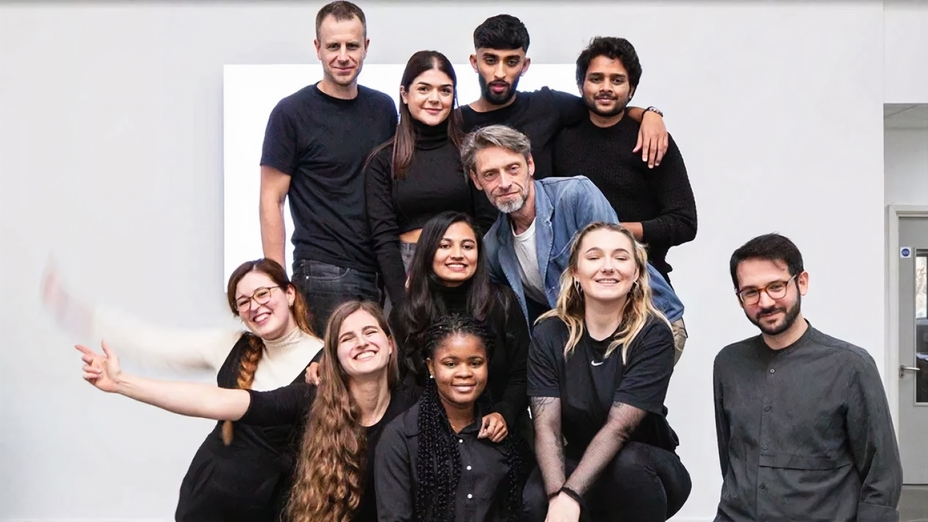
L’équipe de développement de Sugarcrete®. Photo par Chromaphotography, avec l’aimable autorisation de l’UEL
Depuis 2006, le partenaire certifié Gold d’Artec Patrick Thorn & Co. a permis à l’UEL de passer d’une poignée de fraiseuses à une installation adaptée à l’industrie, tout en dispensant des formations. Grâce aux appareils de ce Fab Lab, les étudiants ont déjà découvert qu’il était possible de numériser toutes sortes d’objets, des œuvres d’art aux environnements extérieurs, à des fins de surveillance, tout en obtenant des résultats exceptionnels.
Dans le cas présent, les développeurs ont utilisé le premier appareil sans fil Artec Leo pour évaluer les prototypes en Sugarcrete®. L’absence de câbles et l’écran intégré a rendu l’appareil incroyablement maniable et facile à prendre en main pour les débutants. L’extrême précision de l’appareil leur a également permis d’identifier le retrait exact de chaque bloc et de trouver une solution : une recette améliorée.
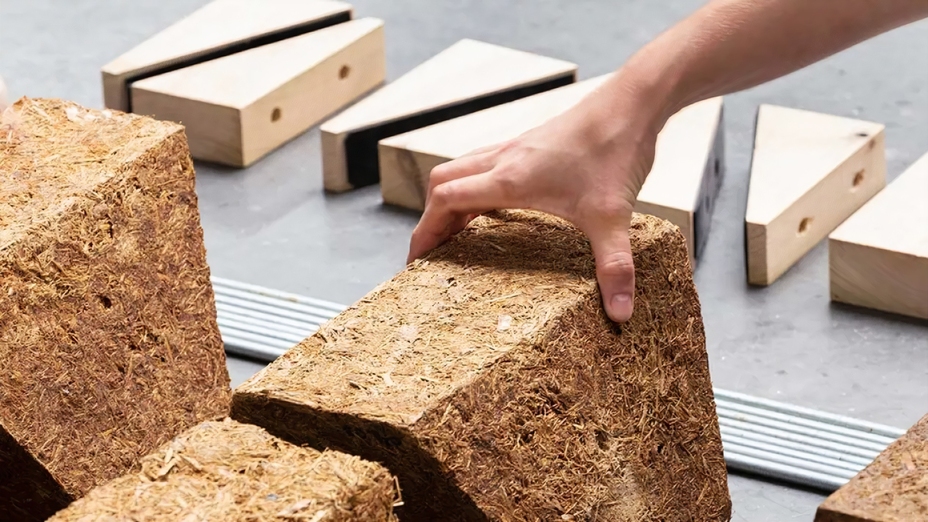
Un bloc en Sugarcrete® en cours d’assemblage par emboîtement. Photo par Chromaphotography, avec l’aimable autorisation de l’UEL
« Nous avions utilisé de la chaux, un matériau de construction classique qui émet moins de carbone que le ciment. Mais elle contient de l’eau, qui a tendance à rétrécir, explique Alan Chandler, codirecteur de l’Institut de recherche sur le développement durable de l’UEL. Désormais, nous utilisons un liant silicone sans eau qui « gélifie » le mélange, ce qui réduit la déformation et augmente la résistance à la compression. »
« Il était particulièrement utile de pouvoir capturer le matériau fini. Avec Artec Leo, nous avons prouvé que les dalles en Sugarcrete® peuvent avoir des propriétés améliorées. »
De la théorie à la réalité
Artec Studio a lui aussi été un élément central de la réussite du projet Sugarcrete®. Grâce à des fonctions comme le pilote automatique, qui automatise de nombreuses étapes de traitement manuel des données, les étudiants de l’équipe ont pu rapidement et facilement passer d’un scan à un maillage 3D très détaillé. L'intégration parfaite d’Artec Studio à SOLIDWORKS a également simplifié le processus de scan vers la CAO.
Grâce à la fonctionnalité d’exportation directe des maillages, les fichiers ont pu être envoyés à SOLIDWORKS en un seul clic. Cette intégration s’est avérée un véritable gain de temps, car l’équipe a dû transformer plus d’une centaine de maillages de blocs en modèles CAO. Selon M. Chandler, cette étape a été déterminante pour « décortiquer les différences » entre les échantillons, éviter les généralisations et exclure les défauts causés par pur hasard.
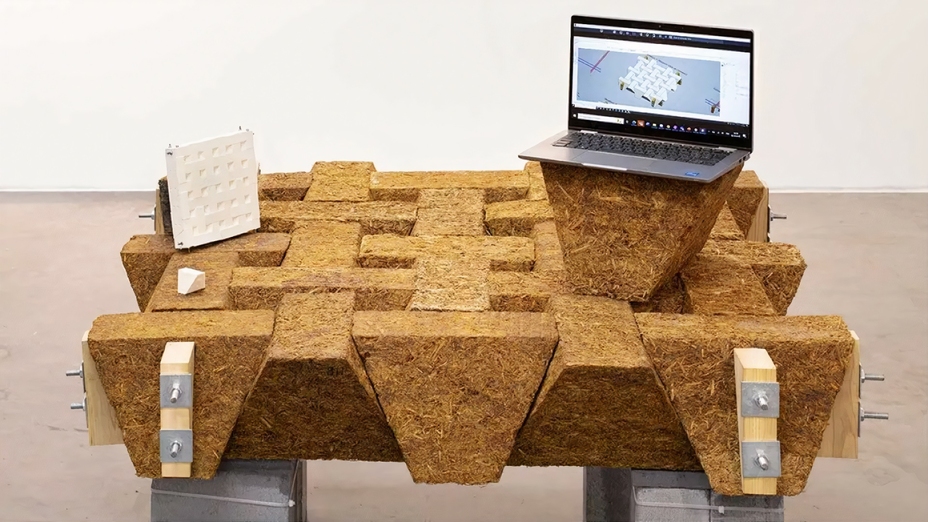
Une dalle complète en Sugarcrete® avec un modèle 3D de la conception finale. Photo par Chromaphotography, avec l’aimable autorisation de l’UEL
Alors que l’équipe travaille avec Tate & Lyle Sugars pour identifier les possibilités d’application dans le monde de la production sucrière, il ajoute que le scan 3D d’Artec peut désormais contribuer aux objectifs de l’Institut de recherche sur le développement durable de l’UEL – en matière d’optimisation de la conception, de modélisation des performances et d’analyses du cycle de vie (ACV).
La mesure du retrait des blocs n’est plus un exercice théorique, c’est devenu un exercice pratique, conclut M. Chandler On peut prédire les trajectoires de charge sur un ordinateur, mais il est beaucoup plus facile de numériser et d’étudier les variables. Avec le scan 3D, nous voulons être capables de relier les ACV à la performance et à la conception des bâtiments. Il ne s’agit pas seulement d’obtenir des données de bonne qualité, mais aussi de produire des résultats positifs. »
« Nous avons dû dépasser le stade de la théorie. La possibilité d’évaluer notre approche à l’aide du scan 3D très précis d’Artec nous a permis de voir comment les blocs se comportent véritablement. »
Vous voulez en savoir plus ? Vous pouvez lire les détails complets du projet Sugarcrete ici.
Scanners derrière l'histoire
Essayez les meilleurs scanners 3D au monde.