Construire un van International Metro de 1957 propulsé par un moteur Hellcat avec Artec Leo
Défi :Accélérer et simplifier considérablement la construction à partir de zéro de pièces et de composants automobiles introuvables sur le marché, sans sacrifier qualité ni précision.
Solution :Artec Leo, Artec Studio, Autodesk Alias, SOLIDWORKS
Résultat :Réduire le temps nécessaire de plusieurs jours à quelques heures à peine pour transformer d’anciennes pièces physiques en de tout nouveaux modèles CAO prêts à la fabrication ou au prototypage, en utilisant pour références des données de scan d’Artec Leo.
Pourquoi Artec ?Leo garantit à Scratch Build une liberté permise par aucune autre option. L’acquisition accélérée des données permet de consacrer plus de temps à la modélisation CAO, à la conception et au prototypage.
Contexte
Depuis ses cinq ans, Chad Forward sait qu’il veut construire des choses. Après avoir passé quinze ans à travailler dans de grands studios de design automobile en Australie et comme conseiller en conception pour des ateliers de customisation de voitures, il a ouvert sa propre entreprise de restauration,Scratch Build Co, pour continuer à faire ce qu’il aimait depuis toujours : construire des voitures.
Lancée en 2012 comme projet secondaire auquel Chad se consacrait le week-end, Scratch Build est devenue un studio de conception et un espace de collaboration à part entière. Chad et d’autres sous-traitants – designers automobiles, techniciens et électriciens – y créent des designs pour des créateurs de produits automobiles ou de voitures customisées.
« J’ai toujours été attiré par les personnes passionnées par ce qu’elles essaient de créer, commente Chad. En observant des artistes et des designers incroyables chez Toyota, Ford et dans d’autres studios de conception, j’ai pu me rendre compte de l'intérêt d’employer ces personnes et de construire un espace où toutes peuvent venir créer quelque chose dans l'intérêt du marché automobile australien. »
Comme l’indique le nom de son studio, Chad crée la plupart du temps à partir de zéro, qu’il s’agisse d'une pièce plus disponible à la vente ou d'un processus complet qu'un client essaie de réinventer. Jusqu’en 2017, son processus de rétro-ingénierie prenait beaucoup de temps, sans que les résultats ne soient forcément à la hauteur. « Il me fallait parfois une journée entière pour mesurer un châssis, effectuer des mesures élémentaires puis essayer de créer un modèle CAO à partir de ces informations, ajoute Chad. Je ratais souvent des éléments cruciaux parce que je devais me dépêcher. Et je devais aussi refaire certaines choses plusieurs fois. »
« Leo, le scanner de pointe réellement portable d’Artec, est une véritable révolution dans le secteur du scan 3D. »
Lorsqu’Artec a sorti sonscanner 3D portable sans fil Artec Leocette année-là, Chad a immédiatement été convaincu. « Il y a vingt ans, lorsque j’ai commencé à travailler dans la personnalisation automobile, je pensais que cette technologie n’existerait jamais de mon vivant », se souvient-il. Chad a précommandé le scanner auprès d’Objective3D, revendeur australien d’Artec, et, à en croire l’équipe, il a été le premier client à le recevoir.
« Leo, le scanner de pointe réellement portable d’Artec, est une véritable révolution dans le secteur du scan 3D. Objective3D est fier de fournir cette technologie aux marchés australien et néo-zélandais, explique Matt Minio, directeur général d’Objective3D. Il est particulièrement intéressant pour les ingénieurs automobiles qui peuvent s’en servir pour larétro-ingénierie de pièceset pour voir comment celles-ci influent sur les performances d'un véhicule. »
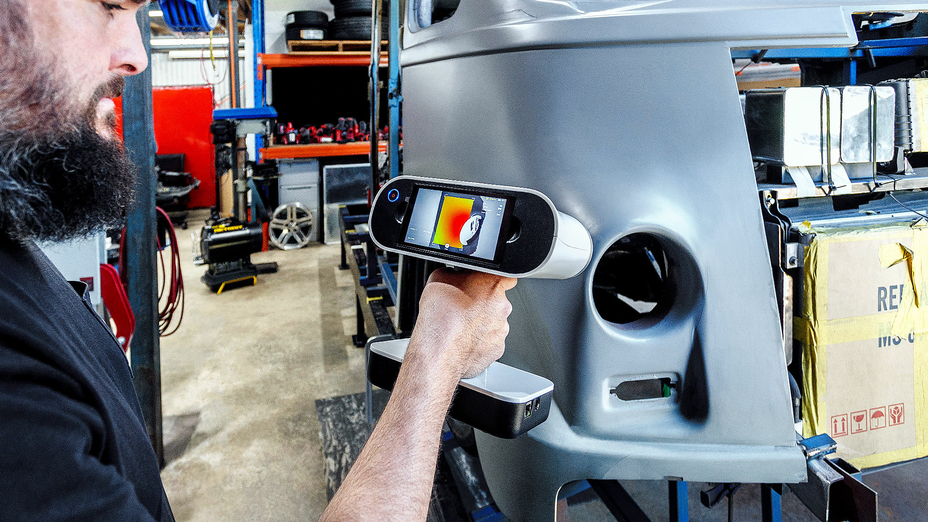
Artec Leo permet au fondateur de Scratch Build de mesurer simplement n'importe quelle pièce (Photo fournie par streetmachine.com.au)
Conçu avec la mobilité et la facilité d’emploi pour priorités, Artec Leo est un scanner 3D puissant et unique qui fonctionne sans ordinateur de bureau ou portable. Son vaste champ de vue lui permet de scanner facilement en 3D des pièces industrielles de moyenne ou grande taille, voire des véhicules entiers, avec une précision garantie et une résolution exceptionnelle.
Fort de son processeur embarqué automatique, de sa connectivité sans fil, de son écran tactile intégré et de sa batterie, le scanner procure une autonomie complète et une liberté de mouvement quel que soit l’endroit où se trouve l'utilisateur, qu’il s’agisse d’un atelier de personnalisation automobile, d’une usine ou d’un site reculé non raccordé à l’électricité.
Pour Chad, c’était tout vu : « Il m’a fallu quatre ans pour me décider à dépenser 4 000 $ dans une imprimante 3D, mais il ne m’a fallu que 15 minutes pour me convaincre d’acheter un scanner à 40 000 $. »
Au travail !
Une fois le scanner livré, Chad l’a immédiatement sollicité et n’a pas arrêté depuis. Toutes les pièces automobiles qui doivent être mesurées sont désormais scannées avec Leo, dans l’atelier ou sur le terrain, ce qui lui fait gagner un temps précieux mais aussi à ses clients. Il consacre ces heures bonus à la modélisation CAO, à la conception et au prototypage de pièces et composants automobiles, en utilisant pour références les données scannées.
« Je n’arrive pas à croire qu’un seul appareil puisse m’offrir une telle liberté, ajoute Chad. Peu importe le lieu ou la complexité des pièces, je peux maintenant acquérir facilement leurs données. »
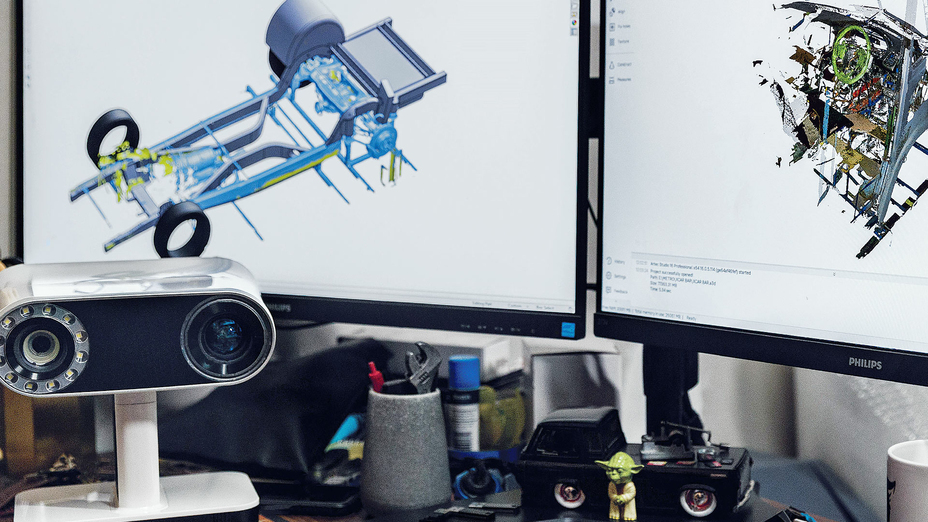
Chad utilise les données de Leo comme références pour la modélisation CAO dans SOLIDWORKS et Autodesk Alias (Photo fournie par streetmachine.com.au)
Sa méthode est la suivante : Chad ou un de ses collègues designers se rend chez le client et scanne ce qui doit l’être. Toutes les données sont ensuite transférées sur leur ordinateur de bureau exclusivement réservé au traitement dansArtec Studio.
« J’ai deux ordinateurs de bureau : un pour le traitement de toutes les données scannées, le second pour la modélisation CAO, explique Chad. Comme j’ai toujours des projets en cours, je préfère les réaliser en parallèle. » En fonction de la pièce scannée, il charge ensuite celle-ci soit dans SOLIDWORKS soit dans Autodesk Alias pour créer un modèle CAO solide.
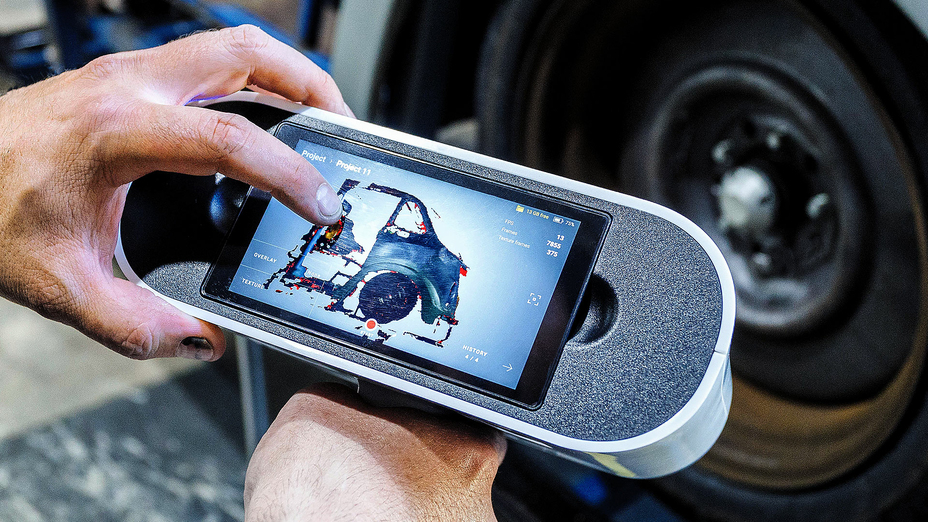
L’écran intégré d’Artec Leo permet à Chad de prévisualiser les résultats de son scan en temps réel (Photo fournie par streetmachine.com.au)
En utilisant un scanner 3D chez ses clients, Chad élargit aussi ses horizons professionnels : « À chaque fois que j’emmène Leo quelque part, je peux être quasiment certain de repartir de cet endroit avec un nouveau projet, raconte-t-il. Un client me recommande à quelqu’un d’autre, et ainsi de suite. » Sur le terrain, il collecte plus de données que nécessaire, étoffant ainsi son catalogue et recueillant des données précieuses de pièces devenues introuvables.
Le van International Metro de 1957
Jusqu'à présent, un des plus gros projets pour lesquels Chad a pu tirer parti de son scanner est le van International Metro de 1957 que Luke Williams, un associé travaillant dans un autre atelier automobile, et lui comptent restaurer de A à Z d’ici la fin de 2023.
Le propriétaire du van ne voulait pas simplement faire retrouver au véhicule son état d’origine mais aussi combiner son extérieur rétro à la puissance d'une voiture de sport avec un moteur survolté V8 HEMI Hellcat de 6,2 litres.
Fourni avec les modèles Dodge Challenger SRT® Hellcat, la plus puissante des muscle cars américaines modernes, le V8 offre plus de 700 chevaux, ce qui, à la différence du moteur d’origine du van, permettra à son propriétaire de conduire librement son van aux quatre coins du pays. Outre le moteur, il voulait également retoucher le design pour que le van paraisse moins « gonflé » tout en gardant tous les composants électroniques d'usine.
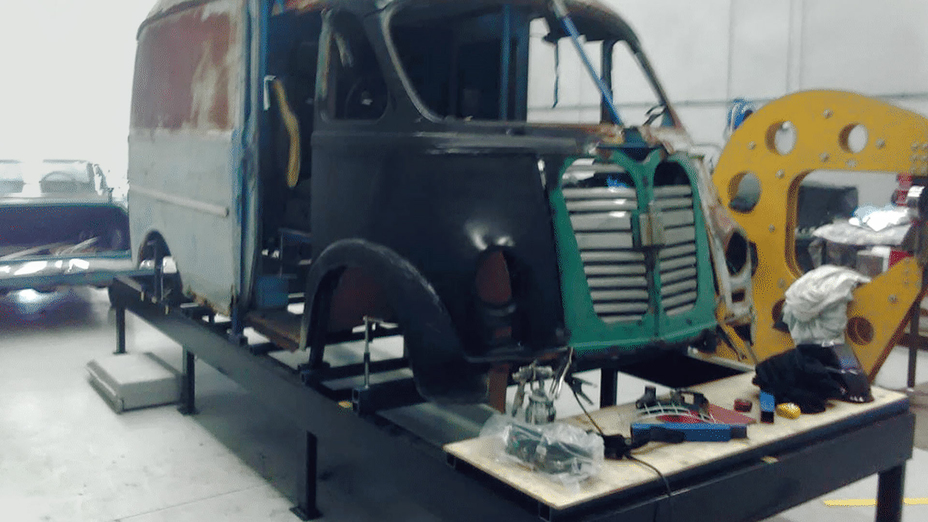
Carrosserie d'origine du van Metro de 1957 avant la restauration (Photo fournie par Chad Forward)
Après avoir pris note des exigences du propriétaire concernant le design et l'ingénierie et tracé de premières esquisses, Chad et Luke ont eu l’idée suivante : étant donné que la carrosserie du van était trop abîmée et rouillée pour la restaurer, il serait plus rapide de construire le véhicule entier à partir de zéro en utilisant les scans des pièces anciennes modifiées comme base pour la modélisation CAO de nouvelles pièces.
1reétape. Sculpter la carrosserie
Première étape : découper et sculpter la carrosserie. L'objectif était de modifier une carrosserie existante – ou une de ses pièces – de façon à lui donner la forme voulue, puis de scanner en 3D cette pièce et d’utiliser les données comme point de départ pour la modélisation CAO d’une carrosserie complète.
Pour ce faire, Luke a découpé une carrosserie d'usine avec une disqueuse, l’a ressoudée dans des positions légèrement différentes, puis a utilisé beaucoup de mastic et d’apprêt pour créer une surface matte dont il était satisfait.
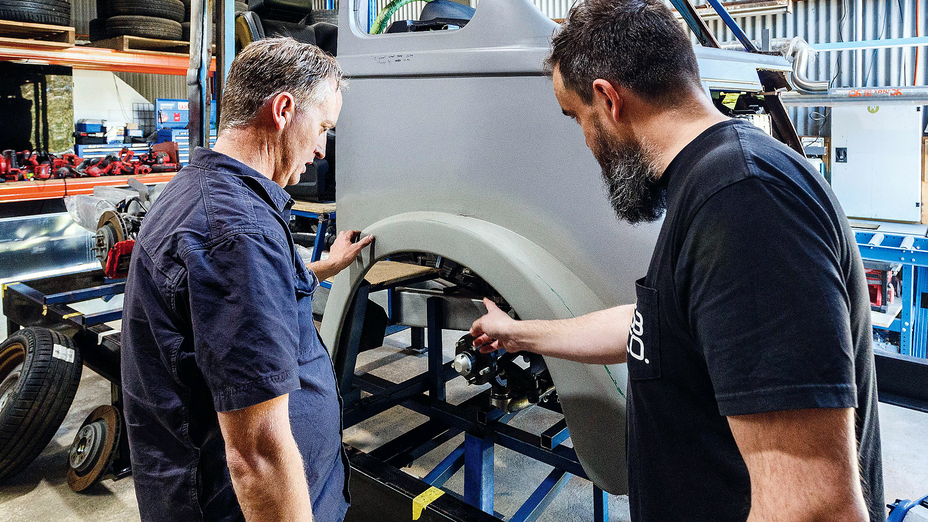
L'objectif était de modifier une des pièces de la carrosserie de façon à lui donner la forme voulue, puis de scanner en 3D cette pièce pour la modélisation CAO d’une carrosserie complète (Photo fournie par streetmachine.com.au)
2eétape. Construire le châssis
Pendant ce temps, Chad a installé tous les éléments de la transmission secondaire d’une Dodge Hellcat (le moteur, tout le câblage, la suspension avant et arrière) sur une plateforme qu'il a construite autour du châssis. Il voulait voir comment tous les éléments s’emboîtaient, s'ils respectaient les normes ADR (règles de conception australiennes), et les scanner pour savoir quelles nouvelles pièces du châssis devaient être modélisées en CAO.
3eétape. Scanner en 3D
Il a ensuite été temps pour Chad de scanner le coin gauche avant du van ainsi que le châssis et d’autres composants internes à l’aide d’Artec Leo. Le scan complet n’a pris que quelques minutes. Chad a ensuite téléversé toutes les données dans Artec Studio pour les traiter et créer un fichier .STL.
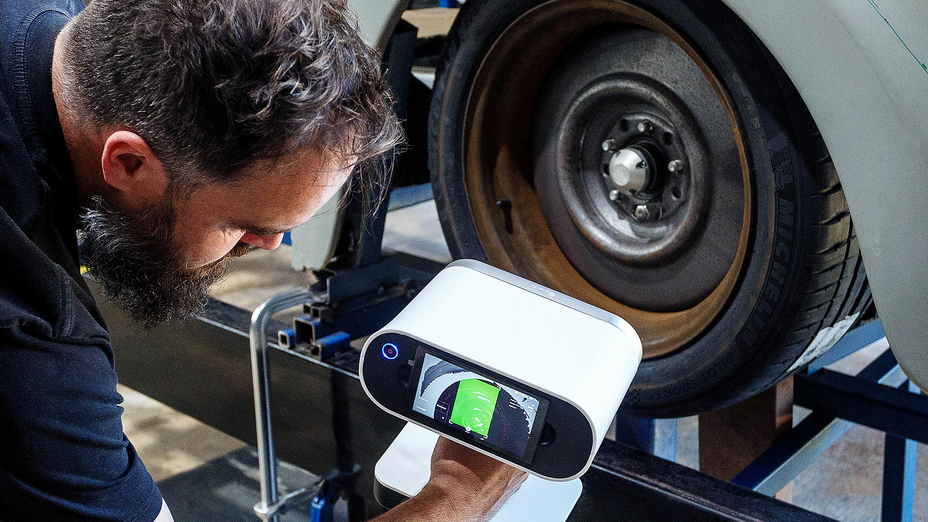
Chad scanne le van avec Artec Leo (Photo fournie par streetmachine.com.au)
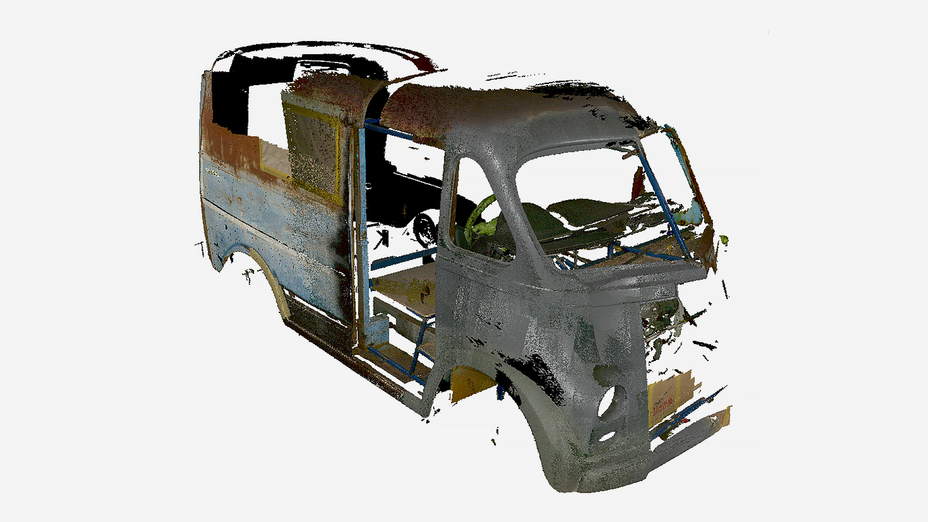
Scan 3D d'une carrosserie modifiée, scannée avec Artec Leo
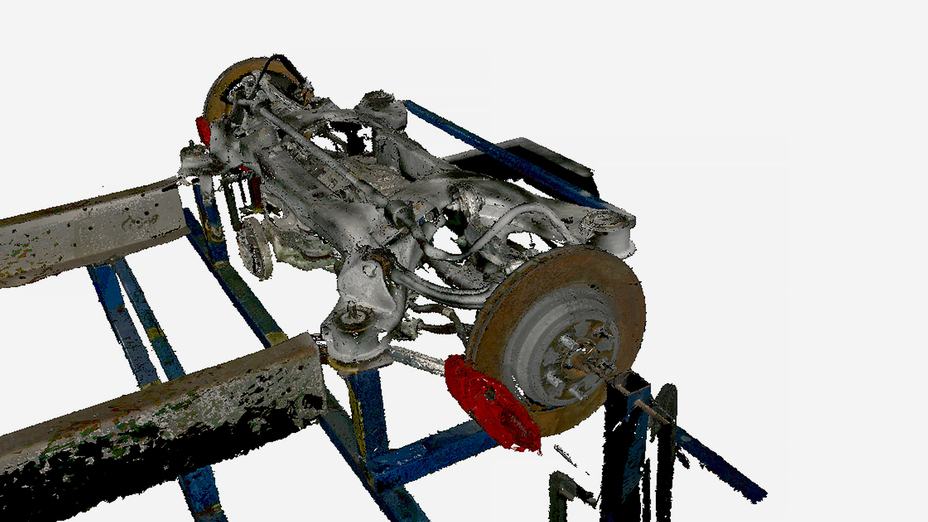
Scan 3D d’une suspension arrière
4eétape. Modéliser la carrosserie du van
Étape suivante : modéliser la surface de la carrosserie. Pour ce faire, Chad a importé les données de scan d’Artec Studio dans Autodesk Alias, un logiciel de CAO industrielle conçu pour les extérieurs de voiture, et a utilisé ces données comme références pour créer les croquis d'une future surface de carrosserie.
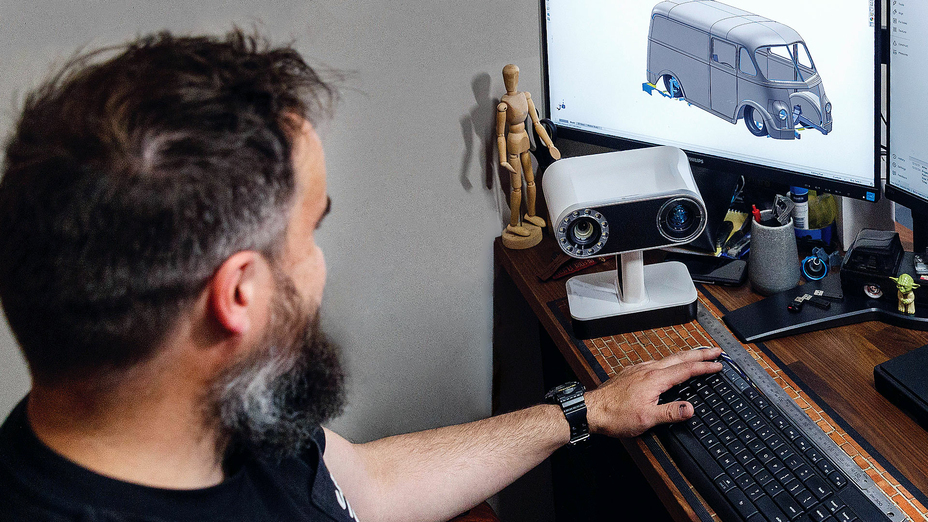
Chad utilise le logiciel Autodesk Alias pour créer des surfaces de carrosserie à partir de croquis qu'il trace au-dessus des données scannées (Photo fournie par streetmachine.com.au)
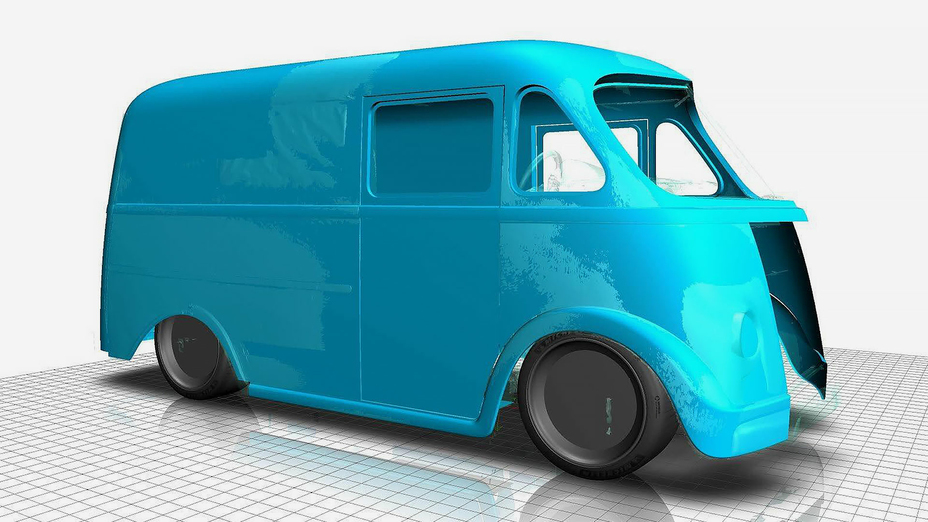
Scan 3D (bleu pâle) et données CAO (bleu) dans le logiciel Alias
5eétape. Modéliser le châssis
Pour modéliser le châssis et toutes les autres pièces d'ingénierie, Chad utilise SOLIDWORKS. En adoptant la même méthode, il a téléversé les données scannées avec Leo dans SOLIDWORKS et modélisé les nouvelles pièces autour des données. Disposer de copies 3D exactes des composants internes permet à Chad de les utiliser comme références précises lors du processus de conception et d’avoir une meilleure idée des difficultés qu'il pourrait rencontrer. Au fur et à mesure qu’il progresse dans son design, il scanne davantage de composants et les ajoute au logiciel comme modèles de référence.
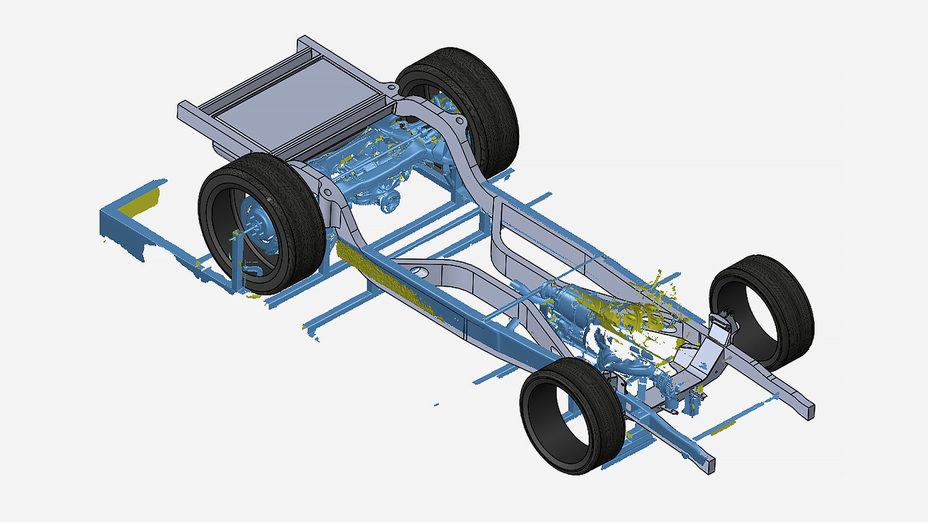
Chad utilise le scan du châssis à modéliser comme base pour créer un modèle CAO dans SOLIDWORKS
6eétape. Découper au laser & souder les nouveaux composants
Après l’étape SOLIDWORKS, Chad a envoyé tous les composants CAO à la découpe laser, puis au soudage.
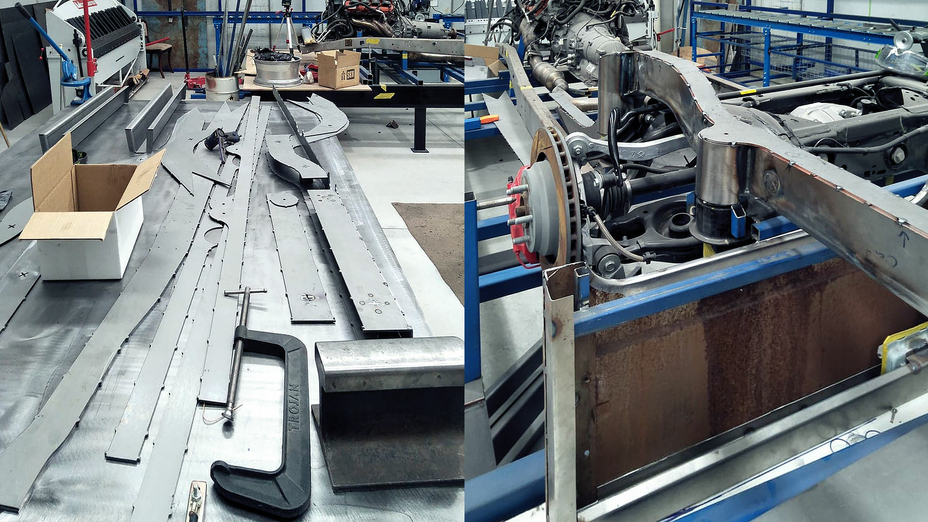
Découpe laser des pièces planes provisoirement attachées ensemble avant leur soudage final au châssis (Photo fournie par streetmachine.com.au)
Après le soudage de tous les composants du châssis, la structure interne complète a été envoyée à un électricien automobile pour assembler le châssis avec tous les composantes Hellcat d’origine. Parallèlement, Chad s’est préparé à découper la surface de la carrosserie modélisée à partir des données de scan (voir la 4eétape) pour construire un squelette de voiture qui pourrait ensuite servir à fabriquer les panneaux et le banc d’essai.
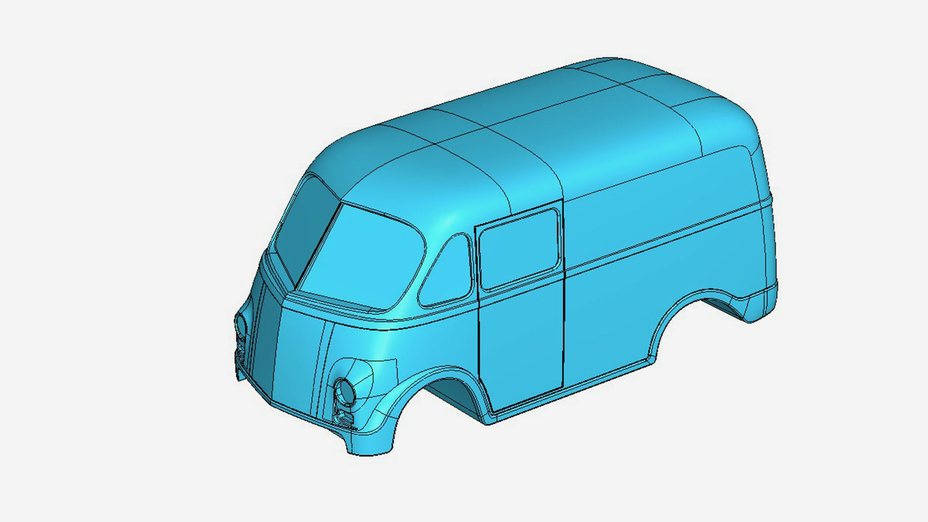
Design final du nouveau style de carrosserie que Chad utilisera pour créer le squelette de la carrosserie
L’équipe espère terminer le travail sur la carrosserie au cours des douze prochains mois et s’est donné quelques mois supplémentaires pour travailler sur l'intérieur, la peinture et d’autres menues tâches d'ici la fin de 2023. Une fois ce projet terminé, Chad espère qu'il deviendra une plateforme éducative pour d’autres studios et des clients.
« Le van Metro est un excellent exemple de la façon dont toutes les voitures devraient, d’après moi, être recréées, explique Chad. Bien que notre processus prenne du temps, cela prend encore plus de temps de redonner à une voiture son état d’origine que de la construire à partir de zéro grâce aux données acquises avec un scanner 3D. Pouvoir obtenir des informations en 3D, rétro-concevoir et fabriquer des composants en fonction de ce que j’ai scanné : voilà au fond ce pour quoi j’ai ouvert mon entreprise. »
« Dès que le Mode HD a été disponible, il m’a époustouflé : c’est comme si j’avais acheté un nouveau scanner. »
Chad n’a jamais regretté d’être passé au scan 3D. Pouvoircréer des copies numériques parfaites de pièces automobilesau lieu de les mesurer manuellement a révolutionné sa façon de travailler, la précision des données qu'il collecte et, de manière générale, sa productivité.
Et ce n’est que le début. « Je suis toujours impressionné par ce processus et les améliorations constantes apportées par Artec pour rester à la pointe, commente-t-il. À chaque mise à jour du logiciel, je ressens de toutes nouvelles émotions. La différence entre Artec Studio 15 et 16 est incroyable. Dès que le Mode HD est sorti, il m’a époustouflé. C’est comme si j’avais acheté un nouveau scanner. »