Cómo A.B. Engineering de Israel usa Artec Leo para el blindaje de vehículos personalizados
Desafío: Mientras trabajas con plazos ajustados, escanea en 3D de forma rápida y precisa vehículos reducidos, de modo que puedas construir los modelos CAD precisos necesarios para crear el blindaje personalizado de una amplia gama de automóviles, furgonetas, camiones y autobuses.
Solución: Artec Leo, Artec Studio, Dassault Systemes CATIA V5
Resultado: Ahora, con el Artec Leo, en sólo dos horas, un automóvil, camioneta o camión desmontado puede escanearse con precisión submilimétrica, de parachoques a parachoques. No se requieren aerosoles ni targets. Cinco horas de procesamiento, y los escaneos están listos para el CAD. El escáner 3D anterior del cliente exigía aerosoles, miles de targets y una semana entera para escanear dichos vehículos, además de una semana adicional para procesar los escaneos para el CAD.
¿Por qué Artec 3D?: Al ser 100% inalámbrico y sin computadoras portátiles, el Leo se puede sacar para escanear proyectos en cualquier momento. Lo suficientemente fácil para principiantes, pero lo suficientemente potente para los ingenieros de metrología, el Leo brinda a los clientes esa ventaja para completar proyectos más rápido, con mayor precisión, reduciendo así los costos y haciendo posible asumir entre un 200% y un 300% más de trabajo sin sacrificar la calidad.
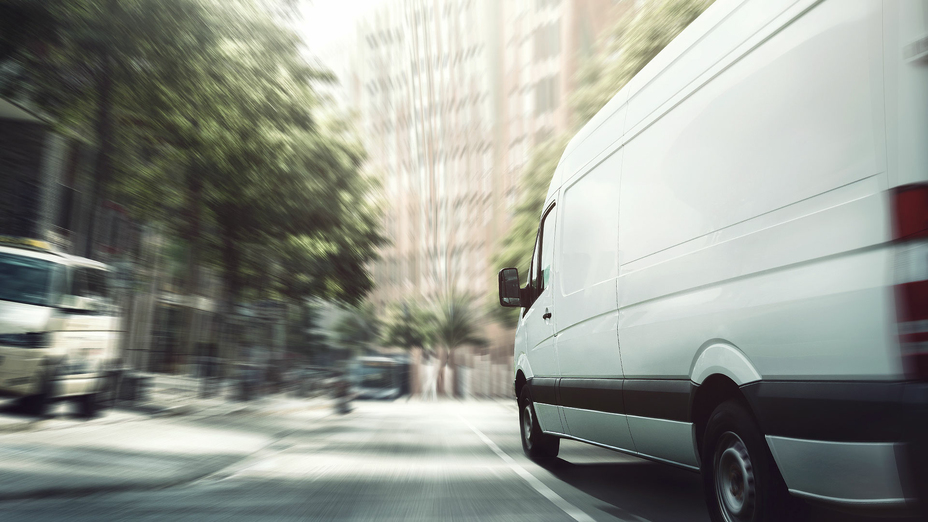
Mientras la minivan llena de niños y sus padres doblaba la esquina, los dos pistoleros estaban esperando. Saliendo detrás de los autos estacionados, levantaron sus AK-103 y abrieron fuego, ametrallando rápidamente el vehículo que se acercaba con ráfagas controladas de 3-4 balas.
Pero el conductor no se detenía. En segundos, las armas de los pistoleros estaban vacías y la minivan llena de balas se alejó a toda velocidad, sus ventanas quedaron destrozadas pero intactas. Todos los ocupantes dentro temblaron pero resultaron ilesos.
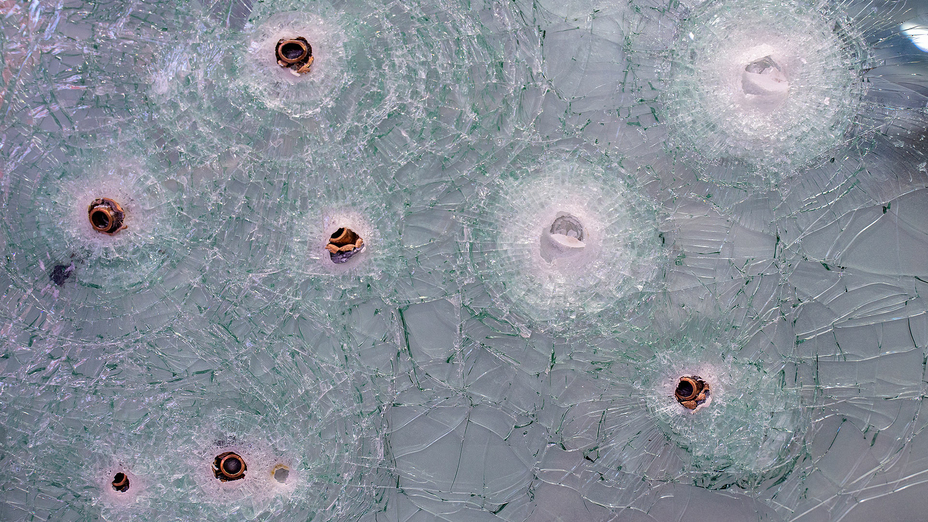
Vidrio resistente a balas
Vehículos blindados: no sólo para papas y presidentes
En todo el mundo, desde Ucrania hasta Oriente Medio y más allá, la necesidad de vehículos blindados nunca ha sido mayor. No sólo para militares, gobiernos y los ultra ricos, sino también para las agencias y grupos humanitarios, para transportar pasajeros de manera segura incluso a través de las áreas más peligrosas.
Los mejores de estos vehículos resistentes a las balas están discretamente blindados con varios compuestos, aceros y cerámicas, suficientes para detener una variedad de amenazas balísticas, desde el calibre .22 hasta .50, dependiendo del nivel de armadura elegido para cada vehículo individual.
El objetivo es lograr la máxima protección mientras con un mínimo de peso.
Piensa en el blindaje como hacer un traje a medida para un vehículo, aunque se use en el interior. Debe encajar lo más perfectamente posible, por varias razones.
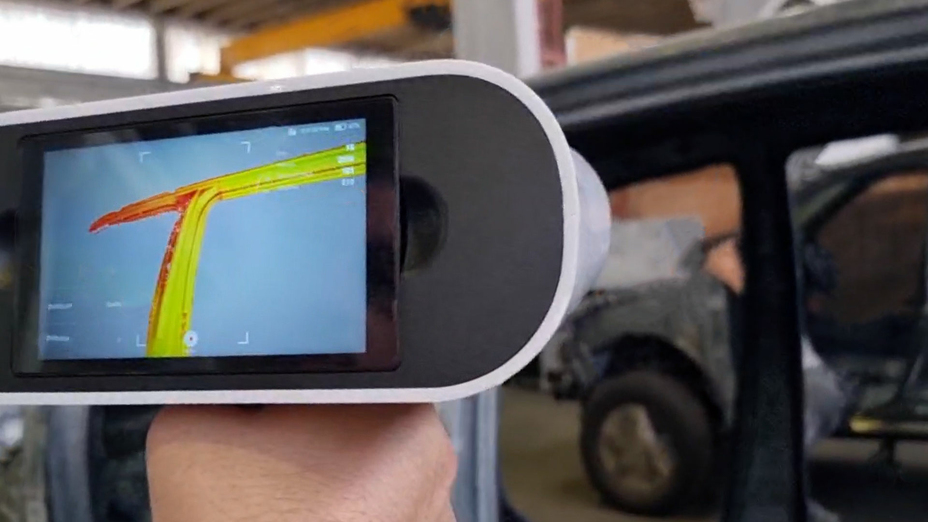
Artec Leo 3D escaneando el marco de una Toyota Hi-Lux 2022. Imagen cortesía de A.B. Engineerin
A veces es necesario poder reinstalar las piezas interiores OEM en sus ubicaciones originales, con cambios mínimos por obvias razones de costo. Y si se pide, el vehículo debe parecer discreto para la persona (pistolero armado) en un peaje que hable con el conductor.
Luego, una vez que todo está en su lugar, los ocupantes no deberían sentir ninguna pérdida de espacio libre. Y, finalmente, el blindaje debe ser indetectable desde el exterior, de modo que incluso los ojos bien entrenados no puedan distinguir tales automóviles, furgonetas y autobuses protegidos de los vehículos ordinarios y no modificados.
Tales «solicitudes de sigilo» son hechas por los clientes en una misión específica, automóvil por automóvil, con requisitos que establecen a qué distancia de visualización debe verse el vehículo común. Estas distancias pueden variar desde 160 pies (50 metros) hasta de cerca y en persona, de pie justo al lado del vehículo.
Para lograr una hazaña tan desafiante, el vehículo primero debe ser desmontado de su bastidor y elementos más básicos, y a partir de ahí, medido con la mayor precisión posible, en cada milímetro cuadrado.
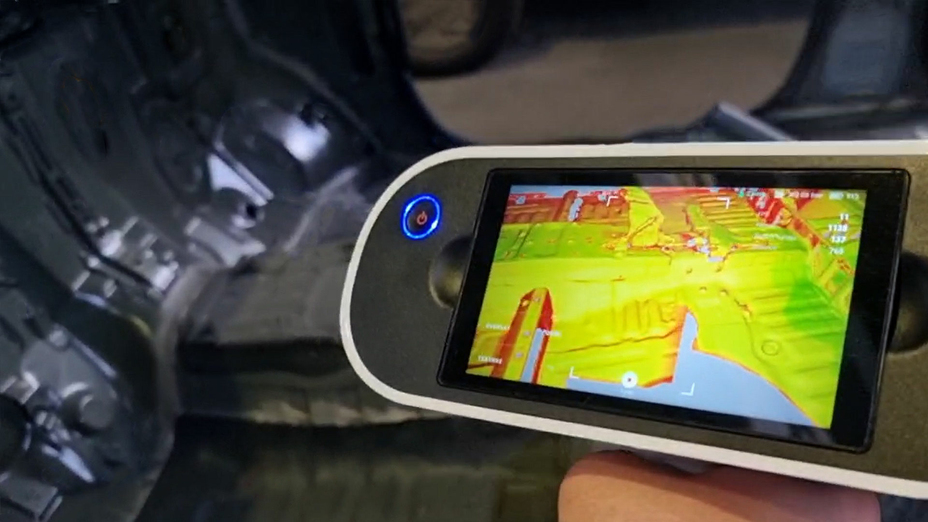
Artec Leo 3D escaneando el marco del Toyota Hi-Lux. Imagen cortesía de A.B. Engineering
Luego, en las siguientes etapas, todos los elementos de blindaje personalizados pueden diseñarse en CAD y fabricarse bajo condiciones estrictas para que una vez que se instalen y las piezas OEM se vuelvan a colocar en su lugar, existan pocos o ningún espacio entre el blindaje, las puertas y cualquier otra sección potencialmente vulnerable del vehículo.
Cuando esto no es posible, se crea un nuevo acabado interior personalizado para imitar perfectamente el acabado interior del OEM, pero con más espacio asignado para la armadura.
Es un proceso que puede tomar de 1 a 2 meses para un vehículo pequeño, como un camión Toyota J79, hasta más de 4 meses para un SUV grande y complejo, por ejemplo, un Chevy Suburban.
Blindaje de vehículos mediante escaneo 3D
Uno de esos especialistas en blindaje de vehículos con una merecida reputación en la industria es A.B. Engineering Ltd. de Israel, una empresa de ingeniería mecánica que trabaja con las principales empresas aeroespaciales y de defensa desde 2012. En la base misma de su flujo de trabajo de blindaje integral está el escaneo 3D.
Según el fundador y CEO de la empresa, Irakly (Ika) Baitish, «cuando se trata de blindar un vehículo para la máxima protección de sus ocupantes, así como el motor, el tren motriz y otras partes esenciales que mantienen el vehículo rodando para que pueda escapar de la zona de peligro, es absolutamente importante comenzar con mediciones precisas».
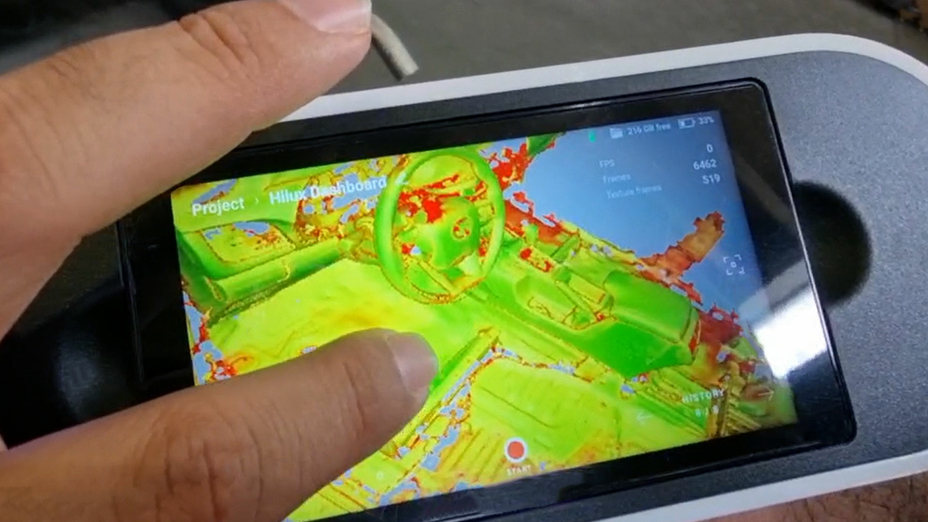
Revisando un escaneo 3D del Hi-Lux en la pantalla táctil de Leo. Imagen cortesía de A.B. Engineering
Continuó: «es por eso que elegimos el escaneo 3D como nuestro medio de medición preferido, porque con él podemos obtener las dimensiones exactas de todo el vehículo, incluidas las áreas que normalmente son difíciles de medir manualmente, como el firewall, la sección que separa al conductor del compartimiento del motor».
Una vez que se han procesado los escaneos 3D del vehículo, se exportan los escaneos a su sistema CAD, Dassault Systemes CATIA V5.
Allí, utilizan los escaneos como modelos de referencia para diseñar los paneles balísticos que pronto se fabricarán y otros componentes de blindaje, y luego los instalan virtualmente en el vehículo, para garantizar que sus resultados finales garanticen una protección perfecta y sin espacios, de parachoques a parachoques, después de que se instale el blindaje en las próximas semanas.
Encontrar el escáner 3D adecuado
Pero no todos los escáneres 3D son iguales. Al principio, Ika y su equipo estaban utilizando un conocido escáner 3D portátil de alta gama para su trabajo, uno que requería un gran número de targets y grandes cantidades de aerosol, así como una computadora portátil, algunas capacidades y una fuente de alimentación de 220V.
Un ejemplo de un proyecto típico en ese momento fue cuando estaban escaneando la cabina y el chasis desmontados de un Skoda Kodiaq que necesitaba blindaje.
Después de aplicar más de 3,000 pegatinas y los volúmenes necesarios de aerosol, les tomó dos semanas completas escanear, y los datos resultantes no fueron tan limpios como lo que necesitaban.
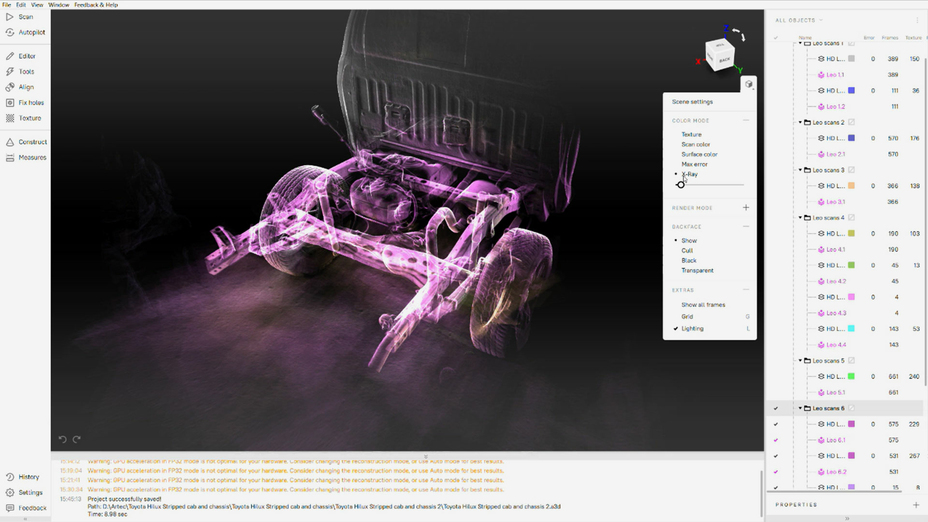
Captura de pantalla de Artec Studio: Vista en modo de rayos X del escaneo Leo de la parte trasera del Hi-Lux. Imagen cortesía de A.B. Engineering
Antes de que pudieran unir con confianza los escaneos y crear un modelo 3D altamente preciso para el CAD, siguió otra semana de limpieza de los datos y remediciones manuales.
Uno de los compañeros de equipo (el que tuvo peor suerte) se encargó de despegar los más de 3,000 objetivos del vehículo y luego le tocó limpiarlo. Desafortunadamente, algunas de las pegatinas dejaron residuos en los paneles de adorno interiores, haciéndolos inutilizables.
Al observar la cantidad excesiva de tiempo y esfuerzos que esto implicaba, Ika entendió que su escáner 3D estaba ralentizando seriamente a su equipo.
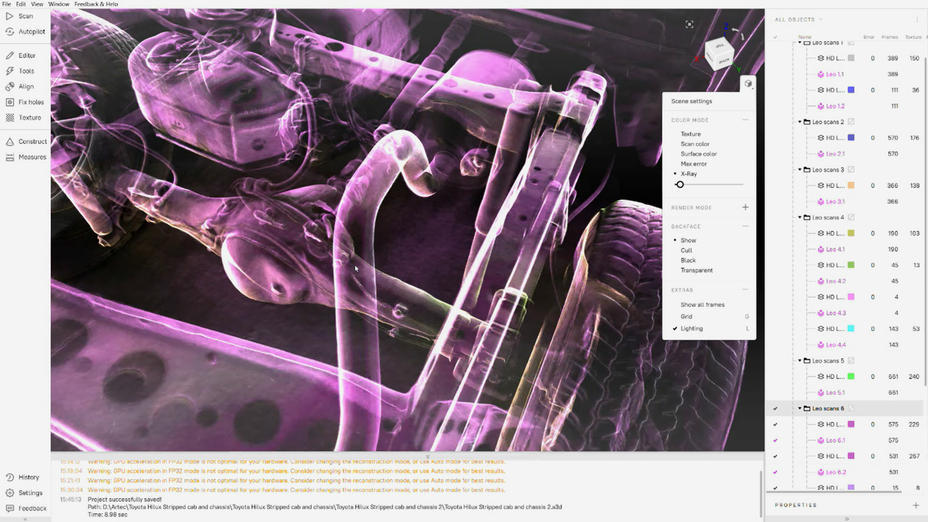
Captura de pantalla de Artec Studio: Vista en modo de rayos X del escaneo del Leo de la parte trasera de la Hi-Lux. Imagen cortesía de A.B. Engineering
En una industria donde los plazos de los proyectos no son flexibles, cada día y cada hora pueden marcar la diferencia. Entonces, una vez que el proyecto estuvo terminado, Ika comenzó a buscar fervientemente un mejor escáner 3D.
Decir adiós a semanas de escaneo, targets y sprays
Pronto encontró el sitio web de Artec 3D y se centró en Artec Leo, un escáner 3D de mano profesional que ha sido uno de los favoritos para la ingeniería inversa, la medicina forense, la atención médica y otras aplicaciones durante años.
Al ofrecer escaneos 3D en color de alta resolución con precisión submilimétrica, el Leo cuenta con una pantalla táctil y un paquete de baterías incorporado, lo que lo hace 100% portátil, con una alta tasa de captura de FPS y un gran campo de visión de escaneo.
Escaneando una Toyota Hi-Lux 2022 más rápido que nunca
Para destacar un solo ejemplo de cómo el flujo de trabajo de A.B. Engineering ha mejorado desde que adoptó el Leo, uno de sus proyectos de blindaje recientes requirió escanear la cabina y el chasis desmontados de un camión Toyota Hi-Lux de 4 puertas 2022.
Con el Leo en mano, Ika y su equipo se pusieron a trabajar capturando la Toyota. Sólo dos horas después, sin tener que aplicar un solo objetivo o un chorro de aerosol, terminaron completamente con el escaneo.
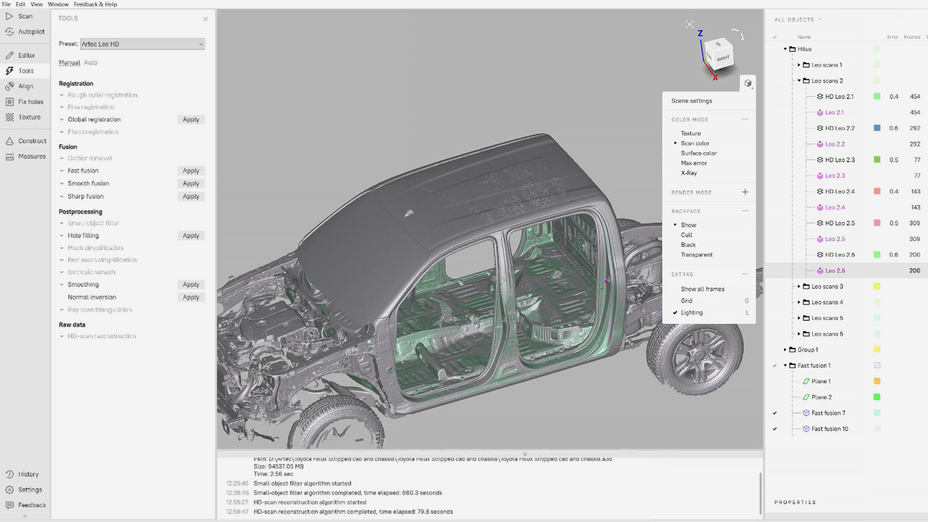
Captura de pantalla de Artec Studio: escaneos Leo combinados de la Hi-Lux. Imagen cortesía de A.B. Engineering
A partir de ahí, tomó solo cinco horas en el software Artec Studio procesar los escaneos y crear los archivos STL que se enviaron al CAD para definir el blindaje para la Hi-Lux.
En comparación con una semana de escaneo de su escáner anterior, más otra semana de procesamiento de escaneo para lograr casi los mismos resultados, pero con una calidad notablemente menor, el contraste fue asombroso.
En palabras de Ika, «recordando cómo solía ser, el Leo nos da una diferencia de velocidad increíble. Y los datos que obtenemos con el Leo son mucho más limpios, sin problemas de desalineación en absoluto».
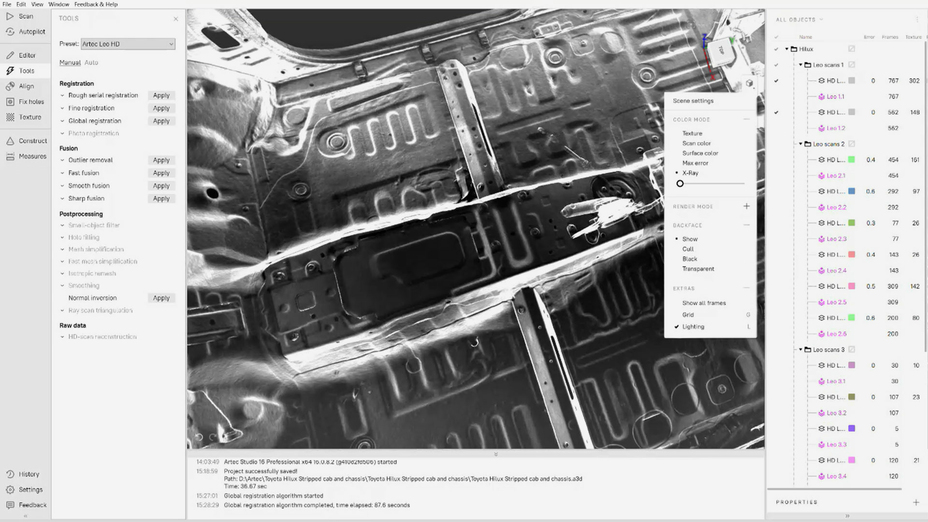
Captura de pantalla de Artec Studio: Vista en modo de rayos X del escaneo Leo del interior de la Hi-Lux. Imagen cortesía de A.B. Engineering
Continuó: «nuestro proceso de medición ha mejorado significativamente tanto en términos de tiempo como de calidad. Leo ha cambiado drásticamente la calidad de nuestra producción de ingeniería y la capacidad de obtener ese pequeño porcentaje adicional necesario para cerrar las brechas balísticas, lo que literalmente puede salvar vidas».
«Todos y cada uno de los vehículos exigen un enfoque personalizado»
Para cada vehículo que blindan, Ika y su equipo consultan con el cliente, teniendo en cuenta el grado de protección balística necesario, el uso previsto del vehículo, así como las expectativas con respecto a los plazos y las actualizaciones del vehículo secundario requeridas.
Teniendo en cuenta esto último, un trabajo de blindaje típico puede agregar fácilmente 500-2,000 libras (230-900 kg) al peso total de un vehículo. Para acomodar tal aumento, ocasionalmente se requieren frenos, ejes, transmisiones y transmisiones especiales de servicio pesado.
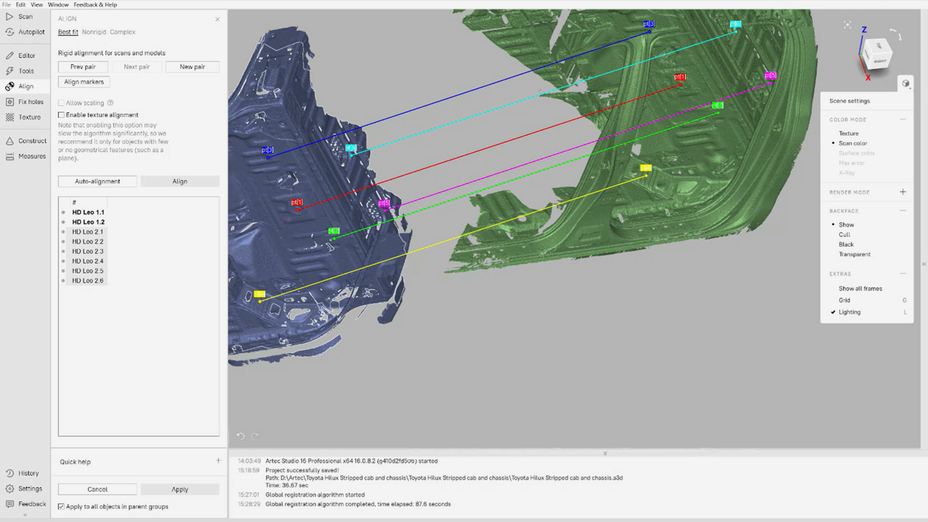
Alineación sencilla de los escaneos del Leo de la Hi-Lux en Artec Studio. Imagen cortesía de A.B. Engineering
«Dado que este refuerzo del vehículo implica que se agregue mucho peso adicional», dijo Ika, «esto nos impone una presión aún mayor para optimizar el blindaje, con el peso más bajo y con los más altos grados de cobertura defensiva».
Continuó: «ahora que tenemos al Leo, lograr este tipo de máximos resultados es mucho más rápido y fácil».
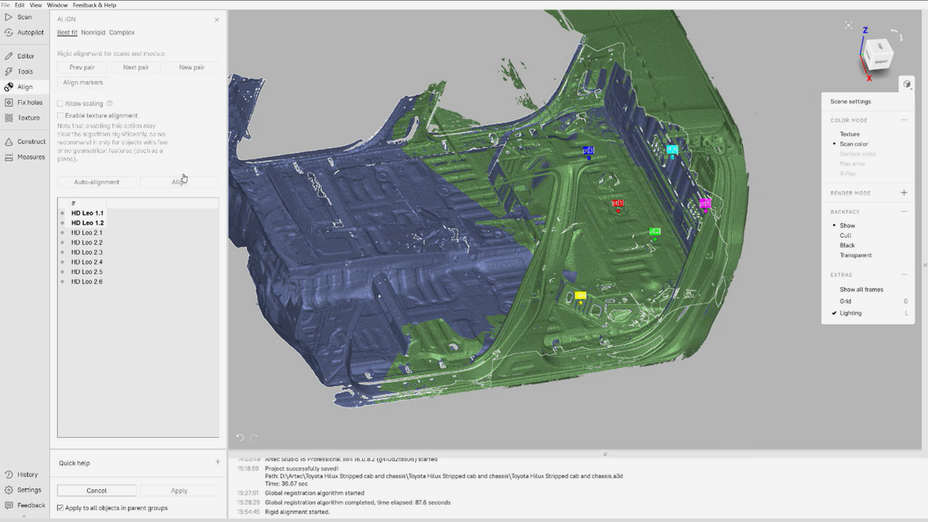
Con solo unos pocos clics, los escaneos de la Hi-Lux se alinean en Artec Studio. Imagen cortesía de A.B. Engineering
Probando su trabajo en el campo de tiro con fuego real
Ika y su equipo respaldan firmemente su trabajo, independientemente del tamaño o la complejidad del proyecto, y Leo les permite hacerlo con mayor confianza. Una demostración reciente de la calidad de su blindaje habla por sí misma.
Uno de sus vehículos, un camión blindado pesado, fue llevado a una instalación de prueba de fuego real, donde se dispararon más de 800 rondas de todos los calibres (hasta .50) de una variedad de armas contra el vehículo, con cero penetraciones.
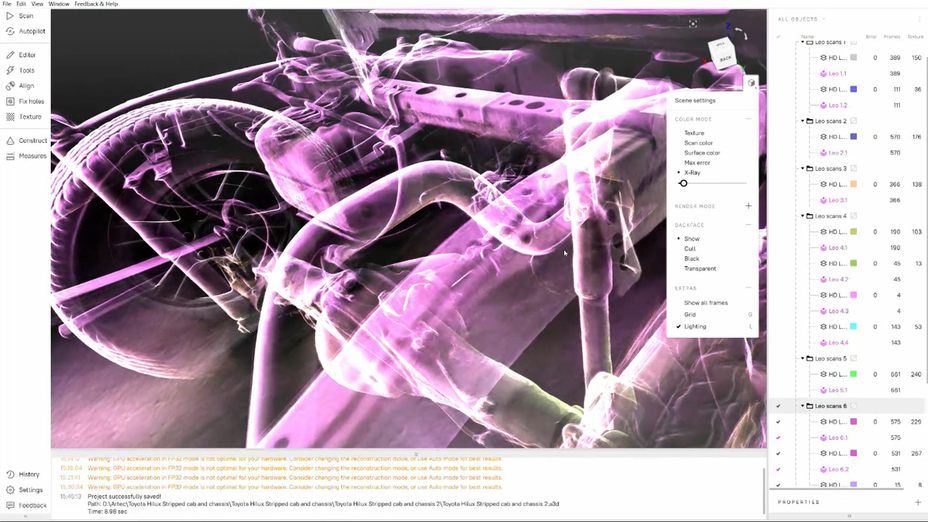
Vista en modo de rayos X de Artec Studio de los escaneos del Leo de la parte posterior de la Hi-Lux. Imagen cortesía de A.B. Engineering
Mientras tanto otro vehículo blindado, uno de una empresa competidora, fue sometido a un aluvión similar de balas de las mismas armas. Sufrió cientos de penetraciones, mucho más allá del punto en que, si ese hubiera sido un escenario de la vida real, los ocupantes habrían tenido cero posibilidades de supervivencia.
Tener el Leo y viajar: blindando coches, camiones, autobuses y aviones
Desde hace años, el equipo de ingenieros y técnicos experimentados de A. B. Engineering ha realizado un amplio portafolio de proyectos de blindaje, desde simples hasta complejos, para una amplia variedad de vehículos, aeronaves y otros objetos.
«Debido a que el Leo es fácil de llevar con nosotros, estamos subiendo a un avión y volando donde sea que nos lleve nuestro próximo proyecto. Cuando lleguemos allí, sabemos que terminaremos más rápido que nunca, y todos los datos estarán allí en la tarjeta SD del Leo, limpios y listos para funcionar», dijo Ika.
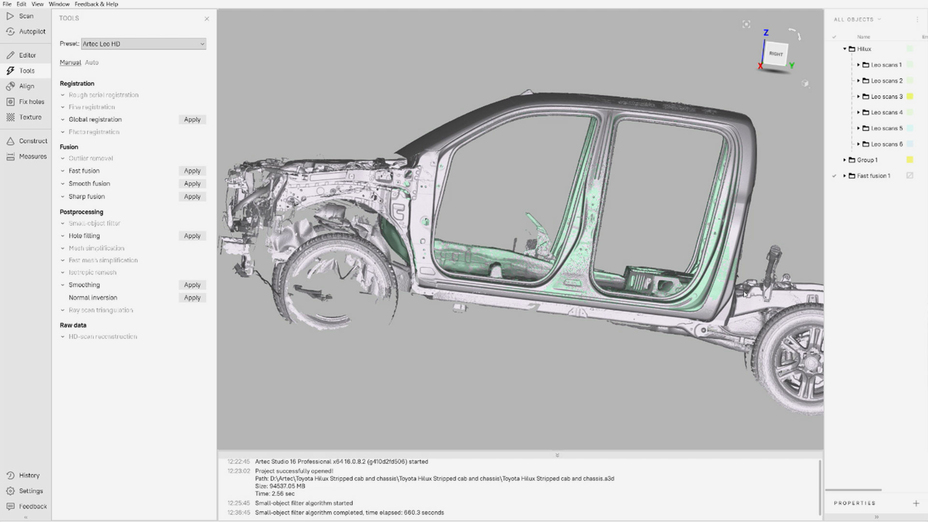
Listo para el CAD: captura de pantalla de Artec Studio de los escaneos del Leo combinados de la Hi-Lux. Imagen cortesía de A.B. Engineering
Continuó: «el solo hecho de tener la capacidad de llevar únicamente el escáner, sin siquiera una computadora portátil, al campo en cualquier parte del mundo es una gran ventaja, y la opción de escanear sin targets es otro beneficio masivo, ya que no necesitamos preparar el objeto que estamos escaneando. Y esto también significa que no dejamos rastros del proceso de escaneo, que a veces puede ser crítico».
Un flujo constante de clientes y referencias durante todo el año
Desde una perspectiva empresarial, el Leo le ha permitido a Ika y a su equipo ser mucho más competitivos. Hoy, con el Leo en la mano, cada proyecto que incluye escaneo 3D toma 2 semanas menos de tiempo de ingeniería que antes. Esto le permite a la empresa cotizar precios más bajos a sus clientes, lo que resulta en un flujo constante de clientes y referencias durante todo el año.
Ika explicó: «antes de adoptar al Leo, el escaneo 3D representaba entre el 20 y el 30 por ciento del costo total para el cliente, debido a todo el tiempo que exigía. Pero con el Leo, el escaneo es solo del 5 al 10 por ciento del costo del proyecto. Por lo tanto, en algunos casos podemos cobrar un 20 por ciento menos que un competidor que usa un escáner 3D menos avanzado, como el que solíamos tener».
Scanners behind the story
Try out the world's leading handheld 3D scanners.