Tucci Hot Rods modernizing vintage muscle car modification with Artec Leo
Challenge: US automotive modding firm Tucci Hot Rods sought a faster way of digitizing parts so they could be customized and used to build customers’ dream cars.
Solution: Artec Leo, Artec Studio, Rhinoceros 3D
Result: Rather than sizing up the lights, vents, grills, and other areas of automotive classics via a series of cut-outs, Tucci Hot Rods digitizes them with 3D scanning. This allows the firm to modify parts in such a way that they turn out exactly how owners envisioned they would, before 3D printing them in a more efficient, accelerated workflow.
Why Artec 3D? With Artec Leo, the firm is able to more accurately capture hotrod parts before using Artec Studio to edit resulting models, so they’re easier to send for production.
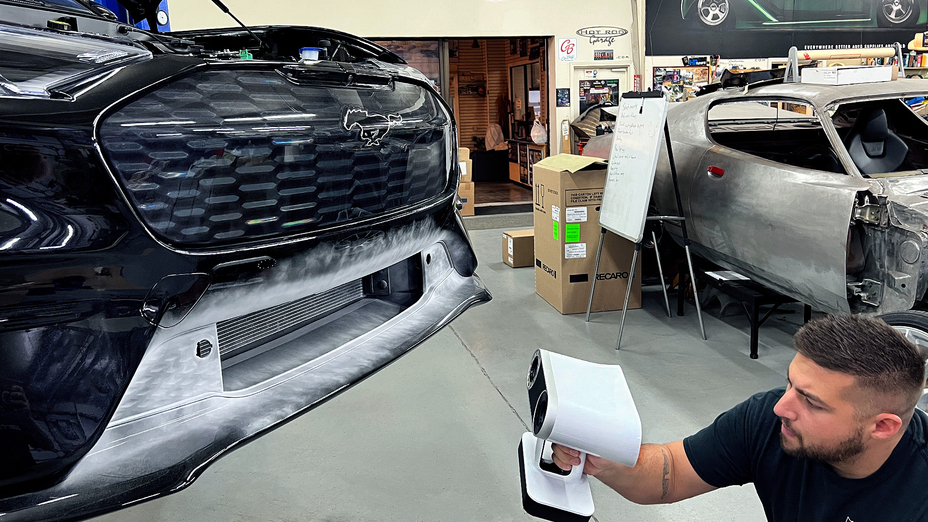
Dom Tucci using Artec Leo to scan the front of a Ford Mustang. Image courtesy of Tucci Hot Rods
Hotrods hold a special place in automotive folklore. Their roots can be traced all the way back to the Great Depression, an era that spanned the 1930s, when many young Americans, short on money but with plenty of time on their hands, experimented with modifying cars.
Not only built for eye candy, these vehicles were modified to race. Alongside flamboyant mods scrounged and swapped among drivers, many featured performance upgrades, and after World War II, formal hotrod racing championships sprung up across the US and Europe.
To this day, the racing of hotrods – a term now used to describe engine-modified vehicles young and old – is still a popular pastime for automotive enthusiasts. Seeking to recapture some of the magic that made the originals so special, some collectors also continue to modify early-to-mid-20th-century vehicles – but the process of doing so is easier said than done.
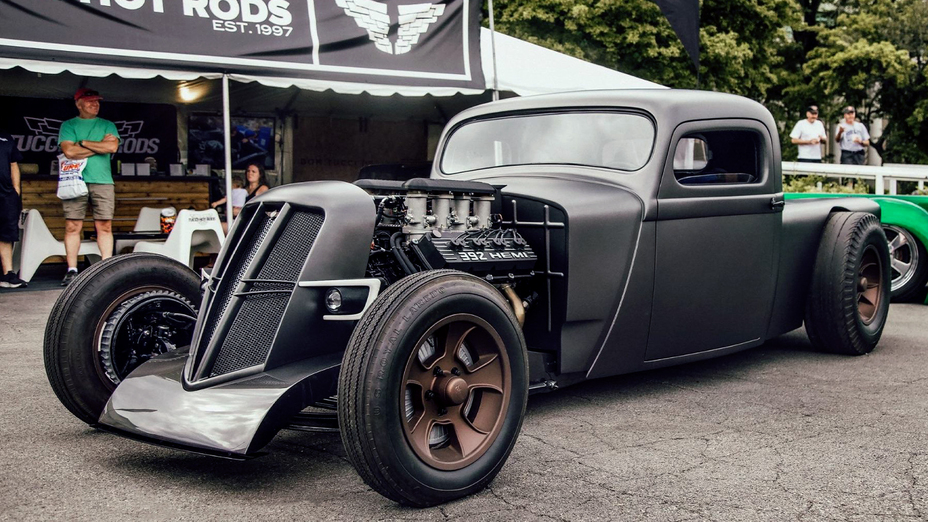
A classic 1936 Dodge truck modified by Tucci Hot Rods. Image courtesy of Tucci Hot Rods
With the production of most classic car parts long having ceased, and some of their designs lost to the pages of history, modding requires many to be remodeled from scratch. While it’s possible to do so via traditional, manual patterning techniques, Tucci Hot Rods has now found a way of making the process faster and more accurate: with the help of Artec Leo.
Tuning at Tucci Hot Rods
Over the past quarter of a century, Tucci Hot Rods has established itself as a major force in the US modding arena, with clients everywhere from New York to Nevada. Initially founded by Dave Tucci Jr. and his wife Jill, the firm continues to be family-led, with their son Dominick Tucci now onboard as an Industrial Designer.
Customers tend to approach the company with plans that are often broad, revolving around a desired style or engine, and with no means of bringing them into reality. And this is where Tucci Hot Rods has made its name: as a partner that walks car modification enthusiasts through the entire journey, from initial design to fabrication and assembly.
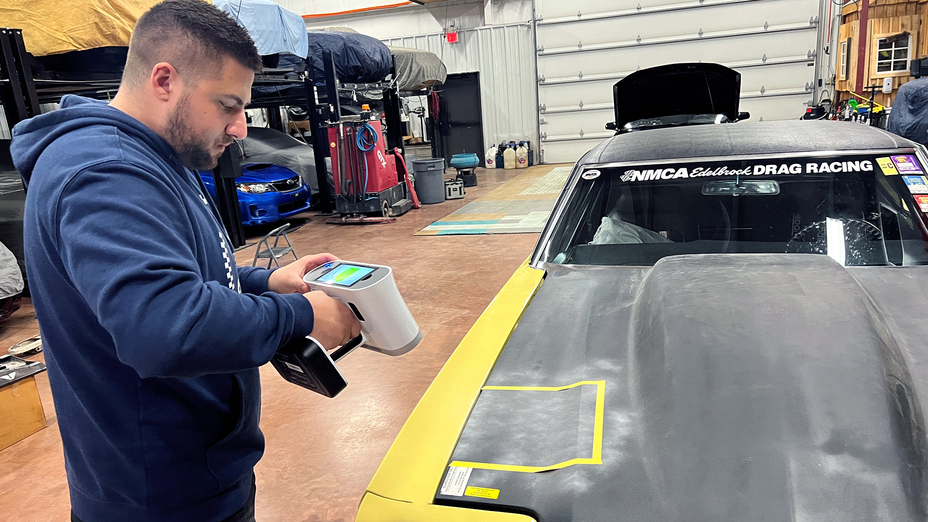
Tucci with an Artec Leo, 3D scanning the front of a vintage Chevrolet hotrod. Image courtesy of Tucci Hot Rods
Impressively, the firm has devised a way of integrating extrusion and resin 3D printers into its workflow, which allows for the creation of custom end-use auto parts like lenses, light covers, and vents. Until recently, though, the company also faced considerable challenges around the way it gained the measurements needed to make such modifications fit.
“Say you have a complex metal shape – you could make a pattern of one side, a pattern of the other, take measurements, and then connect the dots to make something that was close to fitting exactly,” explained Dominick Tucci.
“But we used a lot of cardboard, and there was also a lot of printing prototype pieces, seeing what fit, making changes, printing new ones. Lots of back and forth. If I made a really nice template, it could take me two hours. At that point, it may not even be perfect either.”
Modernizing car customization
In an effort to shake up Tucci Hot Rods’ part-fitting approach, Tucci began to experiment with 3D scanning a few years ago. At first, this saw him toy with an Xbox Kinect camera and cheap scanning software, and while it could only “pick up really rudimentary surfaces,” he said it “gave him an idea of how it would work,” if he could get hold of a higher-end device.
Having seen Artec 3D scanners at a trade show in 2021, Tucci reached out to Artec Ambassador Digitize Designs, who helped choose the correct device and software to meet Tucci Hot Rods’ needs. While he considered corded scanners, the designer says the fully wireless Artec Leo’s all-in-one nature and built-in display were dealmakers for him and his firm.
“I’ve used scanners before where it’s connected to a computer, and you’re constantly looking at what you’re getting, and making sure you’re getting it,” added Tucci. “With Artec Leo, you’re looking directly at it the whole time. Plus, the fact that it’s so portable has already come in really handy a bunch of times.”
Adopting Artec 3D scanning has also allowed Tucci Hot Rods to reduce its lead times. Before, it would’ve taken up to two hours to template part of a customer’s car and then as much as 20 hours to 3D print a prototype – depending on modification complexity. Thanks to Artec Leo’s 0.1 mm point accuracy and its data capture speed of up to 35 million points per second, Tucci and his colleagues are now able to model guaranteed-to-fit parts in minutes.
“A process of three to four days of back and forth – replaced with just 15 minutes of scanning.”
Even in one of his very first projects to benefit from 3D scanning, which saw him design custom tail lights for a classic Dodge, Tucci says the cost and lead time savings were clear.
“Initially, we spent 3-4 days going back and forth, templating, printing a test piece, changing it, printing another. Prints were a minimum of 8-9 hours, and these were made of cheap material as well – not the stuff I used for end parts,” said Tucci. “In the end, we were talking 3-4 days of back and forth, a process we replaced with just 15 minutes of scanning.”
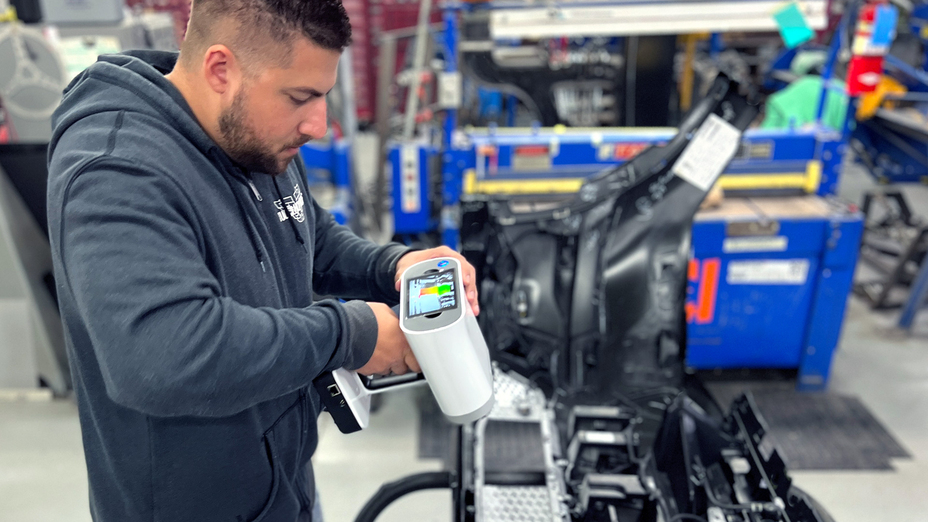
Tucci Hot Rods has found Leo’s built-in display to be a particularly useful feature. Image courtesy of Tucci Hot Rods
“Our collaboration with Tucci Hot Rods, a connection made through a satisfied customer, has enabled us to deliver superior 3D scanning expertise,” added Digitize Designs’ Kyle Burdine. “After an assessment, we recommended Artec 3D as the ideal fit for Dom’s operations. The dividends of this relationship are clear, with high ROI and continued innovation in the auto mod industry.”
Artec Studio has also played its part in improving the company’s productivity. Tucci said he initially worried about “capturing scans with enough detail, but not so much that it couldn’t be moved around Rhino 3D,” a popular CAD design software.
However, with the guidance of Digitize Designs, he has since learned to use Artec Studio mesh simplification to reduce model complexity and avoid this problem entirely. Using the program, it’s now possible to remove small polygons, set a maximum level of deviation, or even target a polygon count, to optimize results, and make models easier to manage when exported to other platforms.
“In Artec Studio, I started to mess around with the tools for reducing the number of polygons in a mesh. Every time I tried to do so in Rhino, it’d crash,” added Tucci. “I realized that I’d rather do that in Artec Studio and bring it into Rhino later.”
“I did a few training sessions before we got the scanner on how to use Artec Studio and process scan data for certain things. It works really well for what we do with it.”
Automotive 3D scanning and beyond
Since turning to Artec 3D scanning, Tucci Hot Rods has digitized all sorts of automotive parts, ready for modification and building on. One of the first it scanned was the grill of a classic 1936 Dodge truck.
According to Tucci, the component’s complex convex outer shape made it particularly tricky to model with traditional methods, and initial prints were a quarter of an inch off at the front and back. Given that there was “not much room for error” in that part of the vehicle, and he says it was “really critical that it fitted exactly,” 3D scanning was a necessity for the project.
In the end, the firm was able to use scan data as a basis for 3D printing headlight covers that perfectly fitted around the car’s grill. Following on from this success, Tucci and his colleagues have gone on to customize vintage Fords, including a 1970 Mustang muscle car and a 1931 Model A sedan.
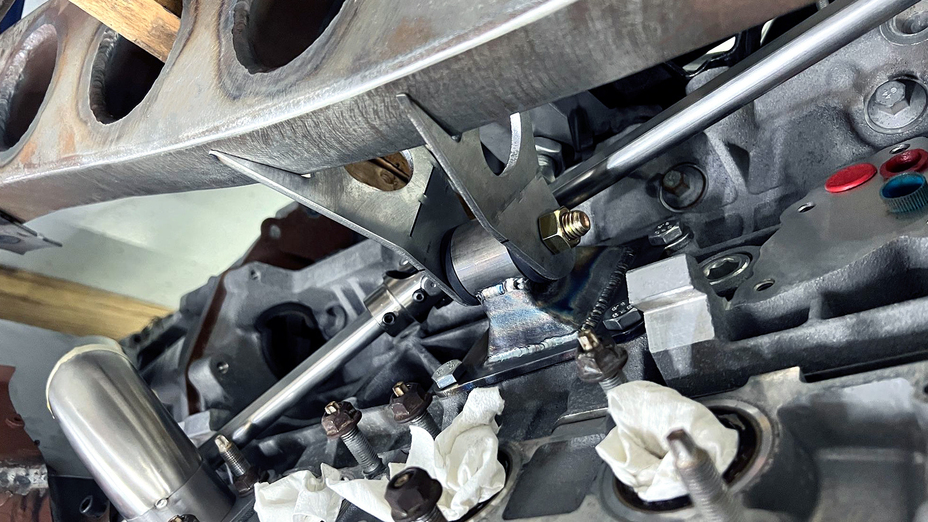
A Tucci Hot Rods custom motor mount fabrication installed on a vintage Model A. Image courtesy of Tucci Hot Rods
“To customize the Model A, we would previously have mounted its motor on frame rails, and cardboard patterned everything,” explained Tucci. “With 3D scanning, I was able to capture the motor and frame in place, draw all the motor mounts, laser cut them out, and then everything just fit right off the bat.”
“If you consider that we charge, let’s say $95-100 per hour as a labor rate, and customizing each car takes 12-18 months, even minor time savings can be hugely beneficial.”
Tucci Hot Rods’ portfolio continues to diversify, with one client recently asking for a modern 2022 Ford Maverick to be digitized, and another wanting to capture a cleanroom.
Through several floors at the latter’s silicon wafer chip plant, concrete-casted holes had been made to accommodate the multi-level piping of machines and pumps. To avoid spillage on different floors, tiny curbs needed to be installed.
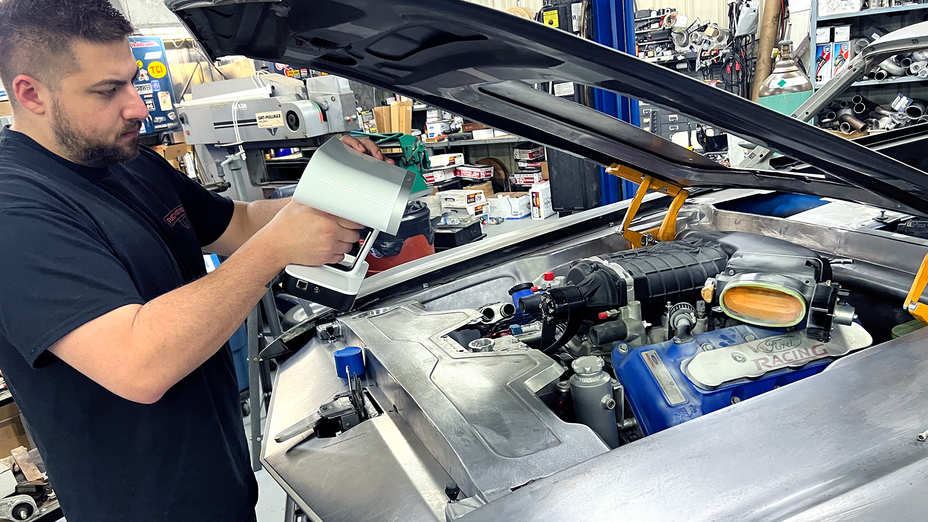
Tucci Hot Rods is now looking to deploy Artec Leo in non-automotive applications. Image courtesy of Tucci Hot Rods
“We developed these plates that go around each pipe and lock into each other, but we still had to scan twenty holes, which had different sizes, tubes, and locations running through them,” Tucci said. “We were able to bring in Artec Leo, and capture every hole, label it, and process it into a model.”
“Each hole had its own plate that we had to make specifically for it. Without having a 3D scanner, the project would’ve been almost impossible.”
Moving forward, Tucci says his company would like Artec Leo to be an integral part of its business, whether that be on the hotrod side of things or in other industries. If someone needs his company to come out and scan something, he concluded, it’s a service they’d like to be able to offer.
Scanners behind the story
Try out the world's leading handheld 3D scanners.