Creating a thought-controlled, 3D-printed bionic arm with Artec Eva
The Goal:To use a handheld 3D scanner to scan the patient's residual arm, then to use the lifelike 3D model of this together with the latest technology to create a thought-controlled bionic arm and hand.
Tools Used:Artec Eva, Geomagic Freeform
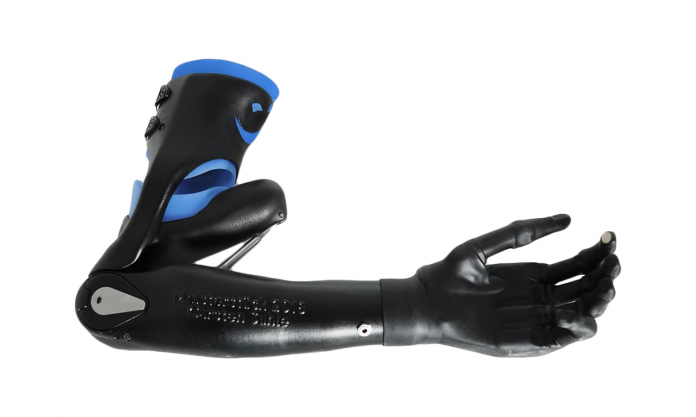
Paul Teupel was born without most of his left arm. He has had many prosthetic arms over the years, starting at the age of 3. Not long after that, he was given his second arm, which, in his words, “was a horrible contraption, like a double-hook held in place by a shoulder strap, so cumbersome to wear, and it looked awful,” he said. “That pushed me to not wear any prosthesis at all for a few years.” Even though he grew up around the turn of the millennium, the look and design of prostheses hadn’t changed much in the previous 50 years or more. Prosthetic arms and hands had become slightly more realistic looking, and a bit more comfortable, yet they were still far from being truly functional and life-enabling.
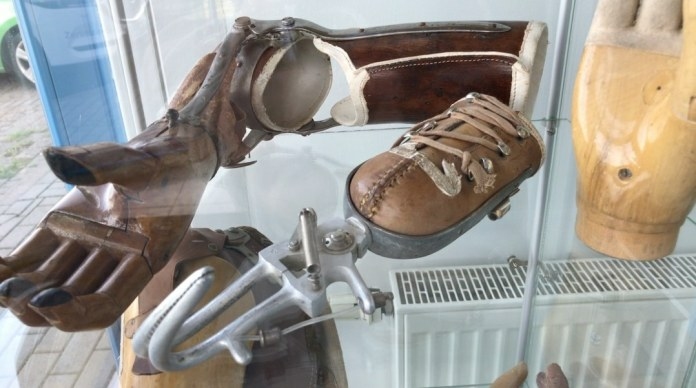
Early 20thcentury prostheses, in the historical collection of Sanitätshaus Klinz
Then at the age of 12, Paul received his first myoelectric prosthesis (with an Ottobock hand). It was a milestone for him, as it was the first time he could grip and hold things using his left arm. From this day on, he wore his prosthesis every day. Even so, this new arm allowed him to bend his elbow only 30 degrees, which was an improvement, but still left much to be desired.
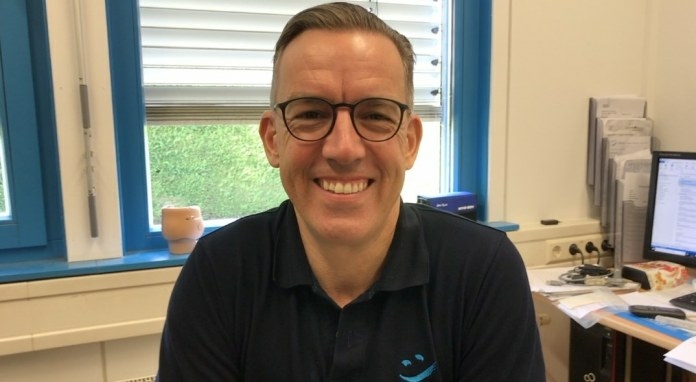
Carsten Suhle, Orthopedic Technician
Paul became a patient ofSanitätshaus Klinzof Bernburg, Germany, in the early 1990s, not long after the reunification of Germany, and has been working with the firm’s orthopedic technician Carsten Suhle since 1997. He has always given Paul the best of the latest technology in prosthetics. From the moment he first met Paul and took a close look at his arm, the wheels of Carsten’s mind surged to life and began to turn. And so, one day in the spring of 2017, with a plan to create an innovative new arm as part of his Master’s thesis, he told Paul not to get used to the prosthetic arm he had, “We’re going to make one for you that will be better than anything you’ve ever tried or even seen, what do you say?” Paul enthusiastically agreed, and over the course of the next 5 months, while working closely with Carsten, Paul’s bionic arm came to life.
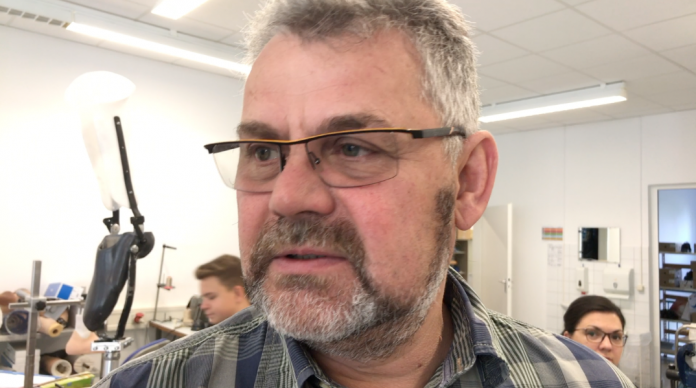
Gerd Klinz, Owner and Founder
Ever since Sanitätshaus Klinz opened its doors in 1990 Gerd Klinz, the owner and founder, has had a guiding light of being at the forefront of innovation and patient comfort, all so they can bring the maximum levels of mobility and independence to their patients. In the company’s everyday work, they’ve used lathes, glue, plaster molds, fiberglass, CNC milling, as well as modern materials and tools and technologies such as 3D scanning and 3D printing, Kevlar, various types of plastics, etc. They have multiple branches around Saxony-Anhalt, Germany, and patients coming to them from other parts of the country as well as flying in from abroad.
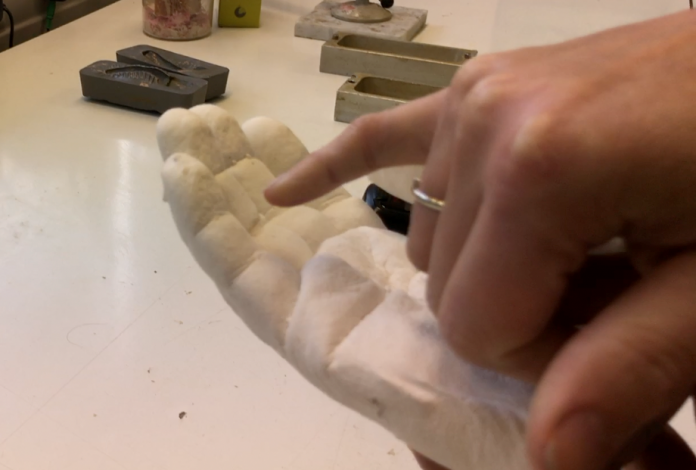
Inspecting a plaster cast prior to scanning
But let’s return back to the early days of Carsten’s work on Paul’s new arm. Bringing together a synergy of his years of expertise in orthopedics, his own kind of design thinking, and the latest in 3D scanning and printing, it was only a short while before he had built his first prototype for Paul. Paul came in for fitting after fitting, never once losing hope in Carsten’s expertise and remarkable imagination that were fueling them closer to success. As the weeks went on, the prototypes more closely matched the vision that Carsten had for what the final arm would eventually look like.
But somewhere along the way, Carsten realized that it wasn’t his vision that was holding them back from achieving the best results, but rather some of the tools they were using. Specifically, the 3D scanners that they were using to create 3D models of Paul’s upper left arm (residual limb), for designing a precise new arm that would perfectly match up with Paul’s anatomy. Unless the connection points and the room to allow for sufficient movement between the prosthesis and Paul’s body were exact, the new arm would not be merely uncomfortable, but also dysfunctional.
“With many hundreds if not thousands of movements performed each day, Paul’s body needs a prosthesis that naturally harmonizes with it, as an extension of the body, so that within a short period of time, he can just live his life and not think about his arm. That was my goal. And it’s my goal with every patient of mine. With Paul, I think we’ve achieved that, but that doesn’t mean we’re stopping there,” Carsten went on, “As the years go on, I’m going to do everything I can to give him the best prosthetic arm using the latest technologies, even if we have to make the breakthroughs ourselves!”
Carsten spoke about this, “Before I started 3D scanning, I never thought that there could be such great differences in 3D scanners…I thought that a scanner was a scanner, with some variations in accuracy and speed of capture, of course, but the reality is that comparing scanners can be like contrasting cheap sedans with Lamborghinis, and then there’s the range that exists between them, from high to low…first you need to decide what is most important to you, and in our case it’s the highest level of accuracy, the cleanest data, along with speed of capture, and then of course there needs to be easy post-processing so that the scans are merged together quickly into a 3D model ready for the next step.”
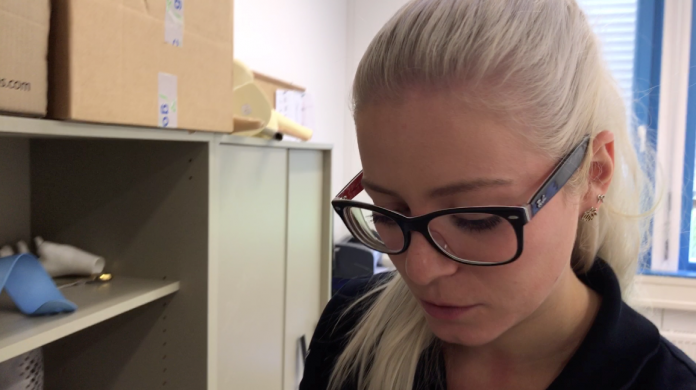
Maria Köhlitz, Sanitätshaus Klinz's orthopedic designer, explained: “We used and tested several 3D scanners in the past, including GO!Scan by Creaform and the Kinect 3D scanner, but every scanner we tried was either not able to provide the accuracy we need, or the frame rate for captures was simply not high enough,” she went on, “So when patients moved during the scan, as patients sometimes do, those scanners lost tracking and we needed to scan the area once again, or the resulting scans were so badly done that editing and aligning them during post-processing was too difficult.”
Carsten elaborated, “When I first began to look at 3D scanners, I imagined that we could just make up for any shortcomings in the scanner by becoming more skilled with the scan processing. But that didn’t work. When you start out with flawed data, you can spend hours and hours with it, and it will never be perfect,” he went on, “Think about if you drop a vase and then spend lots of time gluing it back together. Yes, eventually it may look new again, but close inspection will reveal the cracks. It’s much better not to drop the vase in the first place.”
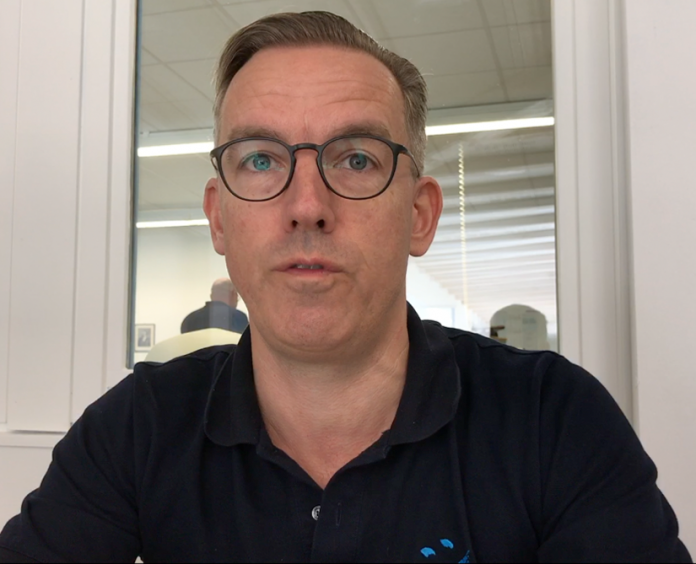
“Start with flawlessly clean data and lifelike scans. That’s what our Artec Eva gives us.”
–Carsten Suhle, Orthopedic Technician
Carsten understood that they needed the guidance of trusted experts in the field, so they turned to Artec Gold Certified ResellerKLIB, whose experienced technicians and consultants introduced them to Artec’s professional handheld 3D scanners Eva and Space Spider and provided them with training on both.
Artec Evais a professional color 3D scanner that uses safe structured white light. Lightweight and comfortable to use, Eva is ideal for digitally capturing medium-sized objects, such as arms, legs, and the human body. Boasting a point accuracy of up to .1 mm, Eva is one of most popular 3D scanners across a variety of industries, fromhealthcaretoindustrial designandscience.
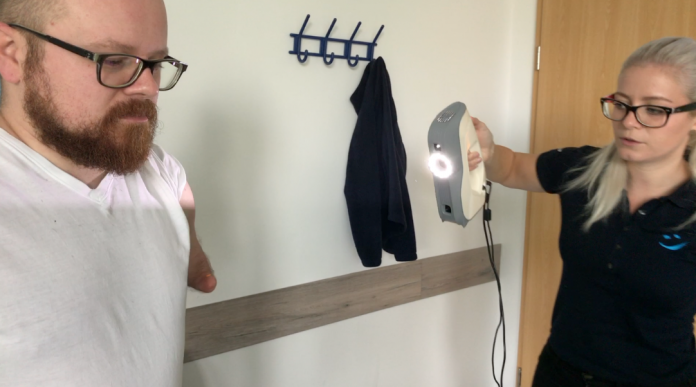
Paul Teupel and Orthopedic Designer Maria Köhlitz with Artec Eva
A handheld color 3D structured light scanner with an extraordinary point accuracy of up to .05mm,Artec Space Spiderexcels at scanning small objects quickly, and is easy to learn and use, with a long-standing track record of perfectly scanning fingers, hands, ears, faces, and more. During the digital capture process, scanning takes place directly within the industry-acclaimedArtec Studiosoftware in real time. Both Eva and Space Spider are fluidly integrated withkaiyun开云体育APP应用下载 modelling software.
As demonstrated in the video, compared to the traditional method of plaster casting, Artec Eva can be a huge time saver. In the example shown, the 2.5 hours required from start to finish with casting was contrasted with only 12 minutes from start to finish with Eva. And that’s in addition to the guarantees of the utmost in both precision and accuracy of Artec’s professional handheld 3D scanners, not to mention the utter convenience of having a perfect digital archive on hand for future use. Such technological advantages are impossible to ignore.
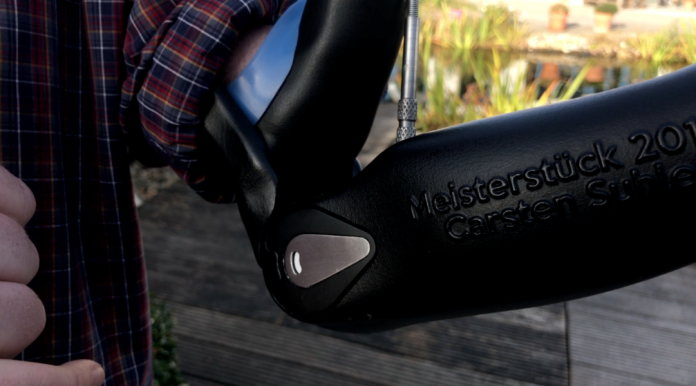
Close-up of the elbow joint of Paul’s new arm
Altogether, it took about 10 months from first prototype until the final arm was ready for fitting. The hand (bebionic) was purchased from Ottobock, while the prosthesis itself was entirely created by Carsten, designed inkaiyun开云体育APP应用下载 , and 3D printed out of PA2200 plastic. There is also blue silicone padding used as an interface between the prosthesis and Paul’s residual limb. Inside the body of the prosthesis are cables and wires leading to sensors from Paul’s skin that use muscle electricity (myoelectricity) to move the new arm and hand. So simply by thinking about a specific movement, the muscles that would normally move the arm in that way are activated, the sensors pick up the electricity via the skin sensors, and the prosthesis moves and functions as Paul has intended.
To say that Paul is happy with the results would be an understatement: “Carsten did a tremendous job of developing and engineering my new arm. He reinvented a double-jointed system with two pivot axes, which allowed a range of movement of more than 90 degrees. I will never forget the moment when, for the first time in my life, I lifted a glass of water to my lips with my left hand and took a sip!”
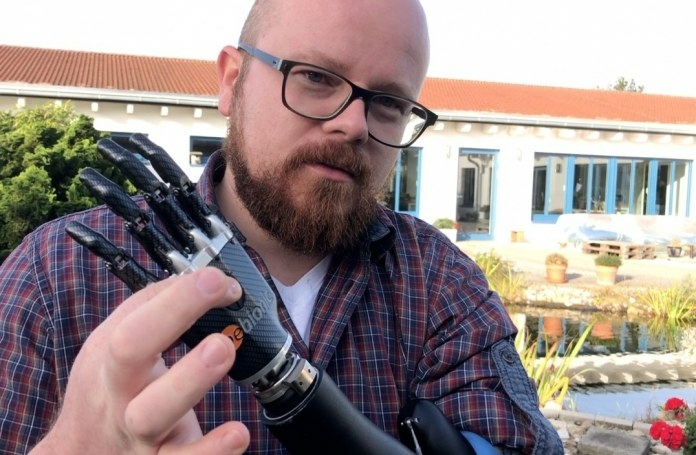
Paul Teupel with his new arm
Paul is one of more than 100 patients they’ve scanned and created cutting-edge orthopedic and prosthetic solutions for. As Maria Köhlitz said, “In the beginning, we purchased Artec Eva, because we wanted to scan the arms and legs of patients. And for this, Eva is the perfect choice. But we then wanted to expand our range of design and creation down to the fingers and small joints, so we purchased a Space Spider. Now the scans and level of detail are so impressive, we can even perfectly see the fingerprints in the scans we’re making.”
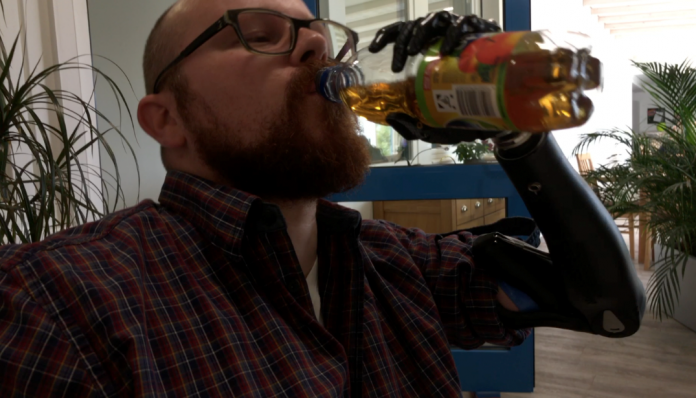
Paul enjoying the freedom of his new bionic arm
Refusing to feel limited or disabled ever again, today Paul has the freedom to indulge in his favorite hobbies: riding and restoring mopeds and motorcycles. His new bionic arm and hand keep up with him every step of the way, allowing him to grip wrenches and screwdrivers, parts great and small, with ten fingers dexterous enough to handle washers and spark plugs, and everything he'd been dreaming of since he was a boy.
The German government health insurance system has decided to nationally endorse 3D scanning and printing of prostheses as superior than the traditional methods of designing and creating orthoses and prostheses. They made this decision not merely because 3D scanning is more cost effective in the short run, but also due to long-term durability, as well as the elevated levels of patient comfort and mobility, both during examination and fitting, together with long-term patient use and reduced frequency of office visits needed. Germany’s health insurance understands that 3D scanning is the future of prosthetics and orthotics.
Scanners behind the story
Try out the world's leading handheld 3D scanners.