How Sherrill Furniture supercharges their CGI workflow with Artec Leo
Challenge:With thousands of unique furniture pieces from across the company’s nine brands lined up for digital transformation, the design team needed just the right scanner to complete their scan-to-CGI imaging pipeline – one that’s 100% portable, accurate to below a millimeter, and can capture furniture-sized objects in minutes with no rescans needed.
Solution:Artec Leo, Artec Studio, SOLIDWORKS, ZBrush, 3D Studio Max
Results:With their Artec Leo, the design team can easily deliver dozens of high-resolution, gap-free 3D scans in a single afternoon, ready for passing over to their CGI team for the final steps. They’re now also able to scan their furniture and reverse engineer it in CAD software, to create ready-to-manufacture versions of the same piece in a variety of looks and styles.
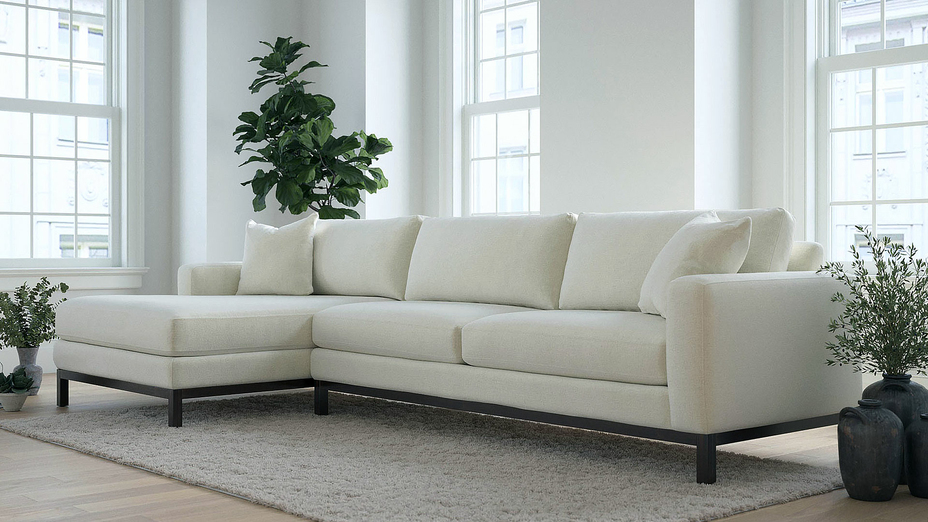
3D-scanned Sherrill Furniture custom sofa set in a CGI-rendered apartment scene. (Photo: Sherrill Furniture)
In the world of custom luxury furniture, clients expect to see what they’re about to order, especially when a virtually unlimited number of combinations of fabrics, leathers, finishes, colors, hardware, and accessories can dramatically change the look and feel of any upholstery or casegoods furniture piece. If not in person, then at least in a printed catalog or online.
But with the traditional method of using photography to create images for product listings, this is no easy feat.
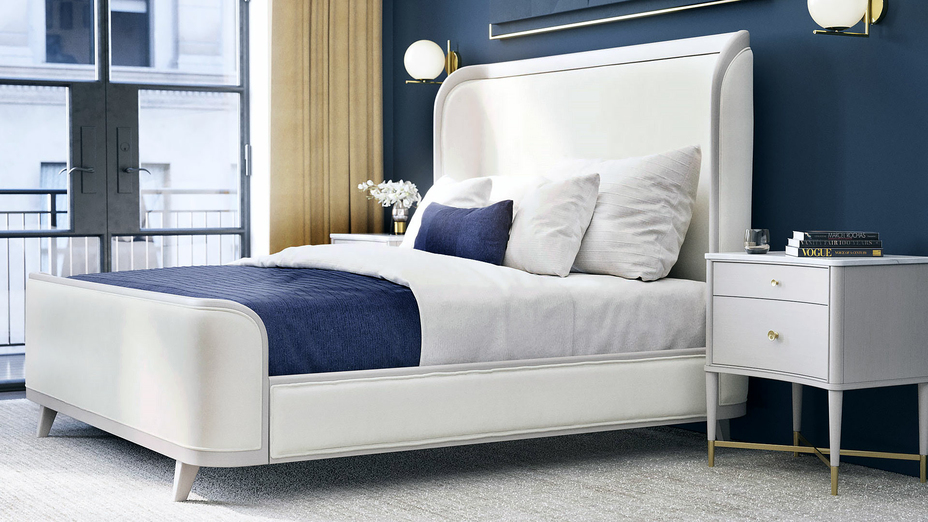
Pairing 3D-scanned custom furniture in a CGI-rendered room scene. (Photo: Sherrill Furniture)
Each individually customized piece must first be manufactured and then captured from multiple angles in a dedicated photo shoot, otherwise the client is simply told to “imagine” what their new furniture will look like when it gets delivered. And from a customer’s point of view, it’s a risky thing to be such a pioneer.
Only the best
ForSherrill Furnitureof Hickory, North Carolina, this wasn’t good enough. Ever since opening their doors in 1945, their goal has been maximum customer satisfaction, not just in terms of the highest-quality materials and craftsmanship, but also meeting and exceeding their clients’ expectations every step of the way.
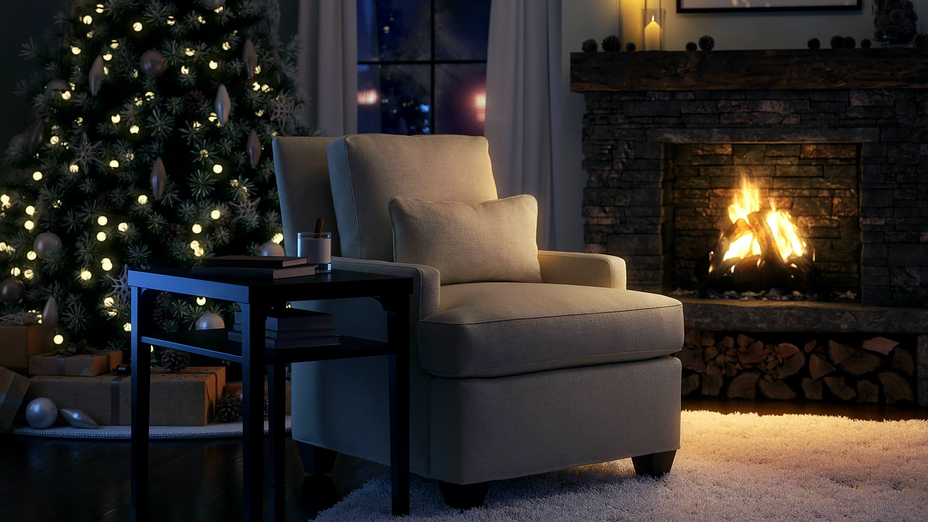
3D-scanned Sherrill Furniture custom chair in a CGI-rendered living room scene. (Photo: Sherrill Furniture)
As such, they searched for a way to show their clients worldwide exactly what the furniture of their dreams was going to look like, even before it’s ever made. And with thousands of unique pieces available, plus dozens of custom furniture programs from across the company’s nine brands, whatever solution they adopted would also need to be fast and flexible.
Sherrill Furniture VP of Marketing Dax Allen and his team’s research led them to3D scanningas part of a dedicated scan-to-CGI imaging pipeline, one that would allow them to create dozens of fully customizable3D modelsfor product listings week after week, year in, year out.
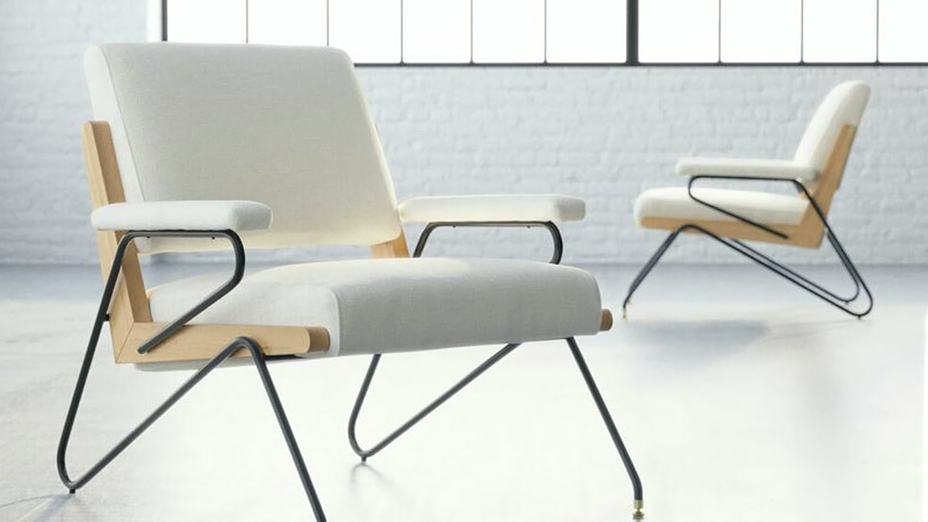
3D-scanned Sherrill Furniture custom chairs in a CGI-rendered room scene. (Photo: Sherrill Furniture)
At the same time, this would also streamline their content creation workflow, removing any existing bottlenecks while preventing new ones from ever arising.
With these requirements in mind, they contacted the 3D scanning experts at Artec AmbassadorDigitize Designsand spoke with Sales Engineer Bo Helmrich, who immediately recommended the Artec Leo to them.
A fully portable,handheld 3D scanner with a built-in touchscreen and computer, which delivers submillimeter-precise color 3D scans, the Artec Leo excels at capturing medium-sized objects, particularly in places where maneuverability is a must, such as the crowded showrooms where Sherrill Furniture’s design team needs to scan.
“Once I realized how quickly Leo captures data, I started moving faster, and Leo has no problem keeping up with me.”
Handheld, hi-tech solutions
After purchasing their Leo, Allen and his team worked closely with Helmrich in coming up with an efficient workflow for capturing furniture pieces and processing the scans inArtec Studio software.
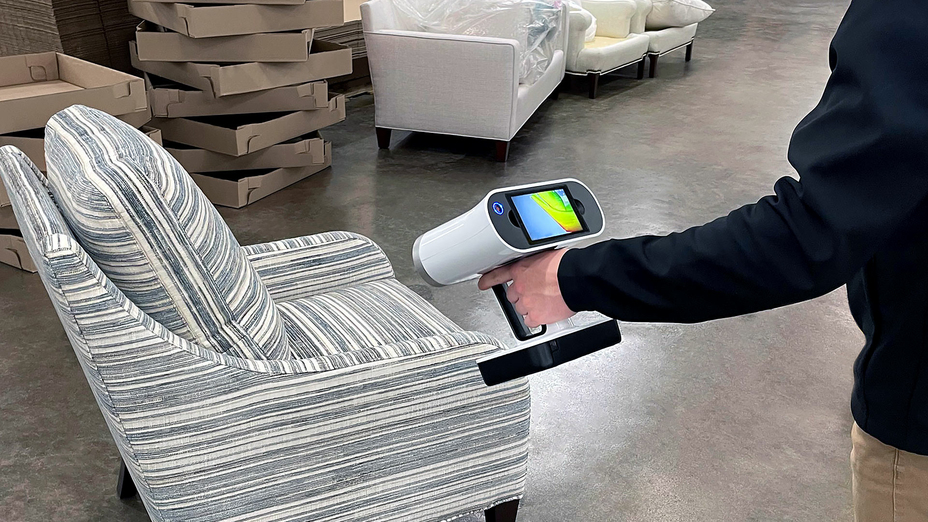
Sherrill Furniture’s Noah Carney scanning a chair with Artec Leo. (Photo: Sherrill Furniture)
In the words of Design Engineer Tanner Pittmon, “Bo helped me work out the best way to scan whatever kinds of pieces I need to capture, from small chairs all the way up to full-sized sectionals, which means working from left to right, while capturing some of the upper and lower parts of the piece along the way.”
He continued, “With Leo, we don’t need to use any targets or markers at all, and the only problem I had initially was that I was scanning too slowly and too much data was building up. Once I realized how quickly Leo captures data, I started moving faster, and Leo has no problem keeping up with me.”
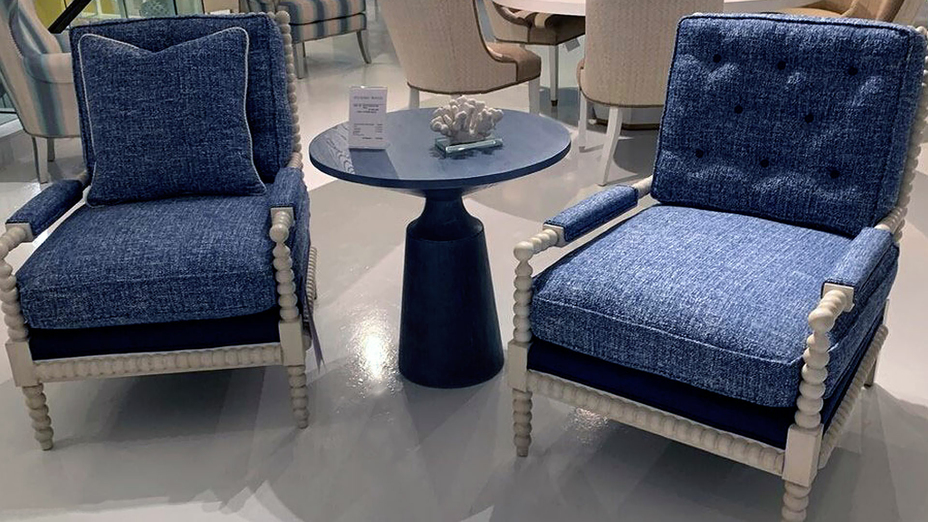
Original Sherrill Furniture wood-frame chairs awaiting 3D scanning with Artec Leo. (Photo: Sherrill Furniture)
If there’s ever some aspect or detail that wasn’t captured in its entirety, “I can confirm this right away on Leo’s touchscreen while I’m scanning,” Pittmon said, adding, “And then with one wave of the scanner, that’s it, I have everything.”
“Having Leo means never having to return to the showroom for a repeat scan.”
Leo’s ability to make gap-free scans of even complex, naturally shaped furniture is crucial to the workflow. If there were any gaps in the scans when the CGI team receives them, they wouldn’t be able to realistically wrap the virtual upholstery to the model, and the quality would suffer.
That’s one reason why each individual component is scanned separately, and then brought together in Artec Studio later on before sending them to the CGI team. This means every cushion and pillow and other element is scanned by itself, thus ensuring full 360-degree coverage from top to bottom.
Marketing Coordinator Noah Carney said, “With Leo, we don’t have to wait until we’re starting to process the scans to understand whether we missed some detail that’s important for the CGI team to do their work.”

Artec Studio screenshot of the wood-frame chair scan. (Photo: Sherrill Furniture)
Carney explained, “When we visit our showroom, we’ll be capturing 20 pieces or more in one afternoon, and then we’ll head back to the office for processing the scans. Having Leo means never having to return to the showroom for a repeat scan.”
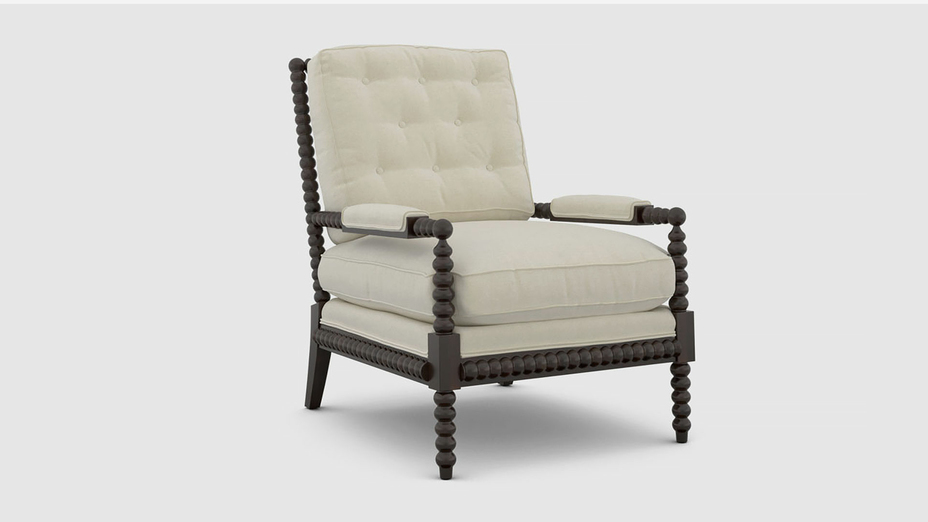
CGI render of the wood-frame chair with customized visualization. (Photo: Sherrill Furniture)
A customized craft
Once the scans are uploaded in Artec Studio software, they’re processed and turned into 3D models, which takes just a few minutes of aligning the various scans for each piece, and cleaning up any non-essential data present.
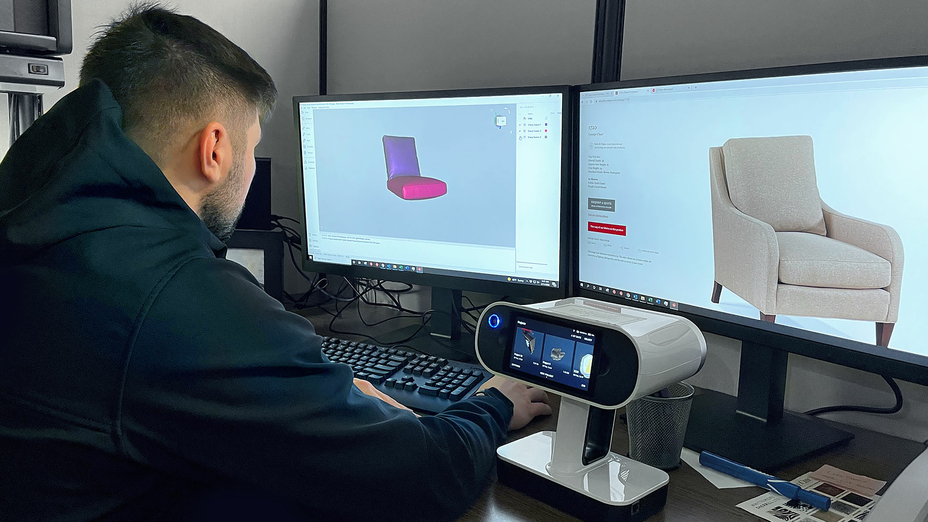
Processing Leo scans of a chair in Artec Studio software. (Photo: Sherrill Furniture)
Following this, the 3D models are sent over to the CGI team, who import them into ZBrush. There, they focus on refining the geometry in preparation for the next step, which takes place in 3D Studio Max. That’s the stage where they add in seams and UV and other model changes not done in ZBrush.
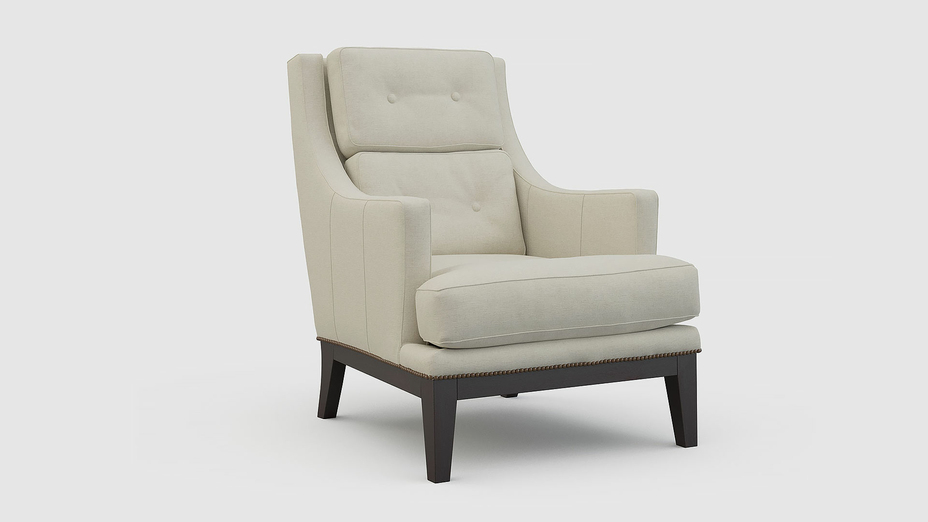
CGI render of Sherrill Furniture’s Dundee Natural chair, from Artec Leo scans. (Photo: Sherrill Furniture)
The final results of their work are vividly lifelike 3D models of each piece, which can be zoomed in on, inspected up close, and modified at the click of the mouse to change the upholstery from Acapella Red to Zussman Seafoam green, or anything in between.
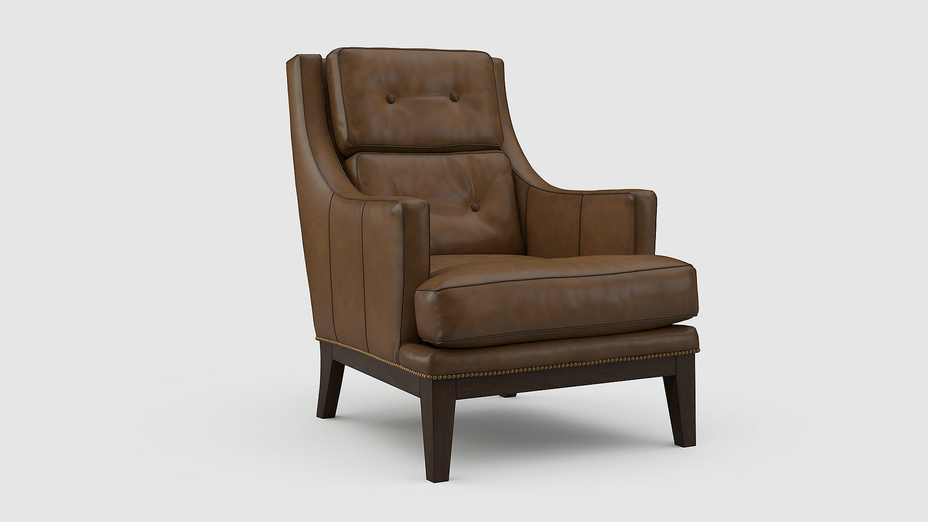
CGI render of Sherrill Furniture’s Sauvage Saddle chair, from Artec Leo scans. (Photo: Sherrill Furniture)
And various finishes, color schemes, and accessories can be instantly selected and visualized, showing the client exactly what the company’s master craftsmen will be bringing to life and shipping out in the days ahead.
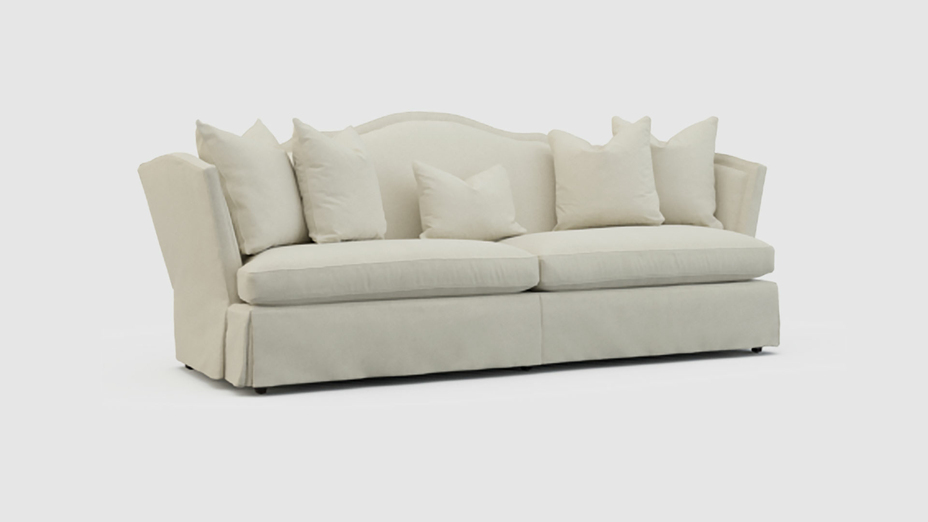
CGI render of Sherrill Furniture custom sofa, from Artec Leo scans. (Photo: Sherrill Furniture)
Pittmon said, “One little trick that we do with Leo for keeping the realism high is when we’re scanning a sofa, for example, we’ll scan both the right and left sides. Many companies out there will take a shortcut and just mirror one side to the other, but we never do that.”
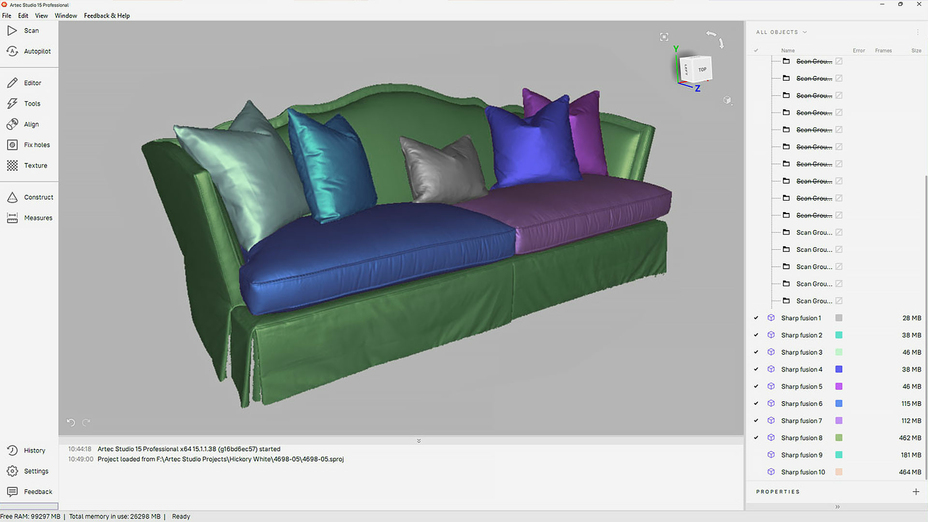
Artec Studio screenshot showing Leo scans of Sherrill Furniture custom sofa set. (Photo: Sherrill Furniture)
He continued, “Because in bench made furniture there are tiny, unique differences between the two sides that will register when you look closely: wrinkles, folds, even the way the light plays upon the surface of the fabric, and without this realism, the model will just look fake.”
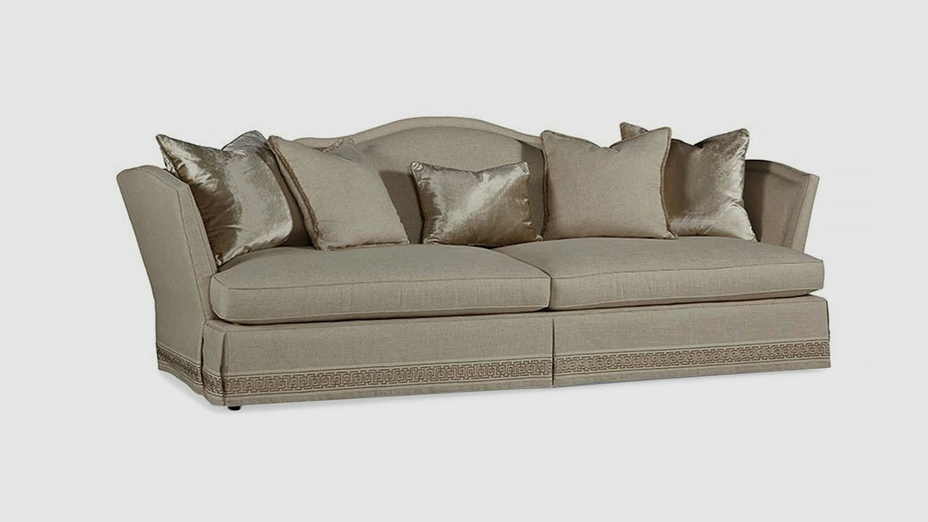
CGI render of the same custom sofa set, visualized with different upholstery and style. (Photo: Sherrill Furniture)
Pittmon has also used Leo in a scan-to-CAD capacity with SOLIDWORKS, toreverse engineerfurniture. One such project involved a classic chair that had no design drawings to accompany it. Less than a day later, and the Sherrill Furniture manufacturing team can now reproduce it anytime in a range of variations, on demand.
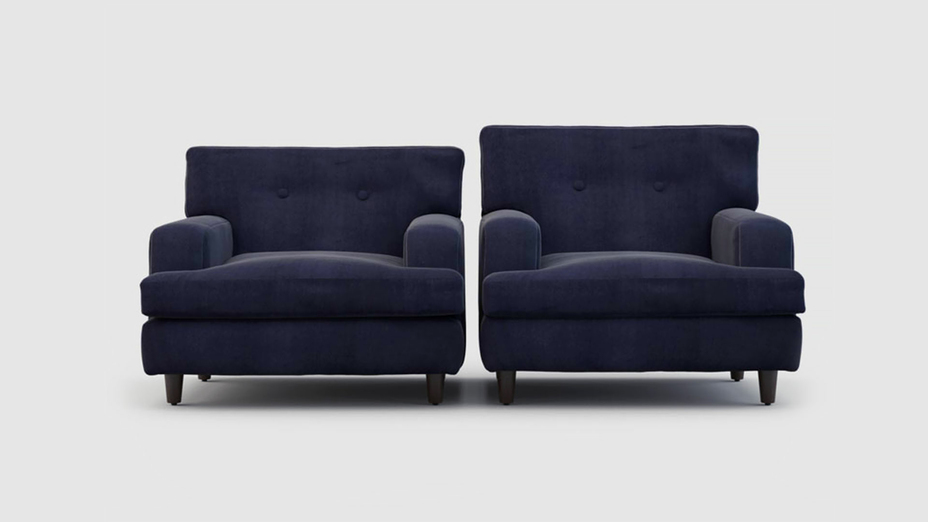
Reverse engineering with Artec Leo: CGI renders of the original classic chair (L) and the final customized version (R). (Photo: Sherrill Furniture)
Explaining this project, Pittmon said, “If you take a look at these two chairs, the one on the right doesn’t even exist. From the Leo scans, the CGI team created a 3D model, extending the back higher. They can also stretch out the width of the chair into a love seat or even a complete sofa.”
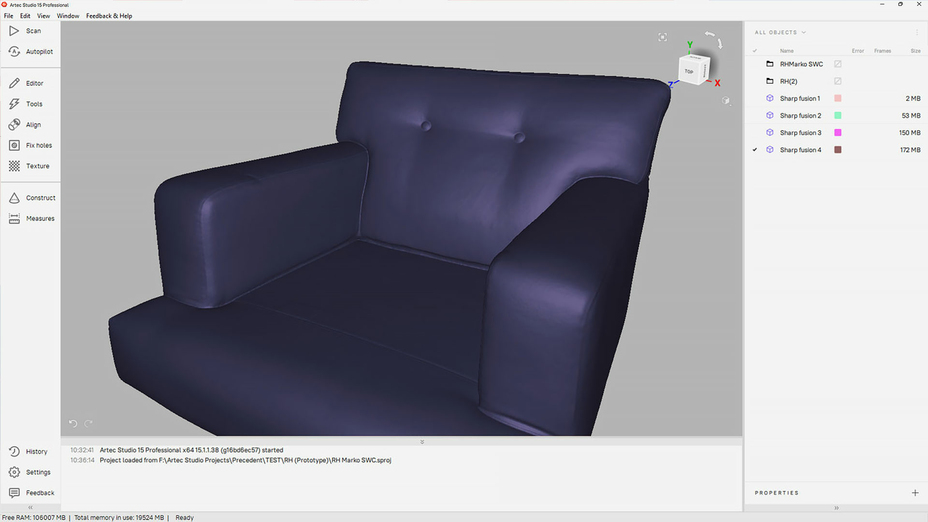
Artec Leo scan of the original classic chair, in Artec Studio software. (Photo: Sherrill Furniture)
He continued, “These customized versions of the chair don’t need to be physically created right now. We’re building them virtually. And then, later on, manufacturing can respond to that need.”
Whenever design drawings don’t exist for a piece, Pittmon can quickly construct a CAD model of the virtual chair or sofa using SOLIDWORKS and send it on directly to the product development team at the furniture factory.
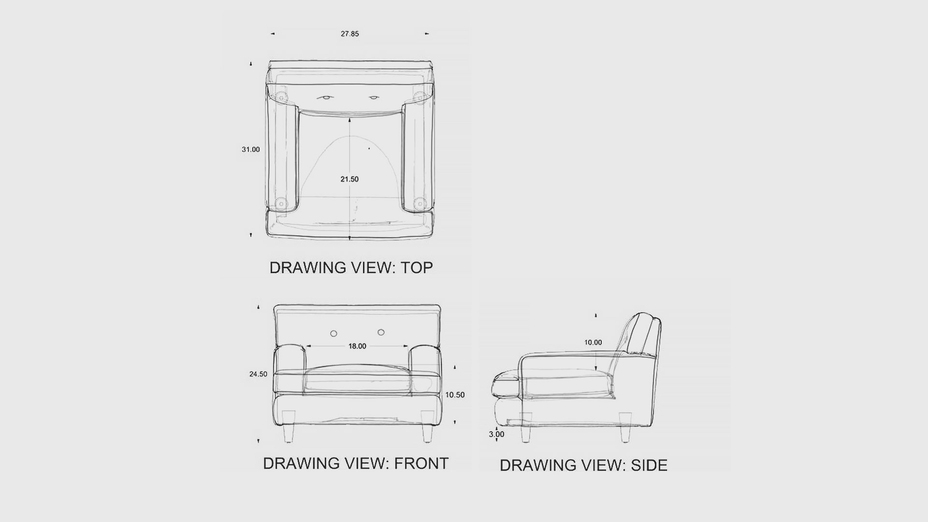
Design drawings for the customized version of the chair, created by the Sherrill Furniture CGI team. (Photo: Sherrill Furniture)
Finding new solutions
Allen spoke about the contrast between old and new: “Early on, we conducted a side-by-side comparison of traditional photography vs our new 3D CGI pipeline with Leo,” he said. While the 3D approach does initially cost more and take longer to complete overall, it does allow them to leverage the 3D model with multiple fabrics, finishes, and more.
“[Using 3D scanning] is at least 30X more efficient on a cost-per-visual-asset basis than traditional photography. And, we’ve actually improved the visual quality vs photography,” he continued. “It’s an amazing result.”
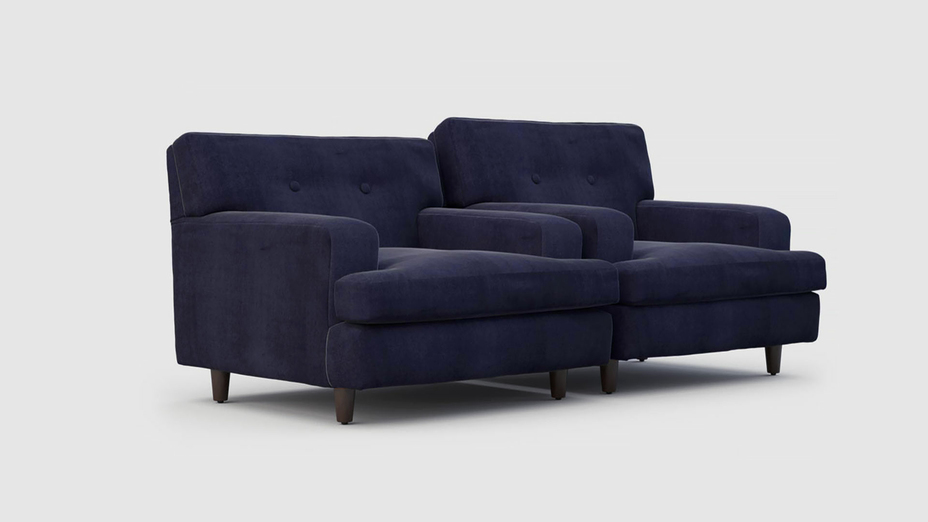
CGI-rendered 3D models of the original classic chair (L) and the customized version with extended back (R), from Artec Leo scans. (Photo: Sherrill Furniture)
He added, “An example of this came up during the testing, when our team realized that a sofa hadn’t been photographed. The photography team had to cancel the shoot and make plans to re-shoot in 4 weeks when the sofa would be ready.”
“In contrast, the CGI team took the 3D model of the chair that was made from Leo scans, matched the sofa frame to it, and used that to digitally create 100% accurate visuals for the sofa in a 2-hour window from start to finish.”
Allen and his team continue to refine their workflow as they look for any edge that will further accelerate the pipeline while never sacrificing even a millimeter on quality.
Scanners behind the story
Try out the world's leading handheld 3D scanners.