Artec Leo & Ray-captured digital twin transforms pea processing efficiency
Challenge: Surveying a leaky outdated pea production line, so a revised system, capable of utilizing a higher percentage of fresh produce, could effectively be erected in its place.
Solution: Artec Leo, Artec Ray, Artec Studio, SOLIDWORKS (with Mesh2Surface plug-in)
Result: With Artec 3D scanning, the firm was able to accurately digitize a factory floor in less than a day, and revamp the sorting setup around the machinery models within.
Why Artec 3D?: Leo’s speed and versatility, Ray’s range, and Artec Studio advanced editing allowed Dodman to capture an entire facility, before using the highest resolution data from each scan, to create a digital twin with unmatched detail.
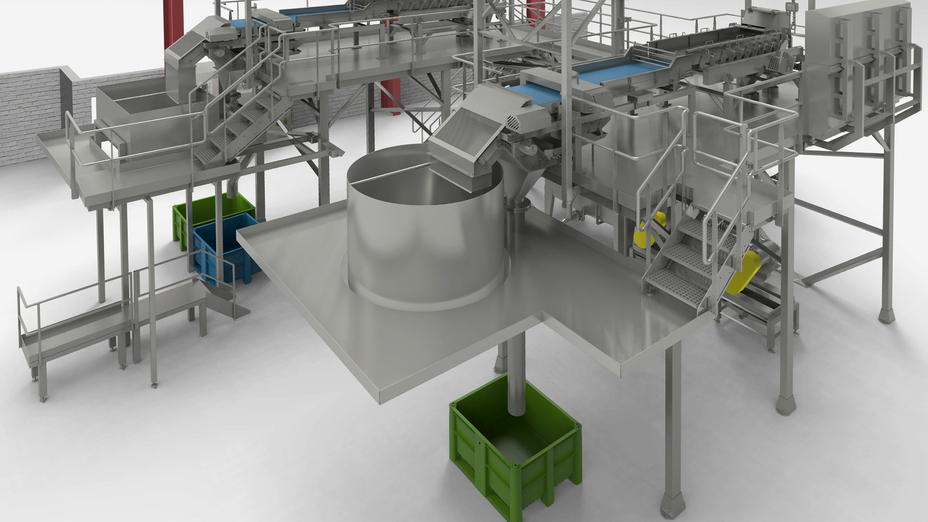
A 3D model of Dodman’s pea production line captured with Artec Leo and Ray
It may not be the first thought that comes to mind when tucking into your Sunday roast, but before most organic foods ever get near your plate, they require significant processing.
Of course, the intensity of this checking and sorting depends on how foods are sourced. When it comes to tiny vegetables or legumes like peas, the process of getting them into stores is actually quite involved. After being shaken free from pods by viner or thresher machines, peas are sorted and cleaned, then rapidly heated and cooled for sterilization.
Once sterilized, they’re checked intensively using a color sorter, metal detectors, and X-ray machines to ensure they reach customers in the best condition possible.
But even then, farming a marketable pea is not a foregone conclusion. Changeable weather and plant disease can be disastrous for quality and yield. If not promptly frozen or vacuum-packed, peas can also lose freshness, resulting in substandard tins making it to market.
So, if you’re not getting enough quality peas to market, what should you do? Approached by a client with this very question, food processing firm Dodman Ltd. helped overhaul its workflow, building a more efficient one – using an Artec 3D scanning-captured factory digital twin.
Chasing pea-processing perfection
Working from its East England HQ, Dodman prides itself on designing, making, and installing high-quality processing systems for the country’s leading food brands. With the firm already having integrated 3D scanning into its workflow, and redesigned everything from conveyors to production lines, it was well-qualified to deal with its customer’s pea-sorting problem.
That said, the UK is both Europe’s biggest pea producer and consumer – the average Brit eats 9,000 per year – so canned food supplier Dodman’s client already had its work cut out keeping up with demand. Leaky machinery was not making things any easier, so the firm decided to reach out to Dodman, asking it to install a new system that stemmed its loss of valuable stock.
Usually, Dodman scans and reverse engineers intricate machinery with a wireless, handheld Artec Leo acquired from Artec Gold-certified partner Patrick Thorn & Co. Having been wowed by an initial online demo, its team were later amazed at how easy it was to capture shiny steel conveyors on-site and compare them to CAD models – it was exactly what they needed.
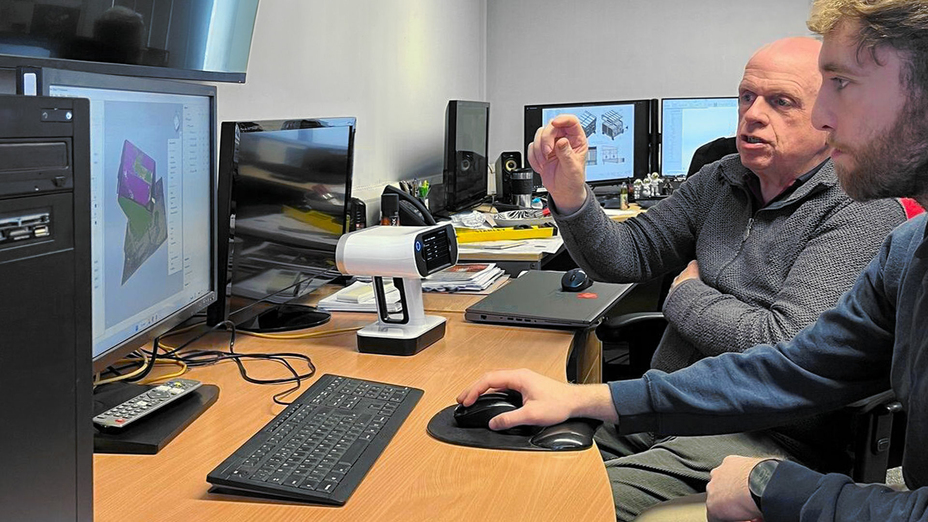
Artec Gold-certified partner Patrick Thorn helping the Dodman team optimize their 3D scanning results
However, due to scale, Dodman initially tried to digitize its client’s facility with a LiDAR Artec Ray. While the long-range 3D scanner was able to capture the entire factory floor, raised platforms and other background noise obscured finer details from the device’s view.
To get around this, Dodman began using Leo alongside Ray to digitize critical equipment with precision at pace. According to design engineer Andy Chase, this workflow proved to be the perfect recipe for gathering the accurate, multi-resolution data needed to progress.
“We got a very high degree of accuracy – down to just 2 mm – and considering how wonky the existing equipment was, this is incredible,” said Chase. “We surveyed the whole area, but we were also responsible for the transfer of product. Our new line needed to be spill-proof, otherwise our client would lose money. This could only be achieved with Artec Leo, which gave us a fully detailed view of the area.”
Surveying with digital twins
At the center of this revamped production line was the client’s pea color sorter. Having come up with a new platform design and pumping system for elevating peas in the tank, Dodman had to ensure this would fit around existing machinery, otherwise it’d be impossible to integrate.
This is where Artec 3D scanning came in: enabling the creation of accurate digital twins, which could be used to survey and plan on a virtual factory floor. With traditional lasers and tapes, this process would’ve taken weeks, and only yielded simple block measurements. By comparison, top-to-bottom capture with Leo and Ray took just five hours.
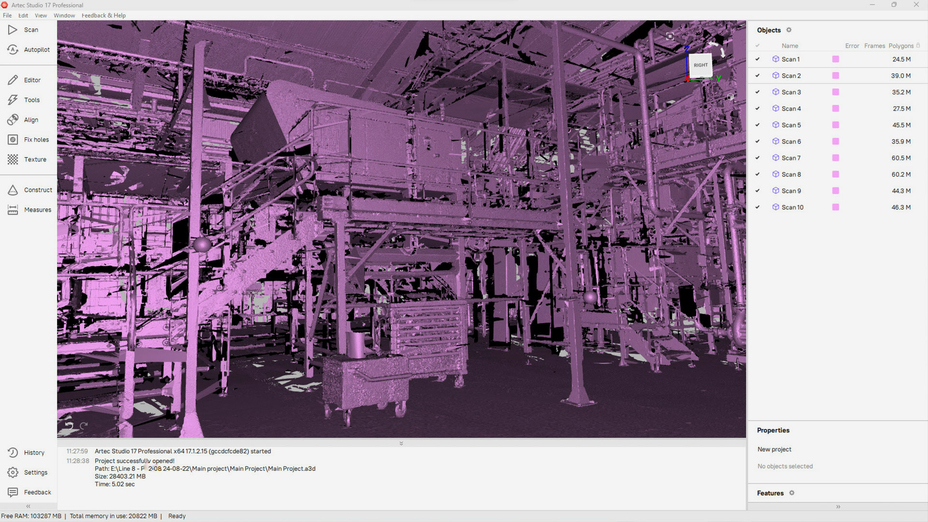
Dodman’s Artec Leo and Ray 3D scan data on Artec Studio
When it came to editing data on the Artec Studio 3D scan capture and processing software, Patrick Thorn also helped greatly, enabling the Dodman team to optimize results. With Thorn, they found the program’s outlier removal and eraser tools could be used to delete misaligned frames, and that mesh simplification allowed file sizes to be reduced for export.
“When we were getting used to the software, Patrick was really helpful, showing us some of the tips and tricks to process data efficiently,” added fellow design engineer Jack Tucker. “I realized that I had loads of background noise and it can be quite difficult to collate information, but Artec Studio’s cropping tools made it so easy to remove unneeded data after alignment.”
Once edited, the factory mesh was sent to CAD design platform SOLIDWORKS, where it was reverse engineered with the Mesh2Surface add-on, so machinery could be separated, moved, and built around virtually. The result? A complex digital twin of the firm’s new production line, which was later used to ensure proper fit and model how it would perform.
“By capturing wider areas with the long-range Ray and filling in finer details with the more portable and accurate Leo, it’s now possible to achieve incredibly realistic 3D models at scale,” added Thorn. “Helping the Dodman team innovate in the factory processing space has been a pleasure and I can’t wait to see where they take 3D scanning and digital twins next!”
Leo & Ray: two peas in a pod
Having deployed Leo and Ray together so successfully, Tucker now sees them finding further multi-resolution, production line-digitizing applications. With the client’s pea project being the first time Dodman had used a Ray, he also expects scan results to get even better.
However, the company’s 3D scanning activities don’t just revolve around surveying. To date, it has used the technology to reverse engineer and upgrade several pieces of equipment, for one customer, digitizing a container and making it a more efficient chemical-mixing vessel.
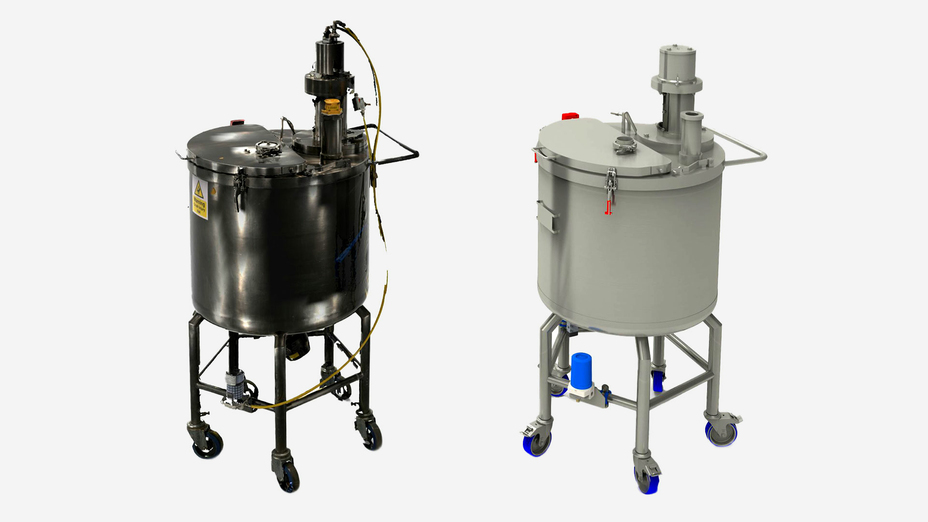
Another 3D model created by Dodman with Artec Leo: a chemical mixing vessel
In-house, Tucker adds that Leo also improves Dodman’s measurement efficiency “on a weekly basis,” especially in cramped, cluttered spaces, or when switching between conveyors, which “takes a lot of time and can cause details to be missed.”
“As projects unfold, you realize you’ve actually scanned an area or detail that you might not have thought was relevant at the time, but now it is,” concluded Tucker. “You only really hand measure what you think you’re going to change – with 3D scanning, projects and designs can change course, but it’s fine, you’ve already captured all the details you need.”
Scanners behind the story
Try out the world's leading handheld 3D scanners.