Artec Eva Lite comes to the rescue in creating made-to-measure medical corsets
Challenge:NEUT, a French orthopedic company, needed a solution to help create state-of-the-art medical corsets while providing a more comfortable, cleaner, and faster patient experience.
Solutions:Artec Eva Lite, Artec Studio
Result:Orthoprosthetists are now able to digitize their patients’ body parts, eliminating any stress and discomfort. In addition to being completely safe, the enhanced precision of 3D scans results in a true-shaped, perfectly fitting medical corset.
Why Artec:Artec Solutions are a perfect choice for bespoke orthotics and prosthetics due to their speed, precision, point-and-shoot ease, and a safe, contact-free workflow.
Even though a medical corset has little to do with arguably the most controversial garment in history, it is still associated with something which brings a lot of discomfort. Despite the fact that corsets are widely prescribed to alleviate back pain after surgeries, relieve muscle tension, and stabilize spinal deformities, this medical device has an intimidating reputation. The challenge for orthopedic specialists, as a result, remains: to take patient care to a new level by designing a perfectly adjustable medical corset that offers support in every way.
Finding better solutions
With technology advancing, the orthopedic sector has quickly learned to combine expertise, experience, and innovation.NEUT, a French company behind the creation of a wide range of custom-made orthopedics, is a brilliant example of this. Based in Paris and Versailles, NEUT operates in Ile-de-France and Champagne, and is constantly looking for new ways to meet the needs of both patients and healthcare professionals.
To ensure perfect fit and support, the corset needs to replicate each wearer’s individual anatomy. The path to the final product, however, has traditionally lain through routines that could be described as nothing but clunky and trying for the patient. The conventional way of designing a corset involves sculpting a plaster mold directly on the patient’s body, whereby a layer of plaster of Paris is laid over the respective area, evened and shaped by hand, and then left for up to an hour to set and harden, with tape measurements taken along the way. The patient needs to remain still throughout the process, which may cause muscle stiffness and pain. But even that is not the end of it. Once hardened, the plaster cast needs to be cut open with an electric saw. For anyone, especially younger patients, being exposed to the screeching sound of a saw cutting close to their skin is a terrifying, albeit safe, experience.
In a process that would take at least three days, corset-making was slow, messy, stressful, and required much physical effort, as the molds were heavy. NEUT’s orthoprosthetists quickly realized that there could no longer be a question of tape measuring, manual sculpting, and molding – so they started looking for a new solution that would allow careful measurement and precise modeling of a corset’s shape.
In order to manufacture bespoke corsets, NEUT specialists realized they needed something that worked where traditional methods fell short. There was only one possible solution: digitization. And so, they turned to their long-term partner,CADvision.
Data capture for excellent results
A leading French company, provider of scan-to-CAD products and services, and trusted Artec gold-certified partners CADvision assisted in exploring the options available. Having analyzed their needs and requirements, NEUT opted for Artec Eva Lite – and high-performance 3D scanning entered the game.
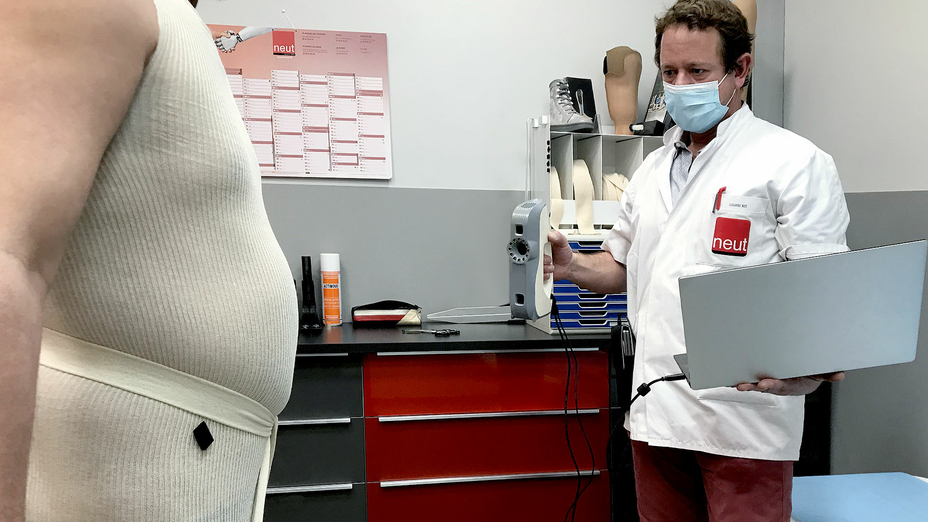
Scanning a patient with Artec Eva Lite (photo courtesy of NEUT)
A tried and tested solution, favored by clinics across the world,Artec Eva Liteoffers excellent geometry-only tracking and capture. This affordable 3D scanner is based on white structured-light technology, and has proved its efficiency with numerous healthcare institutions, including ones on a tight budget. Requiring minimal training, Eva Lite offers quick, professional scans of a human body, which makes it a universal medical favorite. An important prerequisite for NEUT was that the scanning process not interfere with any routines at a hospital ward or instrumentation room: the team was often required to scan right after surgeries.
Even if the patient moves slightly during the scanning, Artec Eva Lite automatically corrects inaccuracies.
Offering precision essential to confidently model every detail of the corset using measurements acquired via 3D scanning and recreating the corset model down to every detail, Eva Lite allows orthoprosthetists to address the needs of both physical and mental health of a patient. Increasingly, 3D scanners are used by health professionals because these quick, harmless, and non-invasive devices provide accurate results while guaranteeing the patients are safe, calm, and spared any additional stress. “The scanner’s high precision – down to the millimeter – is a major advantage compared to other technologies such as mobile applications on tablets, which are less precise and require a lot of manual corrections,” said Alexandre Neut, orthoprosthetist and CEO of NEUT. “Even if the patient moves slightly during the scanning, Artec Eva Lite automatically corrects inaccuracies.”
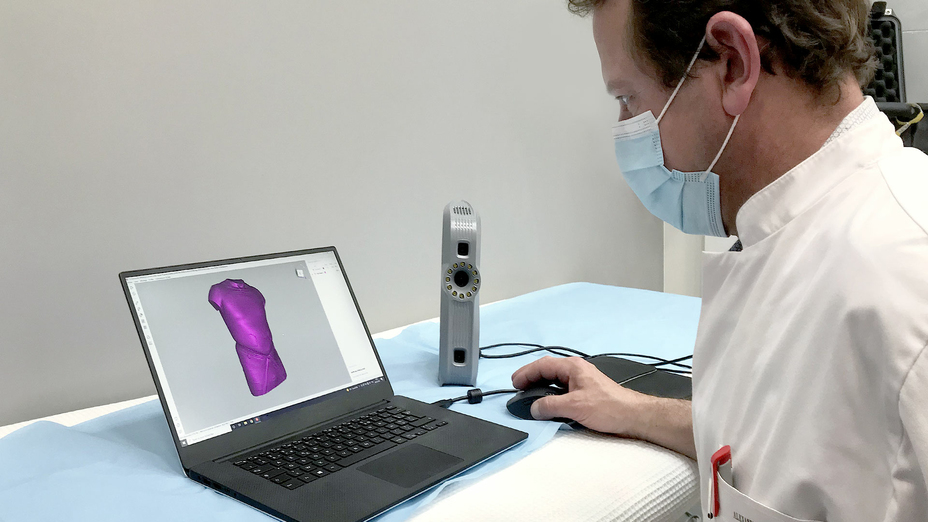
Alexandre Neut viewing the 3D model in Artec Studio (photo courtesy of NEUT)
Yet another pleasant discovery for the team was the ability to bring their Eva Lite to literally any and every place it was needed: the scanner’s portability made it an excellent asset to use in a hospital or a clinic, in a rehabilitation center or during a humanitarian visit. Eva Lite boosted the evolution of NEUT’s workflow, confirming the company’s status of a forward-thinking orthopedic practice.
It only gets better
After scanning, the acquired data is moved on to the next stage: optimizing body scans in Artec Studio – a smart and intuitive3D software for editing and processing scans. Once processed, the scans are then seamlessly exported into a specialized orthopedic software.
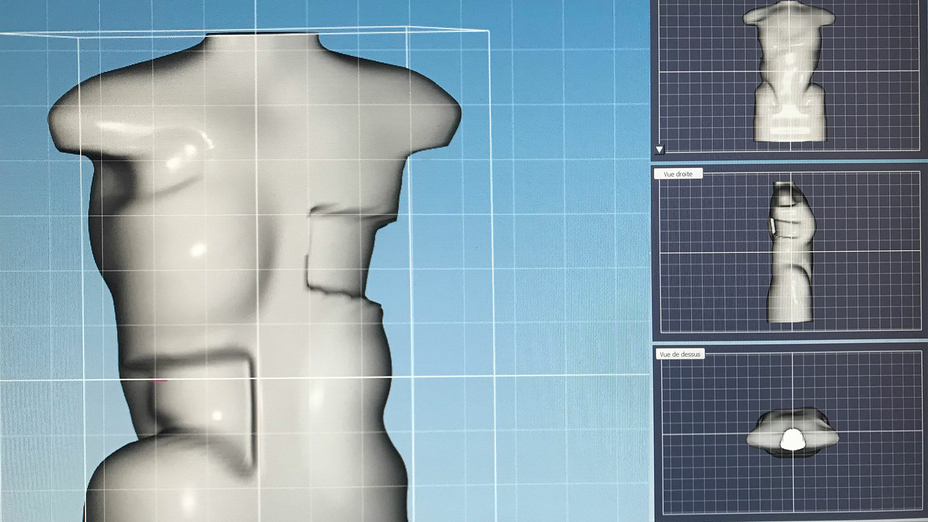
Regardless of the size of the object, 3D scans are easily processed, altered, or integrated into any specialized software
One vital aspect of processing 3D data in Artec Studio is the ability to make all necessary corrections and adjustments to 3D models, depending on doctors’ recommendations and any pathologies present. All adjustments need to be taken care of within 3D software, where accuracy levels can be controlled. If done manually to a ready-made corset, such adjustments could result in chafing, skin irritation, or sores. Now, after effortless alterations (should the need arise) the 3D scan data is put together into a 3D model, which is then sent to a milling machine to make a mold from a block of polyurethane.
For every patient scanned, Artec Studio also allows the archival of data, as well as viewing or updating the digital history later on. This enables doctors to reuse the 3D scan data for the casts if the patient needs to undergo similar treatment, which is often the case with spinal curvatures such as scoliosis, kyphosis, or lordosis. Avoiding the cumbersome storage of plaster positives weighing up to 50 kg also adds much flexibility to an orthopedic specialist’s routine.
“We are now able to perform hundreds of operations virtually, and access them digitally.”
“We’ve been able to take a step forward thanks to the R&D made possible with Artec 3D. We are now able to perform hundreds of operations virtually, and access them digitally,” Alexandre Neut continued.
Since the NEUT team integrated Artec solutions into their process, they have been able to digitize their patients’ body parts ensuring complete safety and comfort. Especially for patients with spinal injuries or deformities, leaving the bed or excessive movement is no longer required; any of the discomfort and stress typically brought by the plaster casting procedure is prevented. Data acquisition, performed with great precision, has made it possible to minimize physical effort, save lots of time, and keep both the patient and the orthoprosthetist in good spirits.
Learn from the past, head for the future
A far cry from how a medical corset was made in the past, the new method seems to be equally appealing to everyone involved. Encouraged by the results they were achieving, specialists at NEUT adopted 3D technology with well-reasoned enthusiasm. “It also turns out that many employees, especially the youngest ones, are eager for these new technologies that are revolutionizing the daily lives of patients, orthoprosthetists, and manufacturing workshops,” Neut added.
“We’ve been able to enhance our century-old craftsmanship and take a technological step forward.”
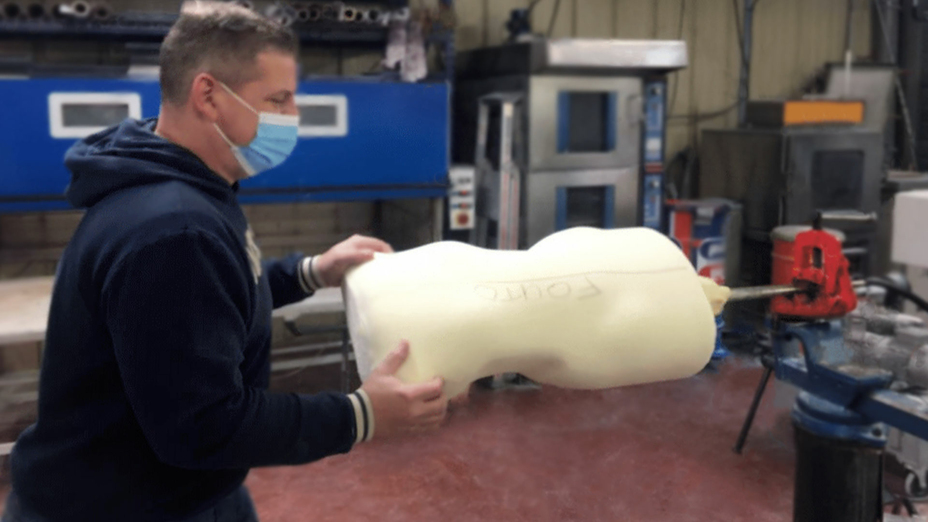
Corset making in progress (photo courtesy of NEUT)
True to their innovative approaches, NEUT’s team continues to dream big when it comes to technology: the orthopedic professionals hope to extend their use of Artec 3D tech to improve other medical devices they produce, and to design patterns for orthopedic footwear. It is especially inspiring that the company, the history of which spans almost a century, manages to respect their traditions without [missing out on] the ways of the future. “We’ve been able to enhance our century-old craftsmanship and to take a technological step forward in order to open ourselves up to new ways of doing, seeing, and designing,” Neut concluded.
NEUT’s high-end prostheses, orthoses, and orthopedic equipment are not just a successful business – besides their patients in France, the company has also helped disadvantaged people in Syria and Lebanon, training local medical teams, and sharing expertise in critical cases.
Whether for mass-produced or custom-made items, it has always been a matter of principle at the company to use cutting-edge techniques, materials, and equipment, to find the most accessible and comfortable solution – and it is this that has led to a perfect pairing with Artec 3D.
Scanners behind the story
Try out the world's leading handheld 3D scanners.