Redesigning an exhaust system from an Artec Leo scan in under one hour with Artec Studio and Design X
The Goal: To use a wireless handheld 3D scanner to digitally capture the undercarriage of the Volvo in 10 minutes, then export the 3D model to Geomagic Design X and redesign the exhaust system in less than one hour.
Tools Used: Artec Leo, Geomagic Design X
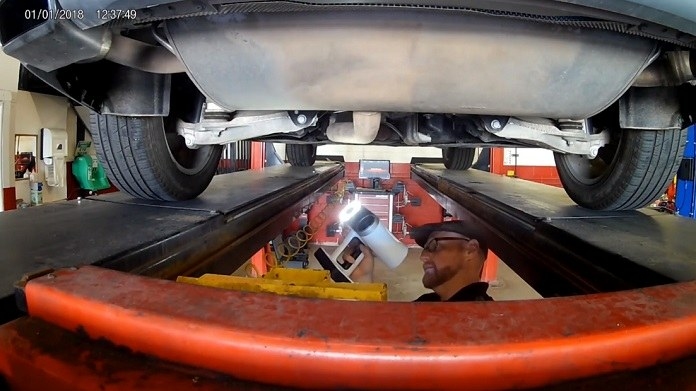
Reality 3D’s Stuart Bell using Artec Leo to scan the undercarriage of a Volvo XC90 in 10 minutes
Reverse engineering auto parts can be a challenging task, especially for modern, high-performance cars, where design tolerances are tighter, and new components must adapt perfectly with the car’s existing structural landscape and technical requirements.
When it comes to working with accurate CAD models of auto parts, even tracking down such models can be difficult to impossible, especially in the case of older parts no longer commercially available. That’s why a growing percentage of design engineers are choosing reverse engineering as the first step towards their new designs.
For years now, 3D scanning has proven itself as an extremely effective tool for this process, delivering highly-accurate results at a fraction of the cost and time of other methods.
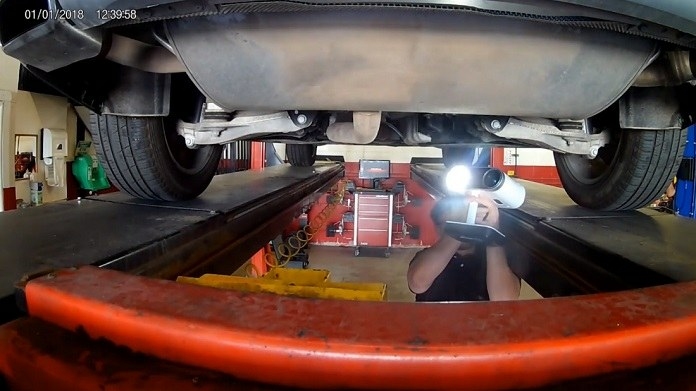
Finishing up the Artec Leo scan of the Volvo XC90’s undercarriage
As part of a demonstration on using 3D scanning and CAD software for reverse engineering the exhaust system of a Volvo XC90, Artec Gold ResellerReality 3Dused anArtec Leoprofessional handheld scanner to digitally capture the entire underside of the car in just 10 minutes.
A revolutionary 3D scanner, entirely wireless, with onboard processing and a battery pack, Leo is rich with intuitive features that make it a favorite among beginners and scanning pros alike.
With the built-in touch screen, you can watch your scan appear in real time, even rotate the scan this way or that, and check to confirm that you’ve captured every single part of your object. With Leo’s fast capture rate, medium-sized objects can be digitally captured in brilliant color in only a handful of minutes.
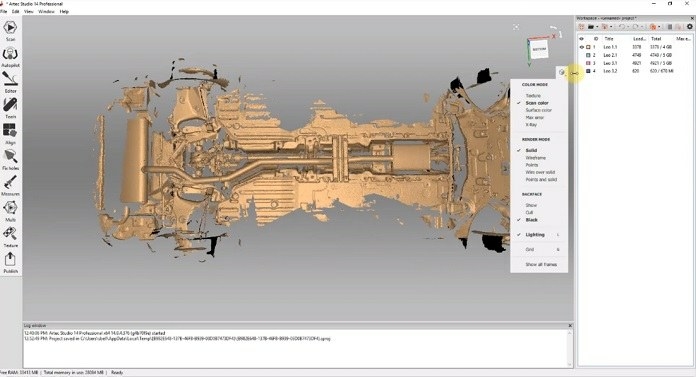
Artec Leo scan in Artec Studio post-processing software
After the underside of the Volvo was scanned, the scan datasets were post-processed inArtec Studio, which took only 15 minutes, with a minimum of effort. Artec Studio is a world-renowned software application integrated with Artec’s full line of 3D scanners. With an intuitive, feature-packed interface, Studio lets you export directly to SOLIDWORKS, AutoCAD, and Design X, easily remove glare from scans, and make your 3D scans better than ever before, in record time.
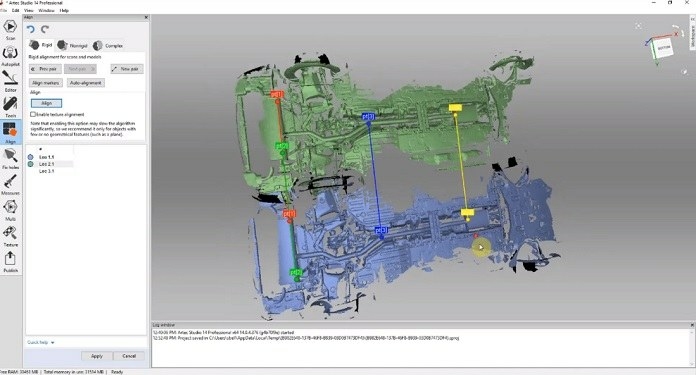
Aligning the scan sets in Artec Studio
Global Registration aligned all the scan sets into the same global coordinate system. Along the way, the Eraser tool was used to clean up unwanted data, to refine the portion of the scan intended for CAD purposes. The next step was to apply Sharp Fusion for creating a single mesh from all the scans.
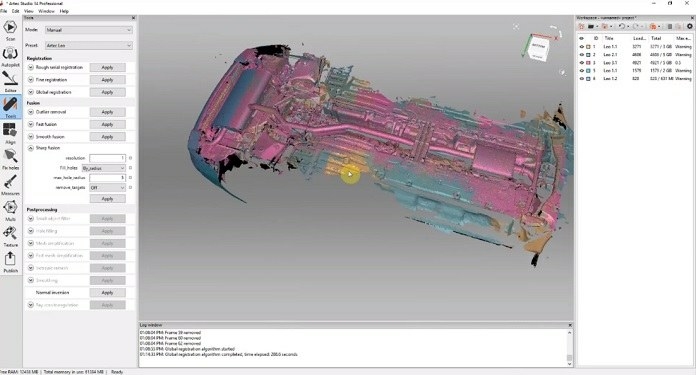
Applying Sharp Fusion for creating a single mesh
At this point, Mesh Simplification was applied, to reduce the size of the mesh, decreasing the number of polygons and making the model easier to work with. Due to the feature’s adjustable settings, the user is easily able to avoid sacrificing any crucial details or complexity.
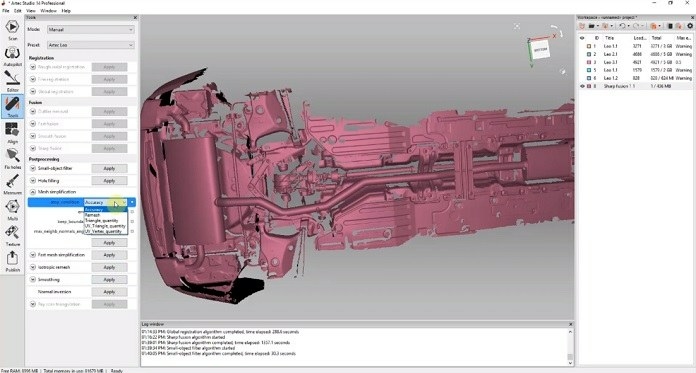
Applying Mesh Simplification to reduce the model size
The 3D model was then exported toGeomagic Design Xas an STL for CAD.
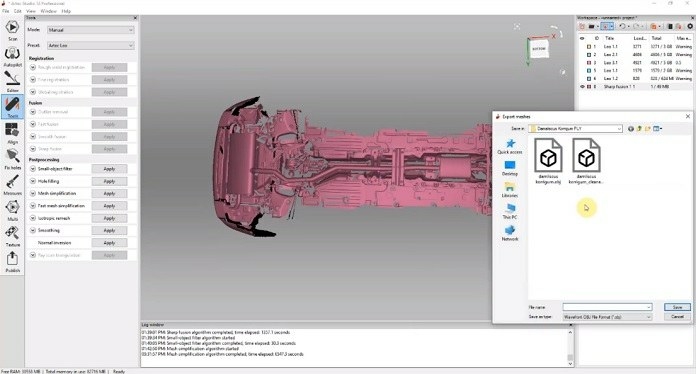
Exporting to Design X for CAD work
In Design X, the STL file was imported; and using Design X’s Pipe Wizard, the existing exhaust pipe was easily selected for reverse engineering. Then by specifying the shape, size, and other details, a new, high-performance exhaust system was created step by step.
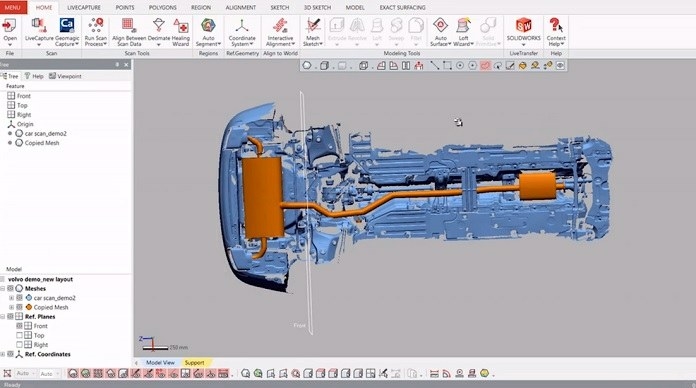
In Design X, where the new exhaust system will be designed in the minutes to come
The exhaust pipes were fine-tuned, making adjustments as needed to seamlessly adapt them to the other components in their path along the underside of the car. After a total of just 30 minutes in Design X, we have the final results: a metrology-grade CAD model of our custom exhaust system, with the diameter, length, and contours of the new pipes matching flawlessly with the car’s existing components and structures.
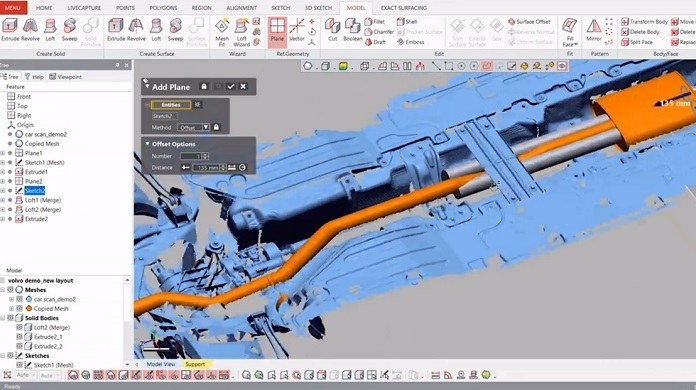
Creating a dual-exhaust system that perfectly matches the car’s existing structure
Summary of work completed: 10 minutes of scanning with Artec Leo, 15 minutes of post-processing in Artec Studio, and 30 minutes of CAD work in Design X.
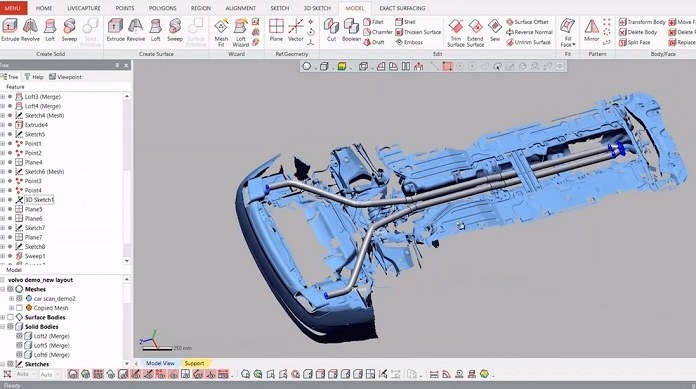
The finished custom exhaust system, designed in under one hour
Scanners behind the story
Try out the world's leading handheld 3D scanners.