BD Engineering digitizes entire Toyota Supra with Artec Leo for custom drifting mods
Challenge: Taking apart an entire Toyota Supra sports car and digitizing its constituent parts to create 3D models that can be customized and turned into aftermarket modifications.
Solution: Artec Leo, Artec Eva, Artec Studio
Result: A Supra model so detailed that it’s set to be used as a dynamic simulation environment for the testing of new suspension geometries, as well as a differential and hydraulic handbrake redesigned for drifting applications.
Why Artec 3D?: Manually measuring each part would’ve made reverse engineering the Supra an impractically time-consuming task. With the incredibly fast, wireless Artec Leo, BD Engineering has easily been able to digitize the car in mere hours, and use resulting data to develop a basis for never-before-seen drift part designs in Artec Studio.
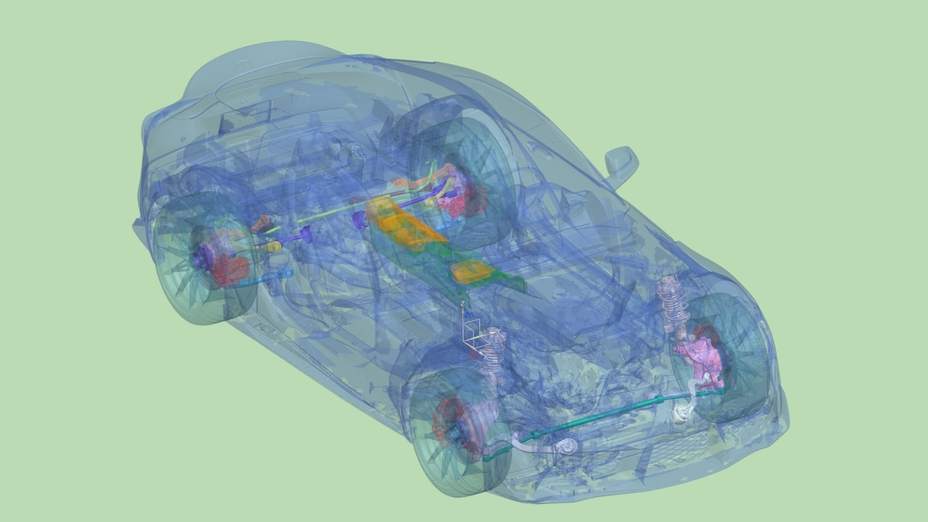
BD Engineering’s reverse engineered Toyota Supra and planned modifications. Image courtesy of BD Engineering
Ever dreamt of putting together your perfect car? Plenty have, as the burgeoning $16 billion US automotive aftermarket part industry shows, but how easy is this to achieve in reality?
One of the main challenges to customization is ensuring that modifications fit seamlessly with a car’s existing chassis or bodywork. As most OEMs aren’t keen on sharing valuable design data with aftermarket part developers, this creates a major problem: how do they know what’s hiding under the hood when modifying vehicles?
Luckily for engineers (and auto enthusiasts), reverse engineering technologies are advancing at pace, and they now allow parts to be digitized in seconds. Some aftermarket firms have stuck to their wheel guns, using carving or molding for customization, but not BD Engineering. It continues to push boundaries in automotive and beyond – with the help of Artec 3D scanning.
‘Closing the loop’ at BD Engineering
Eight years ago, engineer Adam Bao set out to create car modifications at his local college. However, what started out as a passion project quickly snowballed into what is now Illumaesthetic, a thriving business that has customized cars displayed at leading automotive trade shows like SEMA and Tokyo Auto Salon.
In turn, these success stories have led to demand from industrial, medical, and defense clientele, prompting Bao and Co-founder Nikita Rushmanov to set up another firm: BD Engineering. Equipped with 3D scanning and advanced manufacturing machinery, the company helps clients with everything from rapid prototyping and inspection to on-demand production.
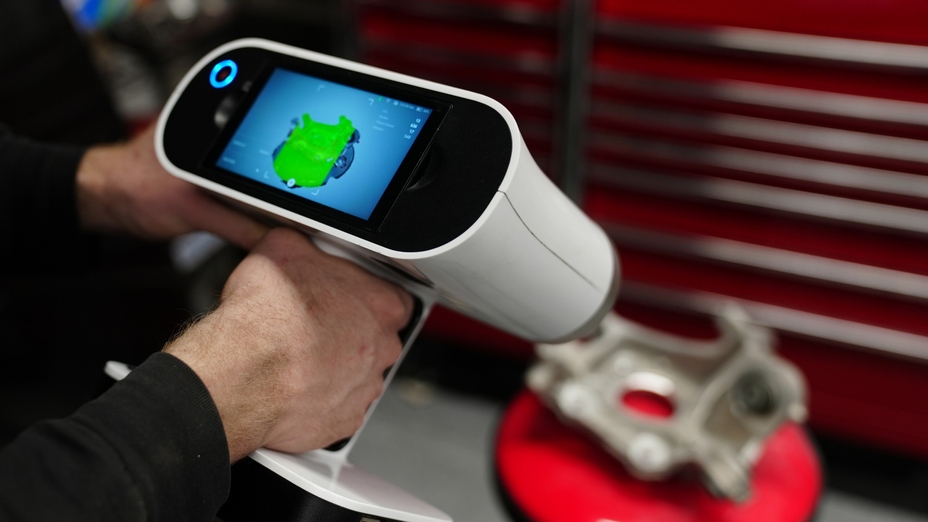
Digitizing a suspension piece with Artec Leo’s built-in display. Image courtesy of BD Engineering
But how did BD Engineering end up using 3D scanning in the first place? In the early days, Bao toyed with smartphone photogrammetry, digitizing objects and turning them into mod-ready design files. Realizing that the technology was neither fast nor accurate enough, he sought out a new approach, based around a rapid, 0.1 mm accuracy 3D scanner: Artec Eva.
As aftermarket demand grew, BD Engineering later reached out to Indicate Technologies. The Artec Gold-certified partner advised the firm to upgrade to Artec Leo, a wireless, AI-powered device that allowed its two original sites to flourish simultaneously. This, despite the premises being hundreds of kilometers apart, in Newark and Los Angeles respectively.
Rushmanov later moved upstate, but the pair found they could initially share Leo back and forth across California, with its all-in-one nature, complete with a built-in display, making it easier than ever to take their work on the road. Since then, the enterprising duo haven’t just integrated 3D scanning into their wider workflow – they’ve come up with a fairly unique way of doing so.
“In automotive, I see a lot of people only scanning half the car,” explained Bao. “That just isn’t a very good idea. When you scan clockwise, you’ll notice that where you start and end can be 6-12 inches off. Unless you have a full circular loop there’s a lot of error propagation. We say, ‘f**k it, let’s scan the whole car.’ I call it closing the loop.”
“With Artec Leo, the difference in time it takes to scan the front end versus the entire car is so insignificant, that we just thought ‘why not scan the whole thing?’”
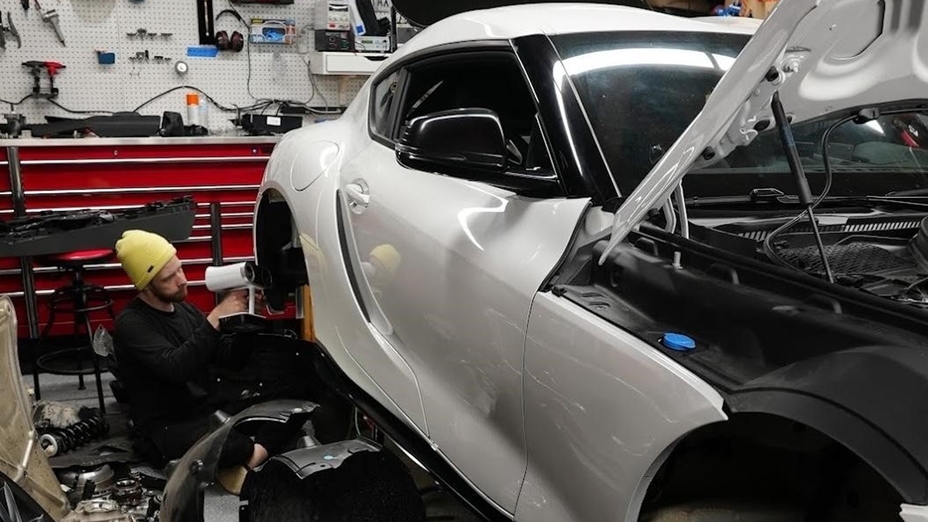
Nikita Rushmanov, Co-founder of BD Engineering, digitizing a stripped down Supra with Artec Leo. Image courtesy of BD Engineering
Drifting into new verticals
Not satisfied with their work at Illumaesthetic, customizing gauges and tail lights for the likes of General Motors and BMW – at one point even enhancing an iconic Subaru’s bumper – the pair have now set themselves a loftier goal: full-vehicle reverse engineering.
In an early full-vehicle exterior scan, Bao found he was able to use Artec Eva to digitize an entire Honda S2000. Though the project only took two hours, he says putting minimal tape on the car slowed him down, and with the 35 million pt/s Leo, he could’ve done it much faster.
“Obviously, I was motivated to put as few markers on the S2000 as possible,” said Bao. “So, I started with what I thought I needed, then realized I needed more, and I was constantly going back and forth. Leo is so quick, you could just spend 15 minutes preparing the headlights, mirrors, windows, any black plastic trim, and another 15 minutes scanning.”
As part of BD Engineering’s latest digitization project, Rushmanov has now fully reverse engineered his work car – a 2023 GR Toyota Supra. By stripping the car down and scanning each piece of its suspension, as well as its subframe, he has been able to create an extensive modification, with a hydraulic handbrake designed for drifting.
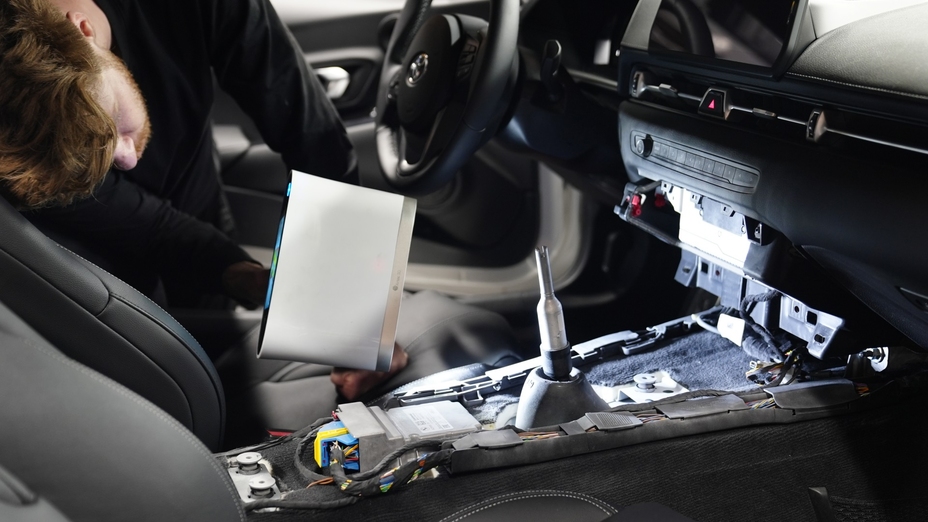
Rushmanov using Artec Leo to 3D scan the handbrake of a Toyota Supra. Image courtesy of BD Engineering
While the rapid, maneuverable Leo ensured this was fast and easy, Rushmanov says Artec Studio’s editing toolset proved equally useful for streamlining mesh alignment, overcoming design constraints, and removing polygons to reduce export file size.
“Artec Studio can go a long way, I actually really enjoy using it,” added Rushmanov. “Artec Studio’s approach to reverse engineering is quite innovative, because of the way it lets you solve all your design constraints at once, then refit. It saves so much time.”
“We’ve reverse engineered the entire car, with the aim to set up a dynamic simulation environment that numerically optimizes the cost of new suspension parts.”
Establishing a “scan-to-factory” setup
Amid growing demand for digitized, 3D printed parts, BD Engineering has increasingly begun working with clients outside Illumaesthetic’s traditional automotive base. According to Bao, it has achieved this by moving beyond offering 3D printing as an “intermediary service.”
Traditionally, he says OEMs would order 3D printed mockups to “market vehicles, not through renders, but physical part photos” for promotion ahead of launch. While Illumaesthetic still gets these customers, BD Engineering has started using the technology elsewhere – in one case to create a fuselage, which has been turned into a mold for making military target practice drones.
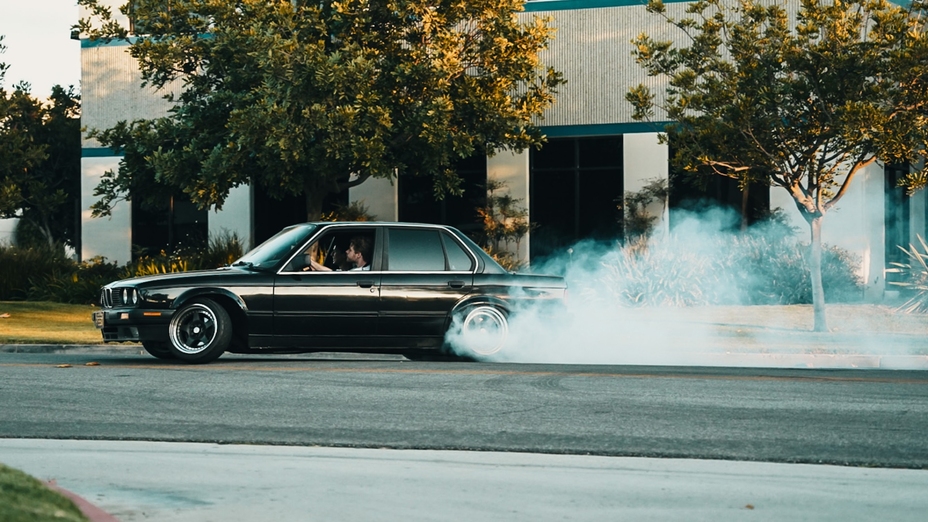
Rushmanov showcasing his drifting skills in a classic BMW. Image courtesy of BD Engineering
In terms of its Supra modifications, Rushmanov eventually plans to manufacture and sell them to drifters around the world. In the meantime, he says his company intends to establish a “scan-to-factory setup,” in which customers can drop things off for digitization and have visual or performance parts ready for production inside a month.
“We’re constantly having things dropped off for 3D scanning, because customers see what we do blows everyone else out of the water. We don’t just scan what’s needed, we take things to another level.”
Scanners behind the story
Try out the world's leading handheld 3D scanners.