Artec 3D scanning technology recreates dinosaurs in Jurassic World
The Goal: To use a handheld 3D scanner to capture the existing Apatosaurus model, turn this into a 3D model, and use this to create a perfect copy of the original head and neck, only bigger, exactly what Mr. Spielberg asked for.
Tool Used: Artec MH (predecessor of Artec Eva)
Jurassic World has just broken the all-time opening weekend box office record, raising the bar for special effects artists, just like the three previous installments of the Jurassic Park series did. We are extremely proud that our clients from Legacy Effects contributed to this box office hit by using an Artec scanner to create the most true to life dinosaurs ever to be seen on screen!
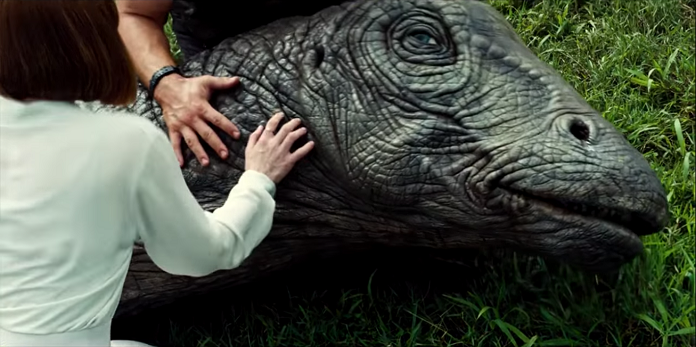
Here’s a really awesome behind-the-scenes video showing the craftsmanship it took to pull off one of the most crucial scenes, featuring a close-up of the head and neck of a dinosaur interacting with the two lead actors. It’s amazing how natural the dinosaur’s movements and mimics look – this animatronic piece is in fact acting in the scene.
Now, how did the LE team make the dinosaur look so realistic? Well, the process was quite complex, as the video shows. The most interesting part for us is how an Artec scanner saved the day for the team. They started out by milling the dinosaur’s head and neck, then detailed them up, and then according to LE’s co-owner John Rosengrant, “Steven Spielberg confirmed with Colin [Trevorrow, the director] it needs to be bigger.”
In the pre-3D scanning world, they would’ve had to start the job all over again from scratch, but luckily they had an Artec handheld scanner, MH. Even though it’s an earlier model, it still works fine for top-notch special effects.
When the team was ordered to do a rescale, they got the MH scanner involved, which you can see at work starting 1:19 in the video. The solution the LE engineers went with was rapid prototyping – they scanned the physical mold with the MH to turn it into a 3D model, which they could then modify in CAD software.
“We scan what the artists traditionally sculpted and at that point once it’s in the computer we can then go to any scale that’s needed,” says LE’s lead systems engineer Jason Lopes. “So instead of starting over we were able to save a lot of manhours.”
The MH scanner is what the next-generation handheld scanner, Eva, was inspired by. Both have the same 3D resolution, point accuracy and linear field of view, but Eva scans faster, boasts a five times higher accuracy over distance rate and renders the texture of the scanned object, meaning you get a full-color model.
Scanners behind the story
Try out the world's leading handheld 3D scanners.