Multi-resolution Leo & Artec Ray II 3D scanning unlocks fuel efficiency gains
Challenge: Uncovering a fast, accurate way of turning vehicles into highly detailed 3D models that can be used in simulations to iterate upon designs and enhance their range.
Solution: Artec Leo, Artec Ray II, Artec Studio
Result: A 3D truck scan captured with such fidelity that it could be fed directly into Airshaper’s program for analysis and design optimization. After just a few hours, the platform had found ways of reducing drag, improving airflow, and making the vehicle more fuel efficient.
Why Artec 3D? Not all scans are precise or accurate enough for meaningful computational fluid dynamic (CFD) simulation. Combining Leo and Ray II, using the highest quality data from each – with Leo capturing difficult to reach areas like wheel arches and Ray II picking up with the wider picture – yielded an ideal aero model with never-before-seen resolution.
The 3D truck model used to carry out Airshaper’s aerodynamic analyses.
If you don’t work in trucking or logistics, you may not be aware that your average semi-trailer truck carries 120-150 gallons of fuel. When you consider that the US alone has nearly three million of these, it’s clear they’re responsible for burning a lot of petrol each day.
Of course, the fuel efficiency of such vehicles is determined by multiple factors, including load, driving style, engine size, and more. But one area that’s easy for truck manufacturers to overlook in pursuit of design functionality, is aerodynamic drag.
Generated by all vehicles as they pass through the air, this force only gets stronger as they travel at speed, and requires them to use more horsepower (and fuel) to accelerate. With the average truck using up 50% of its forward energy to push air away at highway speeds, it’s thought that 20% drag reductions could yield fuel savings of up to 10% per trip.
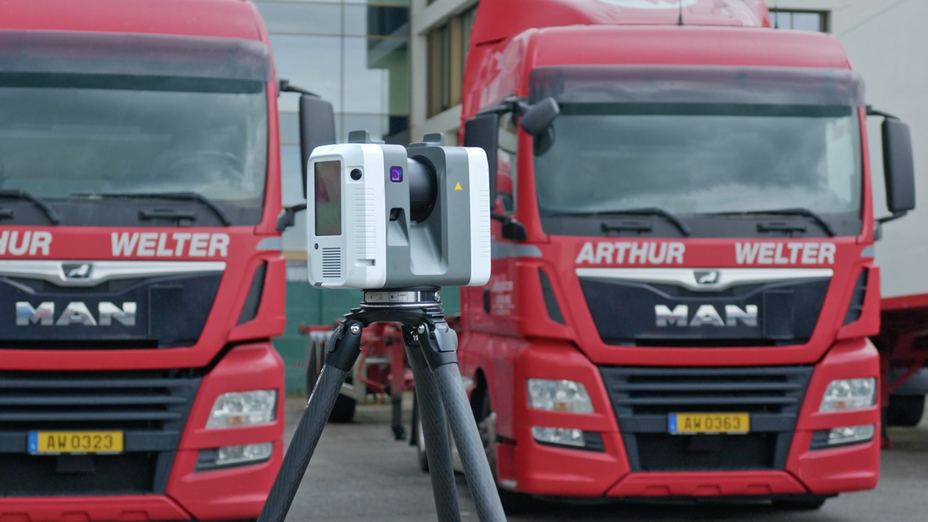
Artec Ray II being used to 3D scan a truck in the carpark of a local air freight company.
Improving vehicle aerodynamics often means conducting CFD analysis to find out which parts are the draggiest, but creating a watertight model for the first simulation takes weeks. Where Airshaper streamlines the process is by allowing users to identify design upgrades by simply uploading and analyzing highly detailed Artec 3D scans – yielding results in a matter of hours.
Multi-resolution truck scanning
Working from its HQ in Antwerp, Belgium, Airshaper is a developer of cloud-based software that allows users to conduct complex aero simulations, without needing heavy-duty hardware. Earlier this year, the firm sought to showcase its platform’s potential in this area by digitizing a truck, only for best results, it needed to be captured in soaring resolution: enter Artec 3D.
Working with Airshaper, Artec specialists helped digitize an entire long-haul vehicle in less than two days’ scanning. Ray II’s scan pre-aligning Visual Inertial System (VIS) was pivotal to this, as was its 2 million pt/s speed and built-in three 36 MP camera system, which allowed the team to capture the HDR textures needed to achieve true-to-life colors.
In tandem, the uniquely wireless Artec Leo, complete with intuitive built-in display and a broad 838 x 488 mm field of view, made it much easier to get around and digitize large parts like radiator grilles and sun visors. According to Artec 3D scanning specialist Dmitry Potoskuev, navigating the same process with a traditional wired scanner would’ve been a nightmare.
“Scanning the top of the cabin on a stepladder was much simpler without a laptop,” said Potoskuev. “The same went for parts between the cab and trailer – the wireless nature of Leo allowed us to crawl in and scan from underneath. The entire front of the truck was scanned with Leo – it certainly made capturing quite a few parts easier than it otherwise would’ve been.”
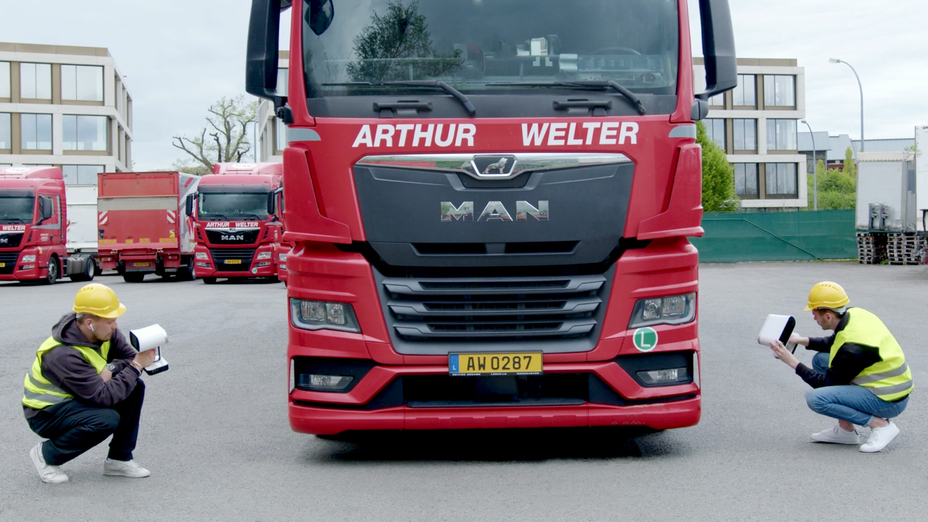
Two Artec Leo 3D scanners digitizing the truck’s main cabin.
Not just a great showcase of Leo and Ray II’s individual capabilities, the project showed how the pair can be combined to create incredibly detailed meshes, using the highest resolution data from both. With Artec Studio’s Smart Fusion algorithm, it’s even possible to merge scans at the click of a button, in a workflow with the potential to revolutionize data capture at scale.
Uncovering fuel savings
Once the team had an accurate truck mesh, analyzing its aero performance was as simple as uploading it to the cloud-based Airshaper platform. From there, they could choose from three project complexity presets, set up simulation parameters, and deploy its ‘virtual wind tunnel’ algorithms to analyze everything from airflow to noise output.
When Airshaper’s report was ready a few hours later, the results were staggering. It turned out the truck used 76,000 watts (102 horsepower, though this figure is likely closer to 200 when factoring in the power to combat forces like tire resistance) overcoming aero drag at highway speeds.
Through detailed 3D visuals, Airshaper’s platform also revealed the main drag perpetrators. In this case, the cabin, flow deflectors, and sun visors were all identified as vital aero elements, but it was the mirrors and roof causing particularly disruptive turbulence.
To make it slip through the air more easily, it was suggested that the mirrors be repositioned, roof openings be limited, and spoilers be better aligned for air deflection. Airshaper’s Wouter Remmerie has hailed 3D scanning for unlocking these insights, as it allowed the team to capture the truck in pieces, and break it down for “part-by-part force analysis.”
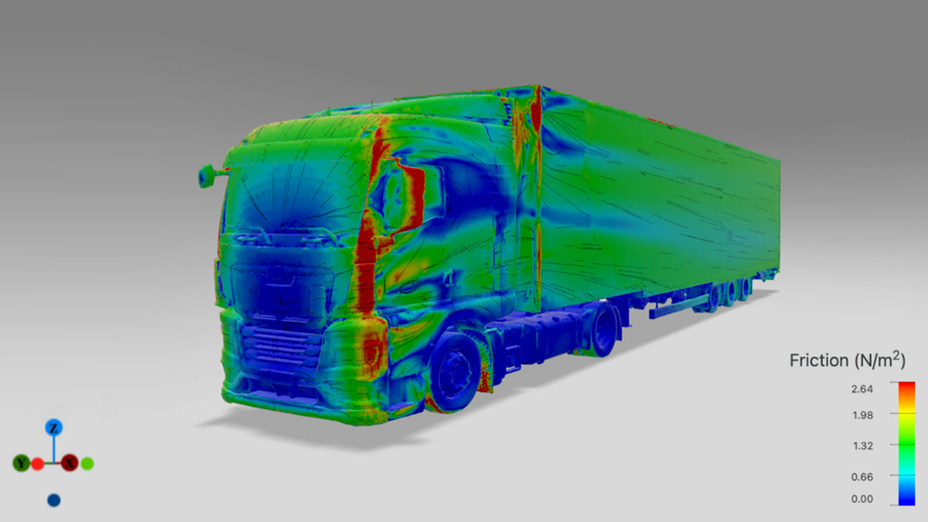
A graphic indicating the highest points of surface friction generated by the 3D scanned truck as it travels through the air.
”We had a massive amount of detail to play with and this was directly captured in the simulation,” said Remmerie. “Even though you have a certain loss of detail as you go from reality to scanning, and scan to mesh, we still managed to capture all the small details fantastically well. In the model, the mirrors and grille were clearly defined, you could even see the tire threads.”
Next up: boosting EV range?
With Airshaper’s platform already used to optimize aero and avoid expensive redesigns or having to bolt on aftermarket parts, by stalwarts like Tesla and Morgan, Remmerie now anticipates it finding further electrical vehicle (EV) use cases.
EVs may be more sustainable than petrol vehicles, but they still spend a lot of energy cutting through the air. Remmerie says making them just 10% more streamlined could yield 5% energy savings, enough to reduce the size and weight of their onboard batteries.
He says this figure is backed by analyses around EVs like the Tesla Semi. A recent Airshaper study showed how changing mirror positioning, cabin shape, and trailer alignment made the Semi less draggy than other trucks. As such, it’s expected that competitor analysis aided by 3D scanning, will soon become a significant draw for the firm’s customers.
“If you’re designing a new truck and someone else produces a vehicle with a massive range, you’ll want to understand how they achieved this through 3D scanning,” concluded Remmerie. ”That’s one of the technology’s key benefits here, you can analyze an existing truck, find out how it tackles aerodynamics, and take those lessons to improve your own vehicle.”
“We used to have a mature market, but with EVs and trucks, things are being pulled wide open again. So understanding new vehicle designs with 3D scanning is only going to become more important.”
Interested in finding out more? You can view Aishaper’s full 3D truck report here.
Scanners behind the story
Try out the world's leading handheld 3D scanners.