3D scanning a Luxembourg Air Rescue helicopter with Artec Leo & Ray
Challenge:To 3D scan a full-sized air rescue helicopter from skids to blades and every single exterior detail in between using a tripod-mounted, long-range laser scanner and a professional handheld 3D scanner. And then, to transform the resulting scans into an exhaustive 3D model of the aircraft.
Solution:Artec Leo, Artec Ray, Artec Studio
Result:All the 3D scanning was carried out onsite in an aircraft hangar, taking less than 11 hours in total for both scanners. Then, in the days to come, the scans were transformed into an exceptionally lifelike 3D model of the helicopter. The process data was then ready for a variety of aerospace applications from reverse engineering to inspection, aerodynamic analyses and more.
Why Artec 3D?With Artec Leo’s portability and onscreen display, combined with Artec Ray’s wide scanning range, the aircraft was easily and accurately captured in its entirety, with a realistic 3D model processed and created in Artec Studio.
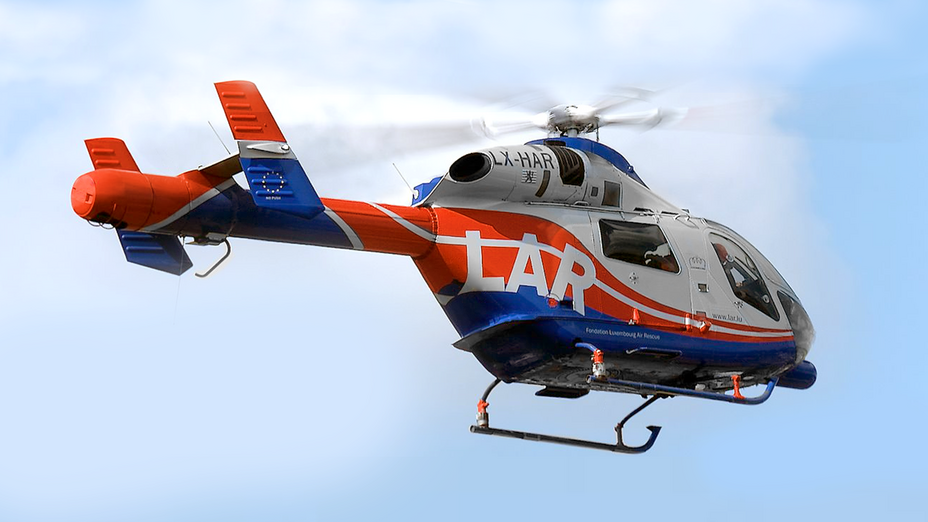
From the moment a call for help comes in via the national 112 emergency call center,Luxembourg Air Rescue’s(LAR) McDonnell-Douglas MD-902 Explorers can soar through the sky and reach any location around the country in 10 minutes or less. Since their adoption in 1996, this non-profit organization’s fleet of helicopters has flown more than 30,000 flight missions.
Apart from special humanitarian missions, LAR’s six MD-902 helicopters see frequent use in response to emergencies as well as transporting intensive care patients between hospitals within Luxembourg and to/from the Greater Region.
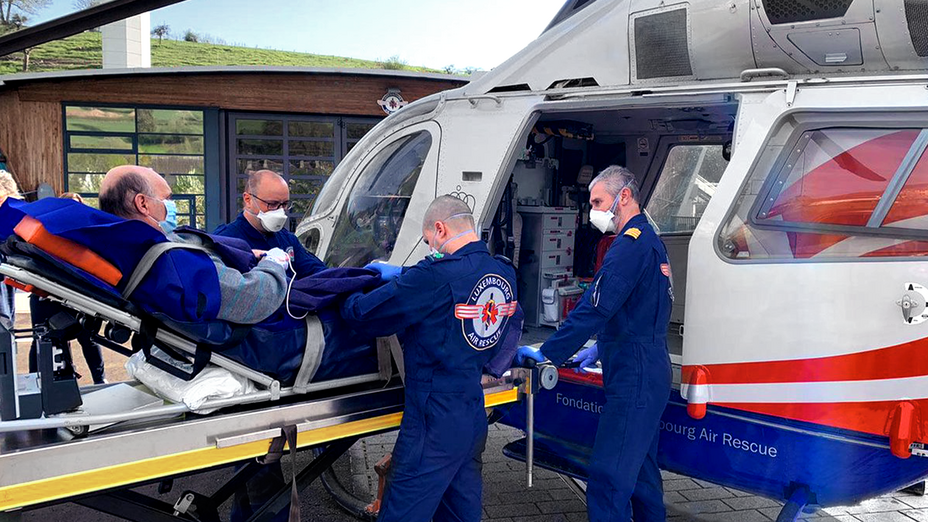
Luxembourg Air Rescue flight team preparing a patient for medical transport
A state-of-the-art helicopter with diverse possibilities
Today, the MD-902 can be found worldwide in a variety of other roles including search and rescue, police, military, light utility, and others. As such, the aircraft can be outfitted with different configurations and equipment, both internally, in the cockpit and cabin, as well as externally, on the fuselage.
The flight deck (cockpit) can be equipped with special avionics suites, tactical displays, and dashboards. And in a military role, the MD-902 can be modified with door-mounted Gatling guns, 70mm rocket pods, and a FLIR sensor beneath the nose section.
As a proof of concept for employing3D scanning technologyto capture large objects such as helicopters and fixed-wing aircraft for applications including reverse engineering, inspection, and aerodynamic flow simulation (CFD) testing, Luxembourg Air Rescue teamed up with Artec 3D – also headquartered in Luxembourg – to scan a McDonnell-Douglas MD-902 Explorer. The helicopter was 3D scanned with two of the latest professional 3D scanners: Artec Leo and Artec Ray.
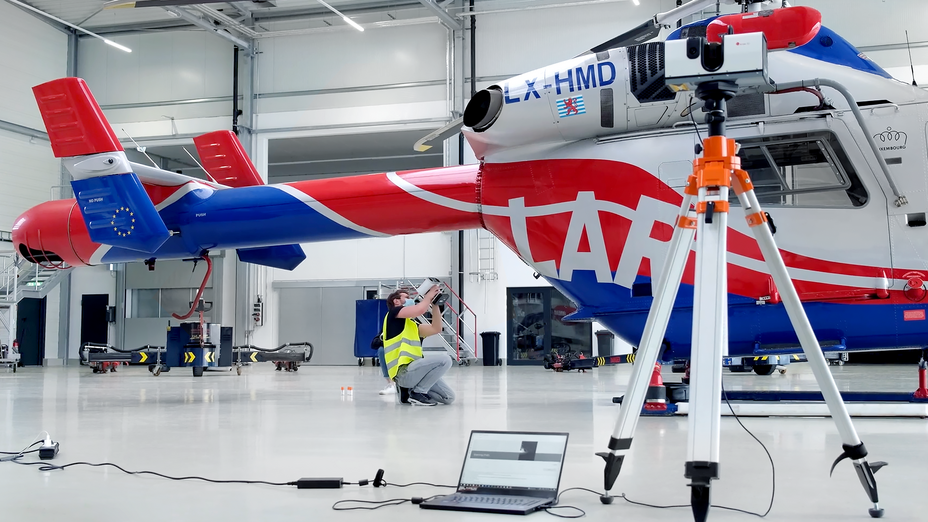
Scanning the MD-902 with Artec Ray and Artec Leo
One day, two 3D scanners
The Artec Leo, a unique, easy-to-use 3D scanner with onboard processing and a rear touchscreen gives users the power to scan medium-sized to large objects without any need for cables, a battery pack, or connected laptop.
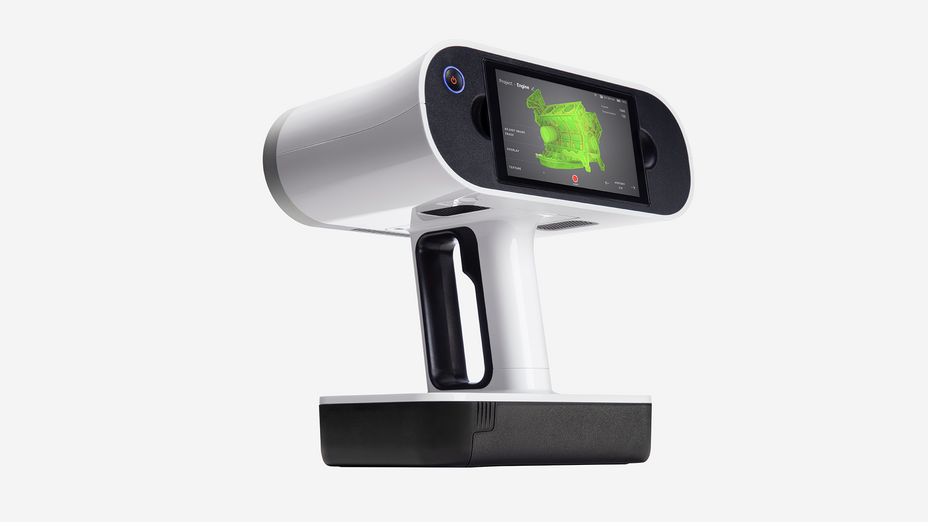
The Artec Leo
With up to .1 mm accuracy, Leo excels at capturing even complex levels of surface geometry as well as a full spectrum of colors via the scanner’s texture camera. Leo was used to scan the MD-902 in its entirety, from tail to nose.
The other scanner used for the project, the Artec Ray, is a tripod-mounted,long-range 3D scannerintended for capturing large objects.
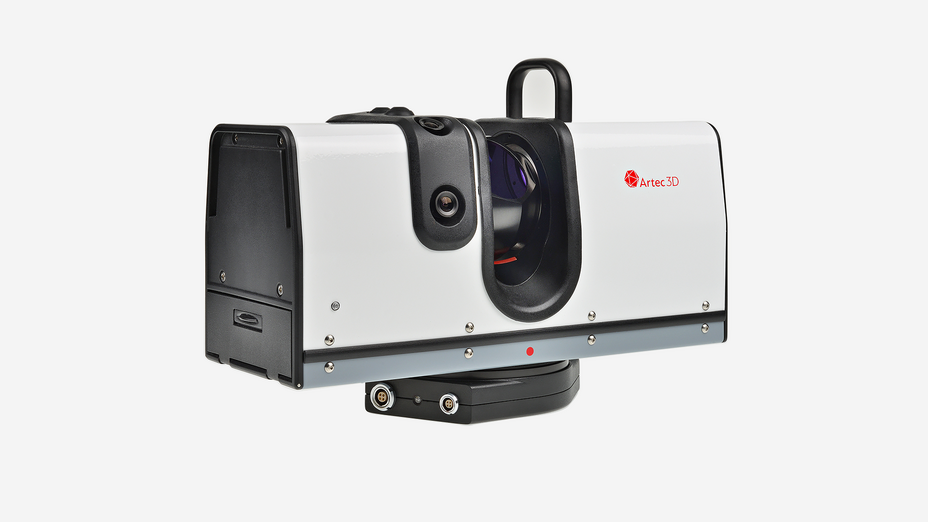
The Artec Ray
With metrology-grade, submillimeter accuracy, and a working distance from two meters all the way out to 110 meters, the Ray can scan anything from a car to a bus or even a massive yacht, not to mention being able to capture entire areas and scenes, such as traffic accident scenes, crime scenes, and more.
Scanning the MD-902 from bottom to top
When it came time to scan the Luxembourg Air Rescue McDonnell-Douglas MD-902, the Artec Ray was used mostly for alignment purposes, taking 16 scans in total, from multiple positions around the helicopter, eight from a lower level, and eight from above. This stage of the scanning took less than three hours from start to finish.
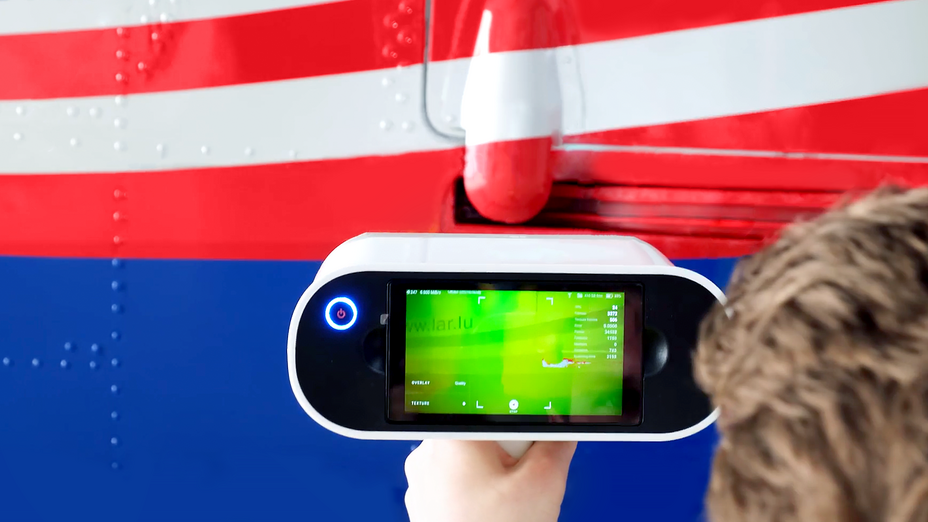
Artec Leo capturing the fuselage of the MD-902
Next up was the Leo, which needed approximately eight hours to make 26 overlapping, submillimeter-accurate scans of the helicopter’s 34-foot-long (10.39 m) fuselage, capturing even the tiniest of details along the way.
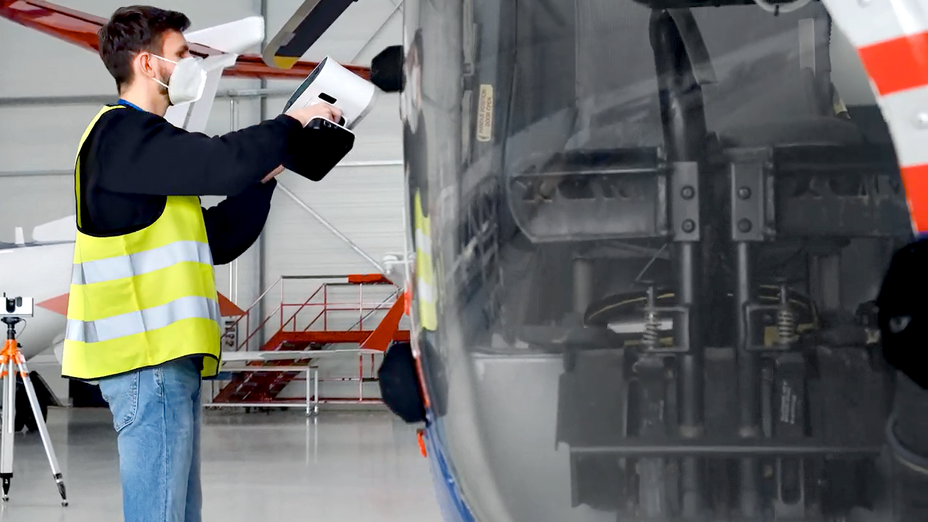
Scanning the side of the MD-902 with Artec Leo
To assist with faster alignment and global registration of the scans during the processing stage, additional texture features were applied, in the form of self-evaporating 3D scanning spray.
A few challenges along the way
To start off, scanning the underside of the MD-902 posed a number of difficulties. Without having a lift to raise the helicopter from the hangar floor, it was necessary to crawl underneath the fuselage and perform the scanning “from the ground up.”
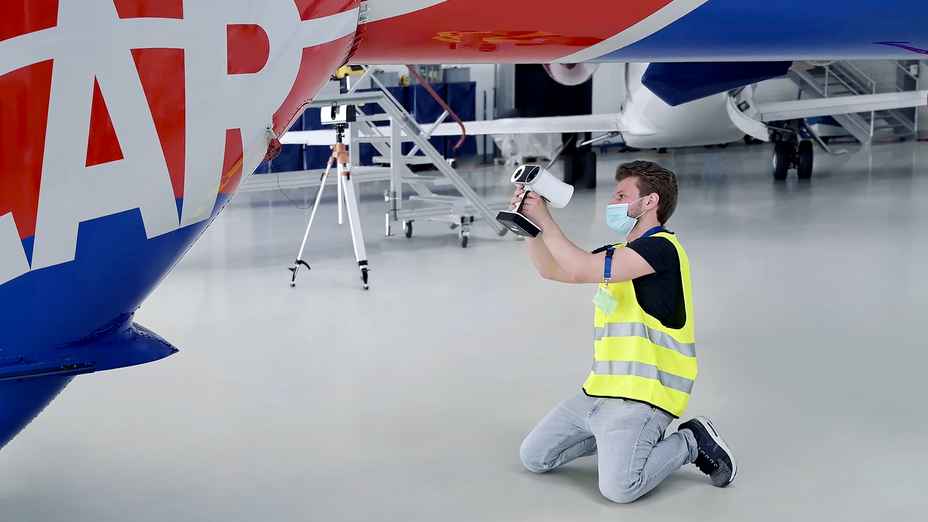
Scanning the lower part of the MD-902’s fuselage with Artec Leo
Working in such a tight space, it was a challenge at times to hold the Leo at a 90-degree angle, simply because the scanning distance to the body of the helicopter was so small: a mere 13 inches (350 mm) in some places.
Another challenge was scanning the blades of the helicopter. Accessing them required the use of Luxembourg Air Rescue’s mobile elevating work platform (MEWP). Since the blades are extremely long, thin, and black, with no distinguishing features to facilitate tracking, it was occasionally necessary to apply some masking tape to them in various sections.
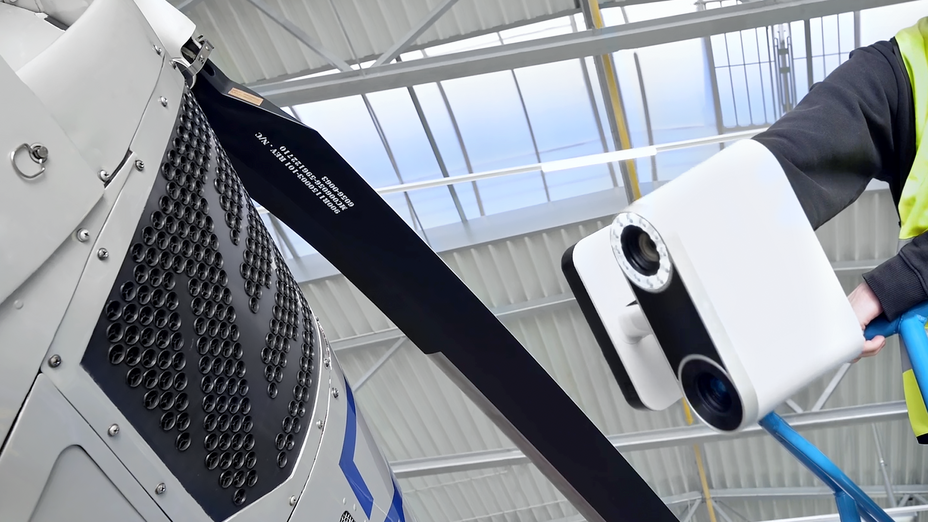
Capturing every single detail with Artec Leo
When it came to capturing the windows of the MD-902, unfortunately, scanning spray wasn’t permitted. Instead, the team was allowed to spray and scan the windows of a nearby demonstration helicopter, which has windows of a similar shape. From there, the scans of these windows were adapted to fit the window frames of the MD-902, with a bit of effort.
Once the scanning was complete, over the next two weeks, the data was processed inArtec Studiosoftware, where the scans were refined, aligned, and brought together to form a submillimeter-precise 3D model ready for a range of applications.
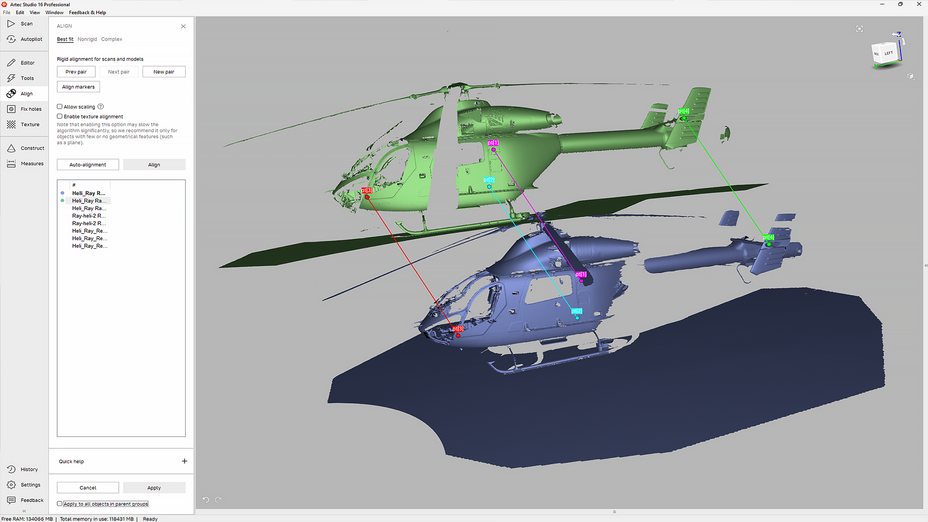
Aligning Artec Leo & Ray scans in Artec Studio software
Scan-to-CAD made easy
Rather than taking manual measurements of an aircraft such as the MD-902, which would demand excessive amounts of time and be subject to operator error, or working off of old blueprints that may or may not be accurate or complete, it’s much easier and faster to use ascan-to-CAD solutionto turn a 3D model of an aircraft into a precise CAD model. Artec Studio software offers a full set of tools designed to help make this process as streamlined as can be.
Whether it’s an MD-902, a Learjet, or anything bigger or smaller, the 3D scans made with Leo or Ray can be exported to a variety of CAD systems, where they’ll be used as dependable references for sketching and extruding an accurate CAD model to life.
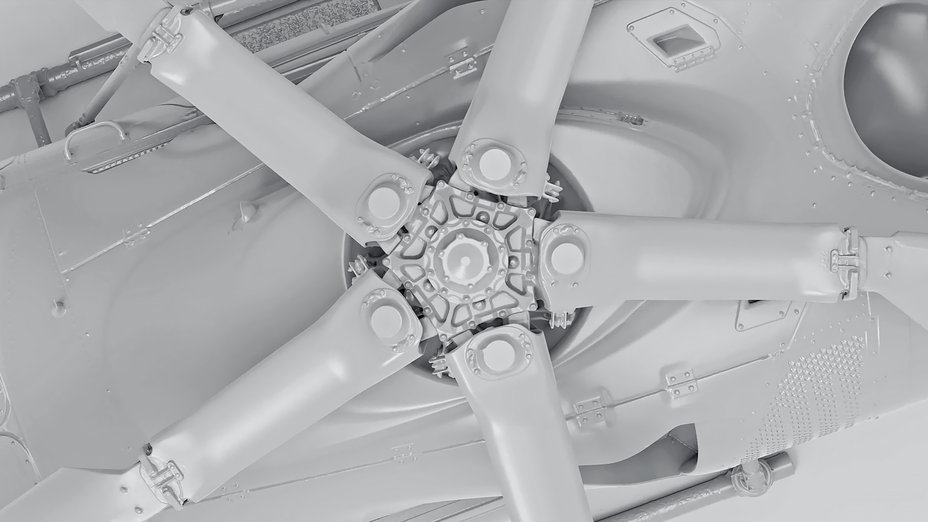
Top-down view of the MD-902 3D model, from Artec Leo & Ray scans
Then, when it comes time to design a new interior (considering scans of the cockpit and/or cabin) or exterior configuration for an aircraft, the resulting CAD model will indicate exactly where every mounting point, bolt hole, and rivet is, as well as how much room there is for installation of the intended components and design elements.
Reverse engineering legacy or hard-to-find parts
For any organization or company regularly flying and maintaining a fleet of aircraft that are decades old, the need will arise for mission-critical parts and components that may either have a lead time of weeks or months, or not be available at all.
In such cases, myriad aircraft parts can bereverse engineeredvia a CAD solution and 3D scanning, with the Artec Leo or Artec Space Spider scanner, for example, after which these components can be produced, on demand, using additive manufacturing, casting, CNC milling, or another technology.
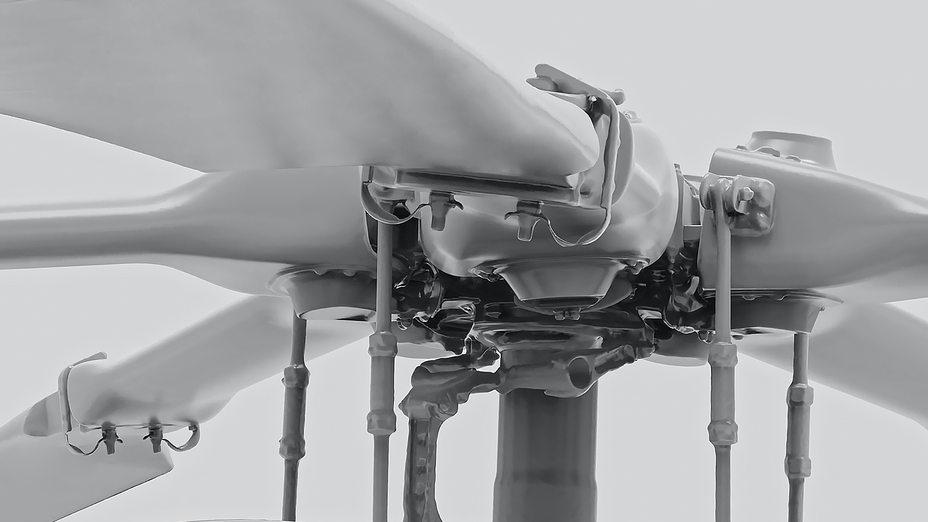
Side view of the rotor assembly of the MD-902 3D model
What’s more, CAD models made from these 3D scans can be used in synergy with FEA (finite element analysis) to design and produce optimized aerospace parts unavailable commercially.
Whether for retrofitting or future-fitting,3D scanning for reverse engineeringis a viable, proven solution for aerospace needs great and small. As the technologies advance rapidly from year to year, making it possible to create lighter, stronger, more affordable parts, and someday, entire fuselages and wings.
3D aircraft inspection
When aircraft of any kind, from light planes to helicopters or even passenger airlines are flying dozens to hundreds of sorties every year, they’re bound to incur some external damage. This can be due to heavy hail storms, hard landings, bird impacts, and other collisions.
Quickly and accurately measuring and quantifying such damage is crucial, not merely for insurance purposes, but also to understand the scope of repair work, to achieve as little downtime as possible.
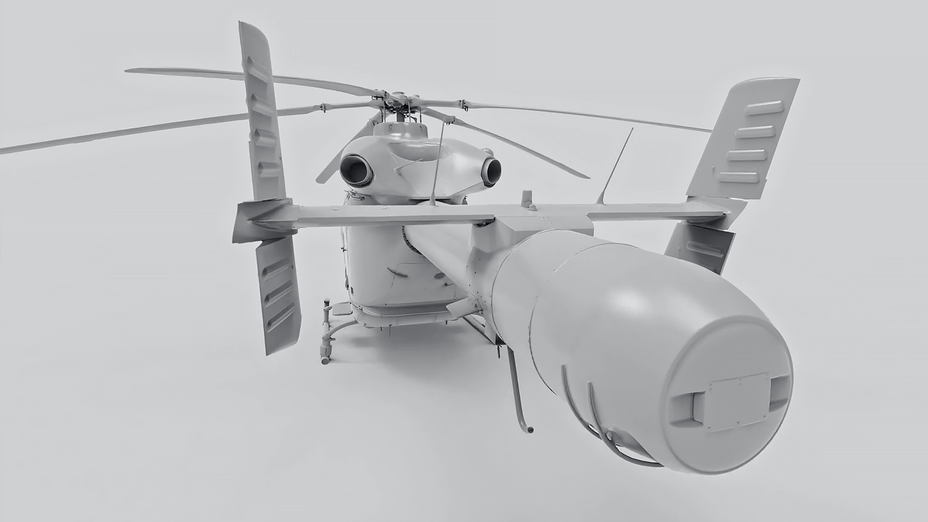
Up-close view of the MD-902 3D model’s NOTAR tail assembly
By 3D scanning a helicopter or other aircraft, as was done with the MD-902, it’s easy to use the subsequent 3D scans as a baseline model for performing surfaceinspections in Artec Studio, using the software’s surface distance mapping feature.
Any damage or changes in the external geometry, even those well below a millimeter, will be immediately visible using an easy-to-read heat-map. The scans can also be exported toGeomagic Control X, for even greater inspection possibilities.
Scanning for CFD aerodynamic analyses
Testing and understanding the aerodynamics of an aircraft is the first step towards optimization for improved fuel efficiency and flight performance. Today, more than ever before, CFD (computational fluid dynamics) testing is within reach of not only aerospace manufacturers, but also private and corporate owners.
What used to be an expensive and complicated process is now easy to implement and carry out on demand. All that’s needed to get started is an accurate 3D model or CAD model of the helicopter or other aircraft in question, such as the 3D model of the MD-902 created from the Artec Leo scans, as explained previously.
From there it’s possible to simulate and study the aerodynamic performance of any aircraft along with numerous design variables and fuselage configurations, in a range of atmospheric conditions.
For aerospace designers, among others, the advantages are many. Virtual prototype models with new configurations can be brought to life in days rather than the traditional weeks or months.
And then, during the prototype flight testing phase, by using an Artec Leo or Artec Ray scanner, depending upon the size of the aircraft, 3D inspections can be performed, to reveal metal fatigue, impact damage, or other structural changes that have taken place.
Summary
Although it can mean a day of scanning, and days or longer to process huge amounts of scan data into a3D model, this small, upfront investment of time and energy can translate to a multitude of benefits over the lifespan of a helicopter or other aircraft, whether for a single unit or an entire fleet.
In today’s world, achieving higher-tolerance results faster, easier, and at less expense should be on everyone’s radar. In aerospace and many other demanding spheres, 3D scanning withprofessional 3D scannersand software, such as Artec Leo and Ray, gives you the power to accomplish this very goal.
Scanners behind the story
Try out the world's leading handheld 3D scanners.