Wie das israelische Unternehmen A.B. Engineering Artec Leo für individuell angepasste Fahrzeugpanzerungen einsetzt
Herausforderung: Durchführung schneller und genauer 3D-Scans von zerlegten Fahrzeugen, um präzise CAD-Modelle zu erstellen, wie sie für die Anfertigung von individuellen Panzerungen für verschiedene Autos, Lieferwagen, Lastwagen und Busse benötigt werden.
Lösung: Artec Leo, Artec Studio, Dassault Systemes CATIA V5
Ergebnis: Mit Artec Leo kann jetzt in nur zwei Stunden ein zerlegtes Auto, ein Lieferwagen oder ein Lastwagen mit Submillimeter-Genauigkeit vollständig gescannt werden. Sprays oder Zielmarken sind in keinem Fall erforderlich. Nach fünf Stunden Verarbeitung sind die Scans bereit für CAD. Ältere 3D-Scanner erforderten Sprays, Tausende von Zielmarken und eine ganze Arbeitswoche, um die Fahrzeuge zu scannen, plus eine weitere Woche, um die Scans für CAD zu verarbeiten.
Warum Artec 3D? Da Leo zu 100 % kabellos und ohne Laptop arbeitet, kann er jederzeit für Scanprojekte eingesetzt werden. Leo ist selbst für Anfänger einfach zu bedienen und erfüllt dabei auch die Ansprüche von professionellen Messtechnikern an die Leistungsfähigkeit. Dieser Scanner verschafft den Kunden den Vorteil, dass sie ihre Projekte schneller und mit größerer Genauigkeit abschließen können, wodurch die Kosten gesenkt werden und gleichzeitig 200 % bis 300 % mehr Arbeit ohne Qualitätseinbußen bewältigt werden kann.
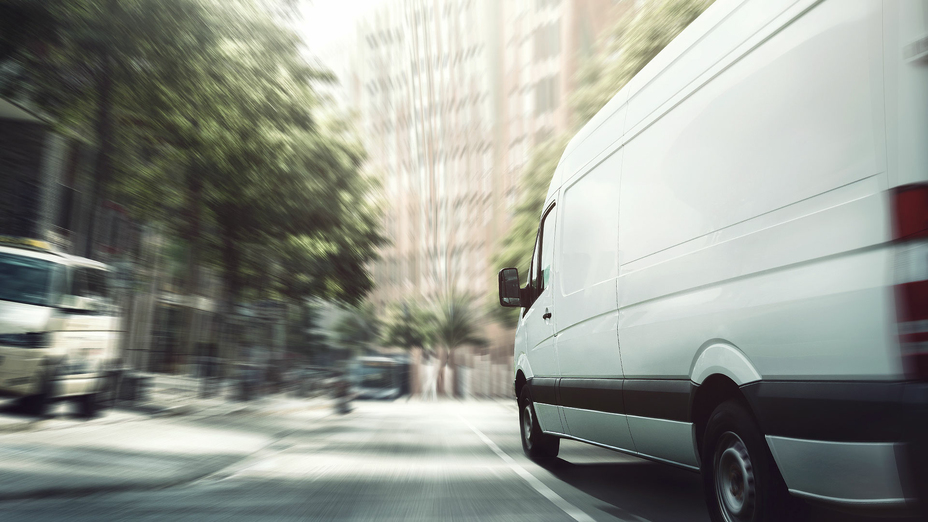
Als der mit Kindern und ihren Eltern besetzte Minivan um die Ecke bog, warteten bereits die beiden bewaffneten Angreifer. Sie traten hinter geparkten Autos hervor, legten ihre AK-103 aus und eröffneten das Feuer, wobei sie das sich schnell nähernde Fahrzeug mit drei bis vier kontrollierten Schüssen belegten.
Doch der Fahrer hielt nicht an. In Sekundenschnelle waren die Magazine der Bewaffneten leer und der von Kugeln durchlöcherte Minivan raste davon. Die Scheiben waren zwar versehrt, aber nicht zerborsten, alle Insassen im Inneren seelisch erschüttert, aber körperlich unverletzt.
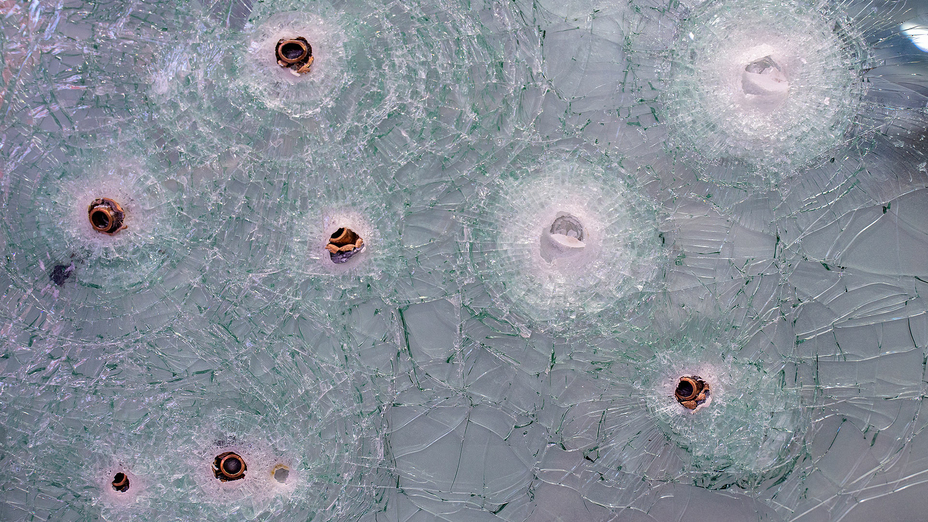
Kugelsicheres Glas
Gepanzerte Fahrzeuge: nicht nur für Päpste und Präsidenten
Auf der ganzen Welt, von der Ukraine bis zum Nahen Osten, war der Bedarf an gepanzerten Fahrzeugen noch nie so groß wie heute. Nicht nur für Militärs, Regierungen und Superreiche, sondern auch für humanitäre Organisationen und Gruppen sind Panzerungen gefragt, um Passagiere sicher durch die gefährlichsten Gebiete zu transportieren.
Die hochwertigsten dieser kugelsicheren Fahrzeuge sind diskret mit verschiedenen Verbundwerkstoffen, Stählen und Keramiken gepanzert. Mit solch einer Ausstattung können eine Reihe von ballistischen Bedrohungen aufhalten werden, von Kaliber .22 bis .50, je nach der für jedes einzelne Fahrzeug gewählten Panzerungsstufe.
Das Ziel ist es, maximalen Schutz bei minimalem Gewicht zu erreichen.
Die Panzerung können Sie sich wie einen maßgeschneiderten Anzug für ein Fahrzeug, der allerdings von innen getragen wird, vorstellen. Und dieser Anzug muss aus mehreren Gründen so gut wie möglich passen.
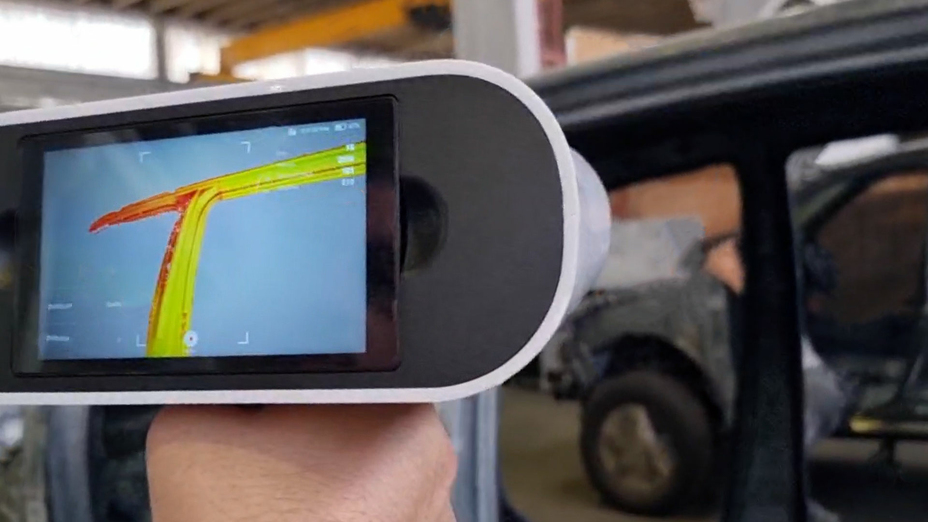
Artec Leo beim 3D-Scannen der Karosserie eines Toyota Hi-Lux 2022. Bild mit freundlicher Genehmigung von A.B. Engineering
Manchmal ist es erforderlich, OEM-Innenteile an ihren ursprünglichen Stellen wieder einzubauen, aus offensichtlichen Kostengründen mit nur minimalen Änderungen. Und falls erforderlich, muss das Fahrzeug etwa für eine (bewaffnete) Person an einem Kontrollpunkt unauffällig aussehen.
Wenn schließlich alles an seinem Platz ist, sollten die Insassen keinen Verlust an Freiraum spüren. Und schließlich sollte die Panzerung von außen nicht zu erkennen sein, so dass selbst gut geschulte Augen derart geschützte Autos, Lieferwagen und Busse nicht von normalen, nicht modifizierten Fahrzeugen unterscheiden können.
Solche „Stealth-Anforderungen“ werden von den Auftraggebern aufgabenspezifisch für jedes einzelne Fahrzeug gestellt, wobei die genauen Anforderungen festlegen, aus welcher Entfernung das Fahrzeug noch wie ein normales Fahrzeug aussehen soll. Diese Entfernungen können ab 50 Metern als Grenze reichen und bis hin zu einer Panzerung, die dem Betrachter auch dann nicht offensichtlich erkennbar ist, wenn er direkt neben dem Fahrzeug steht.
Um eine solche Herausforderung zu meistern, muss das Fahrzeug zunächst bis auf seine Grundstruktur und seine Elemente zerlegt und von dort aus jeder einzelne Quadratmillimeter so genau wie möglich vermessen werden.
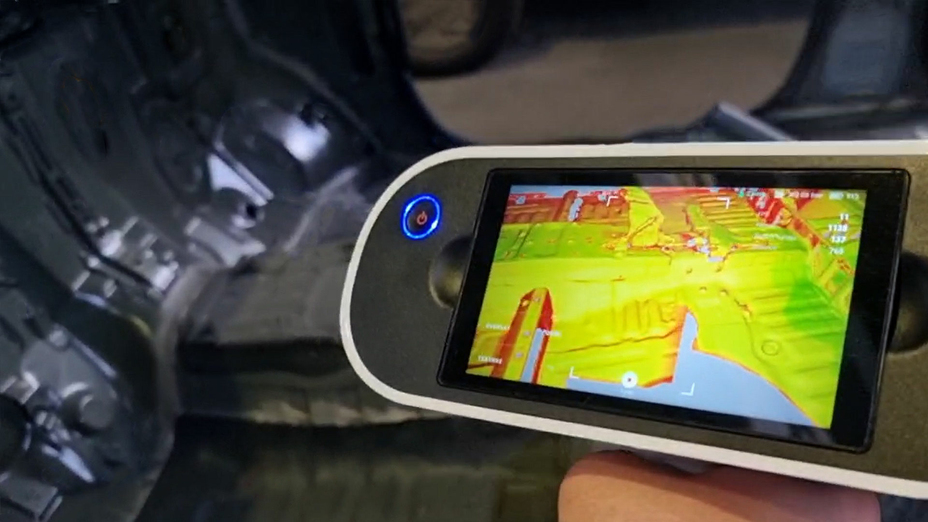
Artec Leo beim 3D-Scannen der Karosserie eines Toyota Hi-Lux. Bild mit freundlicher Genehmigung von A.B. Engineering
In den folgenden Phasen können dann alle maßgeschneiderten Panzerungselemente in CAD entworfen und unter strengen Bedingungen hergestellt werden, so dass nach dem Einbau und der Wiederanbringung der Originalteile nur wenige oder gar keine Lücken zwischen der Panzerung, den Türen und anderen potenziell gefährdeten Teilen des Fahrzeugs bestehen.
Wenn dies nicht möglich ist, wird eine neue, maßgeschneiderte Innenverkleidung angefertigt, die die OEM-Innenverkleidung makellos nachahmt, jedoch mehr Platz für die Panzerung bietet.
Dieser Prozess kann von ein bis zwei Monaten für ein kleines Fahrzeug wie einen Toyota J79 bis zu mehr als 4 Monaten für einen großen, komplexen Geländewagen, etwa einen Chevy Suburban, dauern.
Entwicklung von Fahrzeugpanzerung durch 3D-Scannen
Ein Spezialist für Fahrzeugpanzerungen mit einem wohlverdienten Ruf in der Branche ist die israelische A.B. Engineering Ltd., ein Maschinenbauunternehmen, das seit 2012 mit führenden Luft- und Raumfahrt- sowie Verteidigungsunternehmen zusammenarbeitet. Die Grundlage ihres umfassenden Arbeitsablaufs bei der Panzerung ist das 3D-Scannen.
Der Gründer und CEO des Unternehmens, Irakly (Ika) Baitish, erklärt: „Wenn es darum geht, ein Fahrzeug so zu panzern, dass die Insassen maximal geschützt sind und darüber hinaus auch der Motor, der Antriebsstrang und andere wichtige Teile, die das Fahrzeug in Bewegung halten, damit es aus der Gefahrenzone entkommen kann, ist es absolut wichtig, mit präzisen Messungen zu beginnen.“
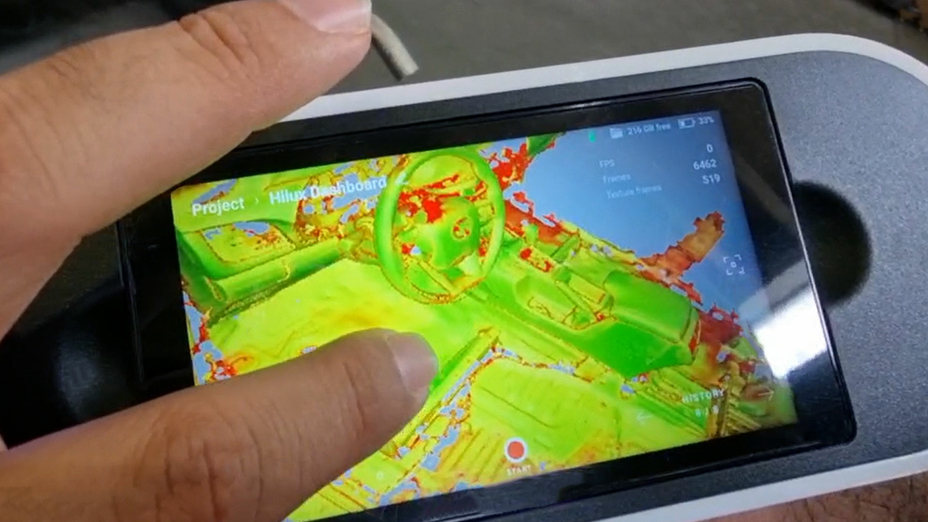
Überprüfung eines 3D-Scans des Hi-Lux auf dem Touchscreen-Display von Leo. Bild mit freundlicher Genehmigung von A.B. Engineering
Er fährt fort: „Deshalb haben wir uns für das 3D-Scannen als Messmedium entschieden, zumal wir damit die exakten Abmessungen des gesamten Fahrzeugs ermitteln können, einschließlich der Bereiche, die normalerweise schwierig manuell zu messen sind – wie etwa die Feuerwand, der Bereich, der den Fahrer vom Motorraum trennt.“
Nach der Verarbeitung der 3D-Scans des Fahrzeugs exportieren die Spezialisten die Scans in ihr CAD-System, Dassault Systemes CATIA V5.
Dort werden die Scans als Referenzmodelle für die Konstruktion der bald herzustellenden ballistischen Platten und anderer Panzerungskomponenten verwendet und dann virtuell in das Fahrzeug eingebaut, um sicherzustellen, dass das Endergebnis nach dem Einbau der Panzerung in den kommenden Wochen einen nahtlosen, lückenlosen Schutz von Stoßstange zu Stoßstange bietet.
Die Suche nach dem richtigen 3D-Scanner
Aber nicht alle 3D-Scanner sind gleich. Zunächst verwendeten Ika und sein Team für ihre Arbeit einen bekannten, hochwertigen tragbaren 3D-Scanner, der jedoch eine große Anzahl von Zielobjekten und große Mengen an Spray sowie einen Laptop, einige Kabel und eine 220-Volt-Stromversorgung benötigte.
Ein Beispiel für ein typisches Projekt war das Scannen des zerlegten Fahrerhauses und des Fahrgestells eines Skoda Kodiaq, der gepanzert werden sollte.
Nach dem Aufbringen von mehr als 3.000 Aufklebern und den erforderlichen Sprühmengen dauerte das Scannen ganze zwei Wochen, und die resultierenden Daten waren nicht annähernd so sauber, wie es benötigt wurde.
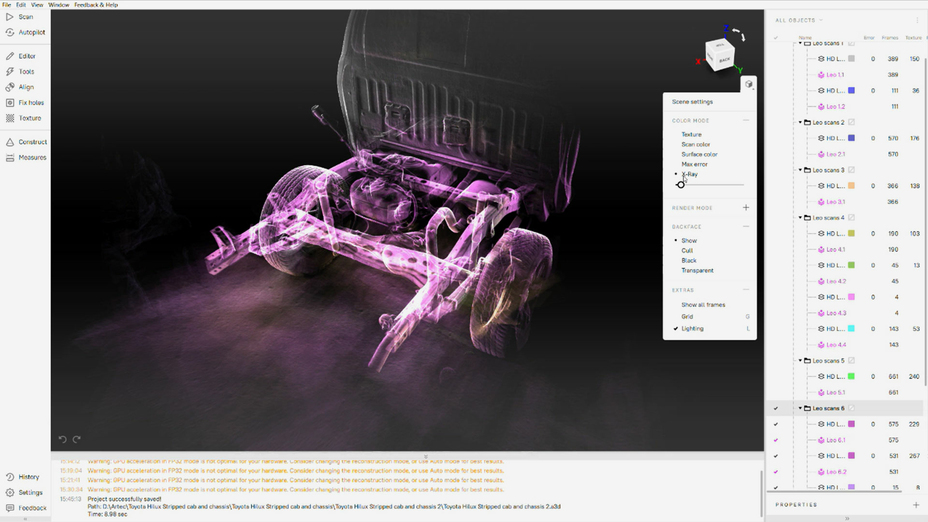
Bildschirmfoto von Artec Studio: Röntgenansicht des Leo Scans von der Rückseite des Hi-Lux. Bild mit freundlicher Genehmigung von A.B. Engineering
Bevor die Scans zusammengefügt waren und ein hochpräzises 3D-Modell für CAD erstellt werden konnte, folgte eine weitere Arbeitswoche für die Bereinigung der Daten und manuelle Nachmessungen.
Einer der Teamkollegen (vermutlich derjenige, der den kürzesten Strohhalm gezogen hatte) war dafür verantwortlich, die über 3.000 Zielmarken vom Fahrzeug abzuziehen und es anschließend zu reinigen. Leider hinterließen einige der Aufkleber Rückstände auf den Innenverkleidungen, die dadurch unbrauchbar wurden.
Angesichts des hohen Zeit- und Arbeitsaufwands wurde Ika klar, dass der vorhandene 3D-Scanner sein Team ernsthaft ausbremste.
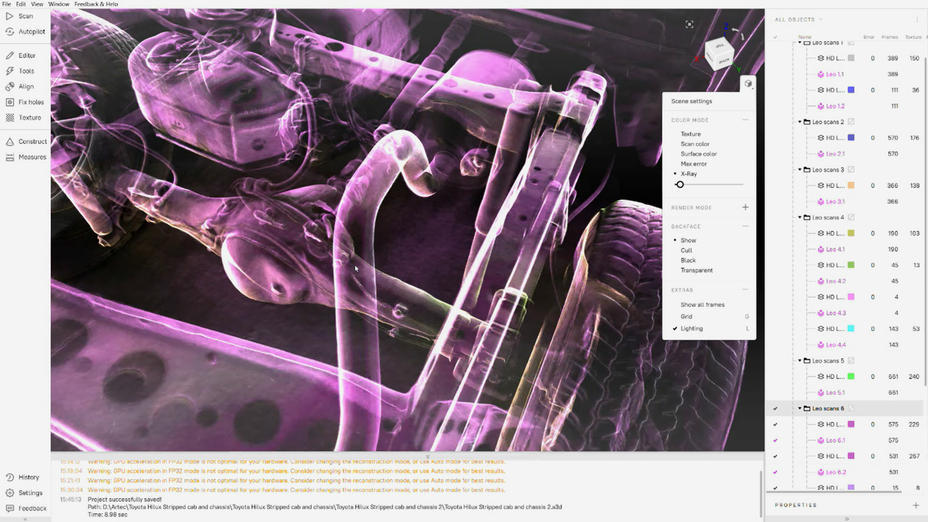
Bildschirmfoto von Artec Studio: Röntgenansicht des Leo Scans von der Rückseite des Hi-Lux. Bild mit freundlicher Genehmigung von A.B. Engineering
In einer Branche, in der die Projektfristen nicht flexibel sind, kann jeder Tag und jede Stunde einen Unterschied ausmachen. Sobald das Projekt abgeschlossen war, begann Ika mit der Suche nach einem besseren 3D-Scanner.
Abschied von wochenlangem Scannen, Bekleben und Sprühen
Bald fand er die Website von Artec 3D und konzentrierte sich auf den Artec Leo, einen professionellen tragbaren 3D-Scanner, der seit Jahren ein Branchenliebling für Reverse Engineering, Forensik, Gesundheitswesen und viele andere Anwendungen ist.
Leo liefert hochauflösende 3D-Farbscans mit Submillimeter-Genauigkeit und verfügt über ein Touchscreen-Display und einen eingebauten Akku, wodurch er zu 100 % tragbar ist und eine hohe FPS-Erfassungsrate sowie ein großes Scan-Sichtfeld bietet.
Scannen eines Toyota Hi-Lux aus dem Jahr 2022 nun schneller als je zuvor
Ein Beispiel dafür, wie sich der Arbeitsablauf bei A.B. Engineering seit der Einführung von Leo verbessert hat, ist das Scannen des zerlegten Fahrerhauses und des Fahrgestells eines viertürigen Toyota Hi-Lux aus dem Jahr 2022, das für eines der jüngsten Panzerungsprojekte benötigt wurde.
Mit Leo in der Hand machten sich Ika und sein Team an die Arbeit und erfassten den Toyota. Nur zwei Stunden später waren sie mit dem Scannen fertig, ohne auch nur eine einziges Zielmarke oder Spray auftragen zu müssen.
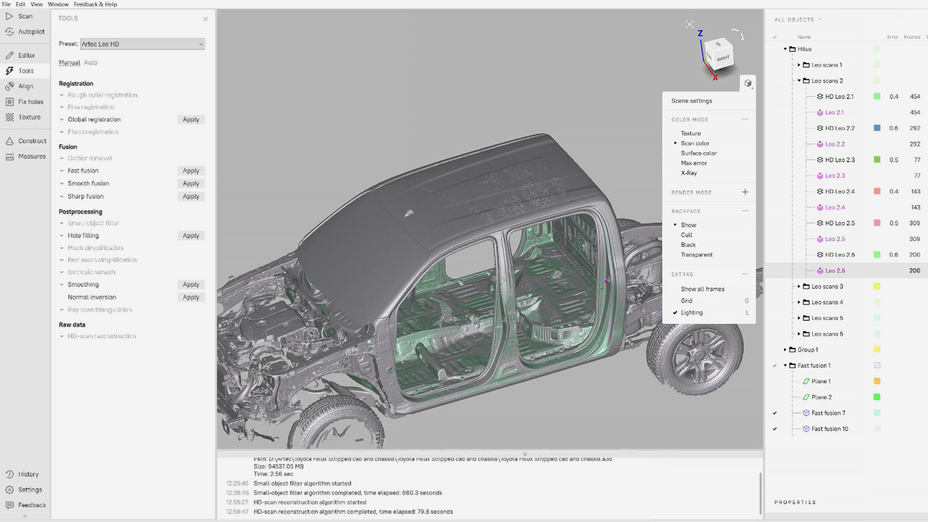
Bildschirmfotos von Artec Studio: kombinierte Leo Scans des Hi-Lux. Bild mit freundlicher Genehmigung von A.B. Engineering
Die Verarbeitung der Scans und die Erstellung der STL-Dateien, die an das CAD-System gesendet worden waren, um die Panzerung für den Hi-Lux zu entwerfen, dauerte in der Software Artec Studio nur fünf Stunden.
Verglichen mit dem alten Scanner, mit dem eine Woche für das Scannen und eine weitere Woche für die Scanverarbeitung benötigt wurden, um fast die gleichen Ergebnisse zu erzielen, jedoch mit deutlich geringerer Qualität, war der Kontrast erstaunlich.
In Ikas Worten: „Wenn wir zurückblicken, wie es früher war, bietet uns Leo einen unglaublichen Geschwindigkeitsunterschied. Und die Daten, die wir mit Leo erhalten, sind viel sauberer, ohne jegliche Probleme bei der Ausrichtung.“
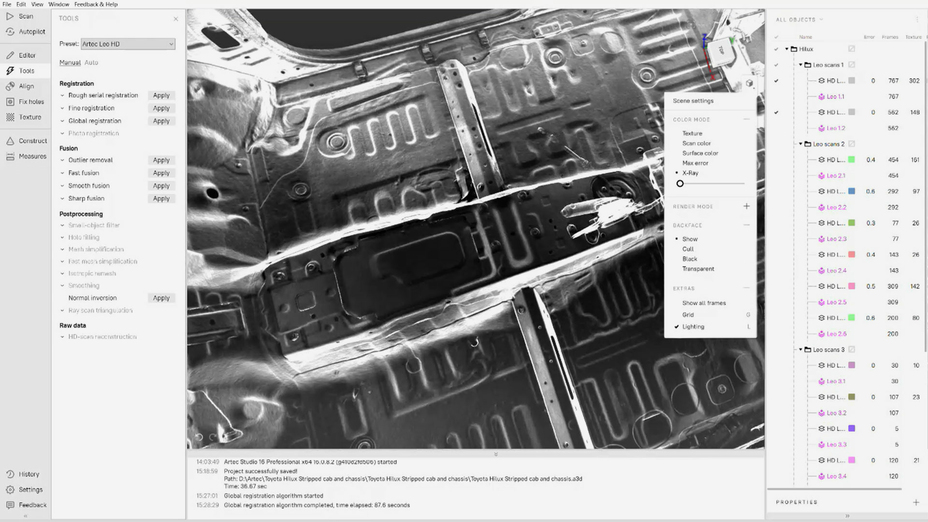
Bildschirmfoto von Artec Studio: Röntgenansicht des Leo Scans des Innenraums des Hi-Lux. Bild mit freundlicher Genehmigung von A.B. Engineering
Er fährt fort: „Unser Messprozess hat sich sowohl in Bezug auf die Zeit als auch auf die Qualität erheblich verbessert. Leo hat die Qualität unseres technischen Outputs dramatisch verändert und ermöglicht, die paar Prozent mehr zu erreichen, die nötig sind, um ballistische Lücken zu schließen, was buchstäblich Leben retten kann.“
„Jedes einzelne Fahrzeug erfordert einen individuellen Ansatz“
Für jedes Fahrzeug, das sie panzern, beraten sich Ika und sein Team mit dem Kunden und berücksichtigen dabei den Grad des benötigten ballistischen Schutzes, die beabsichtigte Nutzung des Fahrzeugs sowie die Erwartungen in Bezug auf den Zeitrahmen und die erforderlichen sekundären Fahrzeug-Upgrades.
Wenn man letzteres berücksichtigt, kann eine typische Panzerung das Gesamtgewicht eines Fahrzeugs leicht um 500-2.000 Pfund (230-900 kg) erhöhen. Um eine derartige Gewichtszunahme zu bewältigen, werden gelegentlich spezielle, besonders leistungsstarke Bremsen, Achsen, Getriebe und Antriebsstränge benötigt.
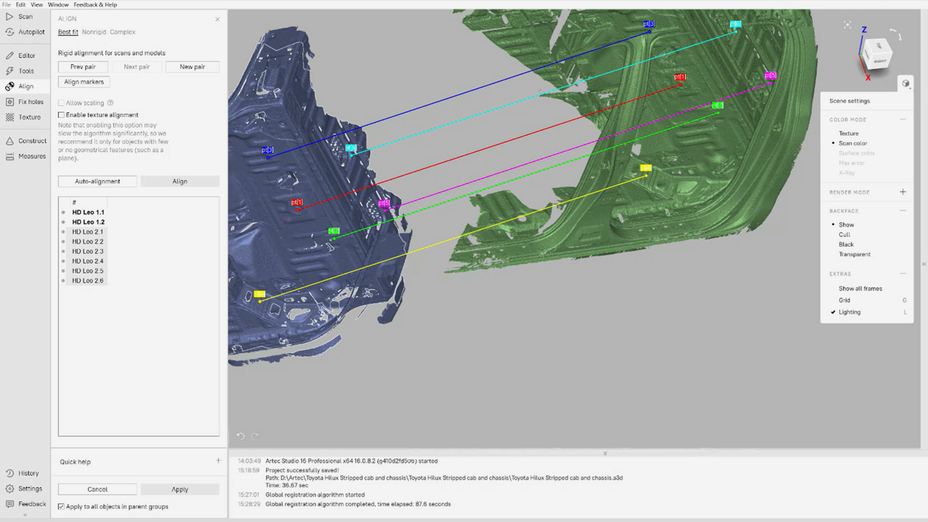
Einfaches Ausrichten der Leo Scans vom Hi-Lux in Artec Studio. Bild mit freundlicher Genehmigung von A.B. Engineering
„Da diese Aufrüstung des Fahrzeugs eine Menge zusätzliches Gewicht mit sich bringt“, so Ika, „erhöht sich der Druck auf uns, die Panzerung so zu optimieren, dass sie das geringste Gewicht mit dem höchsten Grad an Verteidigungsdeckung verbindet.“
Er fährt fort: „Jetzt, wo wir Leo haben, ist es viel schneller und einfacher, ein solches Spitzenergebnis zu erzielen.“
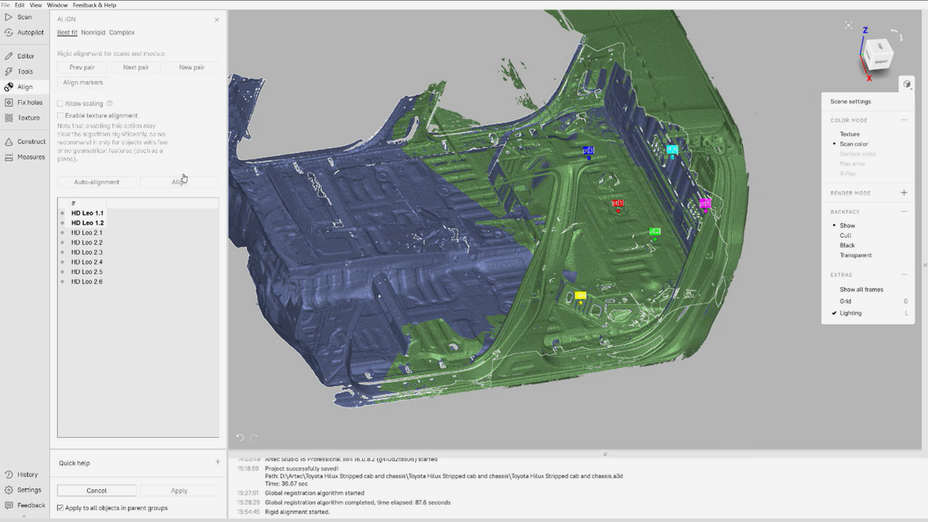
Mit nur wenigen Klicks sind die Scans des Hi-Lux in Artec Studio ausgerichtet. Bild mit freundlicher Genehmigung von A.B. Engineering
Testen der getanen Arbeit auf dem Schießplatz
Ika und sein Team stehen voll und ganz hinter ihrer Arbeit, unabhängig von der Größe oder Komplexität des Projekts, und dank Leo können sie dies umso selbstbewusster tun. Eine kürzliche stattgefundene Vorführung der Qualität ihrer Panzerung spricht für sich selbst.
Eines der ausgestatteten Fahrzeuge, ein schwerer gepanzerter Lkw, wurde auf einer Schießanlage getestet, wobei mehr als 800 Schüsse aller Kaliber (bis hin zu .50) aus einer Vielzahl von Waffen auf das Fahrzeug abgefeuert wurden, ohne es dabei zu durchdringen zu können.
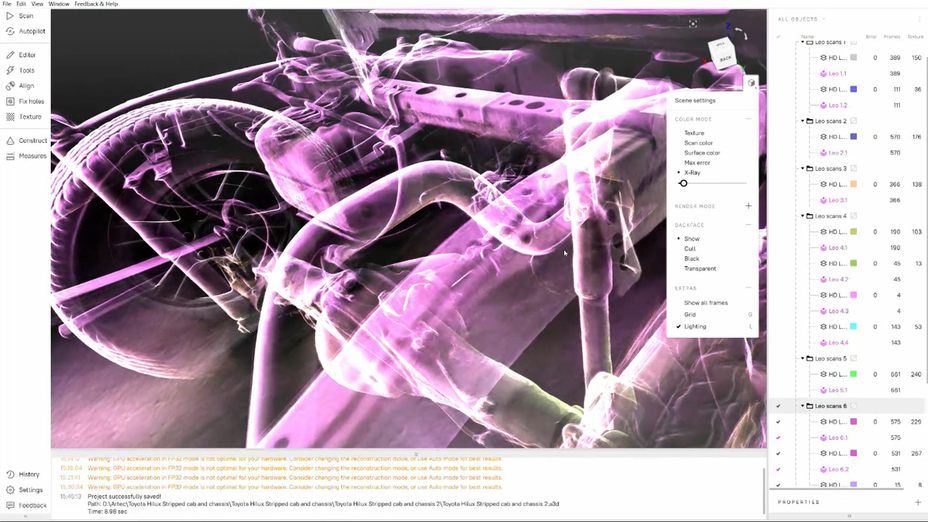
Röntgenansicht in Artec Studio auf die Leo-Scans der Rückseite des Hi-Lux. Bild mit freundlicher Genehmigung von A.B. Engineering
Ein anderes gepanzertes Fahrzeug, das von einem konkurrierenden Unternehmen stammt, wurde einem ähnlichen Sperrfeuer von Kugeln aus denselben Waffen ausgesetzt. Es erlitt Hunderte von Einschüssen, die weit über den Punkt hinausgingen, an dem die Insassen in einem realen Szenario noch eine Überlebenschance gehabt hätten.
Wer Leo hat, wird reisen können: Panzerung von Autos, Lastwagen, Bussen und Flugzeugen
Das Team aus erfahrenen Ingenieuren und Techniker bei A.B. Engineering führt seit Jahren ein breites Spektrum an Panzerungsprojekten durch, von einfach bis komplex, für eine Vielzahl von Fahrzeugen, Flugzeugen und anderen Objekten.
„Da Leo einfach mitgenommen werden kann, steigen wir einfach in ein Flugzeug und fliegen dorthin, wo unser nächstes Projekt uns hinführt. Wenn wir ankommen, wissen wir, dass wir schneller fertig werden als je zuvor, und dass alle Daten gespeichert, sauber und einsatzbereit auf der SD-Karte von Leo landen“, so Ika.
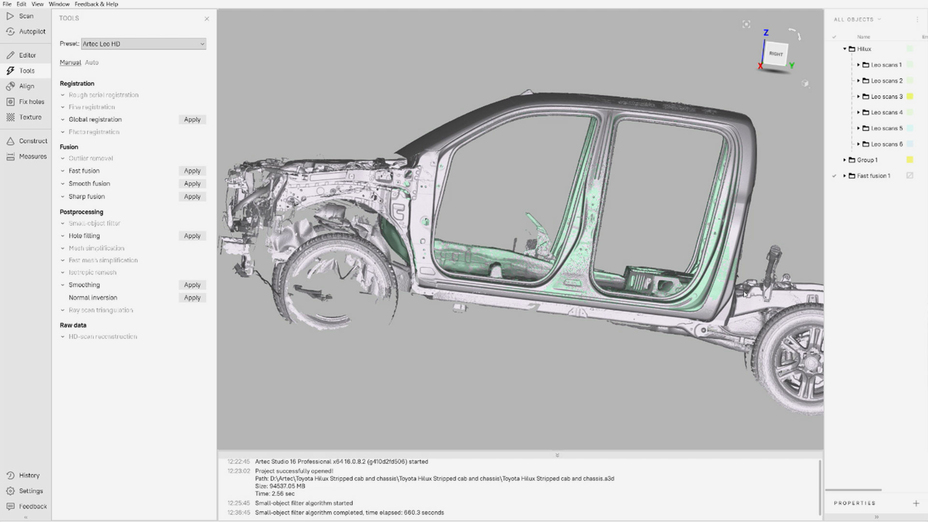
Bereit für CAD: Bildschirmfoto von Artec Studio mit den kombinierten Leo Scans des Hi-Lux. Bild mit freundlicher Genehmigung von A.B. Engineering
Er fährt fort: „Allein die Möglichkeit, nur den Scanner und nicht einmal einen Laptop überall auf der Welt mitzunehmen, ist ein riesiger Vorteil. Und die Möglichkeit, ohne Zielmarken zu scannen, ist ein weiterer großer Vorteil, da wir das zu scannende Objekt nicht präparieren müssen. Das bedeutet auch, dass wir durch den Scanvorgang keinerlei Spuren hinterlassen werden, was manchmal entscheidend sein kann.“
Ein stetiger Strom von Kunden und Empfehlungen – das ganze Jahr über
Aus geschäftlicher Sicht hat Leo Ika und sein Team in die Lage versetzt, weitaus wettbewerbsfähiger zu sein. Mit Leo benötigen sie mittlerweile für jedes Projekt, das 3D-Scannen beinhaltet, 2 Wochen weniger Entwicklungszeit als zuvor. Dadurch kann das Unternehmen gesunkene Kosten direkt an seine Kunden weitergeben, was über das ganze Jahr zu einem stetigen Zustrom von Kunden und Empfehlungen führt.
Ika erklärt: „Bevor wir Leo eingeführt hatten, machte das 3D-Scannen aufgrund des hohen Zeitaufwands 20-30 % der Gesamtkosten für den Kunden aus. Aber mit Leo macht das Scannen nur noch 5 bis 10 Prozent der Projektkosten aus. In manchen Fällen können wir also 20 Prozent weniger verlangen als ein Mitbewerber, der einen weniger modernen 3D-Scanner, wie den, den wir früher hatten, verwenden.“
Scanners behind the story
Try out the world's leading handheld 3D scanners.