Bau eines Hellcat - angetriebenen 57er International Metro Van mit Artec Leo
Herausforderung:Erhebliche Beschleunigung und Vereinfachung des Prozesses zur Herstellung von Autoersatzteilen und -komponenten von Grund auf, ohne bei Qualität und Präzision Abstriche zu machen.
Lösung:Artec Leo, Artec Studio, Autodesk Alias, SOLIDWORKS
Ergebnis:Verkürzung des Zeitaufwands von Tagen auf nur wenige Stunden für die Umwandlung alter physischer Teile in brandneue CAD-Modelle, die für die Fertigung oder Prototyping geeignet sind. Als Referenz werden Scandaten aus Artec Leo verwendet.
Warum Artec?Leo bietet dem Unternehmen Scratch Build Gestaltungsmöglichkeiten, die keine andere Option bieten konnte. Da weniger Stunden für die Datenerfassung aufgewendet werden müssen, kann mehr Zeit für die CAD-Modellierung, den Entwurf und das Prototyping verwendet werden.
Hintergrund
Seit er fünf Jahre alt war, wusste Chad Forward, dass er Dinge bauen wollte. Nachdem er 15 Jahre lang in führenden Automobil-Designstudios in Australien und als Designberater für Autohäuser gearbeitet hatte, gründete er sein eigenes Restaurierungsunternehmen,Scratch Build Co, um weiterhin das zu tun, was er schon immer geliebt hatte: Autos bauen.
Das 2012 als Nebenprojekt gestartete Unternehmen, dem sich Forward an den Wochenenden widmete, ist heute ein vollwertiges Designstudio und ein Ort der Zusammenarbeit. Dort arbeiten Forward und seine Kollegen – Automobildesigner, Techniker und Elektriker – an der Entwicklung von Designlösungen für Hersteller von Aftermarket-Automobilprodukten oder individuell gefertigten Autos.
„Ich habe mich schon immer zu Menschen hingezogen gefühlt, die sich für das begeistern, was sie zu schaffen versuchen“, sagt Forward. „Nach der Beobachtung der unglaublichen Handwerker und großartigen Designer bei Toyota, Ford und anderen Designstudios sah ich die Möglichkeit, diese Leute zu beschäftigen und einen Raum zu schaffen, in dem jeder etwas zum Nutzen des australischen Automobilmarktes erschaffen kann.“
Wie der Name schon sagt, besteht ein Großteil der Arbeit von Forward darin, Dinge von Grund auf neu zu bauen, sei es ein Teil, das nicht mehr gekauft werden kann, oder ein ganzer Ablauf, den ein Kunde neu erfinden will. Bis 2017 nahm sein typischer Reverse-Engineering-Workflow sehr viel Zeit in Anspruch, ohne dass er Ergebnisse vorweisen konnte. „Manchmal brauchte ich einen ganzen Tag, um ein Chassis zu vermessen, die grundlegenden Maße zu ermitteln und dann zu versuchen, anhand dieser Informationen in CAD ein Modell zu erstellen“, so Forward. „Weil ich alles so schnell anging, übersah ich oft etwas, das ziemlich wichtig war. Außerdem musste ich einige Male hin- und hergehen.“
„Der hochmoderne und wahrhaft tragbare Scanner Leo von Artec ist ein enormer Durchbruch in der 3D-Scanbranche.“
Als Artec in diesem Jahr seinenkabellosen, tragbaren 3D-Scanner Artec Leoauf den Markt brachte, war Forward sofort mit an Bord. „Vor 20 Jahren, als ich mein erstes Geschäft für spezialgefertigte Autos führte, dachte ich noch, dass es diese Technologie zu meinen Lebzeiten niemals geben würde“, sagt er. Forward bestellte den Scanner über den australischen Artec VertriebspartnerObjective3Dvor und war nach Angaben des Teams der erste glückliche Kunde, der ihn seinerzeit erhalten durfte.
„Der hochmoderne und wirklich tragbare Scanner Leo von Artec ist ein enormer Durchbruch in der 3D-Scanbranche, und wir bei Objective3D sind stolz darauf, diese Technologie auf den australischen und neuseeländischen Markt zu bringen“, so Matt Minio, Geschäftsführer von Objective3D. „Diese Technologie ist vor allem für Automobilingenieure von Vorteil. Sie können damitTeile zurückentwickelnkönnen, um zu sehen, wie sie die Leistung eines Fahrzeugs beeinflussen."
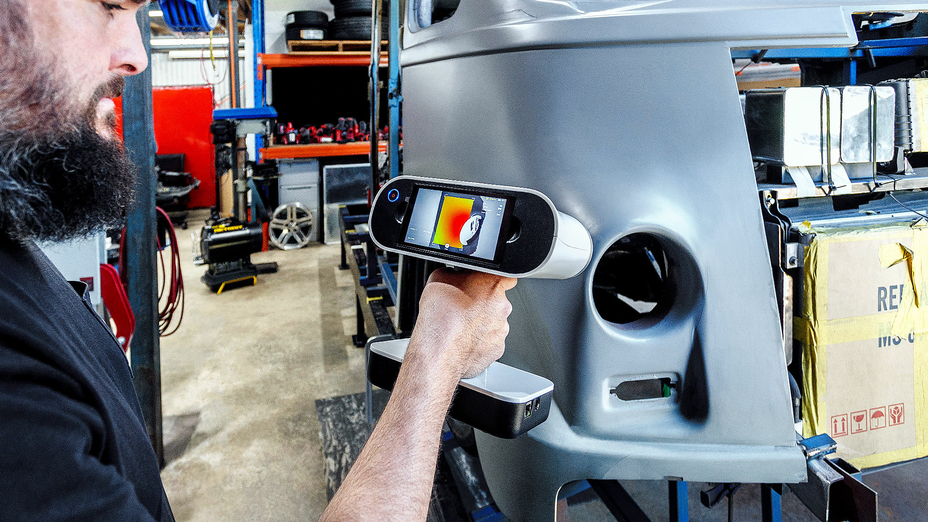
Mit dem Artec Leo kann der Gründer von Scratch Build jedes beliebige Teil einfach vermessen (Bildquelle: streetmachine.com.au)
Artec Leo ist ein leistungsfähiger und einzigartiger 3D-Scanner, der ohne PC oder Laptop auskommt und sowohl mobil als auch nutzerfreundlich ist. Dank seines großen Sichtfeldes kann der Scanner sowohl mittelgroße bis große Industrieteile als auch ganze Fahrzeuge mit garantierter Genauigkeit und außergewöhnlicher Auflösung in 3D erfassen.
Und dank der automatischen integrierten Verarbeitung, der drahtlosen Konnektivität, der integrierten Touchscreens und der Akkus bietet der Scanner volle Autonomie und Bewegungsfreiheit, wo auch immer sich der Nutzer befindet, sei es in einer Autowerkstatt, in einer Fabrikhalle oder an einem weit entfernten Ort ohne verfügbareStromquelle.
Für Forward war es eine klare Sache: „Ich habe vier Jahre gebraucht, um mich davon zu überzeugen, dass ich 4.000 Dollar für einen 3D-Drucker ausgeben muss, aber nur 15 Minuten, um mich davon zu überzeugen, einen 40.000-Dollar-Scanner zu kaufen."
An die Arbeit
Als der Scanner eintraf, machte sich Forward sofort an die Arbeit und hat seitdem nicht mehr damit aufgehört: Alles, was am Auto vermessen werden muss, wird nun, vor Ort in der Werkstatt oder auf dem Feld, mit Leo gescannt, was ihm und seinen Kunden wertvolle Zeit spart. Diese freie Zeit verbringt er nun mit CAD-Modellierung, Design und Prototyping von Autoteilen und -komponenten, wobei er die gescannten Daten als Referenz verwendet.
„Die Freiheit, die mir dieses einzige Gerät bietet, ist unglaublich. Unabhängig von der Lage oder der Komplexität der Teile kann ich jetzt die Daten ganz einfach erfassen“, fügt Forward hinzu.
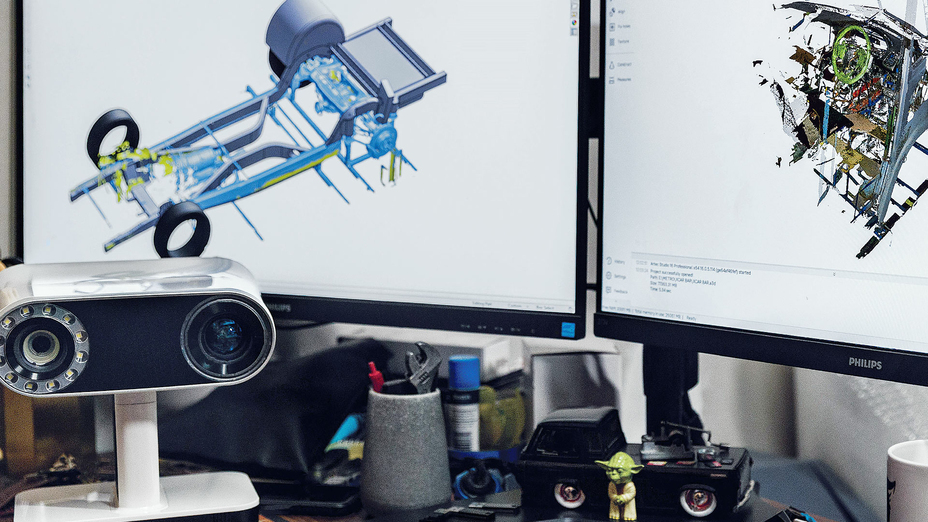
Forward verwendet Daten von Leo als Referenz für die CAD-Modellierung in SOLIDWORKS und Autodesk Alias (Bildquelle: streetmachine.com.au)
Der typische Arbeitsablauf sieht wie folgt aus: Forward oder einer seiner Konstruktionskollegen fährt zum Kunden und scannt alles, was gescannt werden muss. Anschließend werden sämtliche Daten auf einen seiner Desktop-Computer, der ausschließlich für die Verarbeitung inArtec Studioeingerichtet ist, übertragen.
„Ich habe zwei Desktop-Computer: einen für die Verarbeitung aller gescannten Daten und den zweiten für die CAD-Modellierung. Da ich immer etwas zu tun habe, ziehe ich es vor, beide parallel laufen zu lassen“, erklärt Forward. Je nach gescanntem Teil lädt er es dann entweder in SOLIDWORKS oder Autodesk Alias, um ein solides CAD-Modell zu erstellen.
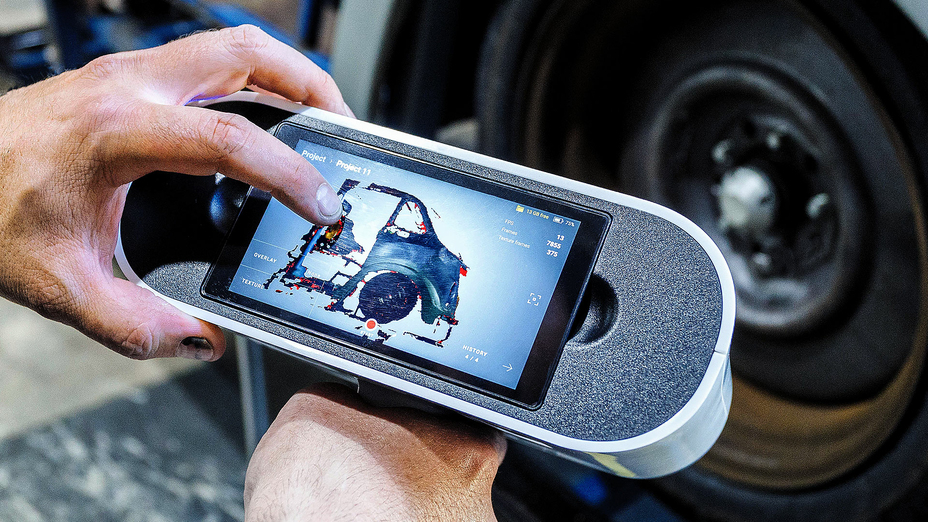
Das in Artec Leo integrierte Display ermöglicht es Forward, die Ergebnisse seines Scans in Echtzeit zu betrachten (Bildquelle: streetmachine.com.au)
Die Verwendung eines 3D-Scanners bei den Kunden eröffnete Forward auch neue Arbeitsmöglichkeiten: „Jedes Mal, wenn ich mit Leo irgendwohin fahre, kann ich fast sicher sein, dass ich einen weiteren Auftrag bekomme, nur weil ich einen Ort besucht habe. Ein Ort führt mich zu einem anderen Ort und so weiter“, erzählt er. Während Forward also vor Ort ist, sammelt er auch immer mehr Daten als nötig – er erstellt eine Art Katalog und sammelt wertvolle Daten von Teilen, die nicht mehr verfügbar sind.
Der International Metro Van von 1957
Eines der größten Projekte, bei denen Forward den Scanner bisher in vollem Umfang nutzen konnte, ist der 1957er International Metro Step Van, den er und sein Geschäftspartner aus einer anderen Kfz-Werkstatt, Luke Williams, bis Ende 2023 von Grund auf restaurieren wollen.
Der Besitzer des Lieferwagens wollte das Fahrzeug nicht einfach in seinem jetzigen Zustand restaurieren, sondern auch mit der Leistung eines Sportwagens zu kombinieren, nicht zuletzt durch Einbau eines 6,2-Liter-HEMI-Hellcat-V8-Kompressormotors.
Der V8-Motor ist serienmäßig in den Dodge Challenger SRT® Hellcat-Modellen, den leistungsstärksten modernen amerikanischen Muscle-Cars, eingebaut und leistet mehr als 700 PS, was es dem Besitzer im Unterschied zum Originalmotor des Vans ermöglicht, seinen Van im ganzen Land frei zu fahren. Abgesehen vom Motor wollte Forward auch das Design optimieren, damit der Van weniger „aufgeblasen“ aussieht, aber dabei die gesamte Werkselektronik beibehalten.
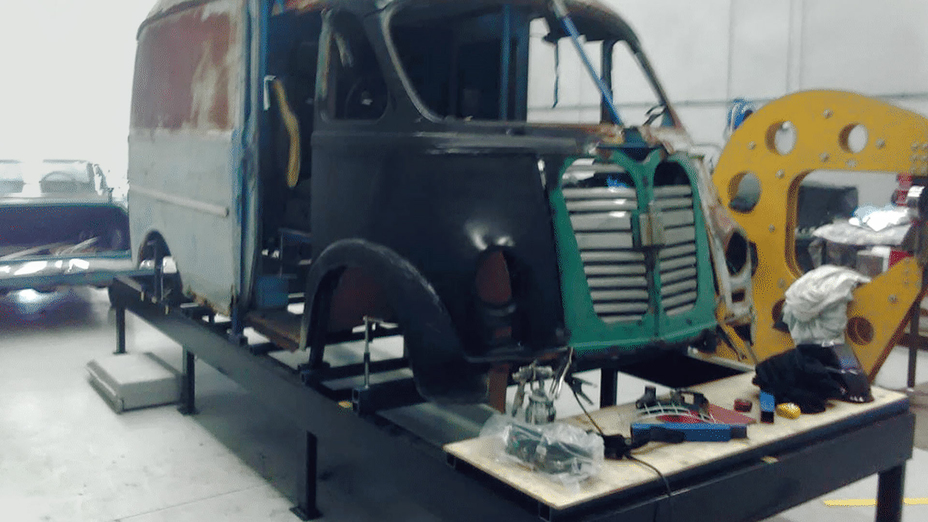
Die ursprüngliche Karosserie des 1957er Metro Van vor der Restaurierung (Bild von Chad Forward)
Nachdem sie die Design- und Konstruktionsanforderungen des Eigentümers erhalten und einige vorläufige Skizzen angefertigt hatten, schmiedeten Forward und Williams einen Plan: Da die Karosserie des Lieferwagens zu abgenutzt und rostig war, um sie zu restaurieren, wäre es schneller, das gesamte Fahrzeug von Grund auf neu zu bauen und die Scans der alten und modifizierten Teile als Grundlage für die Modellierung neuer Teile in CAD zu verwenden.
Schritt 1. Modellieren der Karosserie
Der erste Schritt war das Zuschneiden und Modellieren der Karosserie. Der Plan sah vor, einen vorhandenen Rumpf – oder eines seiner Teile – in die gewünschte Form zu bringen, dann diesen Teil in 3D zu scannen und die Daten als Ausgangspunkt für die Modellierung eines ganzen Rumpfes in CAD zu verwenden.
Darüber hinaus zerschnitt Williams eine Werkskarosserie mit einem Winkelschleifer, schweißte sie in leicht veränderten Positionen wieder zusammen und verwendete dann eine Menge Spachtelmasse und Grundierung, um eine matte Oberfläche zu erzeugen, mit der er zufrieden sein konnte.
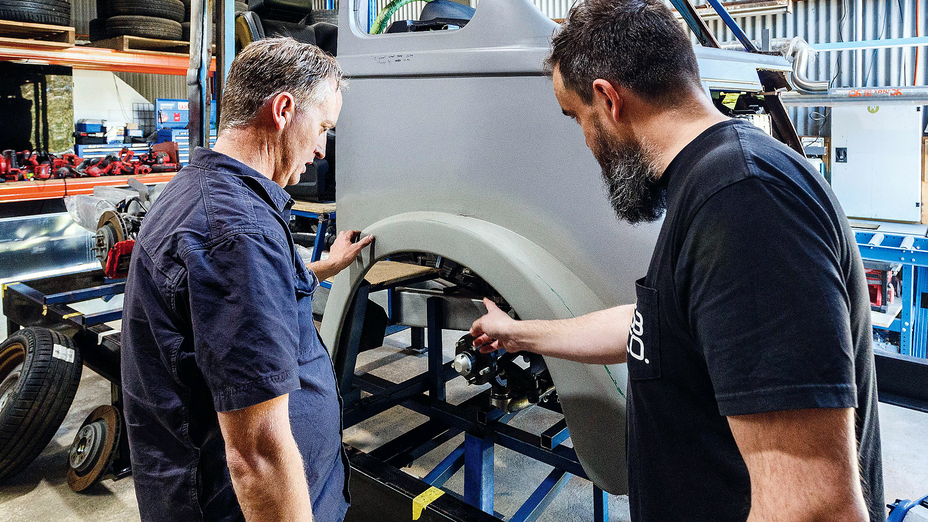
Der Plan war, einen der Rümpfe in die gewünschte Form zu bringen und dieses Teil dann in 3D zu scannen, um einen ganzen Rumpf in CAD zu modellieren (Bildquelle: streetmachine.com.au)
Schritt 2. Bau des Fahrgestells
In der Zwischenzeit stellte Forward sämtliche Komponenten des Antriebsstrangs des Dodge Hellcat – den Motor, die gesamte Verkabelung, die vordere und hintere Aufhängung – auf einer Basisplattform auf, die er um das Fahrgestell herum baute. Er wollte sehen, wie alle Komponenten zusammenpassen, ob sie den ADR-Standards (Australian Design Rules) entsprechen, und sie scannen, um zu verstehen, welche neuen Fahrwerksteile in CAD modelliert werden mussten.
Schritt 3. 3D-Scannen
Dann war es an der Zeit, dass Forward die grundierte vordere linke Ecke des Lieferwagens sowie das Fahrgestell und andere interne Komponenten mit seinem Artec Leo scannte. Das Scannen dauerte nur ein paar Minuten. Anschließend lud er alle Daten in Artec Studio hoch, um sie zu bearbeiten und eine STL-Datei zu erstellen.
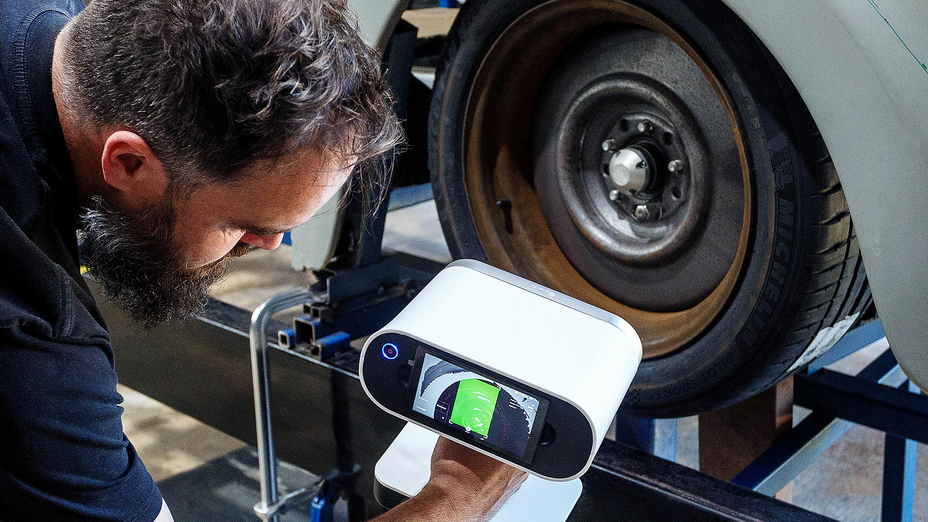
Scannen des Transporters mit Artec Leo (Bildquelle: streetmachine.com.au)
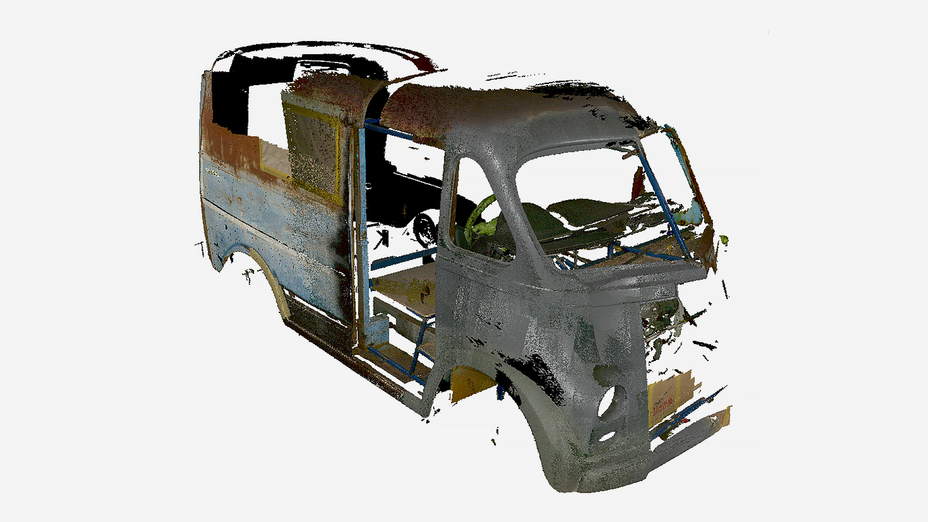
3D-Scan eines modifizierten Rumpfs, aufgenommen mit Artec Leo
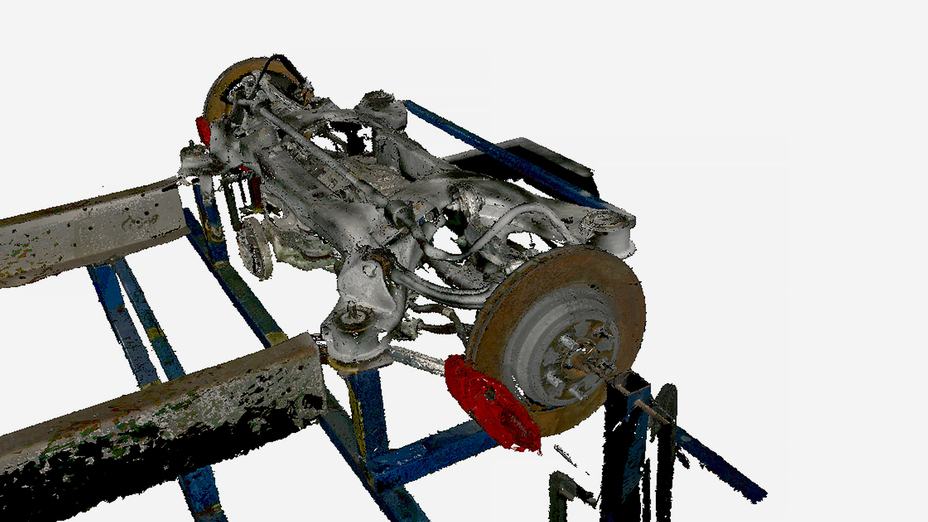
3D-Scan einer Hinterradaufhängung
Schritt 4. Modellieren der Karosserie des Transporters
Anschließend an der Reihe: Die Modellierung der Karosserieoberfläche. Dazu importierte Forward die Scandaten aus Artec Studio in Autodesk Alias, eine Software für computergestütztes Industriedesign für den Fahrzeugaußenbereich, und verwendete diese Daten als Blaupause für die Erstellung von Skizzen einer zukünftigen Karosserieoberfläche.
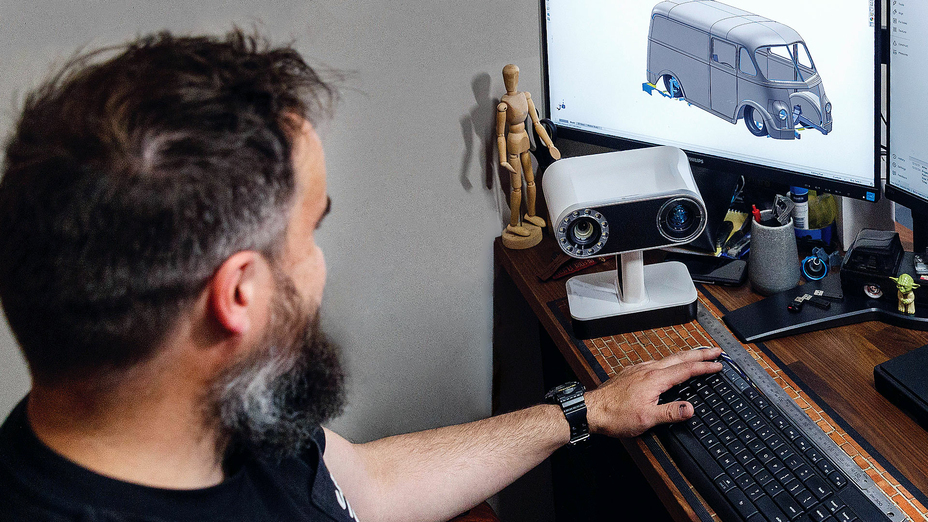
Forward verwendet die Software Autodesk Alias, um aus den Skizzen, die er über den gescannten Daten anfertigt, Karosserieoberflächen zu erstellen (Bild: streetmachine.com.au)
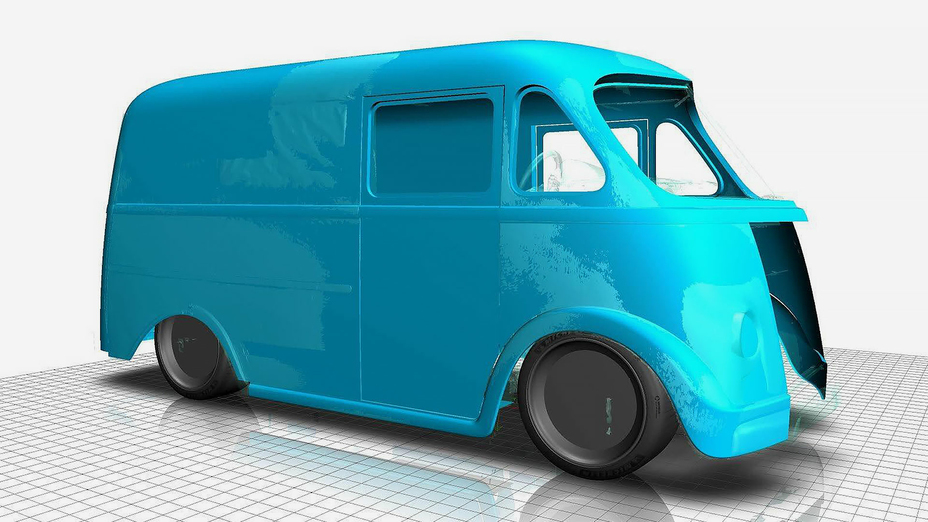
3D-Scan (hellblau) und CAD-Daten (blau) in der Software Alias
Schritt 5. Modellierung des Fahrgestells
Für die Modellierung des Fahrgestells und aller anderen technischen Teile verwendet Forward SOLIDWORKS. Nach dem immer gleichen Arbeitsablauf lud er die mit Leo erfassten Scandaten in SW hoch und modellierte um sie herum die neuen Teile. Dank der genauen 3D-Replikate der internen Komponenten kann Forward sie während seines Konstruktionsprozesses als präzise Referenzen verwenden und erhält außerdem ein besseres Verständnis für mögliche Probleme, auf die er stoßen könnte. Je weiter er mit seinem Entwurf fortschreitet, desto mehr Komponenten scannt er ein und fügt sie der Software als Referenzmodelle hinzu.
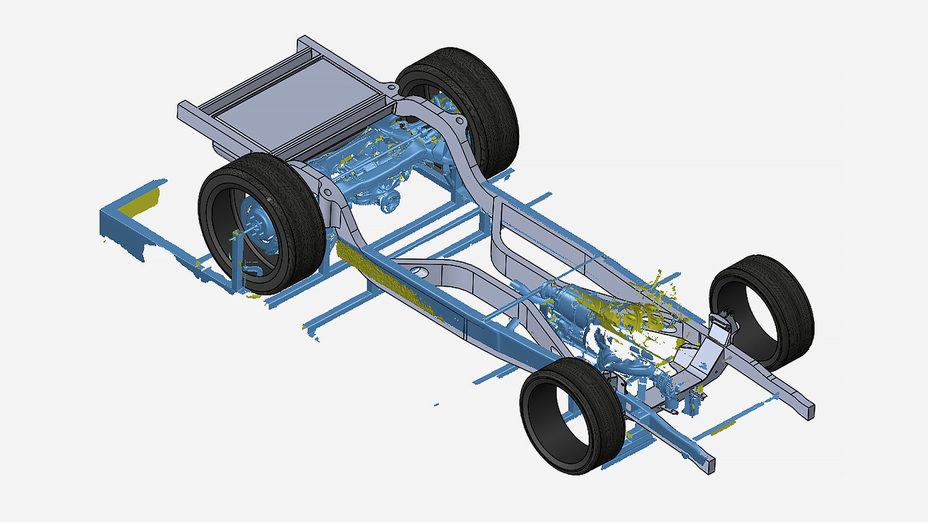
Forward verwendet den Scan des zu modellierenden Fahrgestells als Grundlage für die Erstellung eines CAD-Modells in SOLIDWORKS
Schritt 6. Laserschneiden und Schweißen der neuen Komponenten
Nach der SOLIDWORKS-Phase schickte Forward sämtliche CAD-Komponenten zum Laserschneiden und anschließend zum Schweißen an das Fahrgestell.
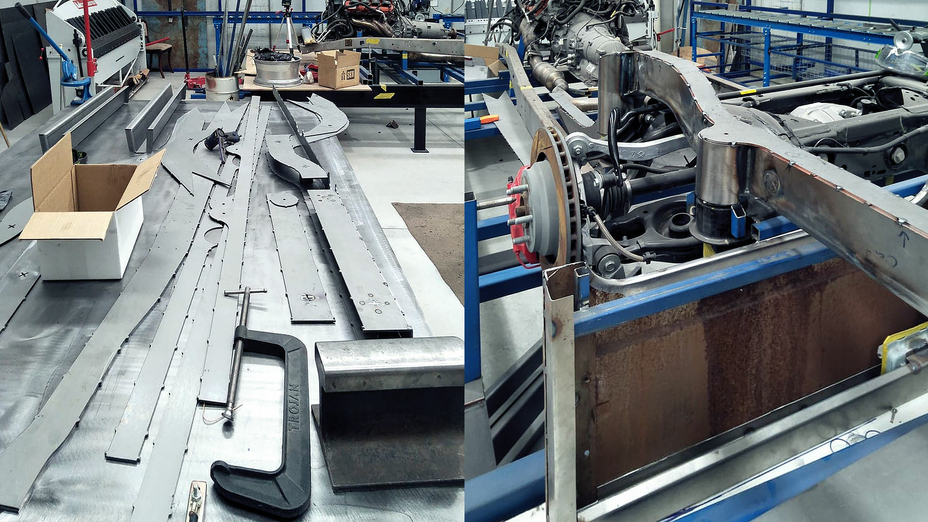
Lasergeschnittene flache Teile, die vor dem endgültigen Verschweißen mit dem Chassis lose zusammengeschraubt worden sind (Bildquelle: streetmachine.com.au)
Nach dem Verschweißen aller Chassiskomponenten wurde der gesamte Innenausbau an einen Autoelektriker geschickt, um das Chassis mit den Originalkomponenten des Hellcat zum Laufen zu bringen. Währenddessen bereitete Forward den Zuschnitt der aus den Scandaten modellierten Karosserieoberfläche (in Schritt 4) vor, um einen Karosseriebock zu erstellen, der dann für die Herstellung der Paneele und die Testmontage verwendet werden konnte.
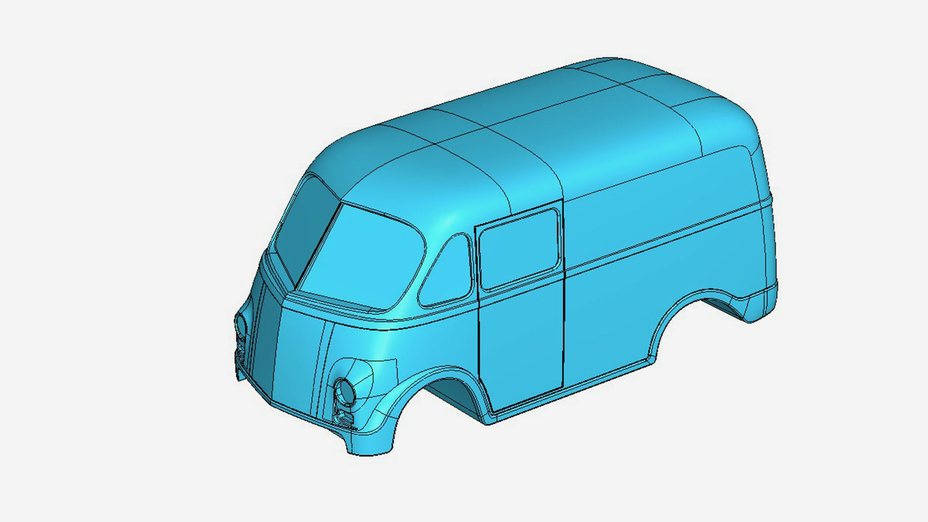
Das endgültige Design des neuen Karosseriestils, mit dem Forward den Karosseriebock bauen wird
Das Team geht davon aus, dass die Karosseriearbeiten in den nächsten 12 Monaten abgeschlossen sein werden. Für den Innenausbau, die Lackierung und andere kleinere Arbeiten hat das Team bis Ende 2023 noch einige Monate Zeit. Nach der Fertigstellung hofft Forward, dass dieses Projekt eine gute Plattform für die Ausbildung anderer Studios und Kunden wird.
„Der Metro Van ist ein großartiges Beispiel dafür, wie meiner Meinung nach alle Autos nachgebaut werden sollten“, so Forward. „Obwohl unser Ablauf Zeit braucht, würde es viel länger dauern, das alte Auto in seiner ursprünglichen Gestalt zu restaurieren, als es mit Hilfe der Daten eines 3D-Scanners von Grund auf neu zu bauen. Die Möglichkeit, Informationen in 3D zu erfassen, ein Reverse-Engineering durchzuführen und Komponenten auf der Grundlage der erfassten Daten herzustellen – das ist es, wofür ich dieses Unternehmen im Grunde gegründet habe.“
„Sobald der HD-Modus verfügbar war, hat mich das absolut umgehauen - es war, als hätte ich einen neuen Scanner gekauft.“
Seit Forward auf 3D-Scannen umgestiegen ist, hat er es nie bereut. Die Möglichkeit,exakte digitale Kopien von Autoteilen zu erstellen, anstatt sie von Hand zu vermessen, hat seine Arbeitsweise, die Genauigkeit der gesammelten Daten und seine allgemeine Produktivität enorm verändert.
Und es wird noch besser: „Ich bin immer wieder erstaunt über die Arbeitsabläufe und die kontinuierlichen Verbesserungen, die Artec vorgenommen hat, um der Entwicklung immer einen Schritt voraus zu sein“, sagt Forward. „Jedes Mal, wenn eine Version neu auf den Markt kommt, bin ich jedes Mal noch begeisterter. Der Unterschied zwischen Artec Studio 15 und 16 ist absolut gewaltig. Als der HD-Modus verfügbar war, hat mich das absolut umgehauen: Es ist, als hätte ich einen neuen Scanner gekauft.